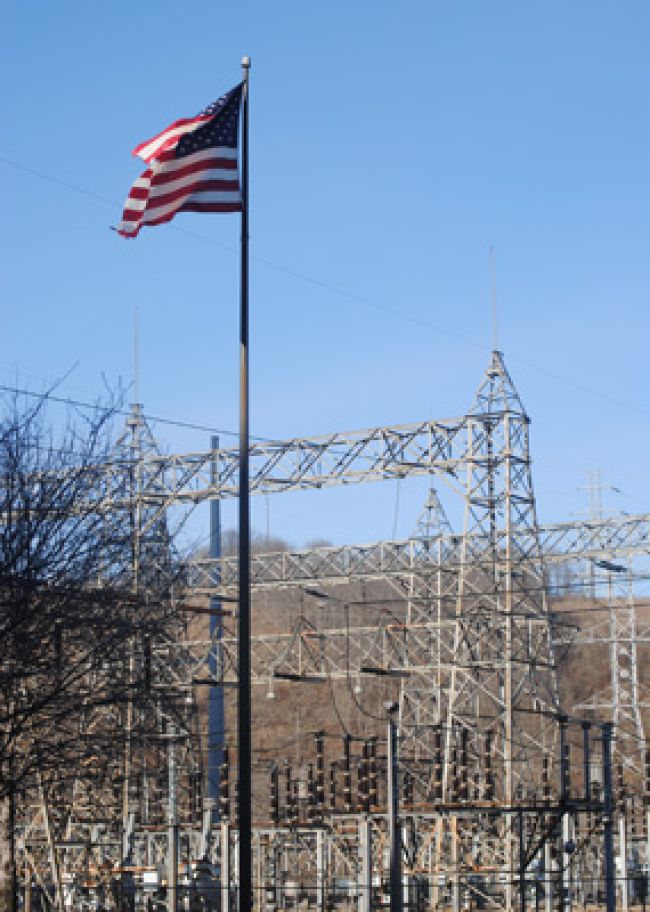
Shining a Light on Ventilation Systems and Surveys in the Electric Power Industry
It takes a wide variety of activities – some obvious and others not so obvious – to keep electric utility operations humming along. With maintenance facilities and power plants in particular, there are sometimes unidentified exposures that grow as the facilities grow. In other scenarios, our understanding of exposures or emerging regulations requires the need for a professional hygienist to assess and remediate exposures. Ventilation surveys, which can detect ventilation system failures, are a critical but often overlooked tool that should be used to maintain safe, healthy operations, whether those are power generation operations, transmission and distribution operations, or peaker operations during which power is produced during periods of peak usage. All of these operations require appropriate ventilation to control atmospheric hazards. Failure to recognize the importance of maintaining and periodically checking ventilation systems may impart substantial hidden risk to personnel, facilities and operations.
However, it is not uncommon to see operations that lack the needed systems; are serviced by jury-rigged systems that do not meet operational needs; or are serviced by well-engineered systems that over time have fallen into disrepair due to a lack of ventilation surveys and preventive maintenance.
How is it that these matters fall between the cracks?
It is easy for occupational health to take a back seat to occupational safety or other priorities. Poor change management can be blamed if a new system is installed and there is either no follow-up or incomplete follow-up for hazard control concerns. A simple lack of subject matter expertise within an organization could be the problem; perhaps there is no knowledgeable industrial hygienist on staff and an overwhelmed safety professional wearing multiple hats gravitates away from his area of lesser expertise. In some cases, chemical exposures take years to become evident and manifest symptoms. As such, they are a lower priority than more high-visibility issues, like falls from height or arc flash. Or, it may be that ancillary activities are out of sight and out of mind, and not recognized as a priority for hazard control.
Regardless of the reason, occupational health and safety cannot be maintained without appropriate attention to ventilation matters. The purpose of this article is to shine a light on these matters and encourage organizations lacking the needed expertise to learn to handle them appropriately.
What is a Ventilation Survey?
As stated earlier, ventilation surveys can be used to detect ventilation system failures. More specifically, this type of survey is an organized procedure of acquiring data to quantify and characterize airflow, pressure and air quality throughout a ventilation system. An optimal ventilation survey will go further, not only measuring the airflow parameters – including airflow, duct velocity and air changes per hour – for comparison to an appropriate standard, but also reviewing a variety of related issues that could impact system effectiveness. These issues could include improper use of the system by employees as determined via employee interviews; system damage revealed by inspection of the area; looking and listening for damaged and/or missing system components; and measuring system component dimensions and placement to ensure adequacy when compared to the given standard.
Regulatory requirements, consensus standards or other applicable guidelines should be consulted to determine the appropriate frequency of performing a ventilation survey for a given system. Otherwise, a best practice is to routinely perform needed ventilation surveys at least annually. If adjustments or modifications are made to a system, that system should be retested upon completion of the changes.
Of course, if you or someone within your company is going to perform a ventilation survey, it is critical that person has a strong understanding of and experience with ventilation systems. The following sections provide an overview of the purpose of these systems as well as various system types.
Dilution vs. Local Exhaust Ventilation Systems
Dilution and local exhaust ventilation systems serve a critical function as they:
• Prevent the occurrence of flammable and explosive atmospheres; and/or
• Control mist, dust, smoke, fume, gas and vapor air contaminants to maintain worker exposure below the prescribed occupational exposure limits.
What are the differences between the two types of systems? Local exhaust ventilation systems are used to control air contaminants at their source whereas dilution ventilation systems control air contaminants by continuously changing out room air at a specified rate. Dilution ventilation systems do not prevent exposure but rather lower the concentration to acceptable levels. The type of system recommended for an application depends upon the nature of the operation and the level of control required.
It is essential for power operations to establish appropriate controls to maintain the regulatory number of air changes per hour or occupational exposure limits established by OSHA in the U.S. or other appropriate regulatory bodies. As a matter of good practice, it also is important to recognize non-regulatory but recommended, scientifically based occupational exposure limits, such as the American Conference of Governmental Industrial Hygienists’ Threshold Limit Values; American Industrial Hygiene Association’s Workplace Environmental Exposure Levels; NIOSH recommended exposure limits; and chemical manufacturer recommended limits.
Is a Ventilation System Needed?
The risk faced by employees in the power industry is a function of the hazards that are present and the level of exposure to those hazards. An organized, systematic method of exposure and risk assessment is key to being able to control health risks. This method – known as qualitative exposure assessment, or QEA – can be used to characterize workplace exposures to chemical, physical and biological agents. The method is illustrated in Figure 1 below; in-depth information can be found at https://phc.amedd.army.mil/topics/workplacehealth/ih/Pages/ExposureAssessmentStrategies.aspx. More specifically, a QEA performed by a qualified industrial hygienist can:
1. Uncover the potential need for any nonexistent engineered ventilation systems; and
2. Catalog all existing mechanical ventilation systems to be scheduled for survey and assessment by a competent person at the appropriate intervals.
Local Exhaust Ventilation
Following are some areas within the electric power industry where local exhaust ventilation may be required, as well as examples of local exhaust ventilation systems that may best serve those areas.
• Abrasive blast cabinets often are used by maintenance personnel to remove surface corrosion or coatings from metal items. Hazardous air contaminants may include but are not limited to crystalline silica (still contained in some blast media) and beryllium (contained in some blast media, including Black Beauty coal slag abrasives), as well as lead and iron oxide from coatings on the blasted media.
• Commercial kitchens are maintained by some electric utilities for their staff. Many utilities are unaware of the potentially serious nature of chronic overexposure to hazardous air contaminants that can be present in all types of kitchens. These contaminants include products of combustion (e.g., carbon monoxide, carbon dioxide, nitrogen dioxide and particulates) and contaminants generated by frying and inadvertent burning of foods, most notably a variety of polycyclic aromatic hydrocarbons and the carcinogens acrylamide, benzo(a)pyrene and formaldehyde.
• Woodworking equipment: Most of us own wooden furniture and have trees in our yards, but a number of people have little to no awareness of hazards intrinsic to wood and wood products. A variety of occupational exposure limits may apply to wood dusts. Health effects upon exposure may vary with the species of wood. Western red cedar is a sensitizer; once sensitized, the body will quickly react on subsequent exposures, even in low airborne concentrations. Oak is a known carcinogen. Other concerns are the possible presence of hazardous constituents related to wood treatments (e.g., arsenic, also a carcinogen), as well as sap, latex, lichens and more.
• Paint booths often are found in vehicle maintenance shops to control contaminants such as isocyanates (sensitizers) and a wide variety of volatile organic compounds.
• Pesticide mixing sinks may be found at locations where companies mix and apply their own pesticides. Health effects from pesticide overexposure, depending on the pesticide, may include neurological effects, cancer or reproductive effects.
• Industrial wastewater pretreatment system chemical tanks may require mechanical ventilation to control exposure to hazardous air contaminants such as acids and caustics.
• Many types of metalworking equipment may require local exhaust ventilation to control emissions of metals and metal coatings.
• Hand grinders are used to grind gaskets made of asbestos, a known human carcinogen, and can be fitted with shrouds.
• Asbestos brake and clutch work. Negative pressure enclosure/high-efficiency particulate air vacuum systems may control exposure to asbestos when more than five jobs are performed per week.
• Common laboratory hoods may be used to control countless hazardous air contaminants.
• Laboratory AA spectrometer hoods may control any of a number of toxic metal emissions, including manganese.
• Laboratory ovens may control humidity and other air contaminants.
• Overhead and underground vehicle exhaust hoods are found in vehicle maintenance shops. They exhaust air contaminants, including carbon monoxide, as well as diesel exhaust, a known human carcinogen.
• Radiator repair hoods may be located in vehicle maintenance shops to control lead emissions.
• Plasma downdraft tables, portable and fixed welding hoods, and welding booths are found in welding shops and used to control emitted hazardous air contaminants, including but not limited to chromium, nickel, arsenic, asbestos, manganese, silica, beryllium, cadmium, nitrogen oxides, phosgene, acrolein, fluorine compounds, carbon monoxide, cobalt, copper, lead, ozone, selenium and zinc.
Dilution Ventilation
Following are some areas within the electric power industry that may require dilution ventilation systems.
• Oil recycling houses. Inhalation of oil mists may cause adverse respiratory effects; OSHA has established permissible exposure limits for these mists.
• Battery charging rooms. These are found at substations, peaker sites, generation facilities, radiofrequency rooms and other locations. Certain batteries may emit varying amounts of flammable/explosive hydrogen gas under normal and/or abnormal charging conditions. Of the many sources that establish ventilation requirements for battery rooms, manufacturers’ requirements and local fire codes must not be overlooked.
• Chlorine storage rooms. Chlorine is used in cooling water applications; proper ventilation prevents a buildup of gases.
• Flammables storage rooms. If these areas contain fuels, paints, thinners or other flammable substances, proper ventilation prevents explosive atmospheres from occurring.
• Pesticide storage rooms. Proper ventilation prevents exposure to toxic levels of pesticides.
• Vehicle maintenance pits. Proper ventilation prevents asphyxiation from an accumulation of gases or vapors that are heavier than air.
Summary
If ventilation systems required for the control of hazardous air contaminants are not properly designed, installed, used and maintained, ventilation surveys performed by a competent individual may be the only means for identifying and correcting a system’s ineffectiveness. And if a system’s ineffectiveness is not identified and corrected, that could lead to the presence of air contaminants and fire/explosion hazards. Further, faulty systems may even exacerbate exposures to hazards by providing management and workers with a false sense of security.
An optimal ventilation survey technique combined with system owner/operator education is paramount to ensuring appropriate worker, facility and operations protection. What you as a manager, worker, safety professional or industrial hygiene professional don’t know about ventilation systems and surveys can result in chronic worker overexposure to air contaminants, lost productivity, liability, facility damage and interruption of operations. Make sure that your air contaminant ventilation systems are scheduled for routine ventilation surveys performed by a competent individual.
About the Author: Connie L. Muncy, CIH, CUSP, MS, REM, serves as senior health and safety administrator with AES Corp. She holds a bachelor’s degree in chemistry from Wright State University and a master’s degree in environmental, safety and health management from the University of Findlay. Muncy is assistant administrator of ASSE’s Utilities Practice Specialty, has published several articles in peer-reviewed technical publications and is a frequent conference speaker. She also has been the recipient of a number of awards, including an ASSE Chapter Safety Professional of the Year award.