Days
:
Hours
:
Minutes
:
Seconds
iPi Monthly Forum for Utility Professionals
The iPi monthly forum is where you can get answers to questions you have from subject matter experts like David McPeak, Jim Vaughn, Danny Raines and other utility safety and ops professionals like yourself. Forums will include industry specific topics, challenges, trends, and solutions along with best practices in leadership, operations, and safety.
KNOWLEDGE, INSIGHT AND STRATEGY FOR UTILITY SAFETY & OPS PROFESSIONALS
Rather than overcomplicating PPE decisions, invest time in safety through design to minimize the likelihood of an arc event.
Accuracies are synonymous with safety and science. While many perceive that electrical safety needs to be highly exact, this article aims at creating awareness of why sticking to the basics is effective. But before we delve into variability in electrical engineering, safe electrical work practices and electrical PPE, here is a brief story my second-year […]
More News…
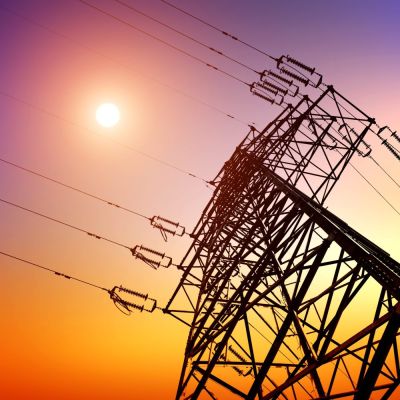
When safety is a true organizational value, employees are more likely to adhere to standards, perform quality work and be more productive.
Built In, Not Bolted On: Using Safety to Drive Operational Excellence
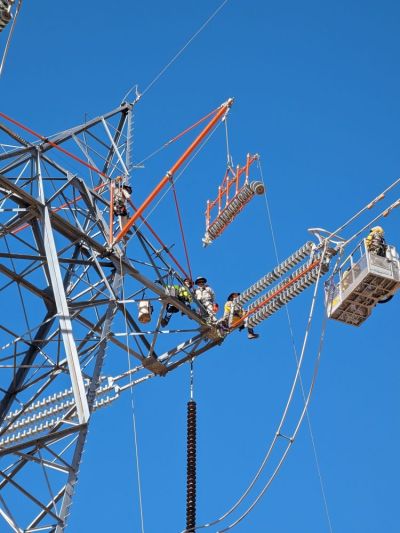
Effective worker protection demands precise equipment selection, thorough worker training and well-rehearsed rescue procedures.
Beyond the ABCs: Fall Protection for Unique Tasks
Holistic worker wellness isn’t a passing trend – it’s a critical component of workplace safety and strong organizational performance.
Making the Safety Connection: The Impact of Total Well-Being in the Workplace
Utility workers perform essential tasks that touch millions of lives every day. The critical nature of the services they provide coupled with the perilous nature of their tasks exposes these workers to life-threatening hazards. This is why the industry highly values and prioritizes safety.
Many utility companies operating today have made significant strides in improving their safety culture. Crit…
A layered approach that includes FR/AR undergarments can enhance worker safety, comfort and compliance.
Optimizing Arc Flash Protection: The Crucial Role of Layered Clothing
Given the arc flash hazards and other risks that exist in electric utility work environments, an employer’s commitment to employee safety must never falter. It is essential for workers to wear personal protective equipment in these environments; in particular, prior to exposure, workers must don flame-resistant (FR) or arc-rated (AR) garments that meet or exceed assessed incident energy levels.
A…
Bucket Truck Safety: OSHA Standards and Other Considerations
I receive numerous and varied questions about the safe use of bucket trucks in electric utility operations, so in this installment of “Voice of Experience,” I am going to share with you the OSHA standards you need to know as well as some things I have discovered during observations and audits of fi…
June-July 2025 Q&A
Q: Can you direct us to information regarding “fuzzing” or “noisy tester” voltage detectors? We’ve heard that with noisy testers, there’s potential for both false negatives (no voltage is detected although it’s present) and false positives (voltage is indicated where none exists). We’ve also heard…
Achieving safety excellence requires thoughtful planning and a commitment to continuous improvement.
Safety By Design: Safety Management System Planning
In the first two parts of this six-part series, I discussed the importance of creating and implementing a safety management system (SMS) that actively involves all employees. This part will focus on (1) identifying and prioritizing an organization’s safety needs based on specific hazards and risks…
OSHA-Compliant Employee Training
“Yes, we are OSHA compliant. Our apprentice lineworkers are trained and certified by a local line school, which guarantees that the training they deliver meets OSHA standards. Every six months, we send the apprentices to the school for two weeks of hands-on training. They also take online classes i…
Effective worker protection demands precise equipment selection, thorough worker training and well-rehearsed rescue procedures.
Beyond the ABCs: Fall Protection for Unique Tasks
The electric transmission and distribution (T&D) industry often requires work in challenging environments. Whether crew members access tall structures by helicopter, use rope-access methods to climb lattice towers, or ride wire carts to install and maintain spacers along energized lines, their…
A growing number of utility organizations are making a shift from using traditional synthetic ropes to those with verified dielectric properties.
From Risk to Reliability: Improving Rope Safety in Energized Environments
The tools and equipment employed by electrical workers must possess the necessary insulating properties to ensure user safety. One such tool, dielectric rope, can be overlooked as a component of electrical safety, but modern standards and rigorous testing protocols are transforming the way this typ…
Rather than overcomplicating PPE decisions, invest time in safety through design to minimize the likelihood of an arc event.
Variabilities in Electrical Arc Flash Protection
Accuracies are synonymous with safety and science. While many perceive that electrical safety needs to be highly exact, this article aims at creating awareness of why sticking to the basics is effective.
But before we delve into variability in electrical engineering, safe electrical work practices…
Social Networks
Recent Posts
Featured Products
Industrial Helmets with Smart Safety Technology
Twiceme Technology, the digital safety standard for jobsites and adventures, has named Securis, a Velotec Sports industrial head protection brand, as its latest PPE partner. Securis will integrate Twiceme’s smart safety technology into its entire product line, enhancing safety for industrial worker…
Safety Management
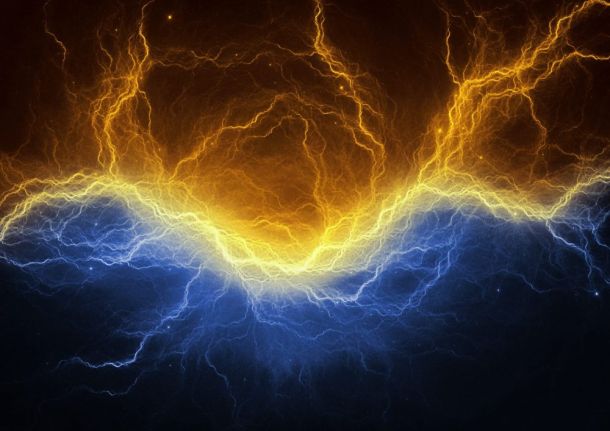
Variabilities in Electrical Arc Flash Protection
Accuracies are synonymous with safety and science. While many perceive that electrical safety needs to be highly exact, this article aims at creating awareness of why sticking to the basics is effective.
But before we delve into variability in electrical engineering, safe electrical work practices…
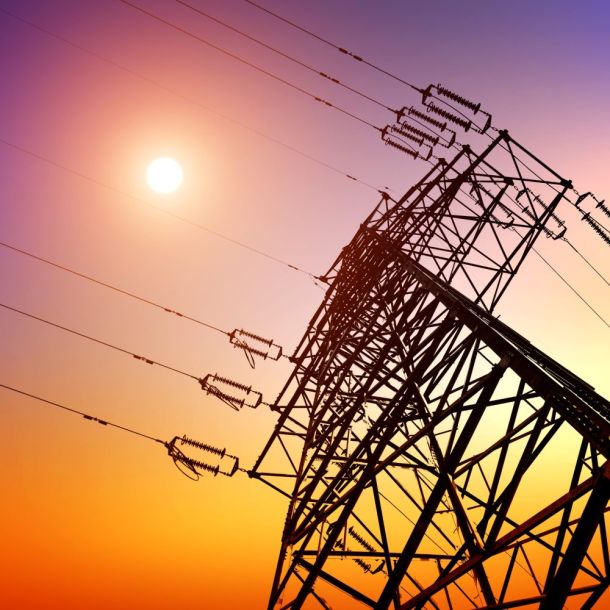
Built In, Not Bolted On: Using Safety to Drive Operational Excellence
Employers in the electric utility industry are currently working on initiatives in various areas of their businesses, including safety, quality, production, leadership, and human and organizational performance (HOP). These are important programs, but it’s unlikely they’ll fully achieve their intend…
Safety By Design: Safety Management System Planning
In the first two parts of this six-part series, I discussed the importance of creating and implementing a safety management system (SMS) that actively involves all employees. This part will focus on (1) identifying and prioritizing an organization’s safety needs based on specific hazards and risks…
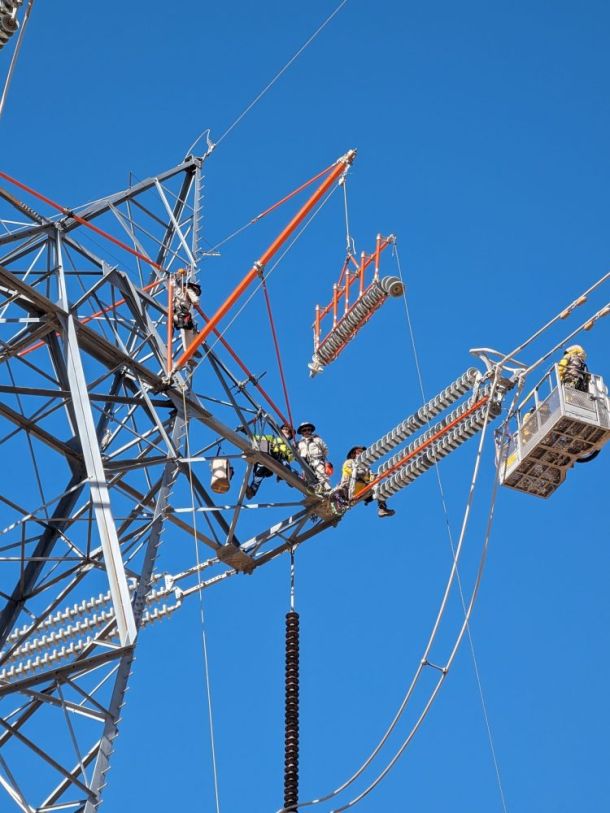
Beyond the ABCs: Fall Protection for Unique Tasks
The electric transmission and distribution (T&D) industry often requires work in challenging environments. Whether crew members access tall structures by helicopter, use rope-access methods to climb lattice towers, or ride wire carts to install and maintain spacers along energized lines, their…
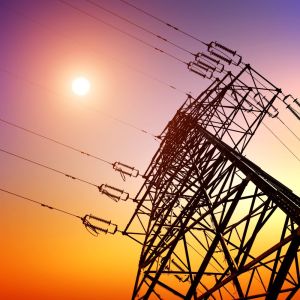
When safety is a true organizational value, employees are more likely to adhere to standards, perform quality work and be more productive.
Built In, Not Bolted On: Using Safety to Drive Operational Excellence
Employers in the electric utility industry are currently working on initiatives in various areas of their businesses, including safety, quality, production, leadership, and human and organizational performance (HOP). These are important programs, but it’s unlikely they’ll fully achieve their intend…
Achieving safety excellence requires thoughtful planning and a commitment to continuous improvement.
Safety By Design: Safety Management System Planning
In the first two parts of this six-part series, I discussed the importance of creating and implementing a safety management system (SMS) that actively involves all employees. This part will focus on (1) identifying and prioritizing an organization’s safety needs based on specific hazards and risks…
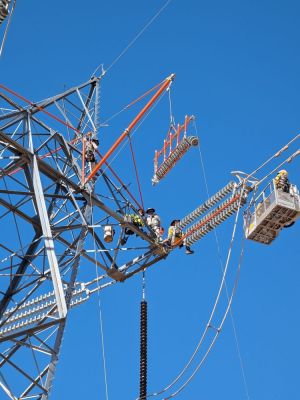
Effective worker protection demands precise equipment selection, thorough worker training and well-rehearsed rescue procedures.
Beyond the ABCs: Fall Protection for Unique Tasks
The electric transmission and distribution (T&D) industry often requires work in challenging environments. Whether crew members access tall structures by helicopter, use rope-access methods to climb lattice towers, or ride wire carts to install and maintain spacers along energized lines, their…
When safety is a true organizational value, employees are more likely to adhere to standards, perform quality work and be more productive.
Built In, Not Bolted On: Using Safety to Drive Operational Excellence
Employers in the electric utility industry are currently working on initiatives in various areas of their businesses, including safety, quality, production, leadership, and human and organizational performance (HOP). These are important programs, but it’s unlikely they’ll fully achieve their intend…
When safety is a true organizational value, employees are more likely to adhere to standards, perform quality work and be more productive.
Built In, Not Bolted On: Using Safety to Drive Operational Excellence
Employers in the electric utility industry are currently working on initiatives in various areas of their businesses, including safety, quality, production, leadership, and human and organizational performance (HOP). These are important programs, but it’s unlikely they’ll fully achieve their intended objectives if…
Holistic worker wellness isn’t a passing trend – it’s a critical component of workplace safety and strong organizational performance.
Making the Safety Connection: The Impact of Total Well-Being in the Workplace
Utility workers perform essential tasks that touch millions of lives every day. The critical nature of the services they provide coupled with the perilous nature of their tasks exposes these workers to life-threatening hazards. This is why the industry highly values and prioritizes safety.
Many…
Research indicates use of these practical tactics can help safety professionals garner greater leadership support for their programs.
The Roadmap to Gaining Senior Leader Buy-In for Safety Initiatives
In a recent survey we conducted, 97% of safety professionals who responded confirmed that gaining senior leader buy-in for their safety programs was either very important or extremely important to them.
This research project was a joint effort between the National Electrical Contractors Associat…
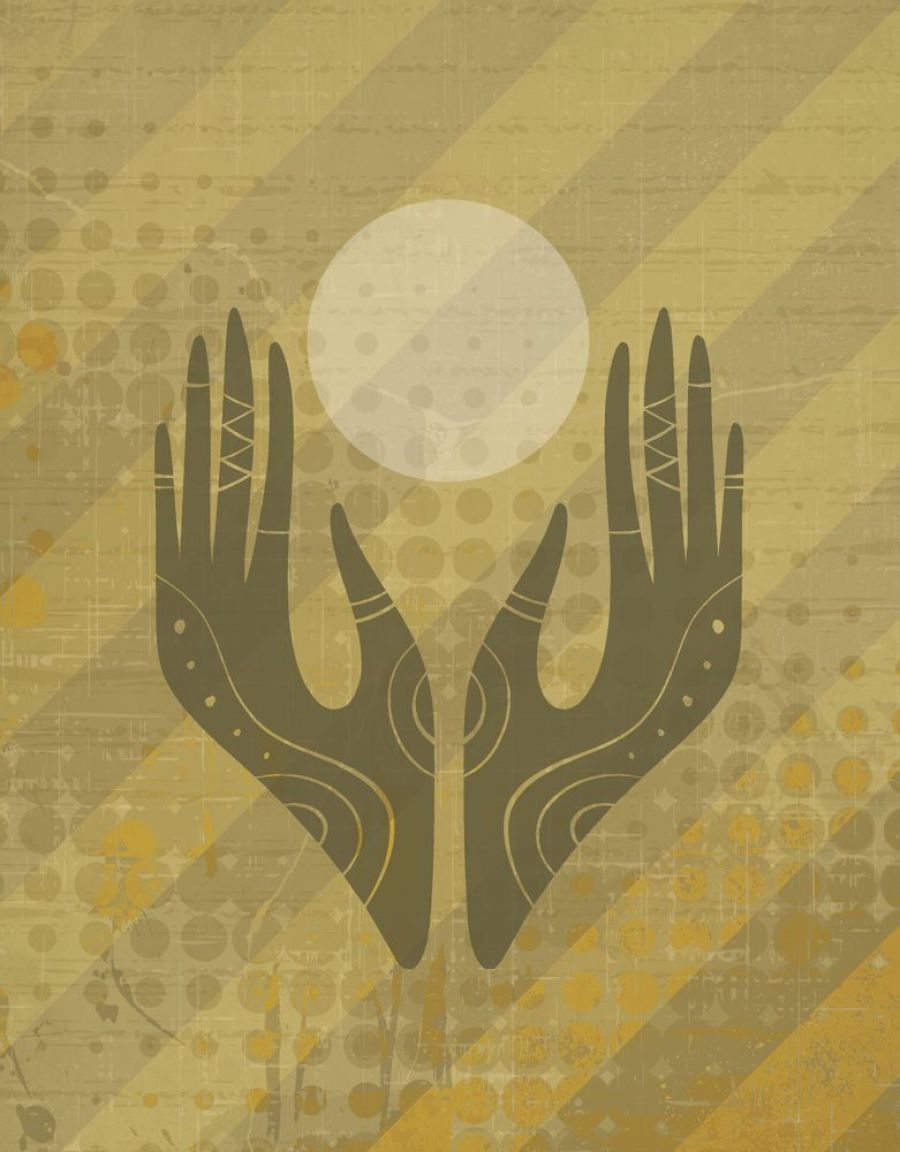
Assessing employees holistically provides an extraordinary opportunity to make a difference – in safety and beyond.
An Inextricable Link: The Safety Benefits of Holistic Wellness in the Workplace
There is an inextricable link between employee safety and mental and physical wellness that is often overlooked. Taking a holistic view of your employees includes looking wholly at each person to better understand and address their mental and physical health challenges and related distractions that…
Worksite Safety
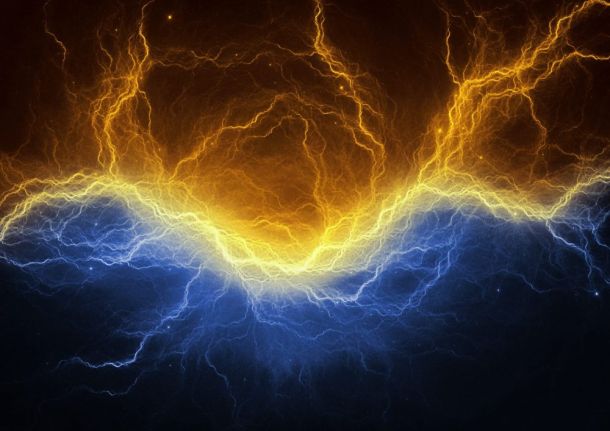
Variabilities in Electrical Arc Flash Protection
Accuracies are synonymous with safety and science. While many perceive that electrical safety needs to be highly exact, this article aims at creating awareness of why sticking to the basics is effective.
But before we delve into variability in electrical engineering, safe electrical work practices…
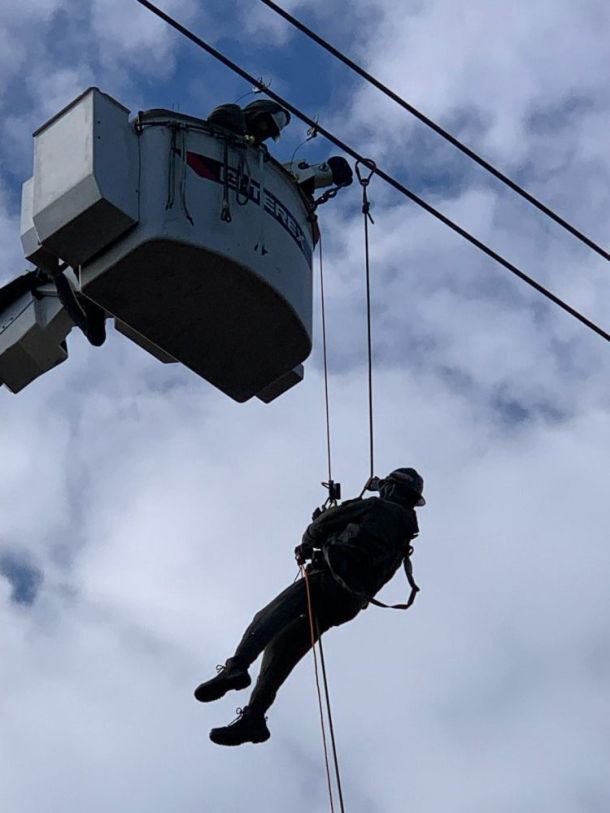
From Risk to Reliability: Improving Rope Safety in Energized Environments
The tools and equipment employed by electrical workers must possess the necessary insulating properties to ensure user safety. One such tool, dielectric rope, can be overlooked as a component of electrical safety, but modern standards and rigorous testing protocols are transforming the way this typ…
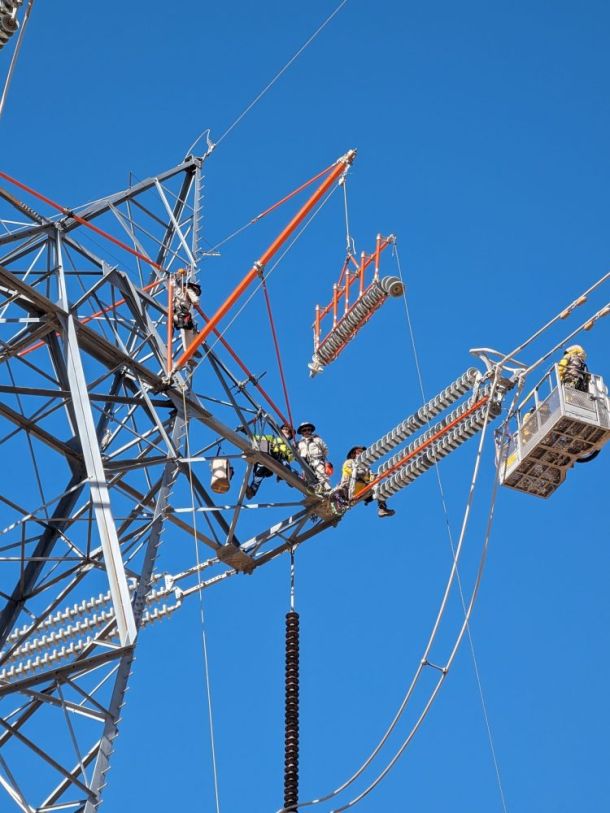
Beyond the ABCs: Fall Protection for Unique Tasks
The electric transmission and distribution (T&D) industry often requires work in challenging environments. Whether crew members access tall structures by helicopter, use rope-access methods to climb lattice towers, or ride wire carts to install and maintain spacers along energized lines, their…
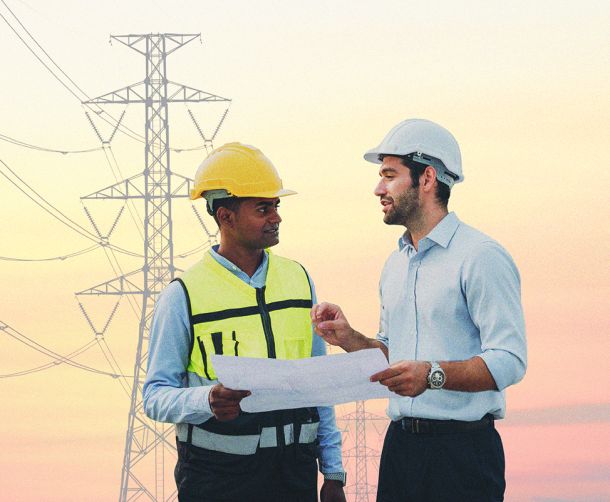
Using the Prediction Model to Prevent Incidents and Near-Misses
As someone employed in the electric utility industry, would you be willing to consider that there may be incident prevention strategies yet to be discovered and tested? Are you open to the idea that a better model could exist to create change in our industry – change that could reduce or even elimi…
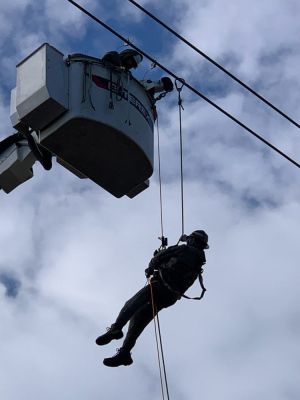
A growing number of utility organizations are making a shift from using traditional synthetic ropes to those with verified dielectric properties.
From Risk to Reliability: Improving Rope Safety in Energized Environments
The tools and equipment employed by electrical workers must possess the necessary insulating properties to ensure user safety. One such tool, dielectric rope, can be overlooked as a component of electrical safety, but modern standards and rigorous testing protocols are transforming the way this typ…
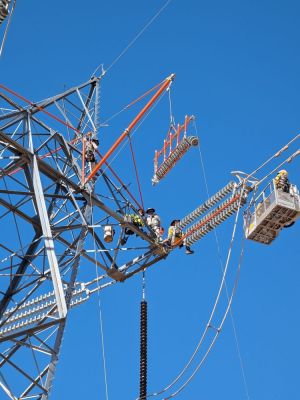
Effective worker protection demands precise equipment selection, thorough worker training and well-rehearsed rescue procedures.
Beyond the ABCs: Fall Protection for Unique Tasks
The electric transmission and distribution (T&D) industry often requires work in challenging environments. Whether crew members access tall structures by helicopter, use rope-access methods to climb lattice towers, or ride wire carts to install and maintain spacers along energized lines, their…
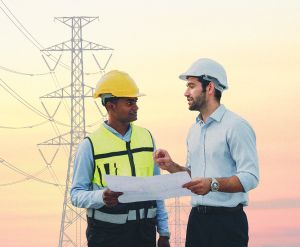
Crews who consistently discuss their safety concerns before work begins create more opportunities to mitigate or eliminate hazards.
Using the Prediction Model to Prevent Incidents and Near-Misses
As someone employed in the electric utility industry, would you be willing to consider that there may be incident prevention strategies yet to be discovered and tested? Are you open to the idea that a better model could exist to create change in our industry – change that could reduce or even elimi…
5 Core Components of a Well-Developed Storm Response Plan
Electric utilities are part of the backbone of modern society, providing essential power to homes, businesses, emergency services providers and more. But this critical service is vulnerable to extreme weather events that can cause massive disruptions, damage infrastructure and jeopardize public safety. Due to the frequency and severity of such events, it is more important than ever for electric power organizations to have a comprehensive storm response plan in place.
I’ve consistently been involved in storm response planning throughout my career, both as a lineman and a safety specialist…

Kirk Coffey, CUSP
Recording and Analyzing Job Briefings Can Save Lives
Planning saves lives. Whether you call it a job briefing or a tailboard, taking time before work begins to identify potential hazards, discuss elimination and mitigation strategies, and align the crew reduces the risk of incidents – and it’s an OSHA requirement per 29 CFR 1910.269(c). Studies consi…

Barry Nelson
4 Strategies to Facilitate Effective Knowledge Transfer
Effectively transferring knowledge from tenured employees to new hires and those climbing the ranks is one of the most significant challenges utility organizations must reckon with. The workforce is continuously evolving, so it is essential to ensure that valuable insights and expertise are not los…

Robert (RL) Eisenbach, CUSP, SMS
Rediscover Your Inner Superhero

Brent Jeffries
Targeted Training: Reducing Stress-Related Cognitive Load in Lineworkers

Bill Martin, CUSP, NRP, RN, DIMM, and Michelle Forkey
Shaking Off the Holiday Hangover

Jennifer A. Martin
Practicing HOP tools in low-risk environments helps to ensure you’ll be able to use them effectively when they’re really needed.
Prioritize Safety Now So It Becomes a Value Before It’s Too Late
We typically excel at safety – after an incident. My question is, can we get it right before an incident occurs? And if so, how? Keeping in mind that you probably learned a stove could be hot by touching one as a child, let’s consider another question: Is it possible for us to develop safety-relate…
The Good Shepherd
If you’re like me, you’ve only encountered sheep at a petting zoo, so here’s a fun fact about them: sheep have rectangular pupils. I included that to make sure you learn something today and to challenge us to explore other sheep characteristics and what we can learn from sheep-shepherd relationship…
Your primary strategy must be to manage your own attitude and actively care about each of your team members.
Bad Attitudes and How to Handle Them
One of the questions I’m most frequently asked during leadership classes is how to handle people with bad attitudes. So, I’d like to take this opportunity to share some highlights from those discussions. I will remind you that leadership is much more of an art than a science. There is no perfect ro…
We must positively reinforce success for it to be repeated.
Win and Win Again: The Blueprint for Repeating Safety Successes
The primary goal of safety is to prevent injuries. We achieve that goal in most cases, though our rare failures often overshadow our frequent successes. And while it’s essential to analyze failures and apply lessons learned, it’s equally if not more important to highlight and replicate our successe…
Bucket Truck Safety: OSHA Standards and Other Considerations
I receive numerous and varied questions about the safe use of bucket trucks in electric utility operations, so in this installment of “Voice of Experience,” I am going to share with you the OSHA standards you need to know as well as some things I have discovered during observations and audits of fi…
A Checkup from the Neck Up
The pastor of the church I attend recently delivered a sermon that deeply resonated with me and inspired the title of this article. Around that time, I’d been ruminating on some incidents I was investigating as part of my consulting work. I’d read the accident reports and conducted employee intervi…
To Improve On-the-Job Safety, Consistency and Continuing Education are Key
It’s a little late to say Happy New Year, but I still want to wish all of you a fantastic and safe 2025. One of my hopes for this year is that I won’t be asked to investigate another incident or fatality – because we’ll all work together to ensure they never occur. We’ve had more than enough injuri…
Don’t Do This: Lessons Learned in the Field
I was so excited when I became a journeyman lineman in the early 1970s. In those days, there was no such thing as a journeyman ticket – a union member or business agent would let you know that you had arrived. Seniority alone was the driver.
I was a union lineman in IBEW 84/896 located in Macon…
June-July 2025 Q&A
Q: Can you direct us to information regarding “fuzzing” or “noisy tester” voltage detectors? We’ve heard that with noisy testers, there’s potential for both false negatives (no voltage is detected although it’s present) and false positives (voltage is indicated where none exists). We’ve also heard a noisy tester can be triggered by induction on a de-energized line, creating confusion in the field…
April-May 2025 Q&A
Q: I’m a municipal utility substation engineer, and I’m hoping you can help me with this question: Does an engineer taking photos in a substation fall under the OSHA 29 CFR 1910.269 work rules?
A: The simple answer is yes. No matter your training or education, if you must be inside the fence to take the photos, you are required to meet the 1910.269(a)(2) qualification standards.
The error p…