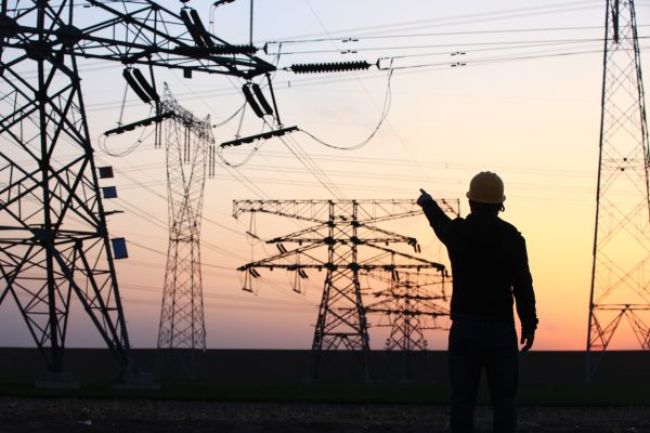
Employee-in-Charge Requirements
EICs have an important responsibility that requires a plan for success.
When was the last time your organization discussed or highlighted the importance of the employee in charge (EIC)? The EIC has the responsibility to ensure job site success, so it is one of the most important job functions within your company. And because electric power workers perform jobs with extremely high-risk hazards that require successful planning and execution, organizations must assess whether they have equipped employees with the knowledge, skills, tools, responsibility and accountability required to successfully implement EIC duties.
The electric power industry continues to experience serious injuries and fatalities (SIFs). Many times, organizations plan work as imagined, but the actual work that must be performed can turn out to be very different. Many SIFs can be linked to weak or no job site planning based on actual work at the job site.
Some questions that you may need to ask within your organization include:
- Do all operational employees know how to implement EIC duties?
- How often do you review the importance of ensuring each job site has an EIC?
- What type of training do you provide?
- Do you feel your team has an opportunity to improve?
NESC and OSHA
Although it should be a no-brainer to have someone on each job site who is responsible and accountable for making decisions, OSHA and consensus standards make it a point to require an EIC on all job sites. The National Electrical Safety Code C2-2023 states that a “designated person shall be in charge of the operation of the equipment and lines and shall be responsible for their safe operation.” Further, it states that if “more than one person is engaged in work on or in the vicinity of the same equipment or line, one person shall be designated as in charge of the work to be performed. Where there are separate work locations, one person may be designated at each location.”
OSHA electric power standards (see 29 CFR 1910.269 and 1926 Subpart V) describe EIC duties throughout the preamble and the standards. Job briefings and de-energizing lines and equipment for employee protection are two major areas of EIC responsibility. Both areas focus heavily on planning and execution, so it is important to ensure an understanding of these rule requirements.
OSHA 1910.269(c) and 1926.952, both titled “Job briefing,” require the employer to ensure that the EIC conducts a job briefing with the employees involved before they start each job. A job briefing sets the stage for effective job planning and execution, so an effective briefing process helps ensure EIC success. The EIC must understand work and task completion requirements along with hazard identification and development of effective controls. This is an extremely important area as it targets the planning that must be successful for the work to be successful.
EIC Qualification
Many organizations define the EIC as the supervisor or the crew leader, but this may not be effective when you consider that some job sites may have neither. If a job site does not have an assigned supervisor or crew leader, an EIC may be at the same skill level as others on the site. It can be challenging for employees to adhere to EIC rules when they all have the same job classification, particularly if their organization is not regularly discussing the requirement to assign one qualified employee to oversee each job.
Additionally, organizations must understand that having a supervisor or crew leader on a job site does not mean the EIC duties are being performed. Some organizations provide frontline leadership training, and others promote employees to these positions without providing any leadership training. The EIC position is a leadership role, and without training and an understanding of required expectations, success likely will not occur. Just because an employee is a good worker does not mean they have the skills necessary to successfully plan jobs, make decisions and lead employees.
At a minimum, EICs must communicate effectively; develop job site plans; know the required rules and ensure compliance; assure work is performed correctly and safely; and ensure everyone is working as a team.
For these duties to be executed properly, an organization must have an effective process to train and qualify EICs, as well as a method to assess the effectiveness of the process. Qualification should be based on demonstrated proficiency. An EIC process should also align with other apprenticeship programs within your organization because successful leaders learn and grow continually, much like a journeyman lineman and others do throughout their career.
EIC Improvements
Do you feel your team has an opportunity to improve? Organizations that want to improve EIC effectiveness on job sites should develop implementation plans based on these key items, at a minimum:
- Acknowledge the importance of EIC job duties.
- Involve employees in EIC decisions and plan development. How can we accomplish exceptional job site planning and execution?
- Regularly communicate EIC expectations and request feedback.
- Provide EIC training and qualification, and provide regular coaching for success.
- Observe what is working and what isn’t. Use key performance indicators to track performance.
- Improve EIC processes based on specific, measurable, achievable, reasonable and timely (SMART) principles. Begin the cycle again once improvement occurs.
Summary
EICs have an important responsibility, and it requires a plan for success. The plan must go far beyond appointing someone responsible without equipping them with the necessary skills. Organizations are obligated to develop EICs who are knowledgeable and understand their role in effective job planning, decision making, leading others and controlling job sites.
About the Author: Pam Tompkins, CUSP, CSP, is president and CEO of SET Solutions LLC. She is a 40-year veteran of the electric utility industry, a founding member of the Utility Safety & Ops Leadership Network and past chair of the USOLN executive board. Tompkins worked in the utility industry for over 20 years and has provided electric power safety consulting for the last 20-plus years. An OSHA-authorized instructor, she has supported utilities, contractors and other organizations operating electric power systems in designing and maintaining safety improvement methods and strategies for organizational excellence.
- Understanding Task-Specific Training
- Be Prepared for the ‘Big One’
- The Art of Safety – Unnormalizing Deviation
- October-November 2023 Q&A
- Direct Current Hazards and Protection Strategies
- Employee-in-Charge Requirements
- Using Flame-Resistant and Arc-Rated Clothing to Mitigate Cold Stress
- Nurturing Strong Leadership: An Approach to Professional Development in Skilled Trades
- New 2023 Products to Watch