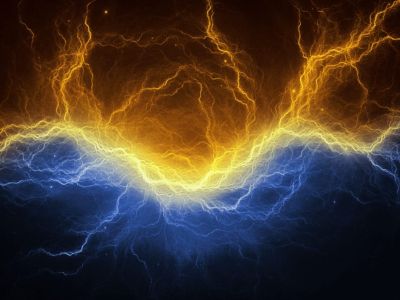
Variabilities in Electrical Arc Flash Protection
Accuracies are synonymous with safety and science. While many perceive that electrical safety needs to be highly exact, this article aims at creating awareness of why sticking to the basics is effective.
But before we delve into variability in electrical engineering, safe electrical work practices and electrical PPE, here is a brief story my second-year engineering physics professor shared when I was in school: A person stands in the center of a boxing ring; their soulmate stands in the corner. The person in the center is only allowed to walk toward their soulmate in discrete steps defined by exactly halving the distance between the two. The physicists witnessing this agree that it will be impossible for the distance between the two to eve…
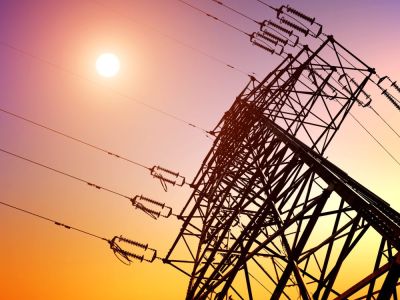
Built In, Not Bolted On: Using Safety to Drive Operational Excellence
Employers in the electric utility industry are currently working on initiatives in various areas of their businesses, including safety, quality, production, leadership, and human and organizational performance (HOP). These are important programs, but it’s unlikely they’ll fully achieve their intended objectives if employees don’t have a firm grasp on how these various aspects of work impact one another – and the ideal order in which they should be addressed.
As someone who has spent a great deal of time studying HOP and teaching its principles to others, I understand that part of the philosophy is building an organizational system that enables employees to complete their work using processes that make sense to them, are easy to follow and…
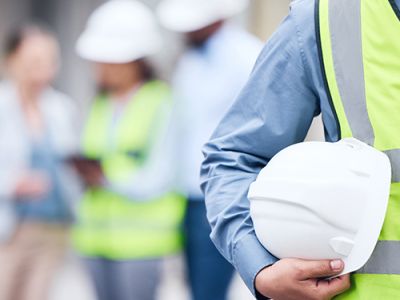
Safety By Design: Safety Management System Planning
In the first two parts of this six-part series, I discussed the importance of creating and implementing a safety management system (SMS) that actively involves all employees. This part will focus on (1) identifying and prioritizing an organization’s safety needs based on specific hazards and risks and (2) developing a plan with clear objectives and targets to meet those needs. Without a solid plan, it’s difficult to assess whether the SMS is effective and adds value to your organization.
Early in my career, I didn’t fully grasp the significance of having a safety plan. I often experimented with new safety trends without understanding what the organization I worked for would gain from them or how success would be measured. Much like a New Y…
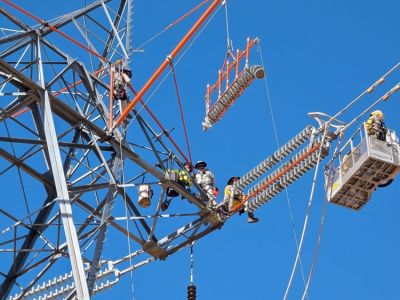
Beyond the ABCs: Fall Protection for Unique Tasks
The electric transmission and distribution (T&D) industry often requires work in challenging environments. Whether crew members access tall structures by helicopter, use rope-access methods to climb lattice towers, or ride wire carts to install and maintain spacers along energized lines, their approach goes beyond standard ground-based operations. These specialized techniques can speed up projects, minimize ground disturbance – especially on protected and sensitive land – and reduce the need for site preparation (e.g., building roads).
Yet all of them present complex fall hazards.
Many readers may be familiar with the so-called “ABCs” of fall protection (anchors, body supports and connectors), but the tasks described above call for mor…
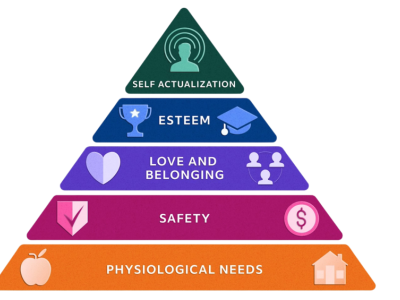
Making the Safety Connection: The Impact of Total Well-Being in the Workplace
Utility workers perform essential tasks that touch millions of lives every day. The critical nature of the services they provide coupled with the perilous nature of their tasks exposes these workers to life-threatening hazards. This is why the industry highly values and prioritizes safety.
Many utility companies operating today have made significant strides in improving their safety culture. Critical risk management programs and a human performance mindset have become increasingly common as organizational leaders more fully understand the link between human behavior and risk. These companies have moved beyond the traditional safety model that primarily focuses on accident prevention, opting instead to embrace risk reduction strategies.
Use…
Safety By Design: Leadership and Employee Involvement
In the first part of this six-part series, I discussed the reasons why it’s important for utility organizations to develop safety systems that align their safety initiatives. This article will address employee involvement, an often overlooked yet fundamental component of any effective safety system.
According to ANSI/ASSP Z10, “Occupational Health and Safety Management Systems,” the phrase “employee involvement” refers to the active participation of workers in the planning, implementation, evaluation and improvement of an organization’s occupational health and safety management system (OHSMS). The OHSMS is a key element of the Z10 standard, highlighting the value of worker input and engagement to appropriately manage workplace risks and pr…
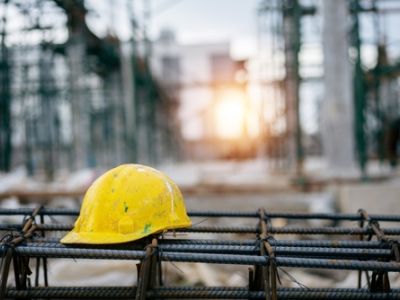
Safety By Design: A System Approach to Organizational Safety Initiatives
Let’s kick off this new series by considering a simple question: Why do we need safety?
Here’s my answer: Safety is a must because hazards and threats exist in our work environments that could cause harm to both our employees and our organizations.
Any initiative designed to protect workers from danger falls under the umbrella of safety. If we were to use minimum approach distances as an analogy, safety is the air gap that insulates an organization. When severe injuries and fatalities occur in our industry, weak safety initiatives – that is, initiatives that do not provide the insulating value needed to appropriately address an organization’s hazards and threats – are often the culprit.
Too many organizations invest their resources in “bus…
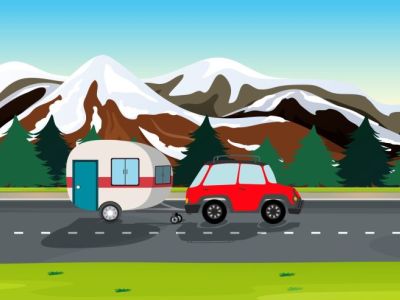
The Roadmap to Gaining Senior Leader Buy-In for Safety Initiatives
| Sharon Lipinski, Wesley L. Wheeler, SMS, CESCP, MSP, and Keith Wheeler | Safety Management, Leadership Development
In a recent survey we conducted, 97% of safety professionals who responded confirmed that gaining senior leader buy-in for their safety programs was either very important or extremely important to them.
This research project was a joint effort between the National Electrical Contractors Association, HR Resources of the Carolinas LLC and Habit Mastery Consulting, with the purpose of discovering the secrets to gaining greater senior leadership support for safety initiatives. Our research included surveying 128 safety professionals and conducting in-depth interviews with 15 deeply experienced safety professionals.
We revealed our research results at the October 2024 iP Utility Safety Conference & Expo in Allen, Texas, sharing with attende…
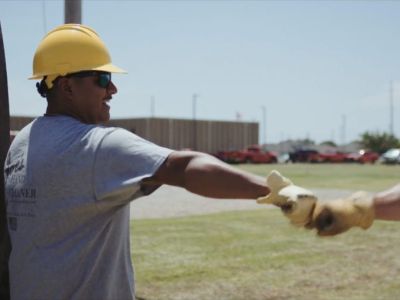
A Three-Tiered Approach to Securing Buy-In for Safety Initiatives
Despite widespread recognition of the importance of worker safety, gaining consistent buy-in for safety initiatives remains a significant challenge for many safety and operational leaders.
Even with the best intentions and efforts, safety programs too often become temporary “flavors of the month” or are reduced to routine check-the-box activities. As a result, these initiatives frequently fall short of their intended impact.
Over the last decade, my team and I have been fortunate enough to partner with dozens of utilities to successfully implement and sustain soft-tissue injury prevention programs. As we began to identify the common factors shared by our most successful customers, several key themes emerged. This article is intended to sha…
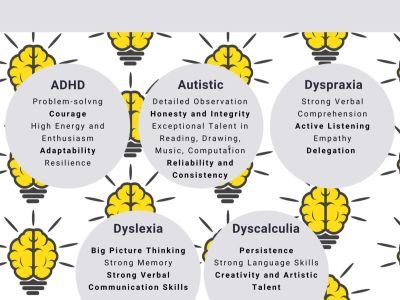
Designing Safe and Inclusive Work Systems for a Neurodiverse Workplace
Editor’s Note: Incident Prevention readers’ initial reaction to the following article might be, “HIPAA?” You are encouraged to check for yourself, but HIPAA – the Health Insurance Portability and Accountability Act – does not apply to the methodologies the author presents (see www.hhs.gov/hipaa/for-individuals/faq/index.html). Incident Prevention recognizes that the author’s work is a deeper dive into the values of human performance recognition. The information presented can improve training and analysis by properly accommodating individual human characteristics that affect both learning and performance. You are encouraged to read on.
Our work systems are based on neurotypical norms and expectations. Neurotypical workers make up most of th…
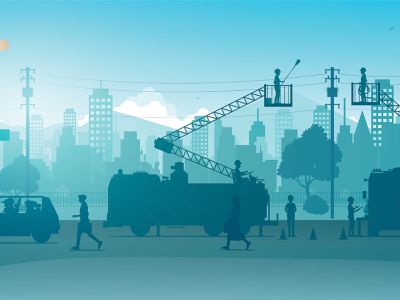
Empowering Utility Workers: Integrating Job Control and Resource Availability for Enhanced Safety
In the utility industry, workplace safety is of vital importance. Utility workers face numerous hazards daily, from working at heights and handling electrical equipment to operating in confined spaces and dealing with extreme weather conditions.
To ensure the well-being of these essential workers, organizations must adopt a comprehensive approach that addresses both job characteristics and resource availability. By integrating the Job Demands-Control (JDC) model and the Conservation of Resources (COR) theory, utility companies can create a safer and more supportive work environment that empowers their employees and reduces the risk of accidents and injuries.
The JDC Model: Empowering Workers Through Autonomy The JDC model, developed by Rob…
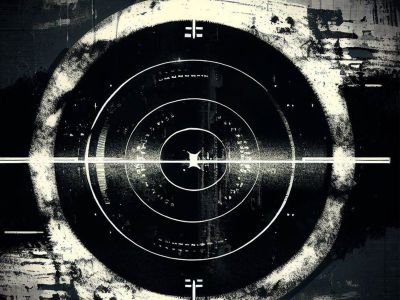
Training Considerations for Active Shooter Response Programs
Active shooter response training for utility professionals is a subject that shouldn’t be ignored. However, few subjects are as challenging or controversial.
For decades, active shooter response training has been touted as a one-size-fits-all remedy that instills long-lasting, actionable survival skills in one easy application. In reality, off-the-shelf training programs seldom deliver on promises. Training is often poorly delivered cookie-cutter sessions that focus on the wrong messaging and outcomes. Active shooter response programs are fraught with complications and issues that, if left unresolved, can make the training more of a hazard than a help.
You may think, “OK, so let’s just skip the training.” Sorry, but that’s not the answer e…
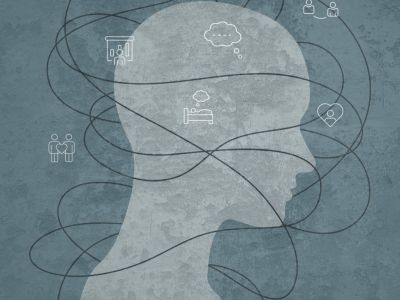
Beyond the Physical Toll: The Collateral Damage of Safety Incidents
While leading a recent workshop at a client location, the introductions began by individually discussing how incidents at work have affected us. One story shared left an impact on all in attendance.
Fifteen years ago, an employee suffered what at the time seemed like a simple and small fracture to their leg after a fall. What resulted was a total of 12 surgeries, and the employee’s wife became addicted to the opioids he was prescribed. Tragically, she passed away due to her addiction. Workplace injuries and incidents can have far-reaching consequences that extend beyond the immediate physical harm suffered by an employee.
The collateral damage resulting from such incidents can significantly impact various aspects of an organization and the…
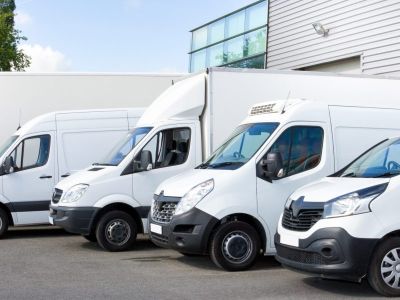
DOT Compliance Considerations for Electric Utilities
The roar of diesel engines fills the midnight air as a crew of linemen prepares to depart for a critical repair job. Their trucks are loaded with tools and equipment, ready to tackle a downed power line that lies miles away. But before they hit the open road, there’s one crucial hurdle to clear: ensuring that their vehicles and the way they operate them comply with U.S. Department of Transportation (DOT) regulations.
Electric utility providers operate a complex network of vehicles, from bucket trucks scaling towering heights to service vans navigating city streets. Each vehicle plays a vital role in ensuring a reliable flow of electricity. However, these workhorses on wheels also pose potential safety risks if they are not operated and mai…
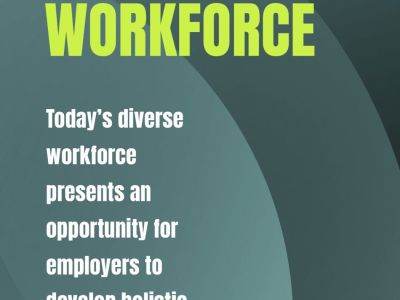
Ergonomics for a Multigenerational Workforce
Gray wave. Silver tsunami. Population aging.
We’ve all heard the names and metaphors, and experts have talked about the phenomenon for years. In 2024, it’s truly upon us: The population, both in the United States and abroad, is getting older, with major implications for the workforce and how employers manage it.
But these descriptors don’t capture the full reality of the situation. Today’s workforce, which is older on average than in previous decades, is also more diverse than ever, including members of as many as five generations born across nearly a century. So, while researchers have anticipated the aging phenomenon for many years, employers – and their safety leaders in particular – now must deal with the broader issue of a truly multi…
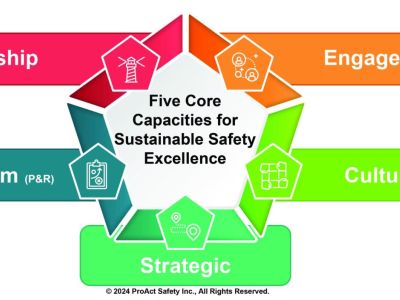
Five Core Capacities for Sustainable Safety Excellence
Does your organization have the capacity to achieve sustainable excellence in safety performance and culture?
For excellence to become a reality in any important area of operations, especially safety, there are five vital capacities that organizations must develop, monitor and synergize to adapt and thrive in a fast-paced and ever-changing world: system, leadership, engagement, cultural and strategic. Based on extensive cross-industry research and decades of experience leading change in all major industries, this article introduces the model titled “Five Core Capacities for Sustainable Safety Excellence.”
System Capacity to Prevent and Recover For a long time, safety efforts primarily focused on preventing unwanted events and gave little r…
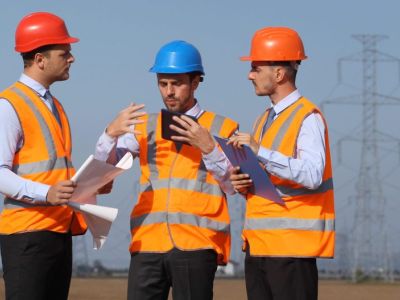
An Experiment in Crew Member Engagement
I don’t talk about myself a lot – I listen. I developed this skill after taking on a leadership position with a utility contractor in an industry I knew nothing about.
My work history prior to this role included management in pretty much every industry except utilities. In each of my previous jobs, I strived to learn and advance from an entry-level position. In this new position, I no longer had the advantage of knowing how the company ran from the ground up; I had to trust and depend on others to help me. It did not take me long to realize that safety is the most important priority in this industry. Lack of attention to the detail of safety can kill a lineworker and damage a company beyond repair. So, while you could say our company’s jou…
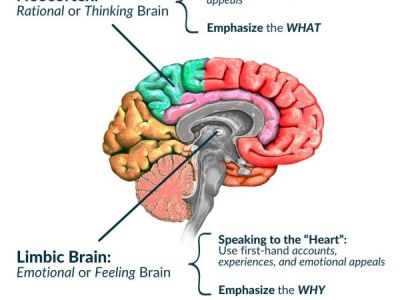
Getting to the Heart of At-Risk Behaviors with Facilitative Learning
In a recent workshop with a client in southeast Louisiana, a breakout session reached a tipping point. The rhythmic flow of dialogue among the seven supervisors in the group found an unscripted but purposeful path of its own. The task given to the group involved identifying at-risk behaviors or shortcuts likely to occur in their work environment. Participants were also asked to discuss motives for the identified behaviors and strategies for shifting perspectives regarding them. The intent of the three-part exercise, which was deliberately constructed to achieve the resulting outcome, was to pull information from the collective experiences of those in the session needed to improve operational safety. My role in the process wasn’t to instruc…
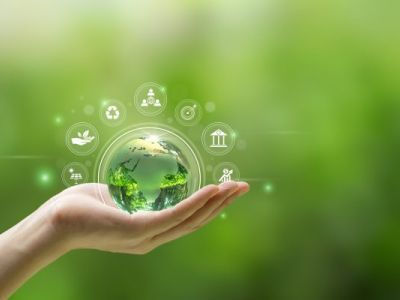
ESG: Health and Safety Obstacle or Opportunity?
Over the past few years, much has been written and discussed about the role of environmental, social and governance, commonly referred to as ESG. Investors and customers are increasingly applying these nonfinancial factors as part of their analysis process to identify material risks and growth opportunities in the companies they decide to invest in. According to research from the Weinreb Group, in publicly held U.S. companies, the position described as chief sustainability officer has grown from 29 such officers in 2011 to 183 in 2023 (see https://weinrebgroup.com/2023-cso-report-press-release/). These are roles that typically sit in the C-suite of a company and have direct strategic decision-making responsibilities.
Many health and safety…
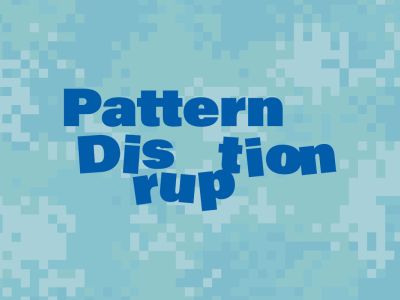
Pattern Disruption: Don’t Start with ‘Why’
In the northern latitudes, Mother Nature is deeply vested in a cycle of pattern disruption. The four seasons change the ecosystems and habitats. As the seasons shift in New York, the lake that I live on moves from a warm thermocline with colder layers on the bottom and warmer water on top to the opposite. In the coldest months, the top of the lake freezes entirely. The ground freezes, too, while the monarch butterflies leave and many of the birds fly south.
But even those pattern disruptions – the four seasons – become a rhythm, an expected ritual during which we trade lawnmowers for snowblowers and put away the outdoor furniture, only to reverse those actions when the weather becomes warm once again.
You may already know that the human br…