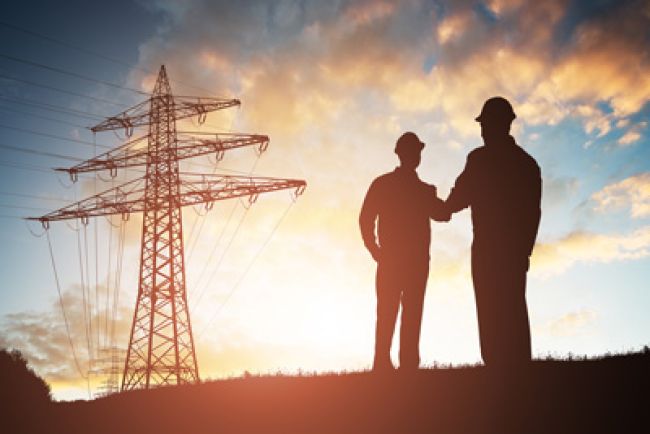
How to Develop a Contractor Safety Management Standard
Have you ever questioned whether a contractor or subcontractor was qualified to perform electric power work? If so, you should consider developing a contractor safety management standard. This type of standard defines minimum safety requirements that contractors must adhere to when they perform work for your company.
Years ago, many electric power organizations used contractual language and a hands-off approach to establish contractor safety responsibilities. In fact, organizations hired contractors to perform work they felt was unsafe because they knew the contractor would do whatever it took to complete the job. These work practices have significantly changed throughout organizations that recognize employers share responsibility for working conditions and safety at multiemployer worksites. Utilities and contractors are adopting a shared commitment to worker and system safety within their organizations.
Regulatory Requirements
In the preamble to 29 CFR 1910.269 – the electric power generation, transmission and distribution standard – OSHA states the following: “When OSHA promulgates new safety and health standards, it does so against this background principle that employers share responsibility for working conditions, and thus for OSHA compliance, at multiemployer worksites. Therefore, when the Agency issues a new safety or health standard, it is with the intention that creating, exposing, and controlling employers at multiemployer worksites will exercise their respective responsibilities to ensure that affected employees are protected as required by the standard.”
Given that statement in the 1910.269 preamble, two regulatory areas to include in your standard development discussions should be:
- OSHA’s Multi-Employer Citation Policy, CPL 02-00-124 (see www.osha.gov/pls/oshaweb/owadisp.show_document?p_table=DIRECTIVES&p_id=2024).
- 29 CFR 1910.269(a)(3), “Information transfer,” or 29 CFR 1926.950(c), “Information transfer.”
Basic Components
It may be prudent to contact a utility or contractor with an existing contractor safety management standard to better understand what’s included and how the standard is applied. Another good resource to consider is Edison Electric Institute’s Model Contractor Safety Program Guidelines. These guidelines identify the following four basic components of a successful contractor safety program:
- Pre-qualification requirements
- Contract terms
- Safety oversight requirements
- Safety performance evaluation
Let’s take a closer look at each of these components to determine what they should include.
Pre-Qualification
Are you willing to hire contractors that have had multiple fatalities, serious OSHA citations, high incident statistics and/or are not qualified to perform electric power work? If not, then it is important to outline what is acceptable and not acceptable for contractor performance before a contractor can bid on future work.
Pre-qualification involves a review of the contractor’s past safety performance to ensure it aligns with your expectations for future work. Prime contractors and subcontractors should always be included in the pre-qualification review process. Many utilities require prime contractors to furnish a list of subcontractors that have met pre-qualification requirements before they can perform work.
There are several ways to manage a pre-qualification review. An in-house review can be performed using a pre-qualification application and a contractor management specialist who will accept or deny the application based on acceptable guidelines. Also, third-party pre-qualifying companies collect required data and report whether the performance data is acceptable or needs improvement. Many electric power organizations elect to use third parties due to the amount of contract work and the time involved to research and maintain pre-qualification status. At a minimum, the following areas should be considered during the pre-qualification process:
- Number of fatalities and serious incidents.
- Experience modification rate – recent year certificate.
- OSHA citations – number of OSHA citations over the past three to five years.
- Total recordable incident rate – numbers over the last three years.
- Days away from work, days of restricted work activity and/or days of job transfer – numbers over the last three years.
- Written safety manual for the type of work performed.
Contract Terms
During the contract submittal process, the contractor should describe in advance how they will establish, manage and control safety, reliability and quality as terms of the contract. Your company may have multiple types of contracts for specific work projects or for extended work involving multiple projects. In either case, it is important to include your legal staff in the development of all contract terms. This may be a good time to ensure legal staff has working knowledge of OSHA multiemployer worksites and information sharing requirements, especially if they do specialize in OSHA law.
Unfortunately, many contracts only outline insurance requirements and a few basic safety requirements. Set the stage for what you require in advance so the contractor can summarize how they will ensure your requirements are met. Consider including the following elements at a minimum:
- Contractor safety performance expectations: written safety policies, requirements for site-specific safety plans, safety program oversight, electric power qualification, incident prevention methods, incident reporting and corrective action plans.
- Contractor responsibility and accountability for subcontractors: vetting and on-site notification, information sharing requirements, electric power qualification, safety program and rules, safety performance and safety oversight.
Safety Oversight Requirements
Safety oversight requirements will establish how the contractor is going to do what they said they would do and how the utility is going to establish responsibility and accountability.
Let’s revisit the initial question in this article: How do I know a contractor or subcontractor is qualified to perform electric power work? Now is the time to answer this question. Request a copy of the contractor’s qualification document outlining demonstrated proficiency. Think of it as an accountability system to ensure the contractor has a process in place and can furnish the documentation upon request.
Contractor and utility oversight requirements are two areas to include in your contractor safety management standard. Following are major areas to include in the contractor oversight requirements:
- Safety resources: site safety support, safety meetings, leading and lagging safety indicators, and information transfer.
- Safety training: safety orientations, OSHA-required training, electric power qualification, subcontractor training verification and OTI 10-/30-hour training.
- Risk assessment: job hazard analyses, job briefings, and safety defenses and controls.
- Safety audits and inspections: audits/observations of work and inspections.
- Safety performance reviews: leading and lagging indicator reporting, compliance trends and post-review.
- Incident investigations: root cause analyses, lessons learned, safety stand-downs and corrective actions.
Major areas to include in your utility oversight requirements are document review, providing OSHA information sharing requirements, performing on-site observations, and developing performance feedback and action plans. Utility personnel can be used to perform utility oversight, or a third-party company may be utilized. In either case, the process needs to be defined and personnel must be allocated to perform these tasks.
Safety Performance Evaluation
Safety performance evaluation is a process developed to communicate and evaluate performance, monitor and track results, and provide performance feedback with action plans.
What happens if a contractor is not meeting your expectations, or if the contractor violated the contract and/or items outlined in the contractor oversight requirements? This component should clearly address methods to identify and communicate violations along with the process for developing improvement and action plans to ensure the violations are corrected. It is important to link improvement and action plans to a risk matrix to ensure timely correction for high-risk violations. Major areas to include in safety performance evaluations are:
- Key performance indicators: establish safety and performance rules, identify schedule of audits and investigations, define consequences of exceeding key performance indicators and define triggers that cause concern (safety rule violations, serious incidents, no safety meetings, no audits, poor job briefings, no training, no qualifications).
- Results monitoring and tracking: develop schedule, including rapid follow-up.
- Performance feedback: notification process, action plans to address and follow up on deficiencies.
Summary
These four components – pre-qualification requirements, contract terms, safety oversight requirements and safety performance evaluation – are critical to an effective contractor safety management standard. During development of the standard, it is important to include, at a minimum, safety professionals, line management, contract management, engineering, procurement, legal and senior management. Each of these groups needs to fully understand and buy in to the process. Also, implementation of the standard takes time and resources to provide training, management and oversight. A strong commitment from senior management must be in place to ensure success.
Whether you are a utility or a contractor hiring subcontractors, you can benefit by developing and implementing a contractor safety management standard. The major benefit is knowing all employers on multiemployer worksites understand their safety responsibilities and are held accountable to provide a safe workplace for all employees.
About the Author: Pam Tompkins, CSP, CUSA, CUSP, is president and CEO of SET Solutions and a 39-year veteran of the electric utility industry. She is a founding member of the Utility Safety & Ops Leadership Network and presently serves on the executive board. Tompkins has authored and presented technical papers on high-voltage electrical safety issues at iP conferences, IEEE workshops, ASSE conferences and for many other organizations. She is an OSHA-authorized instructor who specializes in helping electric power organizations in the U.S. and abroad comply with today’s safety and training requirements.