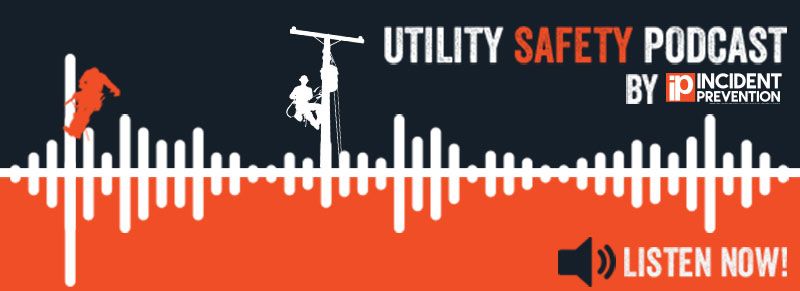
Incident Prevention Utility Safety Podcast
Welcome to the iP Utility Safety Podcast, your go-to resource for enhancing safety, leadership, and operational excellence in the utility industry. We cover a wide range of topics, including building a culture of safety, innovative safety programs, human performance, and strategies for preventing workplace injuries. Each episode delivers actionable insights to help utility professionals foster safer work environments and achieve organizational success.
PODCASTS BY INTERVIEWER
Utility Safety Podcast: Deep Dive: Bucket Truck Safety: OSHA Standards and Other Considerations Written by Danny Raines, CUSP
In this episode, we unpack the vital safety standards, OSHA regulations, and field-tested insights that govern bucket truck operations in the electric utility industry. Based on the article “Bucket Truck Safety: OSHA Standards and Other Considerations” by Danny Raines, CUSP, we dive into key differences between Class A and Class B trucks, daily control tests, fall protection, and the nuances of operating near energized lines. You’ll learn why dielectric testing matters, how improper tool placement can lead to serious hazards, and what often-overlooked basics can prevent catastrophic incidents. Whether you’re in utility operations, safety management, or just curious about what keeps linemen safe, this is your shortcut to understanding critical compliance.
Gain practical takeaways, understand real-world challenges, and walk away with a new appreciation for the safety systems behind the power grid.
Read the article: https://incident-prevention.com/blog/bucket-truck-safety-osha-standards-and-other-considerations/
Key Takeaways:
-
OSHA 1910.67 is the foundational standard for bucket truck safety.
-
Daily lift control tests and proper bucket stance are mandatory safety practices.
-
Class A (barehand) and Class B (gloving) trucks serve different functions and require different protective strategies.
-
Fall protection is a non-negotiable requirement—fall distance and impact risk must be minimized.
-
Misconceptions about insulation and inadequate cover-up procedures are common contributors to incidents.
3 Podcast Questions and Answers:
Q1: Why is OSHA 1910.67 considered the backbone of bucket truck safety?
A1: Because it outlines non-negotiable requirements such as daily lift control testing, safe bucket operation, and movement restrictions—all of which are essential to preventing falls and electrocution.
Q2: What’s the key difference between Class A and Class B bucket trucks?
A2: Class A trucks are designed for direct contact with high-voltage lines and rely on the boom’s insulation, while Class B trucks require full cover-up and rubber glove protection due to lower insulation properties.
Q3: What unsafe practice is commonly observed and highlighted in the article?
A3: Moving trucks with elevated booms without proper exemption, and workers failing to properly cover energized parts—both of which dramatically increase risk.
Subscribe to Incident Prevention Magazine – https://incident-prevention.com/subscribe-now/
Register for the iP Utility Safety Conference & Expo – https://utilitysafetyconference.com/
Danny Raines, CUSP, is an author, an OSHA-authorized trainer, and a transmission and distribution safety consultant who retired from Georgia Power after 40 years of service and now operates Raines Utility Safety Solutions LLC.
#UtilitySafety #BucketTruckSafety #OSHAStandards #LinemanSafety #ElectricalUtilityWork
Silencing the Noise: Creating a Culture of Actionable Safety and Synchrony with Bill Martin, CUSP
In this episode of our Actionable Safety series, host Nick talks with Bill Martin and Kate Wade about moving beyond “safety noise” to create real, lasting change on the job. They dive deep into achieving buy-in through synchrony, overcoming defensiveness, and translating safety theory into real-world practice. With stories from climbing Mount Kenya to lessons learned in the utility industry, they explain how empathy, respect, and clear communication are essential for building a culture where safety improvements take hold. Listen in for practical strategies on fostering trust, testing new ideas without fear, and removing barriers that block true team alignment. If you’re ready to rethink compliance culture and help your crew take meaningful action, this episode is for you.
Subscribe to Incident Prevention Magazine – https://incident-prevention.com/subscribe-now/
Register for the iP Utility Safety Conference & Expo – https://utilitysafetyconference.com/
✅ Key Takeaways
-
Safety success depends on synchrony: Teams need shared purpose and alignment to move beyond noise and see real change.
-
Empathy and respect matter: You don’t have to like everyone you work with, but respecting them enables effective collaboration.
-
Defensiveness is a barrier: Recognize and manage defensive reactions to open the door to candid discussion and feedback.
-
Test and evaluate constantly: Progress requires trying new approaches and learning from all outcomes, not just repeating old rules.
-
Culture change is leadership’s job: Leaders must remove barriers to buy-in, making space for collective learning and growth.
3 Questions and Answers
Q1: What does “synchrony” mean in safety culture?
A: Synchrony is getting everyone on the same page, working toward a shared goal. It’s like a football team running plays in sync or an orchestra staying in tune—it ensures teams work together efficiently and safely.
Q2: How can leaders encourage buy-in from crews?
A: By removing barriers to participation, listening to feedback, and creating a culture where workers can test and evaluate new ideas without fear of judgment. Buy-in emerges naturally in an environment of trust and shared purpose.
Q3: Why is reducing “defensiveness” so important on the job?
A: Defensiveness blocks communication and critical thinking. By pausing before reacting, crews can shift from compliance mode to discovery mode—enabling safer, smarter decisions on the ground.
#SafetyCulture #UtilitySafety #LeadershipDevelopment #TeamworkMatters #ActionableSafety
Utility Safety Podcast: Deep Dive: Bucket Truck Safety: OSHA Standards and Other Considerations Written by Danny Raines, CUSP
In this episode, we unpack the vital safety standards, OSHA regulations, and field-tested insights that govern bucket truck operations in the electric utility industry. Based on the article “Bucket Truck Safety: OSHA Standards and Other Considerations” by Danny Raines, CUSP, we dive into key differences between Class A and Class B trucks, daily control tests, fall protection, and the nuances of operating near energized lines. You’ll learn why dielectric testing matters, how improper tool placement can lead to serious hazards, and what often-overlooked basics can prevent catastrophic incidents. Whether you’re in utility operations, safety management, or just curious about what keeps linemen safe, this is your shortcut to understanding critical compliance.
Gain practical takeaways, understand real-world challenges, and walk away with a new appreciation for the safety systems behind the power grid.
Read the article: https://incident-prevention.com/blog/bucket-truck-safety-osha-standards-and-other-considerations/
Key Takeaways:
-
OSHA 1910.67 is the foundational standard for bucket truck safety.
-
Daily lift control tests and proper bucket stance are mandatory safety practices.
-
Class A (barehand) and Class B (gloving) trucks serve different functions and require different protective strategies.
-
Fall protection is a non-negotiable requirement—fall distance and impact risk must be minimized.
-
Misconceptions about insulation and inadequate cover-up procedures are common contributors to incidents.
3 Podcast Questions and Answers:
Q1: Why is OSHA 1910.67 considered the backbone of bucket truck safety?
A1: Because it outlines non-negotiable requirements such as daily lift control testing, safe bucket operation, and movement restrictions—all of which are essential to preventing falls and electrocution.
Q2: What’s the key difference between Class A and Class B bucket trucks?
A2: Class A trucks are designed for direct contact with high-voltage lines and rely on the boom’s insulation, while Class B trucks require full cover-up and rubber glove protection due to lower insulation properties.
Q3: What unsafe practice is commonly observed and highlighted in the article?
A3: Moving trucks with elevated booms without proper exemption, and workers failing to properly cover energized parts—both of which dramatically increase risk.
Subscribe to Incident Prevention Magazine – https://incident-prevention.com/subscribe-now/
Register for the iP Utility Safety Conference & Expo – https://utilitysafetyconference.com/
Danny Raines, CUSP, is an author, an OSHA-authorized trainer, and a transmission and distribution safety consultant who retired from Georgia Power after 40 years of service and now operates Raines Utility Safety Solutions LLC.
#UtilitySafety #BucketTruckSafety #OSHAStandards #LinemanSafety #ElectricalUtilityWork
Utility Safety Podcast – Visual Intelligence for a Safer Grid: The Future of Utility Inspections
In this episode, Incident Prevention’s Kate Wade sits down with Kaitlyn Albertoli, co-founder and CEO of California-based Buzz Solutions, to explore how visual intelligence is helping utilities uncover hidden risks and modernize critical infrastructure. Kaitlyn shares how Buzz Solutions’ platforms—PowerAI and PowerGuard—use AI-driven insights to streamline inspections, enhance grid reliability, and reduce operational costs. They also discuss the challenges of adopting new technologies, bridging the field-office communication gap, and what utility safety professionals can expect in the next 5 to 10 years. This conversation is essential for those interested in data-driven decision-making, infrastructure safety, and the future of AI in the energy sector.
To reach Kaitlyn directly, email her at kaitlyn@buzzsolutions.com or connect via LinkedIn: www.linkedin.com/in/kaitlyn-claire-albertoli/
Key Takeaways:
-
Buzz Solutions uses AI-powered visual intelligence to help utilities identify risks and improve inspection accuracy.
-
Their platform PowerAI analyzes images from drones, helicopters, and field crews to prioritize maintenance and reduce operational costs.
-
Integration with GIS and asset management systems makes implementation efficient and less disruptive.
-
Buzz’s tools support storm prep, wildfire mitigation, and long-term grid modernization.
-
Education and communication are key to AI adoption across all levels of a utility organization.
Questions & Answers
Q1: What problem does Buzz Solutions aim to solve for utilities?
A: Buzz helps utilities manage and analyze vast visual datasets, allowing them to spot infrastructure issues early, prioritize repairs, and eliminate data silos.
Q2: How does PowerAI differ from general AI tools?
A: PowerAI is a purpose-built platform that uses machine learning for visual inspection analysis, making it highly specific to the utility industry’s unique needs.
Q3: What concerns do utilities have about AI adoption?
A: Many worry AI could replace jobs or be unreliable, but Buzz focuses on “visual intelligence” to support—not replace—field experts and improve safety decisions.
Q4: Can this technology help prevent wildfires or major outages?
A: Yes, by analyzing infrastructure degradation and identifying high-risk components early, utilities can proactively address threats before they escalate.
Q5: How can utilities ensure smooth adoption of Buzz’s solutions?
A: Success hinges on integrating into existing workflows, gaining buy-in from field users, and automating data flow into GIS and asset management systems.
Subscribe to Incident Prevention Magazine – https://incident-prevention.com/subscribe-now/
Register for the iP Utility Safety Conference & Expo – https://utilitysafetyconference.com/
#UtilitySafety #VisualIntelligence #GridModernization #AIinUtilities #UtilitySafetyPodcast #InfrastructureInnovation
Built In, Not Bolted On with Doug Hill, CUSP – Rethinking Job Briefs – Why the End of the Day Matters Most
In this episode of Built In, Not Bolted On, host Doug Hill challenges traditional thinking around job safety practices. He explores the effectiveness of pre-job briefs, mid-day check-ins, and post-job reviews, emphasizing how learning from experience—especially at the end of the day—can dramatically improve safety outcomes. Drawing inspiration from aviation and military after-action reviews, Doug outlines how three simple questions can spark a culture of continuous improvement and safer work environments.
✅ Key Takeaways
-
Pre-job briefs are essential—but post-job briefs may hold even more value in fostering continuous improvement.
-
A “mid-day check-in” helps adjust controls based on changing conditions like weather or job scope.
-
Successes should be analyzed as deeply as failures to uncover replicable best practices.
-
Three core post-job questions—What went well? What didn’t? What can we learn?—drive future safety improvements.
-
Brief, honest conversations at the end of the day can improve the next day’s job planning significantly.
Q1: Why is the post-job brief considered more valuable than the pre-job brief by aviation professionals?
A1: Because post-job briefs provide real-time insights and lessons learned from completed tasks, which shape better, more informed pre-job briefs the following day.
Q2: What are the three questions Doug recommends asking during a post-job brief?
A2: 1) What went well? 2) What didn’t go well? 3) What can we learn to improve for the future?
Subscribe to Incident Prevention Magazine – https://incident-prevention.com/subscribe-now/
Register for the iP Utility Safety Conference & Expo – https://utilitysafetyconference.com/
#UtilitySafety #SafetyCulture #AfterActionReview #WorkplaceSafety #JobBriefing #ContinuousImprovement
Built In, Not Bolted On with Doug Hill, CUSP – Why Safety Programs Succeed or Fail David McPeak, CUSP
In this episode of Built In, Not Bolted On, host Doug Hill sits down with safety leader and educator David McPeak to explore the real keys to successful Human and Organizational Performance (HOP). Through storytelling, relatable analogies, and a few laughs, they break down the power of caring leadership, building a just culture, the dangers of overcomplicating safety systems, and the importance of embedding safety into the DNA of an organization. From tools like “E + R = O” to the “village-by-village” model of influence, this episode provides a practical, people-first look at how to make safety initiatives stick—for good.
Key Takeaways:
-
Culture eats strategy for breakfast. Safety systems must be embedded into the culture—not simply bolted on as compliance requirements.
-
Toxic culture is a showstopper. No safety program will succeed in an environment that lacks trust, respect, and accountability.
-
Success starts with relationships. Building strong, caring teams helps create the psychological safety needed to speak up and improve performance.
-
Don’t overcomplicate safety. Practical, repeatable tools that workers understand and use in context matter more than complex policies.
-
Peer-level champions and simple tools like “E + R = O” and performance mode awareness can drive real change from the ground up.
5 Relevant Questions & Answers:
Q1: What’s the key to implementing effective Human and Organizational Performance (HOP) strategies?
A1: Commitment and time. It’s not about quick fixes—it’s about embedding care, consistency, and communication into every level of the organization.
Q2: Why do many safety programs fail?
A2: They’re often implemented in toxic cultures or made too complex. Without foundational trust and simple, relatable tools, programs won’t stick.
Q3: How can you tell if a safety initiative is “built in” versus “bolted on”?
A3: “Built-in” programs are part of daily work, language, and habits. “Bolted-on” programs feel forced, top-down, and are quickly abandoned.
Q4: What role do performance modes play in safety?
A4: Understanding if a worker is in skill-, rule-, or knowledge-based mode helps choose the right tool—like saying it out loud, step-by-step checks, or stopping work to seek help.
Q5: How can leaders support cultural safety transformation?
A5: By modeling desired behaviors, creating a safe space for feedback, understanding how each role sees safety, and helping translate tools into all departments—not just field crews.
#BuiltInNotBoltedOn #UtilitySafety #HumanPerformance #SafetyCulture
#OrganizationalLeadership #JustCulture
Contact Doug: doug@utilitybusinessmedia.com
Subscribe to Incident Prevention Magazine – https://incident-prevention.com/subscribe-now/
Register for the iP Utility Safety Conference & Expo – https://utilitysafetyconference.com/
Built In, Not Bolted On with Doug Hill, CUSP – Protecting Our Workforce Through Safety Culture
In this episode of Built In, Not Bolted On with host Doug Hill, CUSP, we dive deep into the world of utility safety culture, exploring the latest risk management strategies, regulatory challenges, and best practices to keep crews safe. Our host shares firsthand experiences and expert insights on hazard identification, compliance updates, and leadership in safety culture. Whether you’re in line work, transmission, or distribution, this episode is packed with valuable takeaways to help you enhance workplace safety and efficiency.
Contact Doug: doug@utilitybusinessmedia.com
Subscribe to Incident Prevention Magazine – https://incident-prevention.com/subscribe-now/
Register for the iP Utility Safety Conference & Expo – https://utilitysafetyconference.com/
Key Takeaways:
•Risk Mitigation Strategies – How to proactively identify and address workplace hazards.
•Compliance & Regulations – Updates on industry standards and their impact on daily operations.
•Technology & Safety – The role of innovative tools in improving worker protection.
•Leadership in Safety – Why management commitment is crucial for fostering a strong safety culture.
•Lessons from the Field – Real-world scenarios that highlight best practices and potential pitfalls.
Five Relevant Questions & Answers from the Podcast:
1.Q: What are the biggest safety challenges facing the utility industry today?
A: The biggest challenges include hazard identification, ensuring compliance with evolving regulations, and integrating new technology while maintaining worker safety.
2.Q: How can companies improve their safety culture?
A: Companies must prioritize training, encourage open communication, and lead by example to create an environment where safety is a shared responsibility.
3.Q: What role does technology play in utility safety?
A: Innovations like wearable safety devices, AI-driven monitoring, and automated reporting systems are enhancing how companies manage risks.
4.Q: How do changing regulations impact utility workers?
A: New safety laws require continuous education and adaptation, ensuring workers stay compliant and protected in evolving work environments.
5.Q: What is one key piece of advice for improving safety in the field?
A: Always prioritize situational awareness, follow protocols, and never hesitate to speak up about potential hazards.
#UtilitySafety #WorkplaceSafety #LinemanLife #RiskManagement #SafetyCulture #OSHACompliance #PowerGrid #ElectricalSafety
Tailgate Topics Podcasts
Tailgate Topics – The Dangers of Distraction: Staying Focused in High-Risk Utility Work by Scott Perrin
In this episode of Tailgate Topics, host Rod Courtney is joined by Nick from Utility Business Media to discuss one of the biggest safety risks in the utility industry—distractions. Inspired by Scott Perrin’s article, The Dangers of Distraction: Staying Focused in a High-Risk Environment, this conversation dives into how mental drift, complacency, fatigue, and technology impact workplace safety.
Read the article: https://incident-prevention.com/blog/the-dangers-of-distraction-staying-focused-in-a-high-risk-environment/
From distraction-related vehicle accidents to the role of fatigue and stress in high-risk environments, this episode explores real-world examples and practical strategies for reducing workplace hazards. Tune in to learn how small changes in awareness and environment can help prevent serious injuries and fatalities in the utility industry.
Key Takeaways:
✔️ Distractions are unavoidable, but they can be managed.
✔️ Fatigue, complacency, and stress increase the risk of accidents.
✔️ Cell phones and modern technology are major workplace distractions.
✔️ Taking scheduled breaks and staying mindful can improve focus and safety.
✔️ Vehicle accidents due to distracted driving are a growing financial burden for utilities.
✔️ Simple steps, like identifying distractions and using hands-free devices, can help reduce risk.
Subscribe to Incident Prevention Magazine – https://incident-prevention.com/subscribe-now/
Register for the iP Utility Safety Conference & Expo – https://utilitysafetyconference.com/
#UtilitySafety #WorkplaceDistractions #SafetyCulture #HighRiskJobs #FatigueAwareness #ComplacencyKills #DistractionFreeWork #UtilityWorkers
Tailgate Topics – Power Restoration Triage and Delta Systems – William Martin, CUSP, RN, NRP, DIMM
August 25, 2023
In this episode of Tailgate Topics, Rod Courtney, CUSP interviews William Martin, CUSP, RN, NRP, DIMM ON his article in Incident Prevention Magazine titled “Power Restoration Triage and Delta Systems”
Important points in the article cover –
- The importance of triage in power restoration: Triage is a way of prioritizing outages so that the most critical ones can be restored first. This is important because it helps to minimize the impact of the storm on businesses, homes, and public safety.
- The different types of triage systems: There are a number of different triage systems that can be used for power restoration. The best system for a particular situation will depend on the factors involved, such as the size and complexity of the outage, the availability of resources, and the severity of the weather conditions.
- The unique challenges of triaging delta systems: Delta systems are more common in rural areas and small communities. They pose unique challenges for triaging because they can create low-voltage conditions that can damage customer equipment.
- The insights of experts in the field: We’ll hear from experts in the field of power restoration to get their insights on how to do triage effectively. This will include tips on how to prioritize outages, how to choose the right triage system, and how to deal with the unique challenges of delta systems.
About the Author: Bill Martin, CUSP, NRP, RN, DIMM, is the president and CEO of Think Tank Project LLC (www.thinkprojectllc.com). He has held previous roles as a lineman, line supervisor and safety director.
Read the article – https://incident-prevention.com/blog/power-restoration-triage-and-delta-systems/
Register for the iP Utility Safety Conference & Expo to hear Bill & Rod Courtney speak – https://utilitysafetyconference.com/
Tailgate Topics – Discuss Drug & Alcohol Awareness on the Job Site – Jesse Hardy, CSP, CIT, CUSP, PCC
June 13, 2023
In this episode Rod covers with Jesse a host of job site issues that relate to drugs and alcohol. This is a very great subject to review with your team and pay attention to on the job site.
You see, this isn’t a “they have a problem” sort of problem – it’s a “we have a problem” sort of problem. It’s the kind of problem that we need to talk about for the sake of you and your family, your company, our industry and our nation.
To share feedback about this podcast, reach out to Jesse Hardy at jessehardy@yahoo.com or our Host Rod Courtney at rod.courtney.usoln@gmail.com
View Jesse Hardy’s article here.
39 min. with Jesse Hardy, CSP, CIT, CUSP
Tailgate Topics -Strategies to Handle Workplace Conflict – Jesse Hardy, CSP, CIT, CUSP
February 7, 2023
Listen to our 2nd installment into our new series “Tailgate Topics hosted by Rod Courtney, CUSP” titled “Strategies to Handle Workplace Conflict” Written by Jesse Hardy, CSP, CIT, CUSP.
“Jack, the people issues are just getting to be too much,” the foreman said. “If it’s not the landowners and members of the public throwing fits and coming into the work zones, it’s our own people getting into conflicts. At best it’s a distraction that steals our focus, and at it’s worst it becomes violent.”
The superintendent replied to the foreman, “I hear you, Billy. Let’s come up with a plan on how to deal with this.”
Three Important Questions
In this month’s Tailgate, we’re going to review answers to three important questions related to workplace conflict and violence, and then we’ll look at how to deal with three areas of conflict in ways that lead to the best possible outcome based on the situation.
View Jesse Hardy’s article here.
33 min. with Jesse Hardy, CSP, CIT, CUSP
Safety by Design – Empowering Leadership and Employee Involvement with Pam Tompkins CSP, CUSP
Safety by Design – Empowering Leadership and Employee Involvement with Pam Tompkins CSP, CUSP
Read the article – https://incident-prevention.com/blog/safety-by-design-leadership-and-employee-involvement/
In this episode of Safety by Design, we welcome back safety expert Pam Tompkins, CUSP, CSP, to explore the foundational role of leadership and employee involvement in building effective safety systems. Based on her recent article in Incident Prevention magazine, Pam shares candid insights on overcoming middle management roadblocks, building measurable KPIs, and empowering workers at all levels—from new apprentices to seasoned frontline leaders. Tune in as Pam breaks down why involving the workforce is not optional but essential to safety success—and how organizations can align top-down and bottom-up strategies to protect their people and drive meaningful change.
Key Takeaways:
-
People are the foundation of safety—rules and programs only work when employees are actively involved in shaping and executing them.
-
Middle management is often the bottleneck in safety performance due to lack of field experience and misaligned priorities.
-
Effective safety systems require alignment across all levels: senior leaders, middle managers, and frontline employees.
-
KPIs must be tailored by role—senior leadership, middle management, and field crews should each have performance metrics tied to their unique influence on safety.
-
Safety is not just policy—it’s integration, and organizations must continuously measure, evaluate, and adapt their systems with employee feedback.
❓ 5 Relevant Questions & Answers:
Q1: Why is employee involvement essential to a successful safety system?
A1: Without employees, there is no safety system. Engagement ensures processes are practical, understood, and effectively integrated into real-world tasks.
Q2: What role does middle management play in the success—or failure—of safety programs?
A2: Middle managers often act as a roadblock if they prioritize production over safety or lack a true understanding of field-level risks.
Q3: How can senior leaders improve safety outcomes?
A3: By understanding the real “look of safety,” engaging directly with field teams, and holding themselves accountable for organizational risk tolerance.
Q4: What kind of KPIs are most effective for evaluating safety?
A4: Role-specific KPIs—like field engagement for executives or measurable improvements in hazard mitigation for frontline supervisors—are key.
Q5: What’s the danger of not aligning top-down and bottom-up safety efforts?
A5: It creates a culture of distrust, disengagement, and missed opportunities to improve safety. Full integration is necessary for success.
#UtilitySafety #WorkplaceSafety #SafetyLeadership #SafetyCulture #EmployeeEngagement #FrontlineSafety
Subscribe to Incident Prevention Magazine – https://incident-prevention.com/subscribe-now/
Register for the iP Utility Safety Conference & Expo – https://utilitysafetyconference.com/
Safety by Design: Transforming Utility Safety with Pam Tompkins, CUSP
In this episode of the Safety by Design podcast, Pam Tompkins, CUSP, shares her extensive 40-year journey in the utility safety industry. Pam dives into the critical importance of intentional safety planning and proactive assessments, emphasizing the need for quality over quantity in safety initiatives. With insights drawn from her global consulting experience, Pam provides actionable strategies to design systems that protect both employees and organizations. She also previews her upcoming article series in Incident Prevention Magazine, which will provide a deep dive into transforming safety practices for utility professionals.
Key Takeaways
- Proactive Assessments are Vital: Most safety assessments are reactive, conducted after incidents occur. Pam stresses the need for proactive assessments to prevent significant injuries or fatalities.
- Quality Over Quantity: Simply adding more safety initiatives doesn’t translate to better safety outcomes. Organizations must ensure their programs are effective and aligned.
- Importance of Standards: Leveraging ANSI and ISO standards can guide organizations in creating robust safety systems.
- Systemic Alignment Matters: Safety programs should align at all organizational levels to ensure effectiveness and consistency.
- Baseline and Metrics: Establishing a baseline and measurable goals for every safety initiative is essential for tracking success.
#SafetyByDesign #UtilitySafety #ProactiveSafety #CUSPLeadership #IncidentPrevention #WorkplaceSafety
You can read the current magazine at Incident Prevention Magazine.
Subscribe to Incident Prevention Magazine – https://incident-prevention.com/subscribe-now/
Register for the iP Utility Safety Conference & Expo – https://utilitysafetyconference.com
Voice of Experience – Checkup from the Neck Up: Preventing Utility Work Mistakes
In this episode of Voice of Experience, Danny Raines, CUSP discusses the critical importance of mental awareness and focus in utility work. Using real-life accident investigations, he explores why experienced professionals sometimes repeat dangerous mistakes and how a “checkup from the neck up” can prevent incidents. From miscommunication in substations to lack of hazard recognition, this episode is packed with insights to improve safety culture and accountability in the field.
Key Takeaways:
- The Importance of Mental Awareness: How small lapses in judgment can lead to catastrophic accidents.
- The Role of Dedicated Observers: Why having a second set of eyes can prevent mistakes.
- Lessons from Incident Investigations: Real-world case studies of preventable accidents.
- Following Procedures & Training: Why workers revert to unsafe practices despite training.
- Taking Accountability: Leadership’s role in enforcing safety and stopping unsafe work.
The Voice of Experience with Danny Raines podcast is produced by the same team that publishes Incident Prevention. It delivers insights based on Danny’s regular column in the magazine, also called the Voice of Experience. To listen to more episodes of this podcast, as well as other podcasts we produce, visit https://incident-prevention.com/podcasts. You can reach Danny at rainesafety@gmail.com
Purchase Danny’s Book on Amazon – https://a.co/d/556LDvz
#UtilitySafety #LinemanLife #WorkplaceSafety #IncidentPrevention #ElectricalSafety #SafetyCulture
Voice of Experience with Danny Raines, CUSP – Test, Verify, Prevent – Lessons from the Field
Join Danny Raines, CUSP, as he shares critical lessons learned from the field in this episode of The Voice of Experience. Danny dives into real-world incidents, including a tragic fatality and a near-miss, emphasizing the importance of testing and verifying in the utility safety industry. With decades of experience, Danny provides actionable insights to prevent accidents, improve safety protocols, and foster a culture of vigilance among utility professionals.
Key Takeaways:
1.Testing and Verifying Saves Lives: Never assume safety; always verify conditions to prevent catastrophic incidents.
2.Human Error Is Inevitable: Acknowledge that mistakes happen and take proactive steps to minimize risks.
3.The Power of Speaking Up: Encourage crews to challenge unsafe practices and prioritize safety over production.
4.Importance of Job Briefings: Thorough planning and hazard identification are critical to mitigating risks on-site.
4 Questions to learn from this podcast with Answers:
Q1: What is the primary cause of unsafe practices in the field?
A1: Assumptions and rushing to complete tasks often lead to neglecting crucial safety checks, like testing and verifying.
Q2: Why is “speaking up” vital in utility safety?
A2: It prevents potential accidents by addressing hazards early. Crew members should challenge unsafe practices without fear of backlash.
Q3: How can utility workers improve safety culture?
A3: By consistently practicing thorough job briefings, hazard identification, and compliance with safety regulations.
Q4: What role does leadership play in utility safety?
A4: Leaders must ensure oversight, provide proper training, and foster a culture where safety is prioritized over production.
You can read the current magazine at Incident Prevention Magazine.
Subscribe to Incident Prevention Magazine – https://incident-prevention.com/subscribe-now/
Register for the iP Utility Safety Conference & Expo – https://utilitysafetyconference.com/
The Voice of Experience with Danny Raines podcast is produced by the same team that publishes Incident Prevention. It delivers insights based on Danny’s regular column in the magazine, also called the Voice of Experience. To listen to more episodes of this podcast, as well as other podcasts we produce, visit https://incident-prevention.com/podcasts. You can reach Danny at rainesafety@gmail.com
Purchase Danny’s Book on Amazon – https://a.co/d/556LDvzc
#UtilitySafety #WorkSafe #CUSP #LinemanSafety #IncidentPrevention #SafetyLeadership
Voice of Experience with Danny Raines, CUSP – Are You Looking Out a Window or Into a Mirror? A New Perspective on Utility Safety
In this episode, safety consultant Danny Raines, CUSP, reflects on critical issues facing the utility industry, including safety practices, training gaps, and the persistent challenges of electrical fatalities. Danny delves into the importance of adhering to safety protocols, fostering a culture of accountability, and embracing innovation in personal protective equipment (PPE). Through stories from his career, Danny emphasizes the life-saving significance of vigilance and teamwork in high-risk environments.
Key Takeaways:
1.Window vs. Mirror Perspective: Evaluate whether you are self-reflective (mirror) or outward-focused (window) in safety practices.
2.“Learn-It-All” Mindset: Embrace a continuous learning approach over the “know-it-all” attitude.
3.The Numbers Don’t Lie: Despite advancements in PPE and training, electrical fatalities remain stagnant, demanding deeper industry introspection.
4.Accountability Saves Lives: The role of dedicated observers and adherence to safety protocols cannot be overstated.
5.A Culture of Safety: Building relationships and fostering open communication among crews enhance workplace safety.
6.Personal Responsibility: Safety isn’t just about individual choices—it impacts families and communities.
You can read the current magazine at Incident Prevention Magazine.
Subscribe to Incident Prevention Magazine – https://incident-prevention.com/subscribe-now/
Register for the iP Utility Safety Conference & Expo – https://utilitysafetyconference.com/
The Voice of Experience with Danny Raines podcast is produced by the same team that publishes Incident Prevention. It delivers insights based on Danny’s regular column in the magazine, also called the Voice of Experience. To listen to more episodes of this podcast, as well as other podcasts we produce, visit https://incident-prevention.com/podcasts. You can reach Danny at rainesafety@gmail.com
Purchase Danny’s Book on Amazon – https://a.co/d/556LDvz
#UtilitySafety #ElectricalSafety #PPEInnovation #LinemanLife #SafetyCulture #DannyRaines
Voice of Experience – Surviving the Storm: Lessons from the Field with Danny Raines, CUSP
In this episode of The Voice of Experience, Danny Raines, CUSP, shares his invaluable insights from decades of storm work as a lineman and utility safety expert. From the devastation of Hurricane Katrina to modern-day storm recovery challenges, Danny takes us through the physical and mental toll of responding to natural disasters. He explains the dangers of backfeeds, the rise of alternative energy sources, and the importance of verifying safety before restoring power. Learn from his firsthand stories, safety lessons, and how the landscape of utility work has evolved over the years. Whether you’re in the utility industry or just curious about storm response, this episode offers a wealth of knowledge from one of the most respected professionals in the field.
Key Takeaways:
- The dangers of storm work: Power restoration involves more than meets the eye, especially with evolving technology like solar panels and generators creating backfeed hazards.
- Mental and physical challenges: Long hours, dangerous conditions, and the emotional impact of storm recovery can lead to severe fatigue and stress.
- Importance of testing and verifying: Danny stresses the importance of safety procedures, especially when dealing with energized systems after a storm.
- Stories from the field: Real-life experiences from Hurricane Katrina and other storms demonstrate the unpredictable nature of storm recovery.
- Utility evolution: Changes in technology, regulations, and community expectations are reshaping the utility industry’s response to natural disasters.
You can read the current magazine at Incident Prevention Magazine.
Subscribe to Incident Prevention Magazine – https://incident-prevention.com/subscribe-now/
Register for the iP Utility Safety Conference & Expo – https://utilitysafetyconference.com/
The Voice of Experience with Danny Raines podcast is produced by the same team that publishes Incident Prevention. It delivers insights based on Danny’s regular column in the magazine, also called the Voice of Experience. To listen to more episodes of this podcast, as well as other podcasts we produce, visit https://incident-prevention.com/podcasts. You can reach Danny at rainesafety@gmail.com
Purchase Danny’s Book on Amazon – https://a.co/d/556LDvz
#UtilitySafety #StormWork #HurricaneKatrina #LinemanLife #BackfeedDangers #MentalHealthMatters #TestAndVerify #PowerRestoration #StormRecovery #AlternativeEnergy #UtilityIndustry #SafetyFirst #DannyRaines #CUSP #ElectricGrid #DisasterResponse
Utility Safety Solutions Podcasts
Utility Safety Solutions: 2022 FR Update Live From the Expo floor at the Utility Safety Conference & Expo
June 6, 2022
Kurt reports in from the expo floor of the Utility Safety Conference & Expo to provide you with a comprehensive look at what’s new in the FR industry!
20 min. with several FR clothing exhibitors
Utility Safety Solutions: Learn How Intellishift’s Telematics and AI Camera Solutions are Improving Utility Fleet Safety
April 19, 2022
Kurt reports in from the NAFA conference where he met up with Intellishift’s Jordan Kittle to talk all about how the company is making innovative technology solutions that improve utility fleet safety as well as a conversation about a celebrity encounter with LeBron James.
20 min. with Intellishift’s Jordan Kittle
Utility Safety Solutions: Talking with Telelink about Their Lone Worker Monitoring and Incident Response Solution
February 25, 2022
Kurt Moreland sits down to talk with Laura Fudge from Telelink about how a monitoring and incident response solution for lone utility workers can help increase safety and save lives. They also talk about how the monitoring has been a vital safety solution for Newfoundland Hydro and even have fun talking about a celebrity encounter with Bill Nye, the Science Guy.
20 min. with Laura Fudge
Utility Safety Solutions: Talking Traffic Safety with Traffix Devices
March 24, 2022
Kurt Moreland reports live from the American Traffic Safety Services Association show where he talks all about utility traffic safety solutions with representatives from Traffix Devices. From cones and attenuators to barrels and flashing devices, you’ll learn about tools that can help your team stay safer on the roads. And, the Traffix Devices team even shares an amusing celebrity encounter story involving a famous Dallas quarterback.
20 min. with Traffix Devices team
Influencing Safety pt 10 – Is Safety Truly the Utility Industry’s First Priority? with Bill Martin, CUSP
Challenging the Status Quo: Rethinking Safety in the Utility Industry
Is safety truly the utility industry’s first priority? And is it even a real thing, or just a byproduct of something deeper? In this thought-provoking episode of Influencing Safety, Bill Martin, President and CEO of Think Tank Project LLC, joins host Kate Wade to challenge traditional views on safety. They explore the critical role of teamwork, communication, and human connection in fostering a truly safe work environment. Bill shares insights on the psychological factors that influence workplace culture, the hidden impact of mental health, and how shifting our focus from compliance to competency could change the game.
Key Takeaways:
✅ Safety isn’t just about compliance—it’s a byproduct of strong teamwork and communication.
✅ A psychologically safe work environment fosters better decision-making and fewer incidents.
✅ The traditional “safety first” mindset might be limiting our ability to create real change.
✅ Human connection and mental health are critical factors in workplace safety.
✅ Small changes, like pre-job huddles and open conversations, can have a major impact.
Subscribe to Incident Prevention Magazine – https://incident-prevention.com/subscribe-now/
Register for the iP Utility Safety Conference & Expo – https://utilitysafetyconference.com/
#WorkplaceSafety #UtilityIndustry #SafetyCulture #PsychologicalSafety #TeamworkMatters #LeadershipDevelopment #IncidentPrevention #CommunicationIsKey #CUSP #IncidentPrevention
Utility Safety in Depth – Bridging the Safety Gap – The Role of USMWF in Workplace Fatalities
In this episode of Utility Safety in Depth, host Kate Wade sits down with John “Scotty” MacNeill and Rena Harrington to explore the mission of the United Support & Memorial for Workplace Fatalities (USMWF). They discuss the critical role USMWF plays in supporting families affected by workplace fatalities, advocating for stronger safety regulations, and raising awareness in the utility industry. With personal stories, industry insights, and a call to action, this conversation highlights the human impact of workplace safety failures and the importance of proactive prevention.
Key Takeaways:
✔️ The Mission of USMWF: How the organization supports families affected by workplace fatalities.
✔️ Bridging the Safety Gap: Why family members must be involved in post-incident investigations.
✔️ The Power of Storytelling: How sharing personal loss creates real change in workplace safety.
✔️ Advocacy & Legislation: Efforts to improve safety laws at the state and federal levels.
✔️ What Utility Companies Can Do: How organizations can collaborate with USMWF to make a difference.
USMWF’s MISSION
Offers support, guidance and resources to those affected by work-related injuries, illnesses or diseases. Dedicated to sharing lessons learned that leads a movement of change in promoting actions for safe and healthy working conditions. Through the collective voice of families of fallen workers and other activists, we strive for the elimination and controls of workplace hazards– therefore preventing future tragedies.
USMWF’s VISION STATEMENT
USMWF is an organized community of dedicated family member victims, a nationally recognized non-profit leader driving the transformation of the work environment to safe and healthy conditions for all employers and employees – both today and tomorrow.
Read the article in iP Magazine – Read Here
Visit https://www.usmwf.org/ to support The United Support & Memorial for Workplace Fatalities.
Subscribe to Incident Prevention Magazine – https://incident-prevention.com/subscribe-now/
Register for the iP Utility Safety Conference & Expo – https://utilitysafetyconference.com/
#UtilitySafety #WorkplaceSafety #IncidentPrevention #LinemanLife #SafetyAdvocacy #StaySafe #USMWF
From the Olympics to the Utility Field: Dr. Kevin Rindal, DC on Preventing Soft Tissue Injuries
In this episode of the Incident Prevention Utility Safety Podcast, Kate Wade interviews Dr. Kevin Rindal, DC, chiropractor, human performance expert, and co-founder of Vimocity. Drawing from his extensive experience with the U.S. Olympic Swim Team and industrial athletes, Dr. Rindal shares insights on preventing soft tissue injuries, implementing dynamic warmup programs, and securing organizational buy-in for holistic well-being strategies. Learn how utilities can leverage sports medicine principles to enhance safety, reduce costs, and improve workers’ quality of life.
Key Takeaways
- Industrial Athletes and Soft Tissue Injuries: How utility workers face similar physical demands to athletes and the role of dynamic preparation in reducing injury rates.
- Proactive vs. Reactive Approaches: The importance of addressing leading indicators like pain to prevent more significant injuries or reliance on opioids and other pain mitigations.
- Integration with Daily Routines: Methods to seamlessly incorporate warmups, muscle maintenance, and recovery into existing workflows, making it scalable for smaller organizations.
- Leveraging Technology and Gamification: How apps, micro learning, and team challenges foster engagement and create sustainable safety habits.
- Leadership and Culture: The critical role of leadership buy-in at all levels in making safety and well-being programs successful.
Connect with Kevin:
- LinkedIn – https://www.linkedin.com/in/kevinrindal/
- Email – kevin@vimocity.com
Resource Links:
- Short form job-task specific training video | LINK
- Dynamic/ Full-body movement routine (5 min or less) | LINK
- Avoid Slips, Trips and Falls video | LINK
You can read the current magazine at Incident Prevention Magazine.
Subscribe to Incident Prevention Magazine – https://incident-prevention.com/subscribe-now/
Register for the iP Utility Safety Conference & Expo – https://utilitysafetyconference.com/
#UtilitySafety #IndustrialAthletes #InjuryPrevention #Vimocity #WorkplaceWellbeing #DynamicWarmups
Utility Safety In Depth: The 100th Monkey Effect and Human Connection in Safety – Doug Hill, CUSP & Bill Martin, CUSP
In this episode of Utility Safety In Depth, we delve into the fascinating concept of the 100th monkey effect and its implications for safety in the utility industry. Join us as we discuss how collective consciousness and human connection can drive significant improvements in safety culture and outcomes. We’ll explore practical strategies to foster a more caring and supportive work environment, emphasizing the importance of communication, empathy, and mutual respect. Discover how embracing the power of human connection can lead to a safer and more resilient workforce.
Key Takeaways:
- The 100th Monkey Effect: How collective consciousness can influence individual behavior.
- The importance of human connection in safety culture.
- Practical strategies to foster a more caring and supportive work environment.
- The power of communication, empathy, and mutual respect.
- The role of leadership in creating a positive safety culture.
#utilitiesafety #safetyculture #humanconnection #100thmonkeyeffect #workplacewellbeing #safetyleadership #utilityindustry
You can read the current magazine at Incident Prevention Magazine.
Subscribe to Incident Prevention Magazine – https://incident-prevention.com/subscribe-now/
Register for the iP Utility Safety Conference & Expo – https://utilitysafetyconference.com/
Special Series – Influencing Safety Pt. 9 – Beyond the Buzzwords – Creating a Culture of Safety
Are you tired of hearing the same safety jargon without seeing real change? Join Bill Martin, President and CEO of think Tank Project, LLC, and Kate Wade, Editor of Incident Prevention magazine, as they dive deep into the root causes of workplace injuries and fatalities. Discover how to move beyond motivation and empty slogans to create a truly safe and connected work environment.
Key Takeaways from this podcast:
- Importance of Synchronization: The way forward in safety management involves creating a synchronized workforce where everyone is connected on a deeper level. Synchronization allows for better communication and understanding, reducing the chances of injuries and accidents.
- Action Over Motivation: Motivational speeches and slogans alone are insufficient to bring about real change in workplace safety. There needs to be actionable steps that translate motivation into tangible improvements on the ground.
- Understanding Human Behavior: The podcast emphasizes that much of human behavior is automatic, driven by the brain’s need to conserve energy. Safety programs should account for this by focusing on changing automatic behaviors rather than expecting constant vigilance.
- The Role of Leadership: Effective leadership is about asking the right questions and involving workers in safety decisions. Leaders should model the behavior they want to see and create environments that encourage participation and ownership of safety practices.
- Continuous Learning and Experimentation: The podcast suggests that safety improvements should be approached as ongoing experiments, where teams try out new ideas, evaluate their effectiveness, and adjust accordingly.
- Dealing with Resistance: Resistance to change is natural, especially in large organizations with many layers. The podcast highlights the importance of addressing this resistance by aligning everyone around common goals and encouraging openness to new ideas.
- Mental and Emotional Health: Addressing mental health issues, such as addiction and depression, is crucial for creating a safe work environment. A connected and supportive team can help identify and mitigate these risks.
- Practical Applications: The podcast concludes with a call to action—what small, tangible change can be implemented on Monday to make the workplace safer? It’s about translating ideas into real-world actions that have a measurable impact.
#safetyculture #workplaceinjury #safetymanagement #safetyleadership #industrialaccidents #safetytraining #safetytips #safetypodcast #accidentprevention #riskmanagement
You can read the current magazine at Incident Prevention Magazine.
Subscribe to Incident Prevention Magazine – https://incident-prevention.com/subscribe-now/
Register for the iP Utility Safety Conference & Expo – https://utilitysafetyconference.com/
Supporting Safety Professionals: A Conversation with Scott Francis, Technical Sales Manager, Westex, a Milliken Brand
Welcome to Incident Prevention’s Utility Safety Podcast, hosted by Kate Wade, editor of Incident Prevention magazine. In this episode, Kate sits down with Scott Francis, the technical sales manager for Westex, a Milliken brand renowned for pioneering protective textiles since 1941. Scott brings decades of experience in the safety industry, especially in the flame-resistant and arc-rated clothing markets.
During this insightful discussion, Scott shares his expertise on the latest advancements in flame-resistant and arc-rated apparel, the importance of live demonstrations, and how Westex is leading the way in educating safety professionals. He also touches on the challenges of balancing cost and safety standards, and the critical role of comfort in ensuring protective clothing is worn consistently.
Whether you’re a safety manager looking to enhance your PPE program or simply interested in the latest trends in utility safety apparel, this episode is packed with valuable information.
Key Takeaways:
- Impact of Live Demonstrations: Live flash fire and arc flash events leave a lasting impression, helping safety professionals understand the severity of thermal hazards.
- Survivor Stories: Hearing from thermal exposure survivors like Brad Livingston emphasizes the real-life consequences of not wearing proper PPE.
- Education and Training: Westex offers extensive educational resources, including webinars, regional safety conferences, and online materials to keep safety managers informed.
- Balancing Cost and Safety: The competitive landscape in flame-resistant fabric manufacturing drives innovation and helps maintain affordable prices without compromising safety.
- Comfort Equals Protection: Comfortable PPE is more likely to be worn consistently, directly impacting worker safety.
#UtilitySafety #FlameResistantClothing #ArcRatedApparel #PPE #WorkplaceSafety #SafetyPodcast #IncidentPrevention
You can read the current magazine at Incident Prevention Magazine.
Subscribe to Incident Prevention Magazine – https://incident-prevention.com/subscribe-now/
Register for the iP Utility Safety Conference & Expo – https://utilitysafetyconference.com/
Do you have insight to share with the utility safety community?
Contact us with your podcast topic and 2-3 learning objectives to be considered for our next podcast episode.
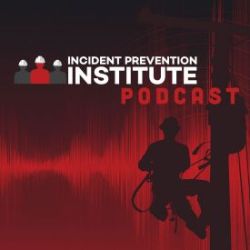