
5 Core Components of a Well-Developed Storm Response Plan
Electric utilities are part of the backbone of modern society, providing essential power to homes, businesses, emergency services providers and more. But this critical service is vulnerable to extreme weather events that can cause massive disruptions, damage infrastructure and jeopardize public safety. Due to the frequency and severity of such events, it is more important than ever for electric power organizations to have a comprehensive storm response plan in place.
I’ve consistently been involved in storm response planning throughout my career, both as a lineman and a safety specialist. I’ve helped to restore power, oversee field operations and support logistics teams. In short, I’ve seen firsthand the necessity of a well-developed, effe…
Recording and Analyzing Job Briefings Can Save Lives
Planning saves lives. Whether you call it a job briefing or a tailboard, taking time before work begins to identify potential hazards, discuss elimination and mitigation strategies, and align the crew reduces the risk of incidents – and it’s an OSHA requirement per 29 CFR 1910.269(c). Studies consistently show that effective planning can prevent up to 70% of workplace accidents.
But not all job briefings are created equal. Research based on 850,000 recorded safety conversations has revealed that many of these conversations fall short of their potential. The average score of these recorded conversations is 18.8 out of 35, with key areas like planning (2.61/5) and question quality (1.88/5) leaving much to be desired.
The good news is that re…
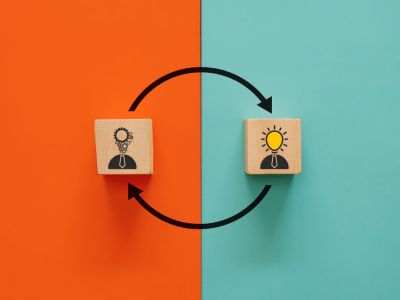
4 Strategies to Facilitate Effective Knowledge Transfer
Effectively transferring knowledge from tenured employees to new hires and those climbing the ranks is one of the most significant challenges utility organizations must reckon with. The workforce is continuously evolving, so it is essential to ensure that valuable insights and expertise are not lost when employees leave or retire. This Tailgate Topic explores four strategies that utilities and contractors can deploy to facilitate successful knowledge transfer among employees.
1. Design and Develop a Mentorship Program Mentorship has long been recognized as a powerful tool for knowledge sharing within organizations. Often used for short-service workers, employers can expand mentorship programs to include mid- and senior-level employees. Pai…
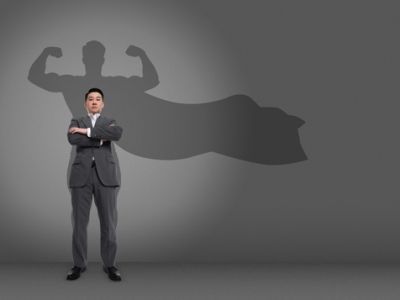
Rediscover Your Inner Superhero
Several years ago, a good friend of mine who worked in the utility industry drove his truck headlong into a tractor-trailer parked along a highway shoulder. In the blink of an eye, he was gone, leaving his wife a widow and their children without a father.
Fast-forward one year later. After conducting some training sessions with a utility company in Mississippi, a co-worker and I were driving home to South Carolina. My co-worker was asleep in the passenger seat, and everything was going smoothly as I navigated the truck and trailer east on I-20 under a clear, starry sky.
I had the radio turned off and my phone was far enough away that I couldn’t reach it. My focus was on the traffic, the terrain, and the possibility that I could encounter a…
Targeted Training: Reducing Stress-Related Cognitive Load in Lineworkers
Lineworkers are accustomed to hearing that they must completely focus on the task they’re performing. For safety reasons, staying fully present and mentally focused on the work at hand is critical in the high-stakes, hazardous environments these employees often find themselves in.
Maintaining full focus for an extended length of time is the goal to strive for – but realistically, that doesn’t align with how the human brain works. An individual can be easily distracted, especially when experiencing personal or professional difficulties. Distractions impair a person’s ability to perform at their highest potential, as numerous studies have demonstrated.
In particular, a person’s financial health and the health of their relationships are two c…
The Dangers of Distraction: Staying Focused in a High-Risk Environment
Working in a high-voltage environment means working in a high-risk environment. Doing so demands technical expertise, attention to detail and unwavering focus. When your mind wanders in such an environment – even for a split second – the consequences can be catastrophic.
Understanding the High-Risk Environment Whether it’s in a power generation plant, a substation, or a transmission or distribution setting, a high-voltage environment is inherently hazardous. Workers are routinely exposed to electrical potential that can cause severe electric shocks, arc flashes and burns. Equipment maintenance, troubleshooting, testing and repairs are tasks that require meticulous attention to detail and strict adherence to safety protocols.
The hazards of…
Shaking Off the Holiday Hangover
The holiday season is a wonderful time to spend with family and friends and to reflect on our gratitude for all the blessings we have. The joy and love we share during this magical season often graces us with memories we’ll cherish for years to come.
But once the holidays are over and Monday rolls around again, it’s time to get back to work. How do you come down from your emotional high and begin to refocus on your work responsibilities?
It’s all about dialing in.
Each of us has an internal switch that we must flip to help ensure we stick around to make more beautiful memories with our loved ones. When we actively, consciously shift our mindset from holiday mode to work mode, we adjust our focus. A significant portion of maintaining that f…
Lightning Safety in Outdoor Work Environments
Outdoor workers across various industries face numerous hazards on the job site. One sometimes overlooked yet potentially deadly threat is lightning. A leading cause of weather-related deaths in the United States, lightning strikes pose a significant risk to workers, surroundings and equipment. According to OSHA, in the U.S., over 300 people are struck by lightning every year, often causing victims injury, disability and even death. Understanding the dangers of lightning and implementing proper safety protocols, including the use of advanced detection technology, is critical for reducing risk and ensuring a safe working environment.
Dangers to Outdoor Workers Lightning is a powerful force of nature; a single bolt can contain up to 1 billi…

Mental Rehearsals: Responding to Heat Emergencies
While temperatures have begun to cool across the country, heat emergencies can still occur. And because heat is the leading cause of death among all hazardous weather conditions in the U.S., OSHA recently published its Notice of Proposed Rulemaking for Heat Injury and Illness Prevention in Outdoor and Indoor Work Settings (see more at www.osha.gov/heat-exposure/rulemaking). Would you know what to do if one of your co-workers collapsed on the job due to heat-related illness?
Let’s say you are working in the right-of-way. It’s a simple pole transfer, but it’s being done out of the hooks. The temperature is already over 90 degrees Fahrenheit and expected to climb close to 100. There are four of you: you and Joe, the climbers, and two other me…
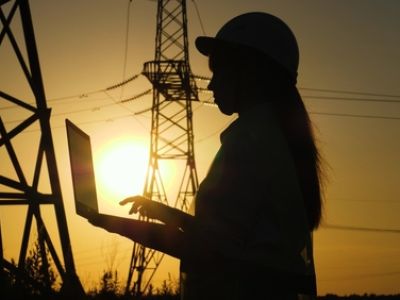
Proactive Risk Reduction: The Key to Sustainable Success
In an increasingly complex and volatile business landscape, the ability to proactively identify, assess and mitigate risks is not merely a valuable skill – it’s a strategic imperative for sustainable success. As leaders, entrepreneurs and innovators, our capacity to anticipate and navigate risks can be the difference between stagnation and growth and between surviving and thriving in a rapidly evolving world.
Risk management is not a one-time task but a continuous process that requires vigilance, adaptability and foresight. By cultivating a proactive approach to risk reduction, we can enhance our resilience, protect our assets, and seize opportunities for innovation and growth. Now, in this exploration of the principles of proactive risk r…
The Evolution of Tree-Trimming Safety Practices
In 2013, tree trimming was a different game.
We worked hard, but safety protocols were often viewed as an inconvenience rather than a necessity. I guess you could say it was a bit like the Wild West – we did what we needed to do to get the job done. Most days, there wasn’t anyone to come out to observe us working, so the only days we really made sure we did our work by the book were the days when someone from the office visited our site. Training wasn’t part of our everyday tasks because the work was primarily done on a production basis – and no one wanted to stop production. They wanted to get the job done. We didn’t delve into human performance either, and we didn’t talk about tools or traps or how to identify them.
Like many others I kn…
The Best Practice
I am not a person who puts much stock in luck. I believe that in our line of business, it takes the correct tools to do a job correctly – especially since I’ve been the victim of a 4-inch lag to the forehead while trying to use a bell wrench as a hammer. I also believe that how you use those tools is equally important. And finally, I believe that there are times when we need a little help from documents called “best practices.”
What exactly is a best practice? It is a set of guidelines, ethics or ideas that represent the most efficient or prudent course of action in a given situation. Essentially, it’s documentation of a procedure that is the most effective in performing a task safely. Best practices may be established by authorities, or t…
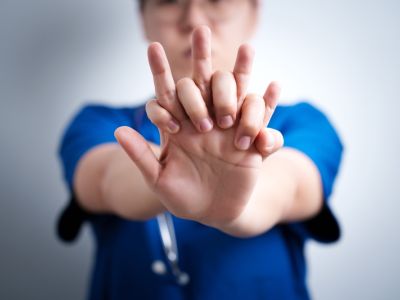
Saving Lives with Quality CPR
With the best of intentions, our industry has not been able to change the persistent statistics of serious injuries and fatalities over the past decade. Even the most brilliant ideas seem to be unable to be translated into a change in work. So, while we continue trying to determine how to slow our serious injury and death rates, we should also gain a better understanding of how to prepare for and respond to serious events when they inevitably occur within our circle of co-workers, family and friends.
In addition to being a lineman, I also have experience as a flight paramedic/nurse, plus wilderness medical training. My experience suggests that we should always be ready to respond to a serious event when it happens. For instance, if you’re…
Expand Pre-Job Briefings to Include Your Hydro-Excavator Partners
Editor’s Note: This month’s Tailgate Topic has timely advice to ensure crews working with unknown subcontractors are kept safe. Remember that OSHA requires those subcontractors to be qualified for the assigned task and that their employer is responsible for their safety. Having subcontractors observe and participate in a line crew’s tailboard is a good way to help them ensure safety without directly supervising their work practices.
Most state’s dig laws restrict the use of mechanized equipment within specified tolerance zones of buried utilities. Because of these laws, hydro-excavation trucks working in conjunction with electric line crews are now more prevalent throughout the industry.
Hydro excavation removes soil with pressurized water…
Do You Really Care?
As EHS professionals, we may scoff at first when a worker asks us, “Seriously, do you really care about what I’m doing?” But this question has a much deeper meaning than you may think.
In our day-to-day activities, much of the relationship building and many of the general discussions fall to skill-of-the-craft concepts. This means there is tremendous variability between individuals regarding how they approach and connect with people at a personal level. Many companies have abandoned engagement-based or team-based training due to budget restraints or a perceived lack of value, so there isn’t a consistent approach or even a dedicated effort to having engagement in the field. For many EHS professionals, unfortunately there is just not enough…
Fighting PPE Complacency
In the fast-paced world of utility work, it’s easy to fall into the trap of thinking, “This is just a quick job” or “I’ve done this a thousand times.” These thoughts can lead to complacency and poor decision-making around proper personal protective equipment use, including flame-resistant and arc-rated apparel. In this month’s Tailgate Topic, we’ll explore how to combat such complacency.
Many utility job tasks carry inherent risks, whether it’s working near live electrical equipment or navigating challenging terrain. Regular training sessions serve as invaluable opportunities to reinforce safety protocols. These sessions should cover the correct use of PPE as well as delve into the rationale behind the need for it.
Additionally, familiariz…
Am I My Brother’s Keeper – Or Not?
I am sure that the safety leaders reading this Tailgate Topic have heard some or all of the following phases: “I’m my brother’s keeper,” “Don’t get hurt,” “Work in a manner that prevents injury,” and “Keep your head in the game.” These phrases are well-intended; they serve as a reminder to keep safety top of mind. But using them will not prevent incidents.
I recently reviewed an incident that resulted in an injury for a client. That client has a very good safety program and culture. The incident report included feedback from co-workers of the injured party (we’ll call him “John”), who said things like, “I knew John was going to get hurt one of these days” and “I was too busy doing my own work; it’s not my fault John got hurt.”
All of us me…
Incidents Require an Immediate Response
Incidents on job sites can cause pain and mental anguish, disrupt project timelines, escalate costs and have lasting repercussions on an employer’s safety performance record. When an incident occurs, company management and safety professionals must respond in a timely manner.
Typically, the first responsive action is obtaining detailed information about the incident as quickly as possible. Ask about any injuries that may have occurred and their severity, as well as whether the injured party is still on the scene or has been transported to a medical facility. Find out if emergency responders and law enforcement have been notified if they aren’t already present at the scene. The health and safety of an employer’s human assets should be the f…
Cleaning Up the Ointment
Earlier this year I wrote a Tailgate Topic titled “The Fly in the Ointment” (see https://incident- prevention.com/blog/the-fly-in-the-ointment) – but I probably should have written this Tailgate first.
Why?
Because sometimes, the fly becomes a problem because of the ointment. By that I mean a work environment can become toxic due to one or more of the people managing it. Like many of you who have had the same experience, I have worked for people whose management skills were so poor that it negatively impacted my performance and the performance of others on my team. In fact, one of the greatest gigs of my life was destroyed in large part by one such manager.
Have you seen the image that shows the difference between a boss and a leader? In i…
Mitigating Predictive Processing Errors
Andy Clark’s book “The Experience Machine: How Our Minds Predict and Shape Reality” was just published in May. The science he discusses in the book is not new, but the methods used to understand our brain are relatively new. This begs the question: Are we basing our safety training on an older model of the human brain?
That older model is an orderly cause-and-effect/stimulus-and-response system. Essentially, if we train to respond appropriately to stimuli, we think we are all set. We imagine our brain patiently awaiting stimuli and sensory information so it can send out the appropriate responses. Much of the older model was derived from brain autopsies. But as Tan Le states in her book “The NeuroGeneration,” “Dead brains don’t talk.”
The R…