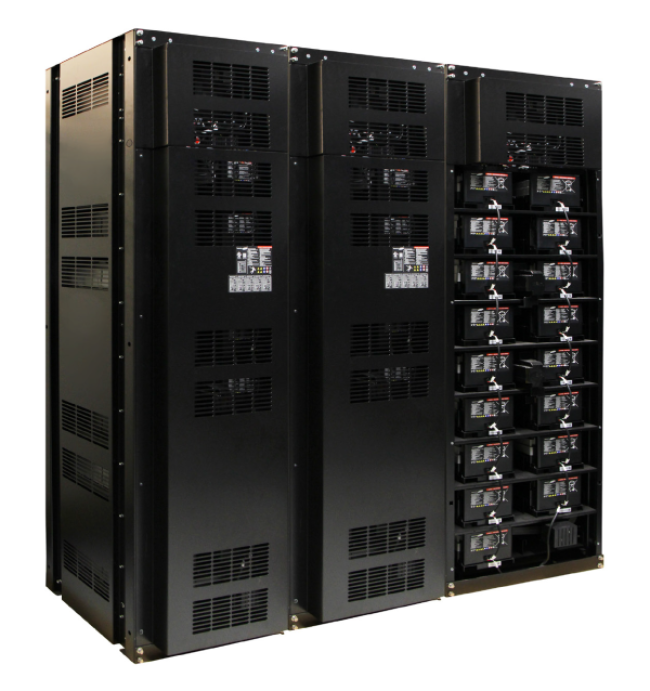
Direct Current Hazards and Protection Strategies
Employers whose employees work around DC systems should establish a safety management system that addresses potential DC hazards.
Protection from direct current (DC) arcs is the latest trend in electrical safety. The growth of commercial and personal electric vehicles (EVs), photovoltaics (PVs), battery backups and grid storage systems makes refreshers necessary. This article introduces some of the DC fundamentals so that end users can build on these concepts to optimize existing electrical safety programs. It will explain the various DC sources, hazards, applicable safety standards and protection strategies.
Direct Current Sources
DC is produced from PVs or solar panels, batteries and smart power electronic devices known as DC converters. The converters utilize semiconductor devices for rapid smart switching of alternating current (AC) using intelligent circuit configurations, and circuits are used to produce DC. PVs use visible light – some infrared and very limited ultraviolet – to produce power. Previously, this power was converted to AC and dispatched to the power grid. These days, the power is used to charge large battery energy storage systems. These large batteries can store several hundred megawatts and, through intelligent automated systems, manage peak loads and power reserves. Although battery energy storage systems can be charged from the power grid, clean energy systems use renewable energy sources.
Batteries are a complex topic, but for the purpose of this article, only the most common battery systems are discussed. DC power for critical services – such as substation protection, fiber-optic panel power, fire protection systems, safe shutdown systems and emergency lighting – is traditionally provided by long-life lead-acid-type batteries. Picture 1 shows a typical substation lead-acid battery layout with a battery charger (DC converter).
Picture 1: Critical Power Battery
New systems transitioned from lead-acid cells (note: a cell is a single unit, and a string of cells is a battery) to lithium-ion, shown in Picture 2.
Picture 2: Lithium-ion system consisting of a battery, smart chargers and AC/DC power disconnects.
The benefits of newer-generation lithium-ion cells are covered extensively in several publications. These benefits propelled this cell to be the DC source of choice for mobility applications and battery energy storage systems.
DC Safety Standards
Lithium-ion battery systems may present various voltages. Critical power systems and family-type EVs are generally low voltage (<600 volts). Battery energy storage systems and commercial EVs (e.g., buses, cranes, semis) are generally >600 volts with battery energy storage systems running into several thousand volts and EVs topping up to approximately 1,500 volts. OSHA standards do not differentiate between AC and DC for a shock hazard.
Power generation, transmission and distribution utilities follow OSHA 29 CFR 1910.269(l)(8)(i), which requires the employer to identify electric arc flash hazards. Commercial industrial users follow OSHA 1910.335(a)(i), which requires the employer to identify and mitigate or control all electrical hazards or provide PPE. Many users, including automotive users, have decided to follow a combination of the referenced OSHA standards but also implement the principles in NFPA 70E.
Presently, two common guidelines take precedence on the arc flash hazard calculations: the iterative method using the Stokes and Oppenlander model and the Kinectrics DC model built into ArcPro 4.0.
Electric Shock Protection Strategies
An uninformed user may think that DC contact is relatively safe since DC sources are closed circuits and isolated from the ground (positive and negative poles are floating relative to ground). This is not true because a capacitive coupling may be present to ground or the negative pole may be grounded at the source. Protection against electric shock is thus essential.
Hazard elimination isn’t always possible since batteries cannot simply be turned off like an AC generator, making safety through design the first tier of risk control in such instances. Modular designs allow for switching off cells until a safe voltage is present at the work area. Another common approach is maintaining a substantial distance between the positive and negative phases to ensure that accidental contact is not possible. In addition to these, manufacturers provide insulated, retractable or hidden terminals to achieve a “finger-safe” (i.e., safe to touch) condition.
When working with DC, PPE can be very effective against shock. The first and perhaps most effective pieces of PPE are rubber insulating gloves meeting ASTM D120. These gloves are generally used with leather overprotectors meeting ASTM F696. Hand protection is best complemented with leather footwear tested to ASTM F2412 with an electrical hazard rating. If footwear isn’t regulated or an additional level of protection is required, the employer may mandate the use of dielectric floor mats meeting ASTM D178. Before permitting work, however, OSHA requires protection against incidental contact by using electrically insulated hand tools meeting ASTM F1505.
When DC busbars are exposed (e.g., solar farm converters or data centers), the employer may mitigate contact or the shock hazard by ensuring that no energized circuit parts or conductors are exposed to the worker. Dielectric blankets meeting ASTM D1048 are suitable for such applications. A more cost-effective option, under the guidance of a suitably qualified engineer, are rubber insulating covers (see ASTM D1049). OSHA’s intent of eliminating the hazard may not be met using this option; however, employers are able to protect against unintentional contact.
Electric Arc Flash Protection Strategies
Although the study of DC arcs is supported by both empirical testing data and research and development work, there is no singular standard or methodology for calculating the arc flash incident energy from a DC source. Most approach the calculations using the methods previously described. At present, the same model is used for renewable power DC, grid power DC and DC batteries. It is currently possible to claim – definitively – that lithium-ion-sourced arcs behave similarly to other DC arcs. Initial studies are limited and there are no records in journals that reference a sustainable arc flash incident from batteries. Sustainable arcs in the literature appear to be exclusively produced from AC or renewable power grid-type DC. This article does not claim that battery arc flash incidents are not possible; rather, it aims at conveying findings from the literature indicating that more work is required.
An article published in the United Kingdom (see https://elecsafety.co.uk/electric-vehicles-and-arc-flash/) lists several examples of when work on EV batteries can create an arc, and it provides some risk control examples. In essence, all cautionary measures applicable to DC electrical shock hazards help control the risk of an arc flash. Additionally, attaining a lower state of charge for a lithium-ion battery indicates a lower incident energy or likelihood of sustaining the arc. Initial studies show that the arc flash energy is likely to be less than the threshold for a second-degree burn if a modular design helps remove battery segments before performing work. If a modular design is not present, such as in a renewable or grid power DC, then protection (i.e., fusing or circuit breakers) set optimally may likely reduce the arc flash energy to safe levels.
In many instances, employers adopt a conservative approach by requiring arc-rated daily workwear (e.g., shirt, pants, face shield) or an arc flash suit. Clothing should comply with ASTM F1506 as it is more than just an arc rating standard. It requires tensile- and tear-strength testing, colorfastness testing, wash-shrinkage testing and flammability testing, along with required quality control systems, as in NFPA 70E. Dual-rated clothing for flash fire and arc flash, and in some cases chemical-resistant PPE, is the optimal approach because lithium-ion cells may experience thermal runaway.
Hand-protective apparel serves a dual function by protecting against both electrical shock and arc flash. Although leather is the most used overprotector, the ASTM F3258 standard allows for non-leather or combination material protector gloves. These may help address the clean-room or clean-conditions limitation posed by leather. The gloves are arc tested and rated, with cut, puncture and even chemical resistance.
Work performed by the NREL, EFCOG DC Arc Flash Working Group (see https://rb.gy/mgr5m) states that DC arcs most closely resemble three-phase (L-L-L) faults. Open-air arc testing to ASTM F1959/F1959M is performed using a single-phase AC arc; presently there are no correlation studies between AC and DC arcs when using the ASTM F1959 open-air arc testing method. Subject matter experts in the field believe that fabric testing is conservative and that the heat flux measurement would display a level of immunity to changes in the source. In other words, existing PPE may not need a separate arc rating for DC sources. However, as with arc ratings of layered systems, the only way to confirm actual performance is through empirical testing. These studies will be carried out sooner rather than later. In the meantime, end users can take comfort in the fact that all arc-rated clothing is flame resistant and non-melting. So, even if the clothing is not optimal, it would not contribute to injuries like synthetic, poly-cotton or cotton workwear.
Other Hazards
Aside from ergonomic concerns, renewable and grid power DC generally do not pose hazards aside from those discussed in this article. Battery systems may expose workers to mechanical, chemical, thermal and health (e.g., respiration, carcinogens) hazards.
Irrespective of the electrical hazards and the gaps in research and standardization, every employer working around DC systems should establish a safety management system. At minimum, this includes a written electrical safety program, risk management systems, electrical safety training, maintenance programs, incident investigation and electrical safety auditing.
About the Authors: Zarheer Jooma is a professional engineer and partner at e-Hazard (https://e-hazard.com). He earned a master’s degree in electrical engineering, is a senior member of IEEE, has convened and chaired arc flash safety standards, and is a member of both ASTM F18 and IEC TC-78. Jooma performs electrical network design, arc flash studies, electrical safety training, incident investigations and auditing. He is also the technical paper review chair for two IEEE journals and the incoming chair for the IEEE Electrical Safety Workshop 2025.
Hugh Hoagland is a mostly retired consultant focusing on ASTM and IEC standards development and arc flash incident investigations.
Brian Shiels is the service line manager for the ArcWear (www.arcwear.com) division of Kinectrics and a leading expert in the testing and development of arc-rated clothing. His professional experience includes quality management as well as the development and testing of thermal protective clothing and equipment. Among other responsibilities, Shiels is a longstanding member of a variety of standards development organizations, including ASTM, NFPA, AATCC and ISO. He earned his master’s degree in textile chemistry from North Carolina State University, with a special focus on protective clothing.
- Understanding Task-Specific Training
- Be Prepared for the ‘Big One’
- The Art of Safety – Unnormalizing Deviation
- October-November 2023 Q&A
- Direct Current Hazards and Protection Strategies
- Employee-in-Charge Requirements
- Using Flame-Resistant and Arc-Rated Clothing to Mitigate Cold Stress
- Nurturing Strong Leadership: An Approach to Professional Development in Skilled Trades
- New 2023 Products to Watch