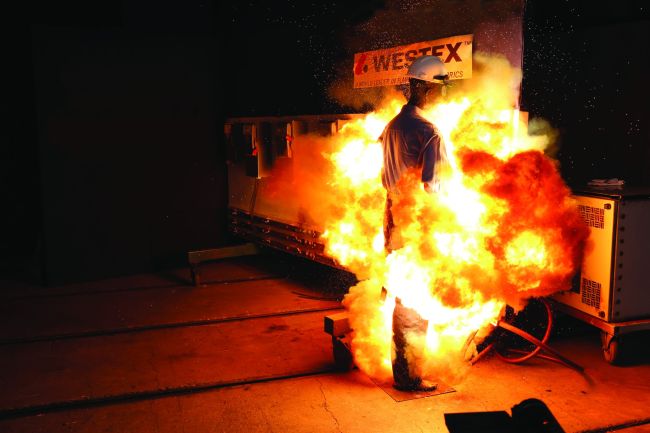
Using PPE to Bolster Safety Resilience
Task-based and daily wear PPE programs help protect a company’s workers and improve resilience.
Task-based and daily wear PPE programs help protect a company’s workers and improve resilience.
Alexander Pope famously wrote that “to err is human,” yet as safety professionals, we often feel that we can prevent incidents if we eliminate all risk.
It’s a concept that has permeated nearly every facet of the safety sphere: account for the risks, eliminate their presence and prevent injuries. Even still, incidents and injuries do happen, sometimes with catastrophic consequences. This has brought about a shift in the safety mindset, moving toward a more resilient outlook.
Erik Hollnagel, a world-renowned professor and champion of the resilience engineering movement, coined the terms “Safety-I” and “Safety-II” as schools of safety thought. According to Hollnagel, “Safety-I is freedom from unacceptable risk, whereas Safety-II is the ability to succeed under varying conditions.”
Thus, Safety-II is all about building resilience – the capacity to respond to, adapt to and recover from a disruptive event while also enhancing the ability to succeed in varying conditions. If you are a car manufacturer, for example, you might apply the Safety-II methodology to the car design process, enhancing a car’s ability to absorb the energy of a crash and keep its occupants safe with airbag deployment. The goal here is not to prevent a car accident but to adapt to and recover from an accident while reducing significant loss and injury.
This shift in thinking encourages safety professionals to widen their approach to their work. The aim is no longer to simply avoid accidents; it’s also to increase resilience so that we can absorb, adapt and recover in all circumstances.
Through the lens of building resilience in our safety programs, the role of personal protective equipment becomes even more amplified. Not only does it help to reduce an organization’s risk by serving as a final layer of defense, but it also improves organizational resilience.
Prepare for the Worst, Strive to Improve
We already know that accidents can and do happen. What’s more, workers in the utility industry may face arc flash and flash fire hazards every day.
So, how do we work toward resilience and still strive for an accident-free workplace?
The foundation is, of course, consensus standards and applicable OSHA regulations. NFPA 70E for arc flash hazards, NFPA 2112 and 2113 for flash fire hazards, and NFPA 652 for combustible dust hazards provide a clear baseline for managing risk. These standards provide guidance to identify and enforce safety measures. They also begin to address the concept of building a safety mindset culture.
Further, a properly conducted risk assessment clearly articulates a job site’s hazards, helping to frame the application of the standards and giving context to how to prevent incidents. Increasingly, though, the concept of human performance is working its way into risk assessments, aiding in the creation of safety plans that strive to prevent incidents but also provide for the possibility that incidents might occur. With more than 90% of injury-causing incidents tracing their root cause back to human error, human performance is a critical concept to address.
Most recently, the 2018 edition of NFPA 70E introduced the concept of human performance and how it can be applied to electrical safety. Human performance is an aspect of risk management that addresses performance as factors that either lead to or prevent errors. NFPA 70E’s “Informative Annex Q: Human Performance and Electrical Safety” outlines the following five principles of human performance, which can be applied to nearly any hazard assessment:
- “People are fallible. Even the best people make mistakes.”
- “Error-likely situations and conditions are predictable, manageable, and preventable.”
- “Individual performance is influenced by organizational processes and values.” (Read another way, organizational processes and values equal organizational culture.)
- “People achieve high levels of performance with encouragement from leaders and peers.”
- “Incidents can be avoided by understanding reasons mistakes occur and lessons learned.”
These five principles broaden the role of safety professionals to account for human performance, which in turn bolsters an organization’s safety culture. It is important to use all the tools in your safety toolbox, so implement an appropriate site risk mitigation plan to protect against incidents, but also consider addressing and improving human performance issues to prevent human error. This is where PPE can really stand out as a risk control.
PPE: A Protective and Preventive Measure
An appropriate site safety program balances the idea of protective and preventive measures, with PPE helping to achieve both.
PPE helps to mitigate injuries should a thermal event occur. This protective measure is the final layer of defense should all other control methods fail. Safety professionals use a risk assessment and risk management principles to reduce site risks to as low as reasonably practicable. PPE is a tool to achieve that end. In particular, safety professionals consider the following key items when determining what type of PPE program is best suited to their needs:
- Is the worker qualified to complete the hazardous task, and have they been trained on safe work practices? If the answer is no, the worker should not be performing the task and would not need PPE.
- If the worker is qualified, what physical and emotional state are they in or likely to be in when completing the hazardous task? Consider if the worker might be feeling fatigued, frustrated or rushed. Could they be a seasoned worker and susceptible to complacency? It is vital to be honest in this assessment.
- What is the status of the work environment and equipment? Think about both the past and present conditions of the equipment, as well as the history of the job site.
Armed with answers to these questions, safety professionals can decide upon a PPE program that makes sense for reducing risk. In some instances, a task-based PPE program – where protective gear is donned before performing a specific task – may be feasible. For example, if qualified workers in a calm and rested state of mind are working on new machinery unlikely to arc, then a task-based PPE program may make sense. It mitigates injury should the worst occur.
Yet a daily wear PPE program can also further safety resilience.
Consider the example above: qualified workers performing tasks they are trained for on new, well-kept equipment. Accidents can still happen, judgment calls may fall short, and new equipment can still cause harm. If you have a Safety-II mindset, you may still want to plan for the eventuality that something will go wrong. Intentionally choosing a daily wear PPE program can be that next-step preventive measure.
With a daily wear program, employees wear flame-resistant/arc-rated garments throughout the duration of their shift. The garments, when worn correctly, are then in place should a thermal incident occur and are not reliant on a worker making a judgment call in the moment. For instance, if your highly trained worker is completing their routine task one morning after being up all night with a sick child, their daily wear garments are in place to help protect them if they are fatigued and have an increased susceptibility to human error.
Daily wear as a preventive measure can also offer a constant, proximate, tactile trigger for the safety mindset you want on the job. Because the garments are put on before work begins, they trigger a worker to set the tone for the hazardous task they are about to perform. And while on the job, the FR/AR garments also help workers to remember other necessary task-based PPE, such as hand and face protection, because they already have safety on their mind. Daily wear underpins a resilient culture where safety goes beyond preventing unacceptable risk and improves the probability of safe outcomes in varying conditions.
Accidents happen, but your outlook doesn’t have to be bleak. Safety professionals have an opportunity to better protect workers by infusing a safety culture mindset into their organizations that bolsters safety resilience. PPE can be a valuable tool to help achieve this.
About the Author: Scott Francis is the technical sales manager for Westex by Milliken. He earned a master’s degree in inorganic chemistry and has been involved with the safety industry since 1991, gaining extensive experience in protective apparel fabrics and PPE. Reach him at scott.francis@milliken.com.
- February – March 2022 Q&A
- From My Bookshelf to Yours: ‘Extreme Ownership’
- Using PPE to Bolster Safety Resilience
- Safety Advancements in the Line-Clearance Industry
- ANSI A92.2: 2022 Changes and Training Requirements
- Grounding Conductor Confusion: What’s the Best One to Use?
- The End of a Career
- Safety Signs and Sign Policy