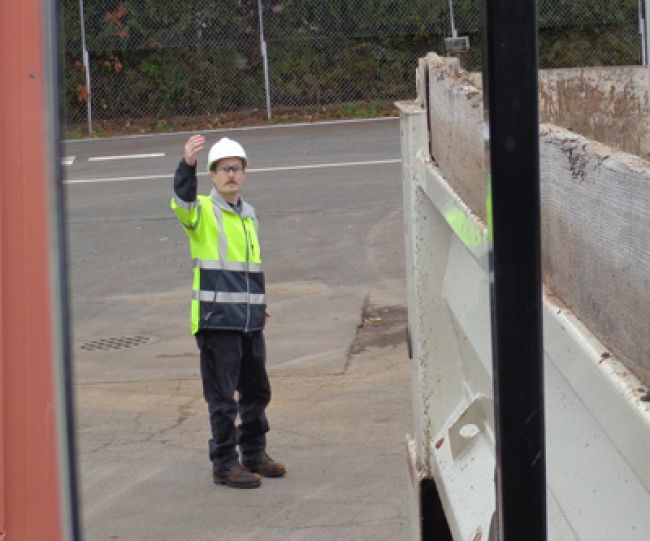
Controlling Struck-By Hazards in Utility Work Zones
Struck-by hazards are one of the greatest threats to workers employed in the utility and construction industries, and thus are hazards every utility and construction company should be focused on mitigating. Typical examples of struck-by hazards include traffic passing through a work zone; vehicle and equipment movement within a work zone or construction area; rotating or swinging equipment, such as an excavator; and falling loads and tools.
Worker fatalities in work zones dropped due to the last recession, hovering around 100 fatalities per year from 2007 to 2013, but numbers are rising again as the economy strengthens and roadway work projects increase. More than 140 worker fatalities in work zones were recorded in 2016.
OSHA is the Minimum
OSHA standards establish minimum legal standards for safety programs, and many employers rely on OSHA when creating company safety plans and policies. In this particular area, it is essential to emphasize the word “minimum” because OSHA standards lag far behind current consensus standards and recognized industry safety practices. Employers committed to protecting workers from struck-by hazards must set their sights higher than the OSHA minimums, looking to ANSI consensus standards and industry practices for guidance. This article explains the current federal OSHA and industry safety practices.
Starting at the most general level, workers must be trained to recognize and avoid hazards they may encounter. This is a very broad requirement, so the employer has to carefully consider how it will apply to the work and work area. OSHA construction standard 29 CFR 1926.21(b)(2) states, “The employer shall instruct each employee in the recognition and avoidance of unsafe conditions and the regulations applicable to his work environment to control or eliminate any hazards or other exposure to illness or injury.” Struck-by hazards are unsafe conditions, and workers must be trained to recognize and avoid them.
Planning, Prevention, Control
Company policies and site-specific procedures must comply with or exceed OSHA standards. Preventing struck-by hazards starts in the planning phase, and struck-by prevention efforts must be monitored and adapted as the work site changes. Management must plan where machinery will operate, where workers will operate and how the two will safely interact – while also considering safety for the public, motorists and interested observers.
A well-marked perimeter establishes the boundary to keep the public out of harm’s way. An internal traffic control plan (ITCP) helps to avoid unintended interactions between workers and equipment. Separating workers on foot from heavy equipment and traffic through the use of barriers is the safest practice, but it’s not always possible depending on the configuration of the job site. Struck-by safety is a shared responsibility – to the extent possible, equipment operators must be trained to avoid striking workers, workers must be trained to avoid working where they can be struck, and supervisors must ensure that everyone follows their training, policies and the ITCP. Management must anticipate travel paths for workers on foot and avoid having foot traffic cross vehicle pathways where possible. Workers must be trained to make radio or eye contact with the equipment operator, and receive positive confirmation from the operator, before approaching heavy equipment.
The MUTCD
Roadway work zone safety is enforced by OSHA, and the details are found in section 6 of the Manual on Uniform Traffic Control Devices (MUTCD). OSHA construction standard 29 CFR 1926.201(a) states that signaling by flaggers (temporary traffic control), use of flaggers and garments worn by flaggers must conform to the MUTCD 1988 edition, Revision 3, or the Millennium Edition (2000). The 1988 and Millennium editions of the MUTCD are outdated; the most current MUTCD is the 2009 edition with revisions 1 and 2. Technology and consensus standards for high-visibility safety apparel (HVSA) have improved dramatically in the last 30 years. OSHA also has published compliance directive CPL 02-01-054 on how it will inspect work zones and issue citations, which can be downloaded at www.osha.gov/enforcement/directives/cpl-02-01-054. The CPL provides valuable insight into developing compliant work zone safety practices and avoiding citations. Flaggers need minimum four-hour flagger training courses, and states vary in recognizing flagger training from the National Safety Council, American Traffic Safety Services Association or both. Flagger certification typically must be refreshed every four years.
High-Visibility Safety Apparel
With regard to HVSA, the American National Standard for High-Visibility Safety Apparel and Accessories, ANSI/ISEA 107-2015, is the go-to reference document. Workers exposed to roadway traffic must wear at least ANSI performance Class 2 high-visibility garments, and those working on interstate highways must wear an ensemble that meets ANSI performance Class 3 requirements. In the latest version of the standard, HVSA garments are now also categorized as Type O (off-road), Type R (roadway) and Type P (public safety).
There is no specific OSHA standard for non-roadway struck-by hazards, but the hazards are recognized in various industries, and the OSHA General Duty Clause applies. OSHA 29 CFR 1910.132(d)(1) requires the employer to “assess the workplace to determine if hazards are present, or are likely to be present, which necessitate the use of personal protective equipment (PPE).” The ANSI/ISEA 107-2015 standard refers to HVSA as PPE, and responsible employers are requiring workers to wear high-visibility garments due to struck-by hazards in the utility yard and on the job site, reducing risk by increasing conspicuity.
Backup Alarms and Spotters
OSHA 29 CFR 1926.601(b)(4) states, “No employer shall use any motor vehicle equipment having an obstructed view to the rear unless (i) the vehicle has a reverse signal alarm audible above the surrounding noise level or (ii) the vehicle is backed up only when an observer signals that it is safe to do so.” The standard may appear to offer two equal choices – that is, the employer can choose to use either a backup alarm or an observer, with no preference or weight given to either. Backup alarm is listed first, which may give an impression that it is the preferred choice, leaving the observer or spotter as the lesser alternative. The reality is that when view to the rear is obstructed, proper use of an observer is a far safer choice than relying on a backup alarm alone. Despite wide use of backup alarms, workers are still struck, injured and killed by reversing vehicles and equipment. Workers on foot can become accustomed to frequent backup alarm sounds from equipment around them. So, where is the guidance for proper use of a spotter?
National Consensus Standard on Proper Use of Spotters
ANSI A10.47-2015, “Work Zone Safety for Highway Construction,” is the current reference for safe use of spotters. It offers detailed guidance on backing construction vehicles and equipment in the presence of workers on foot. While it is grouped with the A10 construction standards, the principles apply wherever heavy equipment and people on foot interact.
Drivers and spotters must agree on the meaning of hand signals, and radio communication is preferred in addition to hand signals. Inexpensive two-way Family Radio Service radios can be used for this purpose. One spotter should be directly tasked with safely backing the vehicle or equipment, and should have no other duties that interfere. Spotters need to be trained to perform their duties safely and consistently without distractions; must not stand in the path of the vehicle or equipment; must wear HVSA; and must remain in the driver’s line of sight at all times. Spotters must not walk backward while directing the vehicle or equipment, since a trip or slip could put them in harm’s way. For longer maneuvers, the spotter should take a position, direct the vehicle or equipment to a reasonable point, stop the vehicle or equipment while the spotter relocates, then resume directing.
Vehicle or equipment operators also must be trained on how to work safely with a spotter; keep the spotter in view at all times; obey the spotter’s signals; keep glass and mirrors clean and in good repair; and immediately stop if they lose sight of the spotter. The driver and spotter need to agree on where the spotter will move during complex maneuvers with limited sightlines – such as cresting a hill or making a three-point turn.
Obstructed View
OSHA issued a memo in 1987 to explain how they define “obstructed view” (see www.osha.gov/laws-regs/standardinterpretations/1987-01-21). According to the memo, “A simple interpretation would be ‘anything’ that would ‘blockout’ (interfere) with the overall view of the operator of the vehicle to the rear of the vehicle, at ground level. ‘Obstructed view to the rear’ could include such obstacles as any part of the vehicle such as structural members, its load (gravel, dirt, rip-rap), its height relative to ground level viewing, damage to windows or side mirrors, etc. used for rearview movement of the vehicle; in addition, it could include restricted visibility due to weather conditions such as heavy fog; or work being done after dark, without proper lighting.” In short, if there is any interference with the operator’s view to the rear, assistance is needed while backing. In decreasing order of effectiveness, that assistance could be a spotter keeping eyes on the path to be traveled, one or multiple rearview cameras, rear-facing sensors or a backup alarm.
Training
The American Road & Transportation Builders Association (www.artba.org) offers a four-hour course on preventing runover and backover incidents. The American Traffic Safety Services Association (www.atssa.com/TrainingCertification/CourseInformation.aspx) offers work zone traffic control technician and traffic control supervisor training throughout the United States.
Summary
Struck-by hazards in the utility and construction industries can be controlled. That control comes about through management commitment to safety, strong policies and procedures, worker training, high-visibility garments (HVSA), proper use of spotters, and technology such as cameras, sensors and backup alarms.
About the Author: Chip Darius, CUSP, OHST, CET, CSHO, is founder and president of Safety Priority Consultants LLC (www.safetypriority.com). He has provided safety consulting and training services to construction, utility and general industry clients since 1991. Darius serves on the AGC of America Health & Safety Committee and is frequently called upon as an expert witness in safety-related legal matters.