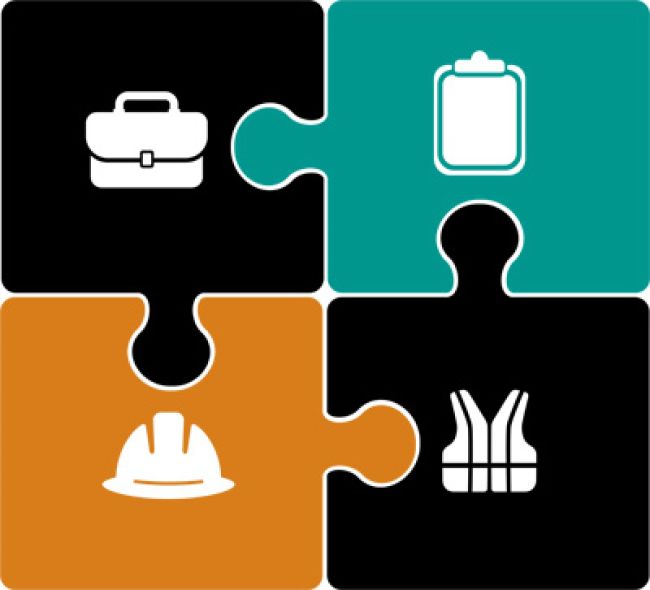
Organizational Safety Roles and Responsibilities
Safety personnel are not the only individuals responsible for safety in an organization. Executive management, operations management and workers also have roles to play in establishing and maintaining a safe working environment.
However, specific roles and responsibilities for each of these groups are not always understood, and they may never have been introduced. This means there may be employees in an organization who do not realize how vital their influence can be on safety – for better or for worse.
The four groups listed below typically comprise a safety team; your organization’s team may vary somewhat. Each group has a specific role and responsibilities for safety in their workplace, as well as some common responsibilities that they share as part of the safety team.
- Executive management are owners, presidents, CEOs and the like. They are the final decision-makers.
- Operations management are operations managers, project managers, supervisors and foremen. These individuals usually are overseers of an organization’s projects, jobs, crews and/or workers.
- Workers are those directly involved in the day-to-day work of the company.
- Safety personnel are those employees dedicated to providing safety support.
For the benefit of overall safety, each group must understand and embrace their roles and responsibilities, work synergistically and consider themselves safety leaders. The remainder of this article will explore the roles and responsibilities of each group mentioned above, plus the common responsibilities of the safety team as well as the common responsibilities of executive and operations management.
Common Responsibilities of the Safety Team
Following are seven common responsibilities of the safety team. While they may seem obvious, not all of them are known, understood or taken on by team members, yet it’s extremely important that an organization’s safety team members speak the same language regarding safety.
- Focus on learning. There should be a continuous, conscious effort to learn and improve. We learn from four distinct areas:
- Failure: This is one of the most common ways we learn because when something goes wrong, we must fix it.
- Near misses: A near miss can be defined as an unexpected event that occurred outside the identified hazards and planned work procedure, but during which no one was injured and no property was damaged.
- Positive work experiences: These occur when employees work within the established and known safety expectations, getting the job done without incident.
- Observations: During observations, attention is paid to work habits and management abilities, including attitude and behavior. Observers learn by asking questions such as, what is going well and meeting expectations? Are there safety gaps that need to be addressed? Are known safe work practices being followed? Are the tools and equipment appropriate for the task? Are workers properly trained?
- Be committed. Each member of the safety team must be committed to being the leader they are expected to be, which includes consistently demonstrating a good attitude and appropriate behavior as well as being transparent and accountable.
- Communicate. Make sure those you lead understand the expectation for safety, and be humble and concerned enough to listen to them when they communicate with you. Effective communication leads to learning, understanding and improvement by all parties.
- Embrace consistency. Be consistent in all areas of your responsibilities as consistency leads to sustainable habits regardless of your role.
- Be understanding and tolerant. People will make mistakes. An error can be an opportunity to identify safety gaps and improve working behaviors. Of course, how long an organization tolerates certain mistakes is based on numerous factors, including whether or not the individual who made the error made a conscious decision to ignore a known safety expectation.
- Have patience. When it comes to change, whether initiated by proactive or reactive inspiration, it may take time for some employees to understand and embrace the “new” or “improved.” Even attitude and behavior changes require patience. Change takes time.
- Follow through. If you say you are going to do something, do it; that proves you mean what you say and helps build trust. But before you say you will do something, first be sure you can deliver.
Common Responsibilities of Executive and Operations Management
I once read a wonderful article in the Journal of Safety Research entitled “High Reliability Process Industries: Individual, Micro, and Macro Organizational Influences on Safety Performance.” The article included this quote: “… management attitudes and behavior are critical components towards safety, permeating down through the organization to the workforce.” Essentially, management sets the tone for what will be expected and tolerated regarding safety in the organization. With that in mind, both executive and operations managers have three common safety responsibilities.
- Respond to failure. Put in the work to determine the causes of a failure, no matter the severity or consequence. You may identify gaps that could lead to improved working conditions and/or management abilities.
- Lead with the appropriate demeanor. As a manager, how you respond to safety requirements – whether verbally or physically through facial expressions and body language – communicates your interest in safety to those you lead. It also gives those you lead permission to respond in a like manner. Choose your demeanor wisely.
- Celebrate victories of all sizes. Doing so encourages and inspires those you lead to continue the effort to meet safety expectations. Always keep an eye out for opportunities to applaud employee efforts.
The level of importance executive and operations management personnel place on worker safety has a direct impact on the entire organization. Managing from a spreadsheet does not fully consider the human aspect of the work being done. While the financial health of the organization should be considered, the health of workers must take precedence.
Executive Management Responsibilities
Now that we’ve looked at the common responsibilities of the safety team and executive and operations management personnel, let’s delve into the roles and responsibilities of each of the four groups referenced at the beginning of the article. We’ll start with executive management personnel, who have the following two important obligations.
- Care. Before anything else, you must care about those who work for and with you. There is a difference between an employee and a person. When you consider someone an employee, the implication is that they are replaceable, like a tool or machine. When you consider someone a person, you are more likely to see them as an individual who has value and meaning. Humans are not replaceable, and they deserve a safe working environment – which an employer, by law, is required to provide.
- Culture. Setting the organization’s cultural expectations means establishing the overall expectations for safety within the organization, and then providing the means for maintaining those expectations.
Operations Management Responsibilities
Operations management personnel – such as field supervisors and foremen – are considered by some to be the gatekeepers to a successful safety environment because they typically spend the most time with employees charged with doing the work. And like it or not, if you are an operations manager, you lead by example based on what you say or don’t say and what you do or don’t do. Following are four responsibilities of anyone in an operations management role.
- Evaluate. Keep production, quality and safety in mind when planning a job or task. Observe the people you lead to make sure they understand their jobs and can perform them effectively. Confirm they have the appropriate training before any work begins.
- Ensure. Make sure the people you supervise understand the hazards associated with the work to be performed, the safety requirements that apply, the proper procedures to be followed and the appropriate equipment needed to safely perform the work.
- Engage. Communicate effectively and consistently so that the people you lead fully understand what is expected of them. Create an environment in which everyone is empowered to ask questions, make recommendations and respectfully remind other employees, including managers, when a safety correction needs to be made.
- Enforce. This isn’t a dirty word. It simply means making sure the people you lead are following all safety expectations. If they are not, it is your obligation to work with them to make the necessary corrections.
Worker Responsibilities
Under the leadership and guidance of executive management and operations management personnel, workers have three responsibilities:
- Determine. They must be sure that they fully understand their tasks before starting, especially any associated hazards.
- Decide. They must decide if they have the training, knowledge, tools, PPE, equipment and time to complete their tasks safely.
- Do. They must use the right tools and equipment and follow the appropriate safety procedures to complete their tasks. Workers are obligated to communicate when necessities for safety are not available, when they have ideas for improvement and when they identify opportunities for correction.
Safety Personnel Responsibilities
Last but certainly not least, an organization’s safety personnel – those charged with providing safety support – have the following four responsibilities:
- See. They must identify gaps in the safety management system, which includes training, leadership and required programs. Also, safety personnel are responsible for identifying hazards and confirming that proper risk control measures are understood and followed.
- Say. They must provide guidance on how, when and why to meet safety expectations. Safety personnel also must make corrections when necessary and communicate what has gone well to workers and management.
- Support. They must support each aspect of the safety team, particularly the workers, to ensure a safe working environment.
- Safety leader creed. They must conduct themselves in a safe, professional, respectful and responsible manner while being a strong example of attitude, behavior, accountability and transparency.
Summary
Effort is the only link between desire and achievement. If you desire to have a safety culture and a safety management system that truly provide a safe working environment, it will necessitate effort on everyone’s part. Part of that effort requires that each member of the safety team understands their safety role and how to successfully carry out their responsibilities. Additionally, when everyone on the safety team knows and understands the roles and responsibilities of everyone else on the team, synergy will be enhanced, and you will be more likely to achieve your goal of establishing and maintaining a safe working environment.
About the Author: Michael Kleinpeter, M.Eng., CUSP, CHST, has been a construction safety manager for 19 years in the Dallas-Fort Worth area. He also is the author of “The Right Way,” from which this article is excerpted. Reach Kleinpeter at mike@advancedsafetymanagement.com.