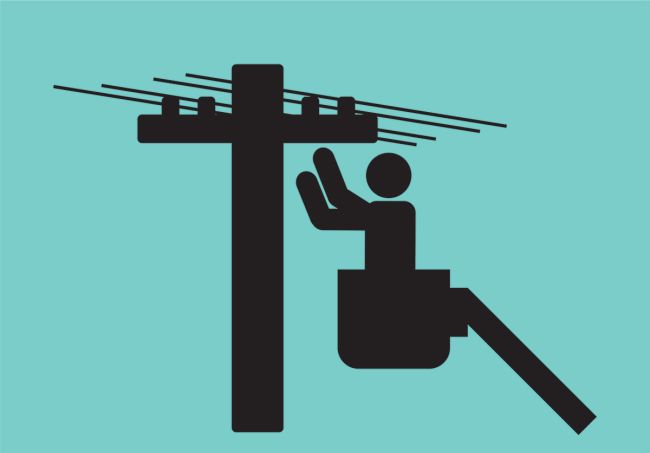
The 8 Habits of a Highly Effective Safety Culture
Developing these habits helps to create a safety culture in which it is safe for employees to fail.
I began writing my new book – “The 8 Habits of a Highly Effective Safety Culture” – in 2004 while working as a civilian contractor for Kellogg Brown & Root in Iraq. I was the area HSE manager for a large portion of the Logistical Civilian Augmentation Program #3 Project. Our contract required us to hire a certain percentage of local national employees (Iraqis) to help build bases for the U.S. military and coalition forces. This was to help the local economy and to teach the Iraqi people new skills that they could use once we were gone. In theory, this was a great idea; in reality, however, it was a safety nightmare.
Being a U.S.-based company, we were required to follow OSHA 29 CFR 1926 (Construction) and OSHA 1910 (General Industry), and in some cases U.S. Army Corps of Engineers EM 385. But none of this translated to the way of life in that part of the world. Without turning this into a discussion of religion, I just need you to understand that many people in Iraq believe they have zero control over the things that happen to them. So, bring this culture to an American construction site and I’m sure you can see the difficulties.
In the Beginning
My time in Iraq got me thinking about how safety cultures have evolved over the past few hundred years. Note: For the purposes of this article, the term “safety culture” refers to what your employees are doing when no one is watching. Safety cultures can be traced all the way back to the beginning of the Industrial Revolution in 1760. While workplace safety now and workplace safety back then are two very different things, 1760 marked the first accounts of company rules being written to keep employees from hurting themselves.
In 1802, the very first legislation dealing with workplace safety was passed. Due to an outcry over child labor conditions, Sir Robert Peel introduced the Health and Morals of Apprentices Act 1802, commonly known as the Factory Act. It applied to all textile mills and factories employing three or more apprentices or 20 employees, and it required factories to have sufficient windows and other openings for ventilation; be cleaned at least twice yearly with quicklime and water; and limit working hours for apprentices to no more than 12 hours a day, excluding time taken for breaks.
While limited to a small portion of the workforce and with limited enforcement, the Factory Act is still generally seen as the beginning of health and safety regulation.
It was 31 years later before any other related laws were passed. In 1833, workers tired of spending over 12 hours a day in factories began a movement – known as the Ten Hours Movement – to reduce working days to 10 hours. Pressure from the group led to the Factory Act of 1833, which extended the 12-hour working limit to all children and included wool and linen mills. Perhaps the most important development, however, was the introduction of factory inspectors.
Over the next 137 years, the following laws were passed to help workers:
- In 1837, “duty of care” was introduced.
- From 1842 to 1878, several acts helped protections strengthen toward women and children. They were prevented from working in underground mines, the use of child labor to clean and maintain moving machinery was stopped, and a 56-hour workweek for women and children was introduced.
- The Employers’ Liability Act was signed in 1880.
- From 1880 to 1969, a number of acts and reforms were passed that improved upon health and safety regulations. Employers were required to provide safeguarding for machinery, the legal working age was gradually raised, and more and more inspectors were appointed across industries.
- On December 29, 1970, Richard Nixon signed the Occupational Safety and Health Act. The Occupational Safety and Health Administration, more commonly referred to as OSHA, was created in April 1971.
The 1970s to the 1990s
In the early 1970s, company philosophies were simple: “Don’t get hurt.” Company leaders honestly didn’t think this new federal department – OSHA – would issue fines for unsafe conditions.
The first citation written by OSHA was to Gimbel Brothers Department Store in New York City. They found two violations and, while a citation was written, no fine was issued.
The first fine was issued October 23, 1972, to Diane Inc., a manufacturing company in Manhattan, for $45 (the equivalent of about $300 today). It was then that the new company philosophy became, “Get caught getting hurt and get fired.” While this did have a profound effect on the way companies viewed employee safety and helped reduce the number of accidents, we found out later that it was counterproductive.
Sometime around 1980, the new company philosophy became, “Accident occurs, discipline employee, create new policy and enforce the new policy.” Then, when another accident happens, it starts all over again: accident – discipline – create new policy – enforce new policy.
In the early 1990s, we started doing more behavior-based safety (BBS). While Ford Motor Co. was the first company on record to use the BBS model, DuPont developed the first widely utilized BBS program called Dupont STOP (Safety Training Observation Program). Now, for over 30 years, we’ve been trying to fix worker behaviors to avoid accidents.
2000s
The 2000s have brought about very few significant changes. There have been numerous variations of the BBS program, but nothing that will take us to the next level.
It is time for a paradigm shift in how we view and do safety.
In my new book, I discuss eight habits that will help to create a safety culture in which it is safe for your employees to fail. We know errors will happen, and the fact is, errors are predictable. So, if we build them into the process, then employees can do their jobs in very complex environments and help us create the systems to protect them.
The Eight Habits
The first three habits are (1) stop making safety a priority – it should be a value; (2) make it safe to raise concerns; and (3) make safety a responsibility of operations. These habits are designed to create a just safety culture that then enables you to truly focus on leading indicators and stop accidents before they happen.
That’s where the fourth habit – focus left of zero – comes in. In a just culture, you can track and trend the information you get from the field. When these first four habits are done in conjunction, we can actually see an accident before it happens and implement measures to stop it.
Stop managing people is habit five. This habit focuses on leadership principles that are essential in creating a culture that is sustainable in every environment. The only constant in life is that things will change. Be prepared to lead your team no matter what comes your way.
Habit six is to stop trying to fix the worker and fix the work; habit seven is find the STCKY (stuff that can kill you) and stop the SIF (serious injuries and fatalities). When I originally wrote the eight habits, these two were based on BBS and using the Heinrich Triangle to stop unsafe acts/behaviors, thereby reducing the number of significant injuries and fatalities. While BBS has helped reduce overall incident rates, it has done little to reduce the number of fatalities we have each year on job sites around the country. So, developing these two habits is going to take quite a shift in the way we view and do safety.
Note: “The 8 Habits of a Highly Effective Safety Culture” was written using data from all industries. While a few segments of industry employed behavior-based principles to effectively reduce incidents and fatalities, BBS was not universally effective in reducing fatalities across all places of employment. The electrical utility industry, however, has done more than most when it comes to implementing human performance, and it shows in our reduction of fatalities and overall injuries.
The final habit – stop trying to influence everyone – is one that will help you implement the first seven. When you try to influence everyone, you end up influencing no one.
Human Performance Principles
I want to mention here that all safety programs should be built on the principles of human performance. I use these five principles designed by Todd Conklin:
- Error is normal. Even the best people make mistakes.
- Blame fixes nothing.
- Learning and improving are vital. Learning is deliberate.
- How you respond to failure matters. How leaders act and respond counts.
- Context influences behavior. Systems drive outcomes.
You, however, can select as many or as few principles as you’d like. Choose the ones that fit your organization. In my book, I list a total of 25 principles called “The Incomplete List” because I’m sure there are others, it just depends on your organization and what it is you are trying to accomplish.
Final Thoughts
During the process of writing “The 8 Habits of a Highly Effective Safety Culture,” I had quite a few aha moments and learned so much from all of you in the safety industry. Here are a few final takeaways for you to consider.
- Workers aren’t the problem; workers are the problem solvers.
- Safety doesn’t prevent bad things from happening; safety ensures good things happen while workers perform tasks in complex and adaptive work environments.
- Safety is not defined by the absence of accidents but by the presence of capacity.
About the Author: Rod Courtney, CUSP, began his career in the U.S. military. After working for a couple different companies, he went to Iraq with Kellogg Brown & Root in 2003 and was the HSE manager for the largest construction project on the planet. In 2007, Courtney began work in the renewable energy sector, building thousands of megawatts of wind turbines and solar plants across the U.S. He is now the HSE manager for Ampirical and serves as a board member for the Utility Safety & Ops Leadership Network.
- The 8 Habits of a Highly Effective Safety Culture
- Advancing Workforce Skills Using Simulation-Based Training
- Thermal Protection for Electrical Work
- From My Bookshelf to Yours: ‘No Compromise’
- Understanding Wind Speed Limitations on Utility Equipment
- The Importance of Proper Coverup: Two Real-Life Tales
- OSHA Electric Power Standards – Simplified