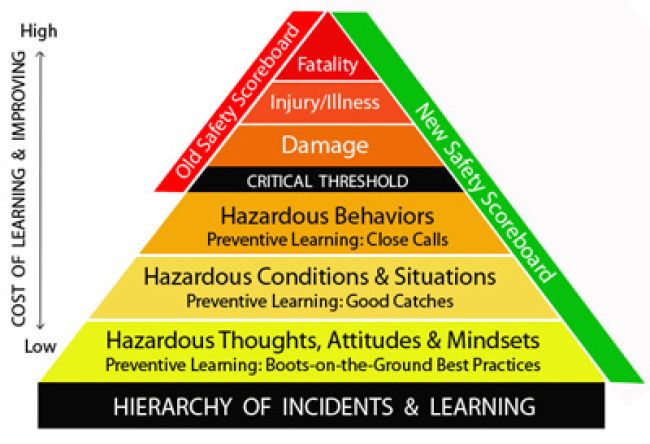
The Hierarchy of Incidents and Learning: Part II
The contractor’s executive team sat across the table from the client’s construction leadership. It was the client’s director who spoke first.
“Let’s ensure everyone is on the same page,” he said. “Over the past six months, you’ve had numerous quality, production and schedule issues, an environmental noncompliance, two injuries and a utility contact that caused a 3,500-customer outage for over six hours. All of this has almost crippled three projects that we trusted you with, and we need to know how all this happened and what you are going to do about it.”
The contractor’s president looked up and humbly replied, “First, I want to apologize for breaking your trust. As for the ‘how’ question, there was no single cause. We missed a lot of good catches and close calls because we weren’t using those indicators on our operational and safety scoreboards, but things are different now. We have a new way of measuring success. What we’ve learned over the past few months is that our workers’ thoughts, attitudes and mindsets affect how much they respect the conditions and situations they face, and that level of respect becomes apparent in their behavior. We’ve been learning about and addressing these issues for the past month, and we’re beginning to see greater operational and safety success. However, we also have to change 52 years of culture, and that’s taking more time and effort than we would like. While I accept the fact that this change will be an ongoing, forever endeavor, I can confidently tell you that if we had begun this earlier, we wouldn’t be sitting here right now.”
The hazardous thoughts, attitudes and mindsets that the contractor’s president pointed to in the scenario above constitute the very first level of the hierarchy of incidents and learning, which I introduced in Part I of this article (see https://incident-prevention.com/blog/the-hierarchy-of-incidents-and-learning-part-i). In that same article, we also took a look at levels two and three of the hierarchy – hazardous conditions and situations, and hazardous behaviors, respectively – and discussed things you and your team members can do to support a continuous growth mindset. It bears repeating that those first three levels have the lowest cost of learning; that is, the higher up the hierarchy’s pyramid you go, the greater an incident’s direct and indirect costs to workers, the project, the company and the customer. You can surmise from the above scenario that had the contractor focused on those three levels earlier in the company’s history, they could have avoided many of the problems they’re now facing with their client.
The Next Three Levels
Now, in the conclusion of this two-part article, we’re going to cover the final three levels of the hierarchy, and the ones with the greatest cost of learning: damage; injury and illness; and fatality. To get to those three levels, we have to cross the critical threshold that leads from a potential issue into the realm of direct harm, which historically has been considered the scoreboard (lagging indicator) by which we measure our level of safety. However, most safety-progressive organizations today see the error of this logic in that an absence of incidents doesn’t necessarily mean there’s a presence of safety. These organizations create leading indicators that measure and guide their programs by capturing lessons learned at the lowest possible levels of the hierarchy.
Let’s explore these three levels of direct harm, how they’re tied to the first three levels of the hierarchy, and what can be done to better understand and more proactively address them.
Damage
We often think of damage as “stuff getting crunched,” but it’s time to expand our definition to include other types of damage.
- Property damage: Damage to property often occurs when we lose situational awareness.
- Environmental damage: Something unexpected happened, and we impacted water, birds, fish, worm snakes, the Indiana bat that sought refugee status in Ohio … and this could damage both our production level and reputation.
- Production damage: Our unintended results harmed profitability and possibly impacted the project schedule, both of which also could damage our reputation.
- Reputational damage: When our reputation is damaged, others’ trust in us weakens because the very essence of our character is called into question.
- Relationship damage: When our relationships with others are damaged, that affects our willingness to work together and effectively communicate.
Breaking New Ground with Our Understanding of Damage
We must realize that our behavior can damage our personal reputation, as well as the reputations of the crew, company and client. That costs everyone involved a lot more than the price tag associated with an object we crunched or the wetland we impacted. I can remember the days when I would hear operational managers say things like, “Torn-up equipment is just a part of getting the job done” or “I don’t care if the guys don’t get along or aren’t happy – I just want those next three structures done before Friday.” Thankfully, those days are long gone, at least in successful companies that strive for continuous improvement and measure success not merely by production levels but by doing the job right and going home unharmed.
We also need to realize that if we let our negative thoughts lead to negative attitudes – which shape our mindsets that direct our behaviors that can damage our relationships – then our level of mission success will be diminished. That’s because our communication and coordination will be less than what they could have been if we weren’t upset with other crew members, contractors or client representatives.
Injury and Illness
Injury and illness are both forms of harm, but it’s important to understand definitions for physical injuries and illnesses as well as emotional and mental ones.
- Physical: This is traditionally what we think of when we hear the word “harm”; it shows up as an injury or illness that is visible to the injured person and others.
- Emotional/mental: This is damage to someone’s thoughts, attitudes and mindset. It steals their focus and creates additional hazards that show up on the job site and at home. Remember, our mission has two parts: to do the job right and to go home unharmed today. If our workers are going home upset, angry or beat down to the point that they can’t connect with their families, need alcohol to get work off their minds or can’t sleep, those issues must be addressed. Our measures of success have to grow to include the overall health of our workforce, not just their physical well-being.
Breaking New Ground with Our Understanding of Injury and Illness
Our emotions affect our thoughts, attitudes and mindset. In turn, that affects our ability to clearly see reality and connect with the world around us. We must deal with all the things that affect the hierarchy of incidents and learning – not just visible physical injuries and illnesses. We also need to understand that emotional injuries often begin as some form of perceived disrespect, and when that’s not cleared up or dealt with immediately, it can lead to bigger issues, such as costly labor disputes and more severe incidents.
Fatality
Loss of life is the ultimate price. However, let’s expand our definition of “fatality” to include workers who unnecessarily quit or were terminated, which has a major impact on those workers, their loved ones and their former co-workers.
- Physical fatality: There’s a funeral, tears and regret, along with high physical, mental, emotional and financial costs to pay, and that’s an invoice that will forever be imprinted on your heart and mind.
- Work-life fatality: Perhaps there’s an unnecessary termination or a worker quits a bad manager. I’m not talking about the guy who needed to be fired; I’m talking about the person who we wouldn’t have had to fire – or who wouldn’t have quit – if negative thoughts, attitudes, mindsets and behaviors had been dealt with more effectively on the job site.
Breaking New Ground with Our Understanding of Fatalities
There are high costs to replacing a worker, not the least of which are training and loss of production while the new person gets up to speed with both the work and the crew dynamics. There’s also a cost to the worker’s family – a loss of income – when that worker is unnecessarily terminated or quits. The simple reality is that if leaders deal with issues in a clear, concise and timely manner – as discussed in Part I of this article – we may not need to replace as many workers, and that’s good for everyone.
Conclusion
When it comes to using the hierarchy of incidents and learning in your organization, perhaps the most important point to understand is this: If your goal is to prevent damage, injury, illness and fatalities on your job sites, you must take the steps necessary to identify and address hazardous thoughts, attitudes, mindsets, conditions, situations and behaviors. By doing so, your employees will have the greatest opportunity to do the job right and go home unharmed – today and every day.
About the Author: Jesse Hardy, CSP, CIT, CUSP, is vice president of HSE for Supreme Industries, a Harwinton, Connecticut-based contractor that specializes in right-of-way clearing, building access roads, drilling and pole pulling.
- Wood Pole Fall Restriction Device
- Project Management Safety Certification Program
- Best Practices for Using Your Aerial Device Jib to Handle Transformers
- The Hierarchy of Incidents and Learning: Part II
- Mother Nature vs. FR/AR Clothing
- Arc Flash and Face Masks
- Opinion: Looking to the Future During an Unprecedented Time
- June-July 2020 Q&A
- Motivators: To Improve Performance, Understand What Drives Your Behavior