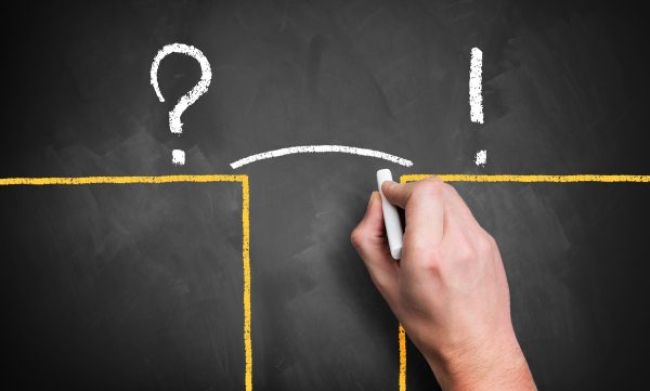
A Targeted Approach to Safety Gap Analysis
Gap analysis is an effective tool that can help improve the reliability of an organization’s safety system.
Does a gap exist between lagging indicator performance and the reliability of industry companies’ safety systems? The bad news is that our work in the industry has led us to believe the short answer to that question is yes. The good news is that our work in the industry has led us to develop an approach that makes gap analysis an effective tool to improve safety system reliability for companies within the utility construction industry.
Our Approach
Our approach to gap analysis began when working with a large utility company to help contractors struggling with safety performance. These contractors had experienced a serious injury or fatality, OSHA violations or a series of potentially serious incidents.
To date, we have performed gap analyses for over 50 companies. Through those collaborations, we have discovered that gap analysis provides immense value to organizations when the approach targets the most critical safety systems.
Elements of an Effective Gap Analysis
The systems targeted in our approach are leadership, policies, training, risk assessment, observation, culture, subcontractor management and incident analysis.
Leadership
The most effective leaders demonstrate passion and concern for safety through direct engagement. We have found that many top-level leaders are unaware of their lack of engagement within the safety program and its negative impact on safety performance. Employees can also be uncomfortable addressing these issues through established communication channels. Including leadership in a gap analysis provides a neutral, nonthreatening method to identify and address leadership gaps. Following are some of the things we look for when we conduct our analyses:
- Are top-level leaders visible to employees at all levels of the organization through participation in safety meetings and events?
- Are leaders responsible for championing the organization’s safety vision?
- Are leaders trained and educated on relevant and applicable safety topics?
Policies
An effective gap analysis assesses the quality of written policies. The quality and effectiveness of implemented policies and procedures are important but often overlooked. It is common for organizations to develop policy documents and never look at them again until there is an incident, a dispute or a need for disciplinary action. An ineffective policy system leads to a lack of clarity that can ultimately result in noncompliance. Following are some of the things we look for when assessing policies:
- Are policies written to the appropriate audience so that audience can clearly understand and adhere to them, including translating policies into an employee’s native language?
- Are policies relevant to the scope of work?
- Are policies in alignment with the most recent regulations and industry best practices?
- Are policies distilled into a readable, transferable format, or is there just one extensive safety manual?
- Are policies distributed in a manner that makes them accessible?
Training
An effective training system is the cornerstone of any safety program. Most organizations we have worked with allocate a significant number of their safety resources to training employees, and we have found that spending money, hiring staff and building facilities are only pieces of the puzzle. Organizations with dynamic training systems have found a method to integrate their training system into the framework of the entire organization. During our analyses, we look for the following:
- Does the training system allow immediate deployment of content?
- Does the training matrix cover the organization’s work activity and hazard exposure?
- Is the training accessible to employees on demand when they need it?
- Are employees trained beyond the initial onboarding session?
- Is the training content relevant to day-to-day work activities?
- Are training records readily accessible?
Risk Assessment
Preventing the next serious injury or fatality begins with having established methods and processes to identify hazards and effectively mitigate them. We have found this is a significant challenge for the organizations we have worked with because it can be difficult to transfer knowledge and expectations from the leadership level to the craft level. This is greatly magnified for many industry partners because they employ a transient workforce hired to perform work with exposure to hazards that, if left unmitigated, can lead to catastrophic results. To gain an understanding of the effectiveness of an organization’s risk assessment methods and processes, we look at the following:
- Is the safety department involved in the project planning process?
- Are there effective pre-job planning processes in place?
- Are quality tailboards conducted every day?
- Are craft leaders formally trained on how to conduct a pre-job briefing?
- Is there a good-catch/near-miss program in place?
- Is tailboard and near-miss data tracked and analyzed?
- Are crews asked to perform a daily post-job review?
- Is hazard assessment data integrated with the other safety systems?
Observation
Observations are a practical method to confirm that employees meet an organization’s safety requirements and expectations. Based on our experience, we have found that many organizations do not have an established observation program that allows for observations to be conducted consistently, data to be collected electronically, and the collected observation data to be tracked and analyzed. We have noticed that organizations with weak observation programs encounter high levels of policy noncompliance, repeated incidents and incident rates above the industry average. It is essential to assess the performance of the observation system as part of any safety gap analysis. Following are some things we consider when assessing observation programs:
- How often is each crew or work location observed?
- What is the quality of the observation?
- Are the observers knowledgeable and trained to be effective?
- Do other employees besides safety professionals perform observations?
- Is there a process to track observation data for analytics?
- How is observation data presented to crews and management?
- Are observations documented electronically?
- Are open items discovered during observations tracked to closure?
Culture
An organization’s culture represents its values, norms and principles. This is the system where we often observe the most significant discrepancy between how the organization views the performance of its safety program versus the program’s actual performance. In these organizations, we commonly find employees with low morale, negative perceptions of the safety program, and a lack of trust between employees and the organization’s leaders. To understand the climate of an organization’s safety culture, we look at the following:
- What is the level of employee participation in the safety program?
- How does the organization recognize positive safety performance?
- Does the organization have a program in place to mentor and develop employees?
- Are there opportunities for employees to engage in the safety program beyond the standard methods like training and safety meetings?
Subcontractor Management
A robust management system integrates an organization’s subcontractors and vendors into its safety program. We often find that when organizations utilize these entities, they fail to ensure that their safety systems are in alignment, which can result in hiring unqualified companies, a lack of productivity, poor work quality and increased incidents. Following are some of the subcontractor management items we look for during our analyses:
- Are there established criteria implemented to select subcontractors and vendors?
- Does the company provide continuous support to those subcontractors and vendors?
- Is the company consistently performing observations of subcontractors to confirm they are meeting expectations?
- Are subcontractors and vendors consistently provided timely feedback?
Incident Analysis
The methods and practices used to conduct incident investigations are essential to understanding the circumstances of an event to develop a plan that prevents recurrence. We have observed that many organizations do not have effective investigation methods and processes in place, and we regularly find that the individuals performing the investigations have had no formal training nor do they follow a standard process or methodology. As a result, these organizations miss the opportunity to use incidents to make impactful changes to their program and educate their workforce. Here are some items we consider when assessing an organization’s incident analysis system:
- Does the organization have an established and consistent method to conduct investigations that identifies the incident’s root cause and causal factors?
- Does the organization conduct a thorough investigation of all incidents?
- Are there established methods to consistently and openly communicate incident-related information to employees?
- Do the corrective and preventive action plans initiate systemic change?
Conclusion
Through our experience performing gap analyses for many organizations, we have learned that an analysis that targets the most critical safety systems provides immense value to any organization. Although every organization is unique, we have discovered that leadership, policies, training, risk assessment, observation, culture, subcontractor management and incident analysis are universal. Targeting the most critical systems identifies the most critical system gaps, leading to critical actions that increase system reliability and drive continuous improvement.
About the Authors: Thomas Arnold, CSP, CUSP, is a principal at Professional Safety Solutions LLC (www.prosafellc.com) with over 20 years of experience in risk management, including the areas of financial risk, data analysis, project planning and management, and policy writing. He provides practical and innovative risk management solutions geared toward a measurable reduction of risk.
Michael Anderson, CSP, CUSP, is a senior consultant for Professional Safety Solutions LLC with more than 15 years of construction safety leadership experience in the electric transmission and distribution, renewable energy, gas distribution and mechanical sectors. He understands the challenges that come with implementing a safety culture in today’s business climate, and he has directed and led superior safety performance for large-scale organizations.
- From My Bookshelf to Yours: ‘Who Moved My Cheese?’
- 6-Step Method for Safety Harness Inspections
- A Targeted Approach to Safety Gap Analysis
- Crash Analysis: A Personal Story
- Electrical Protective Equipment and Live-Line Tools
- Ground Gradient Step Potential and PPE
- Increasing Safety Through Underground Integrity Management
- Influencing Crew Safety