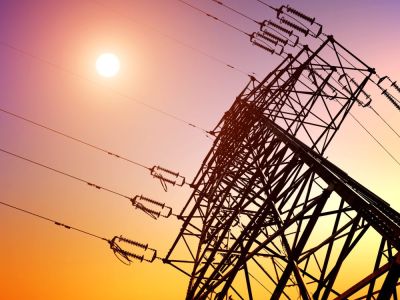
Built In, Not Bolted On: Using Safety to Drive Operational Excellence
Employers in the electric utility industry are currently working on initiatives in various areas of their businesses, including safety, quality, production, leadership, and human and organizational performance (HOP). These are important programs, but it’s unlikely they’ll fully achieve their intended objectives if employees don’t have a firm grasp on how these various aspects of work impact one another – and the ideal order in which they should be addressed.
As someone who has spent a great deal of time studying HOP and teaching its principles to others, I understand that part of the philosophy is building an organizational system that enables employees to complete their work using processes that make sense to them, are easy to follow and…
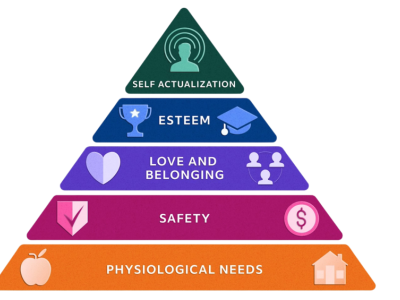
Making the Safety Connection: The Impact of Total Well-Being in the Workplace
Utility workers perform essential tasks that touch millions of lives every day. The critical nature of the services they provide coupled with the perilous nature of their tasks exposes these workers to life-threatening hazards. This is why the industry highly values and prioritizes safety.
Many utility companies operating today have made significant strides in improving their safety culture. Critical risk management programs and a human performance mindset have become increasingly common as organizational leaders more fully understand the link between human behavior and risk. These companies have moved beyond the traditional safety model that primarily focuses on accident prevention, opting instead to embrace risk reduction strategies.
Use…
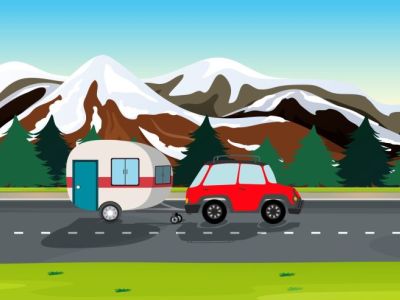
The Roadmap to Gaining Senior Leader Buy-In for Safety Initiatives
| Sharon Lipinski, Wesley L. Wheeler, SMS, CESCP, MSP, and Keith Wheeler | Safety Management, Leadership Development
In a recent survey we conducted, 97% of safety professionals who responded confirmed that gaining senior leader buy-in for their safety programs was either very important or extremely important to them.
This research project was a joint effort between the National Electrical Contractors Association, HR Resources of the Carolinas LLC and Habit Mastery Consulting, with the purpose of discovering the secrets to gaining greater senior leadership support for safety initiatives. Our research included surveying 128 safety professionals and conducting in-depth interviews with 15 deeply experienced safety professionals.
We revealed our research results at the October 2024 iP Utility Safety Conference & Expo in Allen, Texas, sharing with attende…
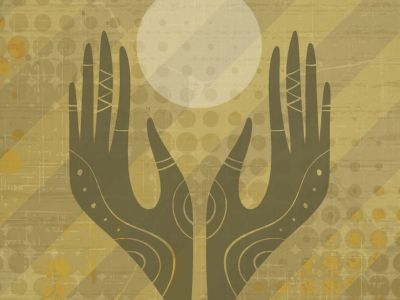
An Inextricable Link: The Safety Benefits of Holistic Wellness in the Workplace
There is an inextricable link between employee safety and mental and physical wellness that is often overlooked. Taking a holistic view of your employees includes looking wholly at each person to better understand and address their mental and physical health challenges and related distractions that can affect their personal safety and the safety of others.
Additionally, demonstrating you care about your employees’ well-being can translate into improved morale, engagement, productivity, and recruitment and retention.
At its foundation, your employee safety program should be viewed as an act of caring about your employees. However, our safety focus can often be siloed. It’s time to break through the silos and take a more comprehensive look a…
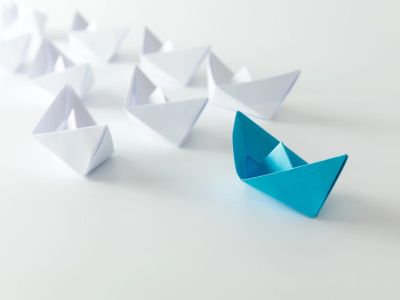
The Transformative Impact of Training for Frontline Managers
Frontline managers are crucial because they bridge organizational goals and frontline employees. They significantly influence workplace dynamics and performance outcomes. In this context, my company surveyed 110 safety professionals and interviewed 10 safety professionals across various industries – including construction, utility, wind energy, public works and manufacturing – to gain insights into the current state of frontline leadership skill development within organizations.
Our research reveals that the significance of frontline leadership skills cannot be overstated, as highlighted by this poignant quote from one construction company’s safety director: “We either have somebody who knows how to manage, who sets an example, who sees a…
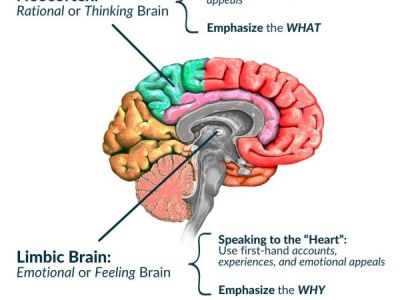
Getting to the Heart of At-Risk Behaviors with Facilitative Learning
In a recent workshop with a client in southeast Louisiana, a breakout session reached a tipping point. The rhythmic flow of dialogue among the seven supervisors in the group found an unscripted but purposeful path of its own. The task given to the group involved identifying at-risk behaviors or shortcuts likely to occur in their work environment. Participants were also asked to discuss motives for the identified behaviors and strategies for shifting perspectives regarding them. The intent of the three-part exercise, which was deliberately constructed to achieve the resulting outcome, was to pull information from the collective experiences of those in the session needed to improve operational safety. My role in the process wasn’t to instruc…
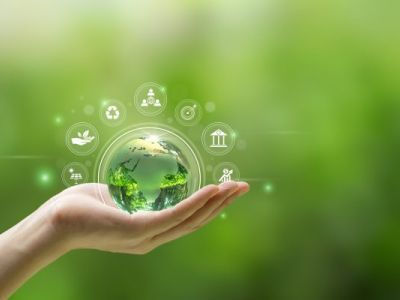
ESG: Health and Safety Obstacle or Opportunity?
Over the past few years, much has been written and discussed about the role of environmental, social and governance, commonly referred to as ESG. Investors and customers are increasingly applying these nonfinancial factors as part of their analysis process to identify material risks and growth opportunities in the companies they decide to invest in. According to research from the Weinreb Group, in publicly held U.S. companies, the position described as chief sustainability officer has grown from 29 such officers in 2011 to 183 in 2023 (see https://weinrebgroup.com/2023-cso-report-press-release/). These are roles that typically sit in the C-suite of a company and have direct strategic decision-making responsibilities.
Many health and safety…
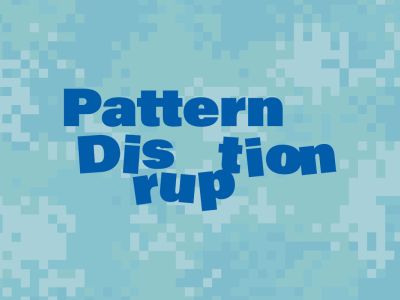
Pattern Disruption: Don’t Start with ‘Why’
In the northern latitudes, Mother Nature is deeply vested in a cycle of pattern disruption. The four seasons change the ecosystems and habitats. As the seasons shift in New York, the lake that I live on moves from a warm thermocline with colder layers on the bottom and warmer water on top to the opposite. In the coldest months, the top of the lake freezes entirely. The ground freezes, too, while the monarch butterflies leave and many of the birds fly south.
But even those pattern disruptions – the four seasons – become a rhythm, an expected ritual during which we trade lawnmowers for snowblowers and put away the outdoor furniture, only to reverse those actions when the weather becomes warm once again.
You may already know that the human br…
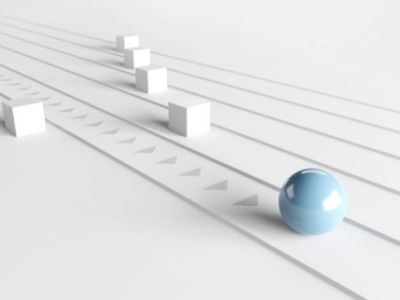
Nurturing Strong Leadership: An Approach to Professional Development in Skilled Trades
| Nathan Boutwell, M.Eng., CSP, SMS, CIT, CUSP, and Mike Starner, CUSP, CHST | Leadership Development
Strong leadership is essential for the success and well-being of a company. Effective leaders play a vital role in setting the course, motivating employees, fostering a positive work culture and making critical decisions that steer the organization toward its goals.
In our industry, leaders face significant challenges due to substantial growth, an aging workforce and concerns about the impact of both on operations. The need for professional development is a crucial item for workers in the skilled trades who will assume leadership roles. This development is necessary to help the next generation of leaders attain safe, reliable and fiscally sound operations.
Two Clear Opinions The best path to leadership in utility operations has been debate…
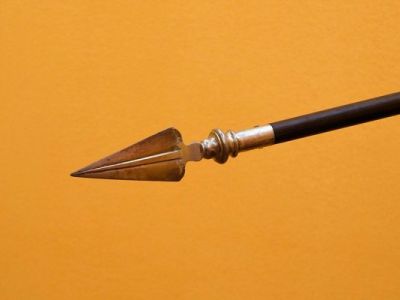
Tip of the Spear: A Tactical Approach to Safety Leadership
Leadership is defined as the action of leading a group or organization; it’s a verb. It’s also a skill that is extremely fluid. Leadership style can change depending on the person and the situation, but all effective leaders have some common qualities. When I developed the list below, I initially came up with 68 possible qualities, and while I know each of them has some merit, I eventually narrowed down the list to these 16 qualities that I believe are nonnegotiable.
1. Ability to effectively communicate 2. Ability to influence 3. Ability to inspire 4. Respect and trust (gives and earns) 5. Humility/no ego 6. Willingness to learn/continuous improvement 7. Master of delegation/empowers others 8. Honest/has integrity/is ethical 9. Flexible/a…
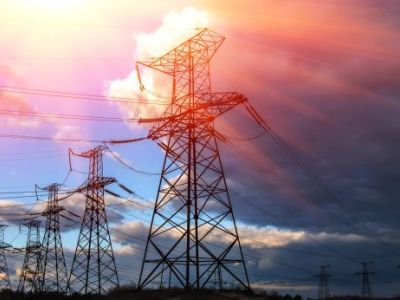
Overcoming the Illusion of Safety
There are striking similarities in how we respond to incidents, injuries and fatalities in our industry. Safety stand-downs are held. Utilities and contractors conduct incident investigations that are typically wrapped up with action items that need to be handled.
But consider this: Is everything we do in the wake of an incident truly effective in preventing future incidents? Let’s take it one step further. Are all the things we’re doing on a daily basis helping to ensure employee safety, or do we sometimes simply check a box, satisfy a requirement and tell ourselves we’re making the job safer for our workers?
My objective in writing this article is to take a hard look at some of the tactics we are currently using in the name of safety. I…
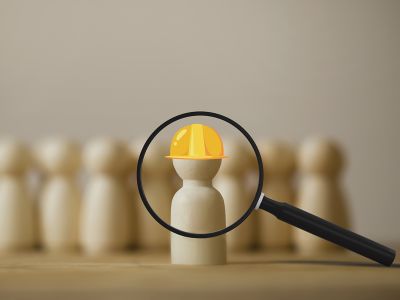
Gauges: How Do You Measure Safety?
The small utility had just lost two journeymen linemen to contractors, and they needed replacements who could hit the ground running. So, the company held some interviews and hired two seasoned journeymen.
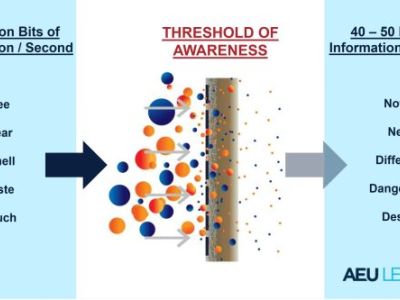
Beyond Behavior-Based Safety: Why Traditional Safety Practices are No Longer Enough
Traditional safety management practices are built on the assumption that human behavior is rational and occurs primarily through conscious decision-making. Nothing could be further from the truth. We are, in fact, irrational by nature, creatures of habit and deeply influenced by past experiences. To create the next step change in the practice of occupational safety, we must revisit existing paradigms defining it, revise them to better align with research emerging from advancements in neuroscience, and adapt to practice realigned strategies of an affective nature.
Irrational by Nature
In 2016, a municipality in western Virginia experienced a fatality when a maintenance worker entered a confined space containing lethal atmospheric conditions…
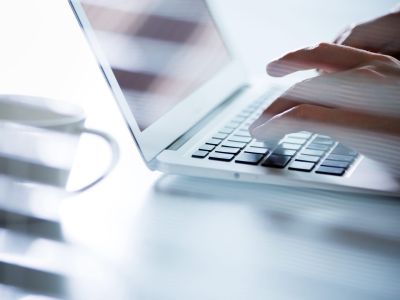
Using a Learning Management System to Augment Lineworker Training
“You can’t learn how to climb a pole by looking at a computer screen.”
That’s a sentence that has been repeatedly used in our industry to discredit web-based learning. And it’s true; in any skilled trade, neither distance learning nor classroom work alone can replace the skills and confidence gained from practicing tasks and building up muscle memory in the field. But does that mean there’s no place for distance learning? Absolutely not. When properly used to augment a field skills training program, online training can speed the development of skills, make your training program more efficient and keep your crews in the field longer.
Three Different Approaches
In 1984, educational psychologist Benjamin Bloom performed a study of three diff…
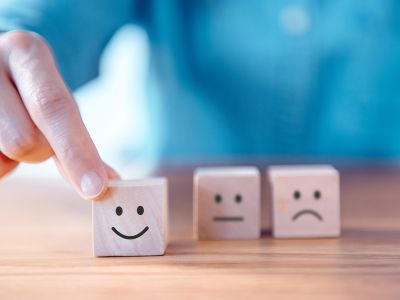
Does Positive Feedback Improve Safety?
Our client is an international utility company with more than 10,000 employees that provides electric and natural gas to 20 million U.S. customers. Their vision is to achieve a generative safety culture in which both employees and leaders are actively engaged. Characteristics of a generative safety culture include proactively resolving issues, focusing on leading indicators, and welcoming bad news as an opportunity for improvement, not for implementing discipline.
The company is well on their way to that destination, and it’s due in no small part to their employees’ dedication to their jobs, the training they’ve completed to excel in their work and their passion for wanting to create one of the best safety cultures in the utility industry.
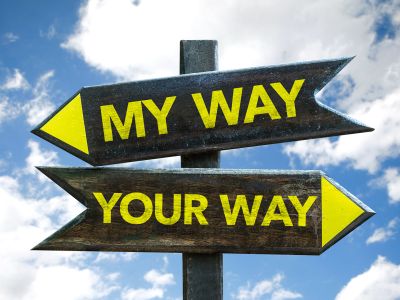
‘But I Don’t Wanna’: 6 Sources of Employee Resistance
“I forgot.” “I don’t want to.” “It’s not that serious.” “It won’t happen to me.”
If your employees are forgetting, ignoring, pushing back against or actively resisting the protections you’ve put in place to ensure their safety, then you know how frustrating it can be to get them to follow the rules.
Crafting a safety initiative so that you end up with employees who want to follow your safety procedures depends on addressing the driving causes of their resistance. Following are six sources of potential resistance and strategies you can use to help overcome each one.
They don’t know.
The source of resistance could be a simple knowledge problem (i.e., they don’t know what they need to do). If employees are new to the workforce, the industr…
From My Bookshelf to Yours: ‘The Success Principles’
During the research and writing process for my new book – “Frontline Leadership: The Hurdle,” published by Utility Business Media Inc. – I read a lot of books, and I want to share some highlights from a few of my favorites. This article will focus on “The Success Principles: How to Get from Where You Are to Where You Want to Be” by Jack Canfield. I hope you find this article useful, and I also hope it inspires you to read both “The Success Principles” and my book as part of your continuing personal and professional development.
To highlight how much I believe in this book and want to encourage you to read it, I completed the program to become a Canfield Certified Trainer in the Success Principles after reading it once and being exposed to…
From My Bookshelf to Yours: ‘Extreme Ownership’
What actions can you take to solve problems rather than blaming, complaining, defending and denying?
During the research and writing process for my new book – “Frontline Leadership: The Hurdle,” published by Utility Business Media Inc. – I read a lot of books, and I want to share some highlights from a few of my favorites. This article will focus on “Extreme Ownership: How U.S. Navy SEALs Lead and Win,” authored by Jocko Willink and Leif Babin. I hope that you find this article useful, and I also hope it inspires you to read both “Extreme Ownership” and my book as part of your continuing personal and professional development.
Overview Have you ever read a book and ended up with so many margin notes, highlights and sticky notes as placehold…
From My Bookshelf to Yours: ‘The 7 Habits of Highly Effective People’
Understanding, developing and applying these habits enable us to better respond to stimuli, making us more effective people.
I am excited to tell you that Utility Business Media Inc. recently published “Frontline Leadership: The Hurdle,” a book that I wrote. During the research and writing process, I read a lot of books and want to share some highlights from a few of my favorites. This article will focus on “The 7 Habits of Highly Effective People,” the bestselling book authored by Stephen R. Covey. I hope that you find the article useful, and I hope it inspires you to read both Covey’s book and my book as part of your continuing personal and professional development.
Overview Most people are familiar with the title “The 7 Habits of Highly…
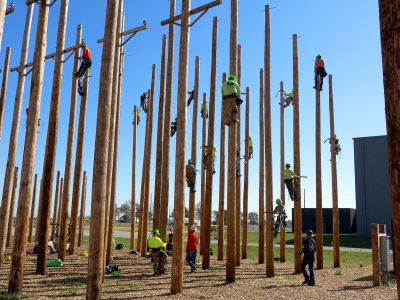
Just Like the Real Thing: Training the Next Generation of Lineworkers
The Missouri Valley JATC offers comprehensive training at its new state-of-the-art facility.
“Many people say that a lot of [lineworker] rules are written in blood, and there is literal truth to that. Safety is our value. We don’t have any competing priorities over safety. It’s not number one. It’s on a list of one.”
That’s a quote from Tim Vassios, a lead instructor at the Missouri Valley Joint Apprenticeship and Training Committee (JATC). Both Vassios and his organization – with the support of the International Brotherhood of Electrical Workers and the National Electrical Contractors Association – are working diligently to train the next generation of lineworkers in the Upper Midwest region of the United States.
Recently, Incident Preve…