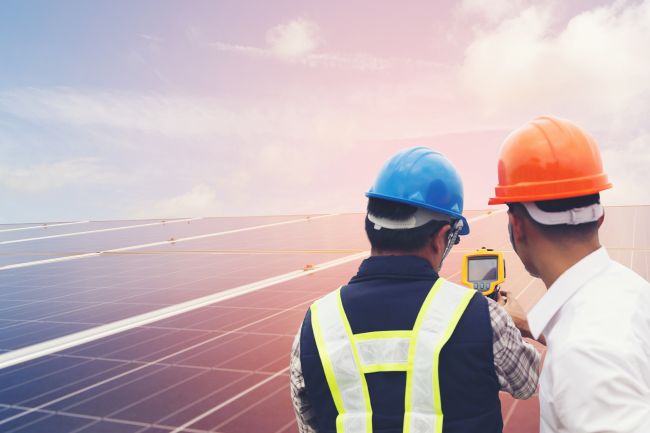
Designing a Safe and Reliable Electrical Maintenance Program
Begin the process by adopting a monitor-inspect-manage approach.
The critical importance of power to every aspect of our world cannot be overexaggerated. It must be generated and distributed effectively to end users, and any disruption in that process means loss of operations, money and, in extreme cases, life. Therefore, the reliability of power creation and distribution must be continually safeguarded and improved. This doesn’t happen by chance or through reactionary maintenance tasks; rather, it must be focused on from the early design stages and continue through the life of the assets tasked with these functions.
Adopting a “Monitor, Inspect and Manage” approach is a proactive way to avoid the concerns at hand by maximizing the value of workforce time and skill. Scalability is no longer an issue when, instead of needing to go through the time and cost of expanding their workforce, an organization can apply the technologies at whatever volume is needed. These reliability technologies should be specified with the engineer and OEM at the initial design/build stage but can also be retrofitted into existing equipment through a simple and inexpensive process.
Monitor
With the use of a wireless monitoring system on transformers and throughout substation electrical equipment, asset conditions can be continually collected, trended and assessed. Monitors feed data through a gateway to software and apps, allowing the information to be continually accessed from workstations and mobile devices.
When the new equipment arrives from the manufacturer with these monitors built in, customized parameters can be set for the specific operating and environmental conditions the asset is exposed to that will keep it within a “safe zone” to maximize functional reliability. When the asset condition data exceeds the custom parameters, alarms can notify electrical technicians of a possible issue that may require inspection. Keeping human interaction with equipment to only instances when inspection of possible faults is deemed necessary not only minimizes risk to workers but eliminates the human error threat to asset functionality.
Inspect
Once the wireless monitoring system notifies technicians of a possible issue with a transformer or other piece of electrical equipment, the use of pre-installed inspection windows on the asset allows for a safe, efficient method of inspecting and assessing any possible issue during an energized condition. Once solely designed for thermographic inspections using infrared cameras, advancements in manufacturing have led to the inclusion of ports that also allow for ultrasound technologies to be incorporated into the inspection. Visual, infrared and ultrasound inspections can be done simultaneously by a single employee.
Additionally, this design protects inspectors from risk of arc flash/electrocution, removes the need for bulky and expensive PPE, and allows the inspection to be accomplished in a more efficient manner. Not only does this represent a major process improvement driven by original design, but it also falls in line with the most recent NFPA 70E updates and continues to protect critical assets from human interactions/mistakes that may cause failure.
Manage
The data collected during inspection can then be stored through an intelligent asset management solution, which are tags that come attached to the pre-installed inspection windows. From the asset location, information can be transmitted into a dashboard system that is also accessible from workstations and mobile devices.
Customizable routes can be established prior to, and condition reports generated after data analysis to further increase efficiency. These designed aspects allow managers to assess operations and make decisions on how best to increase mean time between failure, or MTBF.
Training
One major issue facing the industry is a coming wave of retirements from the workforce, with fewer new workers entering the industry than the pending need created by this exodus. As the electrical industry continues to expand around the globe, creating the need for a larger workforce, the problem is multiplied. The only way to succeed is to capitalize on reliability technologies designed into systems that allow the industry to do more with less.
While designing for safety and reliability on the equipment side should drive the overall process toward continuous improvements, the proper tools are only as good as the proper hands wielding them. Hardware and software designed/specified by the engineer and constructed by the OEM are useless if the people responsible for their oversight do not have the proper training.
Shifting to a new system for the electrical maintenance team means training for new and veteran staff alike. With “Monitor, Inspect and Manage,” the use of technology allows for single individuals to accomplish inspection tasks with minimal training. Specialized skill sets of electrical-focused staff can be used for actual necessary maintenance/repair activities.
A COVID-era issue with learning is that many educational institutions have transitioned to online models. The electrical world can benefit from adding this type of education and certification to on-the-job training programs. These online systems offer on-demand educational and training resources that teach the use of these specific reliability technologies. The workflow being streamlined means that the skill set requirements can be minimized to specific tasks.
Conclusions
From the very inception of new equipment design and manufacturing, all possible measures to ensure asset reliability should be specified and implemented. These measures should prove themselves to be learnable, repeatable and continued throughout any changes in the workforce to cement the successful practices into the culture of the role requirements.
By providing around-the-clock coverage, remote monitoring of transformers and other critical power assets cuts down on the routine tasks required of technicians focused on engineering and electrical operations. When an alarm notification is received, inspection windows allow an individual technician to easily perform visual, infrared and ultrasound assessments of the energized equipment. The data collected on the asset can then be stored, trended and analyzed through the management software. This process increases the mean time between failure by allowing for planned shutdowns and maintenance only when they are necessary.
Staffing issues brought about by the combination of an expanding market and a shrinking labor pool can be overcome by streamlining operations through technology. Both hardware and software can be easily integrated at minimal expense, and the employees responsible for their use can be trained through a combination of online and on-the-job training.
About the Author: For over 30 years, Martin Robinson, IEng., CMRP, CRL, has been a pioneer in the field of condition-based maintenance technology. A recognized authority in the field of infrared thermography, he currently serves as the CEO of IRISS (https://iriss.com), a leader in safety and reliability solutions for critical asset monitoring, inspection and management. Robinson is also a member of IEEE and NFPA, a standing member of CSA Z463 and a member of the IEEE P1854 working group.
- From My Bookshelf to Yours: ‘It’s Your Ship’
- June – July 2022 Q&A
- OSHA Electric Power Standards – Simplified
- Traffic Cones and Flashing Lights
- Does Positive Feedback Improve Safety?
- Mitigating Heat and Cold Stress with FR/AR Clothing
- Best Practices for Bucket Truck Rescue
- Designing a Safe and Reliable Electrical Maintenance Program