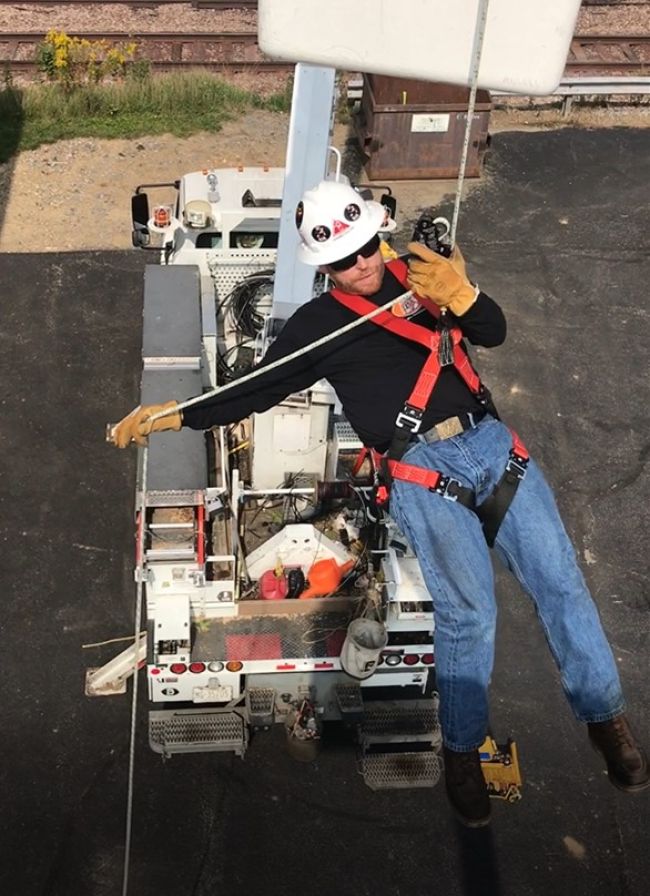
Electrical Arc Flash and Shock Hazards for Fall Protection Using ASTM F887
Electrical Arc Flash and Shock Hazards for Fall Protection Using ASTM F887
The standard helps to ensure equipment safety in multihazard environments.
Arc-rated personal protective equipment (PPE) provides thermal protection against burns to a worker’s body. Fall protective systems, although categorized as PPE, do not have the same primary purpose. A fall protective system’s primary performance requirement is fall protection. In applications where both the exposure to thermal hazards from an electric arc or flame and the prevention of falls must be considered, the fall protective system must retain its mechanical integrity when exposed to thermal stresses. This article introduces the testing and specifications standard and practical considerations for use in such multi-exposure applications.
Duty to Protect
Workers exposed to the potential hazard of falls shall be protected as per OSHA 29 CFR 1926.501, “Duty to have fall protection”; 1910.269(g)(2), “Fall protection”; and 1910.140, “Personal fall protection systems.” Employers shall consider the hazard of falling from heights and provide the necessary safety means to ensure that workers are not exposed to this risk.
It can be summarized that OSHA requires fall protection to be provided at elevations of 4 feet in general industry workplaces and 6 feet in the construction industry. In addition, OSHA requires that fall protection be provided when employees are working over dangerous equipment and machinery, regardless of the fall distance. Further, 1910.269(g)(1) requires that fall protective equipment exposed to an electric arc that exceeds 2 cal/cm2 or a shock hazard inside the minimum approach distance (MAD) be adequately rated for use.
Persons requiring fall protection may not be protected due to two overarching reasons. First, the employer may fail to provide fall protection when needed. This may be due to a lack of awareness, inadequate risk assessments or failure to enforce usage. Portable ladders that are adequately secured per OSHA requirements do not require fall protection. Fixed ladders require fall protection or another means of safety at heights of 24 feet from the fall or ground surface. Although OSHA does not mandate the use of fall protection when the levels between scaffolding are less than 10 feet, they have recommended using it in a letter of interpretation. There is no minimum requirement for fall protection when working over dangerous machines – such as acid tanks, hot surfaces, conveyors and rotating objects – so fall protection is required in these cases irrespective of the elevation. There are several other instances when OSHA requires fall protection, and employers are encouraged to research all at-risk conditions that may mandate its use.
Second, the employer may be using the incorrect type of fall protection. Older-generation fall protection equipment did not consider electrical shock and electrical arc flash hazards. It is also possible that cheaper fall protection was purchased instead of the more expensive multihazard protective equipment. Before 1910.269(g)(2) became law, some harness companies that focused on utilities made harnesses meeting part of ASTM F887, “Standard Specifications for Personal Climbing Equipment,” but they did not meet the arc evaluation portion. These were labeled as such and may still be in service in utilities. Because they are illegal to use in any exposure >2 cal/cm², be sure complete reports that include the arc flash testing portion are provided if the hazard is present.
Shock and Arc Flash Hazards
Historically, certain fall protective equipment components (e.g., safety harnesses and positioning straps) were constructed from nylon. The updated 1910.269(l)(8), “Protection from flames and electric arcs,” follows closely on the heels of NFPA 70E (note: NFPA 70E does not apply to generation, transmission and distribution covered by 1910 Subpart R unless users elect to follow certain sections of this national consensus standard). Article 130.7(C)(11) of NFPA 70E 2021 requires that melting substrates (melting point <600°F) not be used inside the arc flash boundary. However, this requirement applies to clothing but not to other protective equipment. While most modern fall protective equipment used against electrical arcs is constructed from aramid fibers, it is important to know that compliant nylon products are also available. NFPA 70E 2021 permits use of melting substrate if it is arc-tested in blends, while OSHA states that these are allowed if the “employer demonstrates that the fabric has been treated to withstand the conditions that may be encountered by the employee.” OSHA 1910.269(g)(2)(ii) requires that personal fall arrest equipment pass a drop test, using a body-weight adjustment factor, following exposure to an electric arc at 40±5cal/cm2. Products meeting this performance requirement, whether aramid or nylon, are considered sufficient to protect against the thermal effects of an electric arc. ASTM F887-20 requires evaluation at an exposure of 40 cal/cm2, so using this specification would be adequate for meeting the performance requirement detailed by OSHA.
OSHA 1910.269(g)(2)(iii)(G) requires a determination of the electrical withstand rating of non-metallic positioning straps. Although equipment used inside the MAD shall be nonconductive per 1910.269(l)(3)(iii), it is required that hardware on fall protection equipment be constructed of steel or an equivalent per 1910.269(g)(2)(iii)(A)(1). This may appear contradictory, but OSHA does clarify that conductive materials may be permitted inside the MAD if the employee is insulated from energized parts through the use of gloves, shoes, sleeves and so forth. The conductive items remain on the outer side of the non-metallic, electrically tested positioning straps, and they are usually backed by leather instead of having direct contact with the positioning straps or the worker’s clothing, thereby meeting the OSHA requirements for shock protection. There is not a direct requirement that all metal be coated or not in direct contact with the body, but many utilities write this into their specifications.
Most new fall protective equipment that meets the thermal, electrical and load-bearing requirements is manufactured from aramid fibers like Kevlar, Twaron and Nomex. Compacted and high-denier, high-tenacity nylon webbing used in fall protective equipment has also been able to meet the performance criteria achieved by aramid products.
Arc-Tested vs. Arc-Rated and ASTM F887-20
As discussed, fall protective equipment is defined as PPE, but it is not defined as clothing or apparel and thus is not arc-rated. Instead, it is arc-tested using a 40±5cal/cm2 arc, which is followed by a weight-adjusted drop test. ASTM F887-20 is used to ensure that fall protection equipment meets the OSHA requirements for arc flash as well as some dielectric requirements.
Although nine categories (with several subcategories) of fall protection are discussed in this standard, the three broad categories for fall protective equipment are fall restraints (zero-foot free-fall), work positioning (2-foot free-fall) and fall arrest (6-foot free-fall). Several mechanical tests are discussed in the standard, but this article focuses on the flammability, arc response and electrical shock performance of the fall protective equipment.
All fabric, rope and leather are electrically tested by applying 3-kV DC across two electrodes placed 12 inches apart. Alternatively, a dielectric withstand test of 25-kV AC per foot is applied to the dry materials. To pass the DC leakage test, the maximum leakage current shall not exceed 1 mA. The dielectric AC test is sustained for three minutes, and the test specimen should not display any signs of visible deterioration.
The flammability test is performed on the positioning strap or rope that is loaded with a 220-pound mass. A 3-inch blue flame (propane or butane) is held to the edge of the specimen for five seconds and removed. The afterflame shall be allowed to self-extinguish, after which the test specimen should successfully suspend the load. Many companies also test positioning straps and ropes using the 40±5cal/cm2 arc test.
The arc test is typically performed on a mannequin (per ASTM F887 using the ASTM F2621 test method) or a panel (using the ASTM F1959 test method setup). Accessories are placed at the midpoint of the arc gap in either test setup. Three accessories or lanyards specimens are tested unless the back and front differ, in which case both sides shall be tested. The harness on the mannequin is tested for both front and back exposure, and the quantity of arc flash and drop test samples is dependent on the attachment locations (dorsal, frontal). The test lab documents the afterflame time, arc ignition and dripping. The afterflame shall not exceed five seconds, or 15 seconds for accessories. Load-bearing materials shall not display any melting or dripping. However, certain accessories, such as labels and elastics, are permitted to melt and drip if these do not ignite while dripping or propagate flames to other parts of the test specimen.
Harnesses and energy-absorbing lanyards shall be immediately exposed to the drop test following the thermal assault of the arc flash testing. Harnesses are tested by means of a quick-release mechanism on a suspended load. The load remains suspended for five minutes, and no load-bearing element shall display visual mechanical failure such as breaking or separating. Six-foot and 12-foot free-fall energy absorbers are tested to the applicable ANSI/ASSE Z359.13-2013 standard.
Since ASTM F887-20 is a design test, it is important to understand that new specimens shall be tested if any component is changed. Harnesses made of nylon have failed after a year in the field in arc testing, but we know of no field failures of fibrillated harnesses. Many users have moved to aramid harnesses to eliminate the risk of potential harness failures from ignition.
There are limitations to what is included in the scope of ASTM F887 for arc flash testing. Energy-absorbing lanyards, fall protection harnesses and components of these devices (accessories) are applicable. Other items, like trauma packs or self-retracting devices, may be tested for due diligence using the ASTM F887 setup and exposure, but they are not officially included in the scope of the standard. These products may still be exposed at 40 cal/cm2 to check for ignition, melting and dripping.
There are marking requirements for the ASTM F887 specification. Energy lanyards must meet the requirements of ANSI/ASSE Z359.13-2013 and the qualification testing requirements of Sections 22 and 26 for compliance. Harnesses can be labeled as compliant with ASTM F887 if load-bearing webbing used in the construction has a minimum breaking strength of 7,000 lbf, and if they meet ANSI/ASSE Z359.11-2014 and Sections 22 and 25.5 of ASTM F887-20. Make sure the fall protection harness and lanyard of purchase meet both the marking requirements of ANSI/ASSE Z359.11 and list compliance with ASTM F887 if there is risk of an arc flash exposure. A copy of a test report may be requested to review the test results.
Although manufacturers normally perform the design tests, end users may consider testing older nylon fall protective equipment that has not been tested to this standard. Also, it is advisable to perform a test on a piece of in-service sample fall protective equipment if it has become “fuzzy” (fibrillated) from use.
Conclusion
Fall protective equipment used by workers exposed to electrical hazards must perform in a multihazard environment consisting of thermal withstand, electrical withstand and load bearing. The design and testing of this fall protective equipment increases the cost of the end product. Further, products manufactured from aramids are likely to be more costly than nylon-based products. Employers should understand the work that is performed during the company’s day-to-day operations as well as the work defined as construction and ensure that the fall protective equipment provided to a worker is appropriate for the hazard exposure. If employers keep non-ASTM F887-20 fall protective equipment within easy access of workers, care should be taken to ensure that the workers understand the proper selection and use of these products. Failure to do so may leave the employer exposed to unnecessary risk.
About the Authors: Zarheer Jooma, P.E., is a partner at e-Hazard (https://e-hazard.com), has a master’s degree in electrical engineering and is a registered professional engineer in multiple states. He performs electrical workplace safety training, arc flash engineering studies, electrical accident investigations and electrical safety audits. Jooma is a member of the IEEE 1584-1:2021 Working Committee and Ballot Resolution Committee, ASTM F18 – Electrical Protective Equipment for Workers, and IEC TC78 – Live Working, and he has contributed to NFPA 70E.
Stacy Klausing is the PPE project manager at ArcWear (www.arcwear.com). Her professional experience includes project management in testing laboratories, testing and evaluating fabric related to PPE, the quality process of continuous improvement, and execution and management of an ISO 17025 accredited quality system. She earned her master’s degree from the University of Kentucky in merchandising, apparel and textiles with a special focus on textile science. Klausing is also a Six Sigma Green Belt from North Carolina State University.
Hugh Hoagland is a senior consultant for ArcWear, a division of Kinectrics, and the founder of e-Hazard. An expert on electrical arc testing and electrical safety, he serves on ASTM F18 and IEC TC78 and is associate editor for the IEEE Electrical Safety Committee. Hoagland’s accident investigation studies and arc flash research have been widely published in peer-reviewed journals and safety and trade magazines.
- 3 Keys to Transforming Safety and Organizational Performance
- A Historical Review of Workplace Safety in the U.S.
- Electrical Arc Flash and Shock Hazards for Fall Protection Using ASTM F887
- OSHA Electric Power Standards – Simplified | Part 6
- 9 Safety Axioms You Need to Know
- October-November 2021 Q&A
- System Grounding for Worker Protection Against Induced Voltages
- Eating the Elephant