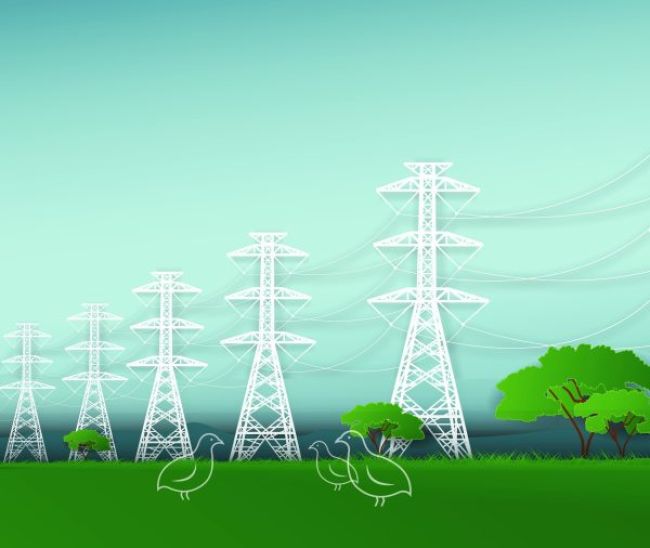
The Quail Effect: An Indicator of Safety Culture
Explore these strategies that can help to improve relationships between safety personnel and field workers in your organization.
It is not uncommon for a flock of birds, such as quail, to scatter when people get too close to them. This sometimes happens on work sites, too, but instead of birds, it’s workers who scatter when they see safety personnel show up on their job site.
A lot can be said about an organization’s safety culture by observing how employees in the field respond to the arrival of safety personnel. Think about it: Do your crews run for cover when they see Safety arrive at the job site? Do they suddenly go on break until Safety leaves? If so, this typically indicates a problem with the organization’s safety culture. But what can you do to change the culture? How do safety personnel overcome this challenge?
In my opinion, the answer is easy – get back to the basics by treating people with respect and dignity and working to get their buy-in – but the road is complex. This article focuses on some strategies that can be used to establish good relationships between Safety and other personnel within an organization. I have found that they work well, although they may need a little tweaking to fit your specific needs.
Initial Field Visits
The first strategy begins with learning the organization’s work practices as well as its safety policies and procedures. Take the time to conduct an evaluation of your safety program. Learn how employees perform work and compare that to established procedures. During your evaluation, spend time visiting crews, reviewing policies and procedures, and taking notes. This is not an uncommon approach for many safety professionals. After all, how can you be expected to change hearts and minds within an organization if you don’t know what is going on? You must first establish trust and credibility.
The trick is not to use a sledgehammer. Treat every encounter as an opportunity to learn from the crews while also teaching them something about safety. When observing less than desirable safety practices, do not overcriticize. Ask the person you’re observing to tell you about the job they are doing and have them explain the process. Hear them out – truly listen – and then inquire about the safety considerations they took when planning the job. Even better, ask what they spoke about during their tailboard or job site assessment. This conversation should not be used to point out flaws in their process but to lead them to reassess the job and develop safer ways of accomplishing the task. Of course, you can also use this time to tell them about what you observed and ask them if they think there is a safer way to perform the task. This provides an opportunity for you to recommend courses of action they can take. Remember, the purpose of these initial field visits is to learn how the organization works and to gain trust among workers.
You may have noticed there’s been no discussion so far about enforcing safety policies and procedures. We’ll get to that soon. But first, I want to emphasize the importance and meaning behind leading workers to recognize unsafe acts, behaviors and conditions. During an initial field visit, you can help to keep workers safe through observations and conversations while also gaining a greater understanding of the organization’s work practices and safety culture.
When you first start visiting crews in the field, yes, they may “quail” on you. It is only through being humble and gaining trust that you become part of the team. It is also important to communicate the value of the work the crew is doing. Explain the positive impact that they have within the organization and that they are the ones who can effect real change in the safety culture. Encourage them to own safety and take pride in ownership. This will take time and patience, but eventually crews will no longer flee when they see you, and they may even welcome you on the job site to witness how well-prepared they are and how they safely address hazards. Of course, workers will still make mistakes, but very seldom will they repeat them. Through trust, you will likely be able to lead them to a point where they want to learn from you.
Enforcement
Now, let’s talk about enforcement. Enforcing safety policies and standards should not be a complex process, but sometimes we make it one. For example, let’s say that during an incident investigation, you interview a supervisor who tells you that they will be issuing a written warning to the person involved in the incident for not following company policy. Be certain to ask for a copy of the policy that was violated and any documentation that shows personnel were trained on the relevant policies and procedures. This is to help complete a root cause analysis and identify opportunities for improvement to prevent a recurrence. But what if you are told by the supervisor that there is no written policy or procedure? Take a moment to ask how the supervisor knew the person involved understood the policy or procedure. Get them thinking about the need for written procedures and training records as one means to prevent incidents, and then confirm whether the person did or did not violate the policy. Remember, before you can enforce a policy, procedure or standard, you must first ensure it exists in writing and that all personnel have been trained to understand it.
How does one effectively enforce safety in the workplace? By being fair and consistent. Ideally, if your organization has a strong safety culture, employees at all levels will police themselves, meaning they look out for each other and make on-the-spot corrections when someone deviates from a safety policy or procedure. This type of enforcement is the most desirable but also the hardest to achieve. In my experience, the only way to achieve it is through trust.
Frontline supervisors are key to ensuring all personnel go home safely. They have a huge responsibility for safety that may sometimes conflict with operational production. This is why we as safety professionals must ensure frontline supervisors understand how safety affects quality and production. This can be done in various ways. One way is through quarterly supervisor safety meetings during which you highlight an incident and how it impacted operations.
Achieving Buy-In
How do you achieve employee buy-in of a safety program? It starts at the top. Senior leadership must demonstrate their own buy-in; this is the key element in creating a positive safety culture. Without management buy-in, employees will simply go through the motions and then default to what they have always done. Another way to gain buy-in is to train employees to make safety decisions, empowering them to act, and to incorporate their suggestions into the organization’s safety program. Not all suggestions will be practical, but you must treat each of them with the same enthusiasm and recognize the individual for supporting the safety program.
Still another way to obtain buy-in is to involve employees in the development of corrective actions and solutions. After all, it is difficult not to embrace a policy or procedure you helped create. In addition, during root cause analyses, identify and use subject matter experts from within the organization. Who can better identify improvement opportunities and solutions than the experts?
What about adopting a meaningful safety slogan that can be incorporated in all aspects of the organization? This is another option you can take advantage of. Ask employees to submit suggestions for a safety slogan, and then work with the safety committee to identify the top three to five submissions. You can then have all workers within the organization vote on which slogan has the most meaning to them. Once a slogan has been adopted, make it a big deal. You may be surprised by the amount of worker participation.
Lastly, the safety committee can be an important factor in obtaining employee buy-in. Consider making it an employee-driven committee, not one owned and run by management or the safety department. You will still need to have some type of oversight, but it should largely be the employees’ program. They set the agenda and determine what actions to take and what recommendations need to be made to management. At least one member of the safety department should attend each committee meeting as a subject matter expert. This type of safety committee helps employees realize how much they can actually affect – and it helps to reinforce their buy-in.
Following Through
Everything you do as a safety professional requires follow-through; you must do what you say you are going to do and evaluate your actions and program. One area of emphasis to consider is that you must follow through on employee buy-in. How long will it last if you do not keep employees engaged? This is the tricky part; when all is quiet, we may think things are going well or as planned. That could be the case, but if we are not engaged in safety at some level, employees might perceive the organization has lost interest – and then they might lose interest, too.
Conclusion
The methods and strategies I’ve included in this article are ones that have worked for me as I’ve strived to improve the safety culture within my organization. You may or may not find success by using these techniques, but if you do not try any of them, you will never know.
About the Author: Joshua Reilly, SMS, CIT, CUSP, is a safety manager at Electrical District No. 3 of Pinal County in Arizona. He earned his bachelor’s degree in occupational safety and health from Columbia Southern University. In 2015, after 26 years of service, Reilly retired from the U.S. Army as a Chief Warrant Officer 3, with specialties in maintenance management and safety.