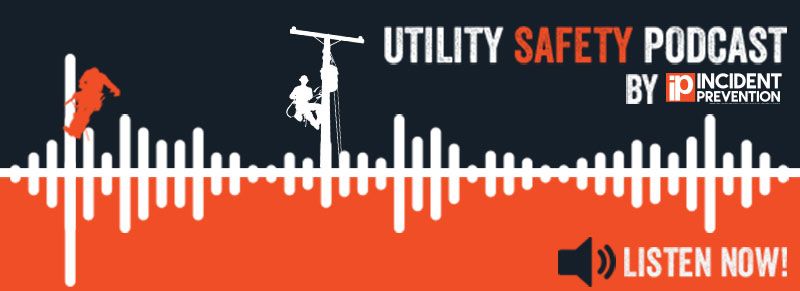
Incident Prevention Utility Safety Podcast
The place utility safety and operations professionals go to learn how to empower themselves and others in their organization on how to become even better safety professionals.
PODCASTS BY INTERVIEWER
Utility Safety Podcasts
Mistakes Are Inevitable: Choose to Invest in Recovery Capacity
When past winters were settling in, my family always took comfort with homemade cocoa. Last winter, one instance of preparing the hot beverage turned into a lesson about the nature of mistakes and the importance of planning for them. As my children worked together in the kitchen, one of my older daughters inadvertently spilled cocoa on one of her favorite sweaters. I stepped in, ready to help, and decided to soak the stained sweater in our utility sink as part of the cleaning process.
Filling the sink took longer than anticipated, so I left the room to tend to another task – and briefly lost track of time. Suddenly remembering the soaking sweater, I rushed into the laundry room and discovered that the sink had overflowed. Thankfully, only a quick cleanup was required. Better yet, the incident provided a valuable reminder about recovery capacity, or the ability to effectively respond to human error and unforeseen events.
Learning From Our Mistakes
In the aftermath of the laundry room mishap, I found myself considering the overflow hole, a small yet crucial design element common to many bathroom sinks. It serves as a safeguard, ensuring water has an escape route if an overfill occurs. This prompted a question: If bathroom sink overflows can be prevented by a simple precautionary feature, what precautionary features or systems have utility organizations implemented to handle mistakes and unforeseen events – and are they the right ones?
Errors are inevitable in any environment. The key to facilitating recovery is ensuring systems are in place that enable quick responses and minimize consequences when things go awry. Organizations should consider these four areas when planning for mistakes:
- Preventive measures. It is prudent to identify and address errors before they escalate. These activities could involve process audits, training and/or real-time monitoring systems.
- Rapid recovery protocols. Organizations should develop recovery plans (e.g., clear communication strategies, designated roles for crisis management) to help them bounce back swiftly after mistakes occur.
- Feedback loops. Creating a culture that promotes learning from errors can result in process improvements that prevent recurrences.
- Flexibility and adaptability. Systems should be designed with a focus on preventing mistakes while also remaining adaptable, enabling teams to respond effectively in unexpected situations.
Theory Into Practice
Errors can have significant implications in the utility sector, which means electric power organizations must have adequate recovery capacity to remain viable. Following are five real-world examples that demonstrate this capacity and reinforce key concepts discussed above.
1. San Diego Gas & Electric wildfire preparedness. In response to increased wildfire threats, SDG&E implemented rigorous protocols to minimize risks associated with its electrical infrastructure. The utility established a comprehensive wildfire mitigation plan that included enhanced vegetation management and power shutoff strategies during high-risk weather events.
Lessons reinforced: This is one example of implementing preventive measures to avoid catastrophic consequences. SDG&E also emphasized rapid recovery protocols – such as communication with customers – to address potential outages and safety concerns, showcasing effective recovery capacity.
2. Pacific Gas & Electric pipeline explosion response. The 2010 San Bruno pipeline explosion in California resulted in significant loss of life and property. In its aftermath, PG&E experienced intense scrutiny regarding its safety protocols and operational procedures. The company committed to substantial infrastructure improvements, implementing rigorous pipeline testing and monitoring while enhancing its emergency response capabilities.
Lessons reinforced: This case highlights the importance of learning from mistakes. PG&E’s response fostered an organizational culture centered on safety and accountability, helping to ensure that systems would be established for rapid recovery following unforeseen incidents.
3. Duke Energy outage management system enhancements. Facing challenges with customer communication during extensive weather-related outages, Duke invested in an enhanced outage management system that integrates real-time data. This has enabled improved tracking of outage conditions and faster response team deployment.
Lessons reinforced: This example emphasizes the significance of rapid recovery protocols, including effective communication strategies, to ensure that customers are promptly informed and impacts are minimized when outages occur.
4. Florida Power & Light storm readiness. FPL has made significant strides in preparing for hurricanes and other severe storms by reinforcing its infrastructure and implementing community education programs on storm preparedness. The company conducts drills, uses advanced technology to monitor weather patterns, and maintains clear lines of communication with customers about safety and power restoration efforts.
Lessons reinforced: FPL’s proactive measures help reduce the impact of storms in its service territory. By planning ahead and establishing clear recovery procedures, utilities can better minimize risks and strengthen their overall resilience.
5. Reliant Energy customer service improvements. Following a major blackout in 2008, Reliant faced customer backlash due to poor communication and slow response times. The company seized this opportunity to enhance its crisis management and customer service systems, introducing improved staff training, implementing new technologies to provide timely updates to customers, and developing a more robust feedback mechanism for understanding customer needs during outages.
Lessons reinforced: Reliant’s experience highlights the importance of establishing feedback loops and fostering an organizational culture that embraces learning from mistakes. By recognizing past errors and implementing necessary adjustments, the company improved its recovery capacity and customer satisfaction.
Conclusion
As we navigate our lives – filled with risks at work, at home and in between – let us embrace the lessons learned from both our everyday experiences and industry practices. Mistakes are a natural part of any process, so we should focus on developing the systems needed to effectively manage setbacks. By fostering a culture of learning, implementing preventive measures and establishing clear communication protocols, utility organizations can transform potential pitfalls into growth opportunities.
About the Author: Shawn M. Galloway is CEO of ProAct Safety (https://proactsafety.com) and an author of several bestselling books. As an award-winning consultant, trusted adviser, expert witness, leadership coach and keynote speaker, he has helped hundreds of organizations within every primary industry improve safety systems, strategy, culture, leadership and engagement. Galloway also hosts the highly acclaimed weekly podcast series “Safety Culture Excellence.”
Rethinking Risk: Safety Culture, Risk Tolerance, and Relationship-Driven Leadership – Mark Taylor, CUSP
In this compelling episode, Mark Taylor, CUSP, Senior Advisor of Corporate Services at Primary Engineering and Construction, joins us to explore how utility professionals perceive and manage risk. Drawing from decades of field and leadership experience, Mark discusses how a worker’s risk tolerance evolves over time, the importance of coaching over compliance, and how building trust and relationships within teams fosters a stronger safety culture.
We also discuss the generational shift in safety attitudes, how to encourage real “stop work” authority, and the power of employee buy-in—whether it’s safety glasses or safety protocols.
Whether you’re a safety leader, a utility worker, or a manager seeking to improve culture and communication, this episode is packed with practical wisdom and stories that resonate.
Don’t miss Mark’s insights, leadership tips, and a sneak peek into the upcoming IUOTA conference in San Diego.
Check out the IUOTA Conference – https://www.iuota.com/
Key Takeaways:
-
Risk tolerance increases with experience—but so can complacency.
-
Relationship-building is key to enabling true stop-work authority and a proactive safety culture.
-
Coaching yields better long-term safety outcomes than compliance enforcement.
-
Younger workers tend to question safety practices more—and that’s a good thing.
-
When employees are heard and supported, buy-in follows naturally.
-
Explaining the “why” behind safety rules is critical to adoption.
-
Culture shifts start with caring—genuinely—about your team.
-
Small gestures (like supporting preferred PPE purchases) can lead to major cultural wins.
Questions and Answers:
Q1: What is risk tolerance in the context of utility safety?
A1: Risk tolerance is a worker’s willingness to accept safety risks, often influenced by experience, previous outcomes, and personal comfort. Over time, routine exposure without consequences can raise that tolerance to unsafe levels.
Q2: How can leaders help reduce unsafe risk tolerance?
A2: By fostering open communication, encouraging curiosity, and modeling behavior that prioritizes elimination over mitigation. Leaders should promote a culture where anyone feels empowered to speak up.
Q3: What role does relationship-building play in safety?
A3: Strong relationships between leadership and field teams build trust. When workers feel respected and heard, they’re more likely to participate in safety discussions, report hazards, and accept coaching.
Q4: How can companies shift from compliance-driven to value-driven safety cultures?
A4: Start by caring deeply about workers, offering flexibility where possible (e.g., PPE preferences), involving teams in decisions, and always explaining the reasoning behind policies.
You can read the current magazine at Incident Prevention Magazine.
Subscribe to Incident Prevention Magazine – https://incident-prevention.com/subscribe-now/
Register for the iP Utility Safety Conference & Expo – https://utilitysafetyconference.com/
#UtilitySafety #RiskTolerance #SafetyCulture #StopWorkAuthority #SafetyLeadership #FieldSafety #UtilityWorkers #IncidentPrevention
50-Foot Hot Stick
Hastings Fiber Glass Products has released a new HV-250 Tel-O-Pole II, a 5-foot-longer version of its popular HV series of telescopic hot sticks. This product addition is a direct response to lineworkers worldwide who expressed a need for increased reach in various utility applications.
The HV-250 maintains the same trusted quality, durability and safety features users have come to expect from Hastings’ products, now with the added benefit of extended length. This enables lineworkers to safely perform tasks in situations where other hot sticks’ reach is limited, enhancing on-the-job efficiency and safety.
Hastings’ unique approach to creating a 50-foot version of its HV series allows the base to retain the same dimensions as the HV-245, making it easy for users to safely and effectively extend the sections of the stick to the full 50-foot length. www.hfgp.com
Leather Protector Gloves
Saf-T-Gard recently announced the availability of the new Saf-T-Gard Voltgard Dura-Fit Leather Protector Gloves. Utilizing a novel, modified pattern to better fit the curve of all industry-standard rubber insulating gloves for long-lasting wear and safety, this new offering takes leather protector gloves to the next level.
Designed for use with Class 1, 2, 3 or 4 high-voltage rubber insulating gloves, the Saf-T-Gard Voltgard Dura-Fit Leather Protector Gloves are made using a tough, premium-grain cowhide leather and packed with a wide range of enhanced safety features. These include a durable, split-leather gauntlet cuff to extend protection past the wrist; an innovative action thumb design with an enlarged reinforcement to provide additional protection to critical wear areas; an adjustable Kevlar strap and flame-resistant buckle to comfortably and safely secure the gloves to the worker’s hands; and high-strength nylon-thread stitching for added comfort and protection. The gloves are also water-repellent. www.saftgard.com
BuckSqueeze Lite
Buckingham has reimagined fall protection with the new BuckSqueeze Lite, its lightest and most efficient wood-pole fall-restriction device to date. Weighing just 3.5 pounds, this innovation offers the trusted security of the original BuckSqueeze, now with advanced features designed for performance, comfort and ease of use.
The BuckSqueeze Lite features a slotted nose D-ring that interlocks with the rotosnap, forming a rigid connection that streamlines climbing and transitioning. An ergonomic handle provides maximum control, while the aluminum WebGrab with extended eye cam ensures smooth strap movement without binding.
The exclusive Treblekern Tough Rope inner strap offers superior durability with a built-in red wear indicator. The BuckHorn adjustment lever enables effortless strap adjustment without unloading. Aluminum carabiners ensure secure, easy connections.
Ideal for lineworkers seeking a lighter, more responsive device, the BuckSqueeze Lite is also fully modular, allowing field replacement of worn parts. https://buckinghammfg.com/products/bucksqueeze-lite-486dk4ma/
Type II + Safety Helmet
Twiceme Technology recently announced that Bullard will embed Twiceme’s smart safety technology in select models of its new Type II + safety helmets.
Twiceme-enabled Bullard helmets will empower safety managers to significantly improve operational efficiency while elevating safety protocols. Using Twiceme’s Safety Management Portal, organizations can streamline daily safety management procedures, manage inventory and inspections, maintain comprehensive worker documentation, and reduce incident response times, all while providing users with advanced protection from Bullard’s trusted helmet designs. www.bullard.com, www.twiceme.com
Simulation-Based Training Solutions
CM Labs Simulations – the leading vendor of simulation-based training solutions in the utilities, construction and ports industries – will showcase Intellia, its intelligent training system, October 7-9 at The Utility Expo in Louisville, Kentucky.
The company will also debut all-new Intellia equipment training packs, which are designed to help organizations build safer, more skilled crews with simulation training that mirrors real-world challenges. In addition, CM Labs will offer live, hands-on demonstrations of new changes coming to its walkaround inspection training. www.cm-labs.com
Built from the Underground Up – Mark Savage’s Mission to Train the Next Generation of Utility Workers
In this episode of Incident Prevention’s Utility Safety Podcast, host Kate Wade sits down with Mark Savage, Marine Corps veteran and founder of DeadBreak — a specialized underground electrical training and consulting company. Mark shares his professional journey, the gaps he identified in underground utility training, and how DeadBreak aims to bridge those gaps by offering curriculum development, hands-on training, consulting, and more. From the importance of replacing tribal knowledge with formal instruction to creating future pathways for veterans and apprentices, Mark’s passion for safety and legacy shines throughout. Whether you’re in the field, hiring apprentices, or overseeing training programs, this episode is a must-listen.
Key Takeaways:
-
Underground utility training lacks standardization — and DeadBreak is working to change that.
-
Mark Savage’s military background influenced his drive for structure, clarity, and service in training.
-
DeadBreak offers custom curriculum, onsite training, manhole rescue, and consulting.
-
Veterans are an untapped, ideal workforce for underground utility work.
-
Tribal knowledge and implied instructions can pose serious safety risks.
-
Proper training isn’t just about compliance — it’s about saving lives.
Three Questions & Answers for Listeners:
Q1: Why is underground utility work often overlooked in formal training?
A: Unlike overhead systems, underground systems vary widely by region and have traditionally relied on tribal knowledge, leading to inconsistent or nonexistent training standards.
Q2: What is DeadBreak’s mission?
A: DeadBreak aims to fill the training gap in underground electrical work by offering tailored curriculum, in-person instruction, safety-based onboarding, and mobile splicing teams.
Q3: How can employers improve underground job safety right now?
A: By investing in standardized training, eliminating implied knowledge, and ensuring tools and procedures are clearly understood and taught by qualified professionals.
Get ahold of Mark Savage:
You can read the current magazine at Incident Prevention Magazine.
Subscribe to Incident Prevention Magazine – https://incident-prevention.com/subscribe-now/
Register for the iP Utility Safety Conference & Expo – https://utilitysafetyconference.com/
#UndergroundUtilities #UtilitySafety #ElectricalTraining #VeteranWorkforce #DeadBreak #CableSplicing #InfrastructureTraining #UtilityWorkforceDevelopment #WorkplaceSafety #SkilledTradesEducation
Voice of Experience: Battling the Storm – Hurricane Season Lessons for Linemen with Danny Raines, CUSP
In this powerful episode of the Utility Safety Podcast: Voice of Experience, veteran lineman and safety consultant Danny Raines, CUSP, shares hard-earned lessons from decades of storm response—from Hurricane Katrina to ice storms in Georgia. With hurricane season in full swing, Danny offers real-world guidance on preparing for storm duty, understanding system hazards, and staying mentally and physically resilient in the face of chaos. Whether you’re a new lineworker heading out on your first storm or a seasoned pro, this episode delivers critical insights to keep you safe, sharp, and storm-ready.
Key Takeaways:
-
Preparation is Everything: Danny emphasizes the importance of personal checklists, including meds, hygiene, and weather-appropriate gear.
-
Test and Verify: Don’t assume equipment is de-energized—especially with the increase in generators, solar, and battery backups.
-
Mental & Physical Fatigue is Real: After 14–18 days, exhaustion sets in, increasing the chance of errors. Know your limits.
-
Find a Mentor: For new linemen, a trusted mentor can be a lifeline during complex storm work.
-
Storm Hazards Go Beyond Electricity: Environmental dangers like snakes, alligators, and aggressive customers add to the challenge.
3 Questions & Answers:
Q1: What’s one of the most overlooked parts of storm prep?
A: Personal medications. Many new crew members forget that pharmacies may be closed or destroyed post-storm, making it impossible to refill critical prescriptions.
Q2: Why is it so important to “test and verify”?
A: With so many modern power sources—from Honda generators to solar panels and battery storage—assumptions can be fatal. Always check for voltage, even on lines you think are isolated.
Q3: How long can a lineworker realistically stay sharp on storm duty?
A: According to Danny, the magic number is around 14–18 days. After that, physical fatigue and mental exhaustion dramatically increase the risk of mistakes and injuries.
You can read the current magazine at Incident Prevention Magazine.
Subscribe to Incident Prevention Magazine – https://incident-prevention.com/subscribe-now/
Register for the iP Utility Safety Conference & Expo – https://utilitysafetyconference.com/
The Voice of Experience with Danny Raines podcast is produced by the same team that publishes Incident Prevention. It delivers insights based on Danny’s regular column in the magazine, also called the Voice of Experience. To listen to more episodes of this podcast, as well as other podcasts we produce, visit https://incident-prevention.com/podcasts. You can reach Danny at rainesafety@gmail.com
Purchase Danny’s Book on Amazon – https://a.co/d/556LDvzc
#UtilitySafety #StormResponse #LinemanLife #HurricanePrep #ElectricalSafety #DannyRaines #CUSP #Lineworkers #StormWork
Bringing Electrical Safety Home – A Conversation with Jennifer LeFevre of Electrical Safety Foundation International
In this episode of the Incident Prevention Utility Safety Podcast, host Kate Wade sits down with Jennifer LeFevre, Executive Director of the Electrical Safety Foundation International (ESFI), to explore how everyday decisions at work and at home can impact electrical safety. Jennifer shares insights into the mission of ESFI, the dangers of lithium-ion batteries, how utilities can access free safety resources, and why public education is critical to preventing electrical fires, injuries, and fatalities. Whether you’re a utility safety professional or simply want to protect your family, this episode is full of actionable advice that could save a life.
Key Takeaways:
-
Electrical safety starts at home—complacency off the job can be just as dangerous as on it.
-
Lithium-ion batteries require proper handling, charging, and disposal to prevent fires.
-
ESFI offers free infographics and video shorts utilities can use to educate customers.
-
Public education is prevention—sharing small safety habits can make a big impact.
-
After disasters, generators and downed lines present serious electrical hazards that people often overlook.
Q&As summary:
Q1: Why should utility professionals care about electrical safety in the home?
A: Utility workers are trained to prioritize safety on the job, but Jennifer LeFevre reminds us that hazards exist at home too. Everyday items—like extension cords, electric blankets, or ladders near power lines—can cause serious incidents if not used safely. Translating workplace safety habits into the home can protect your loved ones.
Q2: What resources does ESFI offer to support electrical safety outreach?
A: ESFI provides free downloadable resources including infographics, short-form educational videos, and seasonal safety newsletters. These are designed for easy integration into utility newsletters, community outreach, and employee training programs.
Get in touch with Jennifer – Jennifer.LeFevre@esfi.org
Subscribe to Incident Prevention Magazine – https://incident-prevention.com/subscribe-now/
Register for the iP Utility Safety Conference & Expo – https://utilitysafetyconference.com/
#ElectricalSafety #UtilitySafety #SafetyEducation #LithiumIonBatterySafety #HomeAndWorkSafety #InjuryPrevention #ESFI #iP
Advancing Safety Through Total Well-Being: Practical Tips and Ideas for Utility Leaders
Over the past 50 years, the electric utility industry has developed and implemented robust engineering controls, detailed work procedures and focused training to reduce injury and fatality rates among workers. However, the total well-being of the worker is another critical safety factor that utility organizations often don’t address.
Well-being encompasses physical health as well as mental, emotional and social dimensions that can significantly influence an individual’s capacity to make sound decisions, maintain situational awareness and successfully mitigate risks. Workers bring their whole selves to the job, which includes their stress, fatigue and other personal challenges. We leave serious gaps in our safety systems when we fail to account for these human factors.
The previous article I wrote for Incident Prevention provided an overview of total well-being and its impact on the workplace (see https://incident-prevention.com/blog/making-the-safety-connection-the-impact-of-total-well-being-in-the-workplace/). This follow-up article offers practical tips, ideas and other information to help leaders integrate well-being into their organizational safety culture. When workers are holistically supported, they are better protected from harm, more engaged and productive, and more likely to thrive. It is time for our industry to move beyond the traditional definition of safety by recognizing total well-being as a core component of risk management.
Start with the person.
Most safety systems are built around physical safeguards, policies, procedures and personal protective equipment. Workers are trained to adapt to these systems. But even the most advanced tools and well-written procedures can fail if the worker employing them is fatigued, stressed or distracted.
Organizational leaders must recognize the human at the center of the safety system and understand that risk increases when workers feel mentally, emotionally or otherwise unbalanced. Strive to foster an environment in which workers (1) understand the connection between their well-being and their ability to work safely and (2) feel safe to speak up when they are struggling.
Tip: Well-being should be viewed as a responsibility shared among workers and leadership, not an individual burden.
Idea: Introduce workers to anonymous self-assessment tools that prompt them to consider questions such as, “Did I sleep enough last night?” or “Am I feeling mentally focused today?” When integrated into daily routines, these and other simple reflection exercises can spur important conversations and proactive safety decisions.
Conduct well-being check-ins during job briefings.
Every job must begin with a safety briefing, which is an ideal time to address not just physical risks but overall human readiness. In organizations with strong safety systems, leaders inquire about the physical, emotional and mental wellness of employees, especially in high-risk or repetitive work environments. For example, a job briefing form could include a prompt such as, “Have you had enough rest to do this task safely?” or “Are there any personal distractions you need support with today?”
Tip: Begin job briefings with a short mindfulness practice. A two-minute breathing or focus exercise can reduce anxiety, improve awareness and reset attention before work begins.
Idea: Launch “Mindful Minutes” during morning meetings. Invite workers to collectively pause and assess their stress levels and mental clarity. This reinforces psychological readiness as a part of doing the job well.
Treat well-being as a core part of safety programs.
Traditional safety programs often focus on external threats like machinery, voltages and confined spaces while downplaying internal threats such as sleep issues, unmanaged stress and poor nutrition. But expanding safety training to include human factors is necessary, not just progressive. Consider the way hydration is discussed on a hot summer day. Most workers understand that they must drink water to rehydrate themselves when they are sweating. But do they fully understand why hydration is so important in terms of their job performance?
Tip: Don’t stop at “Drink water on hot days.” Teach employees how dehydration affects muscle performance, cognitive function and emotional regulation.
Idea: Set up a hydration station stocked with low-sugar, high-electrolyte beverage options. Include a visual handout explaining how energy drinks and dehydration can impact concentration and reaction time on the job.
Provide accessible resources for total well-being.
Numerous companies offer well-being resources (e.g., employee assistance programs, apps, health benefits), but they can be misunderstood and underutilized.
Tip: Regularly talk to workers about well-being in the context of safety. Ensure they are aware of the support available to them and how to access it. Post employee assistance program information in break rooms, locker rooms and job trailers.
Idea: Post clear signage on vending machines and in cafeterias that identifies healthy food and drink options. Highlight how good nutrition affects energy levels, alertness and injury prevention.
Foster a culture of psychological safety.
One hallmark of a high-reliability organization is a working environment in which employees feel safe to speak up about risks, mistakes and their own well-being. Creating this environment begins with leadership.
Tip: Normalize conversations about stress, fatigue and emotional well-being. Train frontline leaders to recognize invisible hazards, such as mood changes, burnout and disengagement. Provide clear referral pathways for mental health and peer support resources.
Idea: Host “State of Mind” check-ins during weekly staff meetings. In five to seven minutes, a leader can share a personal well-being insight or challenge, then invite brief team reflections. These short exchanges help to build trust, reduce stigma and create a psychologically safe environment.
Tailor efforts to a multigenerational workforce.
Organizational well-being programs should resonate across all age groups, career stages and cultural backgrounds. What motivates a 25-year-old new-hire may differ from what motivates a 55-year-old lineman with three decades of experience. For example, younger employees often seek support for mental health, physical fitness and lifestyle balance. Older employees may prioritize joint health, mobility and chronic disease management.
Tip: Avoid one-size-fits-all programs. Offer flexible options, from digital wellness challenges to ergonomic assessments and tailored support groups.
Idea: Launch inclusive movement challenges that track daily steps or minutes of physical activity, measured by engagement, not weight loss. This keeps the focus on health rather than appearance or age.
Conclusion
As utility industry tools and technologies continue to evolve, we must not leave behind the people who keep the systems running. Workers are not just operators of equipment or followers of procedures. They are human beings navigating real lives, complete with personal challenges, stress and fluctuating energy levels. When company leaders understand this and embrace whole-person wellness as part of their safety strategy, they move beyond compliance into the realm of cultural transformation. The return on this investment isn’t just fewer incidents. The workforce becomes healthier and more focused, resilient, productive and committed.
Let’s stop expecting workers to leave their personal lives at the gate. That is an unrealistic expectation. Instead, let’s build systems that acknowledge, support and empower the whole person. In doing so, we won’t just send our employees home the same way they arrived – we’ll send them home even better.
About the Author: Summer Rae is a speaker and culture coach with more than a decade of experience developing and implementing comprehensive safety strategies. She specializes in transforming safety culture using a people-first approach. Native to Mississippi, Summer Rae currently resides in Costa Rica. Reach her at summerrae2024@gmail.com or via WhatsApp at +1-228-297-7447.
Equipotential Grounding for URD Work
I have written about grounding for the protection of employees numerous times in Incident Prevention magazine, addressing both the law and other issues. Let’s begin this installment with the understanding that “grounding for the protection of employees” – which is the phrase OSHA uses – means establishing an equipotential zone or EPZ. The purpose of grounding is to trip circuits. Grounding for the protection of employees can only be assured if it is arranged in an equipotential manner, preventing the worker from being exposed to a hazardous difference in potential. That’s the bottom line, and as I stated in the April-May 2025 issue of iP, equipotential grounding is the law (see https://incident-prevention.com/blog/equipotential-grounding-is-the-law/).
By the way, I reference OSHA 29 CFR 1910.269, part of the General Industry standards, throughout this text. Readers should note that the rules are exactly the same in the 1926.962 Construction standard.
The EPZ Challenge for URD
Now, let’s talk about the difficulty of creating an EPZ for workers in underground residential distribution (URD), which is not exempt from OSHA’s grounding rules. As paragraph 1910.269(n)(3), “Equipotential zone,” states, “Temporary protective grounds shall be placed at such locations and arranged in such a manner that the employer can demonstrate will prevent each employee from being exposed to hazardous differences in electric potential.” There are no exceptions.
But when it comes to URD, especially repairing a cable or replacing elbows or terminators, it’s impossible to create an EPZ by simply arranging ground connections. However, we do have an option found at 1910.269(n)(2), which, after spelling out the requirements for proper switching, states the following: “… [the employer] shall ensure proper grounding of the lines or equipment as specified in paragraphs (n)(3) through (n)(8) of this section. However, if the employer can demonstrate that installation of a ground is impracticable or that the conditions resulting from the installation of a ground would present greater hazards to employees than working without grounds, the lines and equipment may be treated as deenergized provided that the employer establishes that all of the following conditions apply: The employer ensures that the lines and equipment are deenergized under the provisions of paragraph (m) of this section; there is no possibility of contact with another energized source; and the hazard of induced voltage is not present.”
Paragraph 1910.269(n)(2) requires use of equipotential grounding to protect the employee, or the employer must meet the conditions of isolation to prevent employee exposure to any potential that could create an electrical hazard.
Here’s the issue, which will likely ring true with many iP readers. We have crews working URD with no consideration given to what would happen if the URD circuit were inadvertently energized. Maybe even worse, no consideration is given to the presence of neutral current flowing in the URD system. Here is my prime example: There is not an overhead crew in the industry – at least I hope not – who would approach an overhead distribution system, put a system neutral in a hoist, cut that system neutral and then grab both cut ends barehanded. Such an act would expose a worker to an open neutral circuit and the possibility of system voltage in that open. In reality, the voltage in the open neutral is low because we have multigrounded neutral systems. It must be high enough to break the resistance of your skin; if that happened, neutral current would flow through your body. Nobody is going to take that chance. In the past, whenever I took my crew to a job that required opening a neutral, we had detailed discussions about how to mach out the neutral and the hazard to be prevented. Yet a crew who just went through a similar exercise with the overhead neutral will then go work a URD cable repair job in a ditch and reconnect the concentric system neutral with their bare hands.
What’s Really Happening?
Part of the issue is that very few people know of someone being shocked or electrocuted during a concentric neutral repair – but it does happen. Employees in a ditch or working at night will begin reassembling a concentric connection and see a little spark when the conductors touch. That spark tells the tale. It wouldn’t exist if there were no difference in potential. The difference is created by a combination of (1) the distance between the open concentric and the remote ground and (2) the current that is being picked up by the concentric neutral when they touch.
You may be asking, “Why don’t we get shocked?” The answer is the 50-volt buffer, which isn’t actually 50 volts. It’s just universally accepted that 50 volts is the natural average resistance of human skin. That value has evolved from Charles Dalziel’s work on the effects of electrical current on the human body. In the margins of his reporting, Dalziel noted that some of his test subjects required a higher voltage than others to expose them to current flow. The 50-volt resistance is also supplemented by other forms of resistance that a worker is wearing, such as boots and leather gloves. If the voltage cannot penetrate the resistance of a worker’s skin, current can’t flow, and the worker won’t be hurt. The fact is, every time you get between a concentric neutral, you have exposed yourself to a potential difference between the two cut ends that simply wasn’t high enough to penetrate your skin and allow current to flow through your body.
So, if it’s an open neutral, why isn’t the voltage high? The answer is that a multigrounded system created incidental protection. If I’m working on phase B of a community three-phase URD system, phases A and C are parallel to phase B. If phases A and C are intact, they create a remote bond across my open phase-B concentric. In addition, at each transformer on either side of my open, there is a ground rod tying the concentric to earth. URD workers have benefited from this incidental protection since the first URD trouble job was issued.
No Simple Solution
Can you trust this protection? Under normal conditions, it appears to be universally but conditionally protective. If the URD system were exposed to a fault anywhere on the URD and/or overhead feed system, the resulting ground fault on the concentric would likely create a high potential difference between the concentric and the earth the worker is standing on.
The problem here is that there is no simple solution, particularly if the phase conductors are exposed, such as during an elbow or pothead terminator change or in the middle of stripping cable, even if it’s grounded at both ends. Grounding at a remote end of the cable produces a potential difference between that remote ground and the local ground the worker is standing on. The only way to equalize those potentials is to strip the cable down to the phase and attach a ground to an equipotential mat, which, of course, isn’t possible.
This is where the 1910.269(n)(2) “installation of a ground is impracticable” provisions come in. Isolation is the only true solution. It’s used in overhead all the time. If I open a set of switches and have a visible open, the conductor between those two visible opens is no longer dangerous given the (n)(2) provisions that it cannot become energized, that it’s not subject to any other mode of energizing and that the isolated conductor isn’t exposed to an induction hazard.
For continued discussion of URD isolation, see “Worker protection while working de-energized underground distribution systems” (see https://ieeexplore.ieee.org/document/1256391), available through IEEE for a fee.
Visual Explanations
I’ve included three visual explanations on these pages demonstrating what happens when we isolate or attempt to isolate a URD cable. Since I can’t cover every isolation mode, I’m going to use the simplest one, which is incorporating the grounding bushing method you’re using to ground the remote end of a cable (see Image 1). Install the grounding bushing in the conventional manner and close the elbow. You’ve now confirmed that the cable is de-energized by a voltage check and the presence of a ground. When installing the grounding bushing, make the ground lead connection to the concentric lead on the elbow that you’re grounding. Once you’ve confirmed the condition of the cable, you must do two things: (1) lift the ground bushing out of the holding bracket in the enclosure and (2) cut the concentric below the ground lead, isolating it from the ring bond in the transformer, pad or switchgear. Using this method, you’ve totally isolated the cable, and you’ve put the phase conductor in series with the concentric, eliminating any possibility of capacitance on the cable.
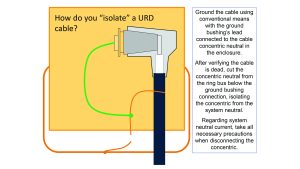
Using the example of our phase-B trouble call, one problem is that, if any system abnormalities exist – like unintended opens in the concentric on phase A or C – cutting a concentric could interrupt the system neutral for the rest of the circuit. Usually, a simple amp clamp test can be conducted to determine potential issues. If all three concentrics are continuous, take an amp current reading at a three-phase takeoff or a switch pad. You should find current on all three concentrics, indicating continuity. To ensure total isolation, drop a blanket over the isolated terminator so that you don’t create contact between the concentric and other parts of the system when you close the cabinet or pad.
Images 2 and 3 are used in the Institute for Safety in Powerline Construction’s personal protective grounding training protocols. iP is not offering them as mandatory solutions or recommendations. We are identifying the hazards and explaining how employers can effectively teach crews about them. Note that I am the author of all three images and give readers full authorization to use them in your training if you feel they could be helpful.
Image 2 demonstrates the electrical properties of isolating a URD cable as previously explained. On each end of the cable, the concentric has been cut free of the ring bond, putting the phase conductor in the elbow in series with the concentric on the cable. In addition, the elbow is draped with an orange blanket, but a 4-kV blanket would probably suffice. Now, look at the worker in the ditch, who’s holding a cable in each hand. The concentrics are not connected. Even if they were connected, no risk would exist for the worker because the concentrics are isolated at the remote end of the cable.
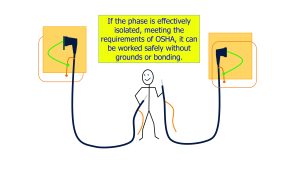
In Image 3, one small change creates an element of risk if it’s not properly understood. You can see that the concentric is still connected to the ring bond at each remote end of the cable. In this configuration, the phase conductor and concentric are still in series with each other. Additionally, the open phase conductor in the worker’s hands is parallel with the concentric. When the concentric is connected, it creates a bonding bridge across the open phase conductor. However, the concentric neutral bond will not be at the same potential as the open phase conductors because of the length of the cable, producing a resistance. It’s quite likely that, under normal conditions, the voltage between the open phase conductors would be very low, but there’s no telling what the potential difference could be in the event of a system fault. Image 3 also provides a visual representation (the meter) of the potential difference between the earth at the worker’s feet and the remotely grounded phase conductor.
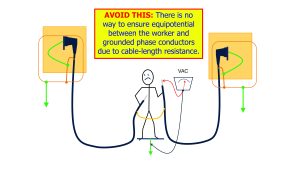
Conclusion
The issues with URD grounding are complex, but we can’t ignore the potential for serious injury. The whole reason we ground a cable is because we think an undesirable event could occur. If we think an undesirable event could occur, why should our preparation only be half-complete? Understand the principle of current flow in the grounded URD system and consider isolation as an effective means of protecting our employees.
About the Author: After 25 years as a transmission-distribution lineman and foreman, Jim Vaughn, CUSP, has devoted the last 28 years to safety and training. A noted author, trainer and lecturer, he is a senior consultant for the Institute for Safety in Powerline Construction. He can be reached at jim@ispconline.com.
The Evolution of Personal Protective Grounding: Part 1
Personal protective grounding, or PPG, is arguably the most critical safety procedure affecting contemporary lineworkers. Over time, it has evolved to include numerous significant elements that contribute to the success of today’s comprehensive methods and procedures.
To adequately address these elements, this article will be presented in two parts. Part one, which you are now reading, covers PPG’s early years. Part two – scheduled to be published in the October-November issue of Incident Prevention – will cover the critical testing and development that led to the methods and procedures currently in use.
1890-1910: The Beginning
Early power systems were relatively simple. A small generating source was connected to a line that served a small number of customers, or sometimes just one. If a line needed to be worked on, the generator was simply shut down while the lineworkers completed their tasks. There were no other sources of energy or adjacent lines to be concerned with. Some early systems, such as one in Niagara Falls, New York, included parallel lines built from the generating station to the load center. This allowed either line to be de-energized for work while the other line provided service.
As power systems were expanded and interconnected with multiple energy sources, clearing and working on lines and equipment became increasingly hazardous. Disconnects, switches and other devices were developed to isolate equipment and sections of lines. But with no established clearance procedures, accidents began to occur in which lineworkers were electrocuted by inadvertently energized lines. They were also introduced to the hazards of induction from adjacent energized lines. During this period, there was virtually no use of protective grounding.
1910-1930: Initial Mitigation Measures
Lighting streets in larger cities was the first widespread use of electric power in the 1890s. Series circuits supplied several arc lamps. Because streetlight circuits required occasional work, accidents happened when station operators inadvertently closed switches while work was in progress. To improve safety, the industry began to employ switches that could be closed to ground series streetlight circuits after opening them.
As the network of power lines grew, lineworkers working on de-energized lines began to feel the impact of induction from adjacent lines. They soon discovered they would not get “bit” by induction if they connected a jumper from the conductors they were working on to earth.
The next protective grounding measure, developed in the early 1900s, was the portable grounding wire. Its use involved connecting one end of a bare wire to earth or, in some cases, a water pipe or fire hydrant. A rope was thrown over all phase conductors. The opposite end of the wire was pulled over the conductors and tied to an object on the ground so that it made positive contact with the phase conductors.
A slight improvement to the wire method was the grounding chain, a long chain typically made of copper, brass or Copperweld. One end was connected to the ground source; the other was pulled tight over the conductors with a rope. This method was included in the 1928 first edition of “The Lineman’s Handbook,” known today as “The Lineman’s and Cableman’s Handbook.” The original handbook emphasized the importance of always (1) connecting the grounding chain to the ground source before pulling it over the conductors and (2) removing the chain before disconnecting it from the ground source.
Little information exists about how underground systems were grounded during this early period. Power companies in large cities with downtown underground systems utilized a variety of homemade grounding devices for equipment in manholes. Initial efforts and development focused on grounding overhead lines, followed by underground. Most power companies developed their own methods and tools for grounding lines and equipment.
No documentation exists from these early periods to suggest that lines and equipment were tested before protective grounds were installed. One of the first testing efforts, developed by Pennsylvania Water and Power, required the lineworker to throw a crescent wrench tied to a conductor that was connected to the grounded tower with a 5-amp fuse. If the line was energized, the fuse would blow.
1920-1940: Grounding Sets with Insulating Handles
In the 1920s, some power companies developed wood-handled protective ground sets. This led to the cluster-type arrangement, in which three conductor jumpers were connected to the junction, where another longer conductor was used to connect to the ground source. Each phase jumper had its wooden handle, which resulted in an entire ground set assembly. These improvements provided a more effective method for grounding conductors and allowed lineworkers to position themselves at a safe working distance in the event an energized line was inadvertently grounded.
Before the 1930s, protective grounding of lines and equipment was not a standard practice for all power companies. In many cases, it was left up to the line crew foreman to decide whether grounds were necessary. By the 1950s, however, protective grounding had become a standard practice and was included as a requirement in power company safety rule books.
Here are two interesting rules from the 1929 Penn Central Light & Power Co. safety rule book:
- “Rule 251 b. When lines or apparatus are killed for work, they shall be grounded and shorted on both sides of the location where the work is going to be done, regardless of whether there is more than one source of energy.”
- “Rule 251 d. Grounds shall never be placed on the same pole or tower where the work is to be done, for when moving the conductor, the ground might become detached. The placement of grounds shall be at least one span away. Under no circumstances shall work be done on a line over one mile from the point of grounding, as sufficient static might be picked up over a greater distance to cause an accident.”
By the 1930s, protective grounding was becoming standard practice for working on de-energized lines and equipment. These two general grounding rules were established and implemented by power companies:
- Grounds shall be installed between the source of energy and the work area.
- Grounds shall be installed in a manner that grounds and short-circuits the conductors.
Up to this point, no comprehensive engineering studies had been conducted concerning protective grounding’s effectiveness in limiting current passing through a worker’s body. Most grounding equipment was made by power companies, with no standardization and limited testing. Procedures varied considerably among companies and regions, and while the number of accidents involving electrocutions had gone down, it was still excessive. The two general rules noted above evolved into an industry-wide practice known as “bracket grounding,” during which grounds are placed on both sides of the worksite.
An interesting graphic created by the Public Service Company of Northern Illinois highlights a 1929 procedure the company developed to ground 66- to 132-kV lines. As shown below, the handline was used to pull a grounding chain over the conductors, along with applying individual grounds to the conductors. Lineworkers were required to wear rubber gloves throughout the process.
1940-1950: Understanding Dangerous Current Levels
Prior to the 1940s, there were no recognized studies on the effects of electrical shock on the human body relative to current and voltage levels. Then, in the late 1940s and early 1950s, Charles Dalziel (1904-1986) – a professor of electrical engineering and computer sciences at the University of California, Berkeley – performed considerable research regarding shock injuries to humans and animals.
Dalziel’s research led to information that could be used to evaluate the effectiveness of various protective grounding methods. Here is a list of his key conclusions:
- The minimum current detected by the human body is 1.2 mA.
- The average let-go threshold of current is 9 mA.
- Ventricular fibrillation thresholds may occur above:
- 03-second shock time duration: 1000 mA.
- 3-second shock time duration: 100 mA.
Thanks to Dalziel’s research, the industry now had credible information it could use to evaluate and optimize PPG methods. That information, which remains relevant today, would eventually lead to several considerable safety improvements for electrical workers.
Conclusion
Hazards abounded in the early days of electrical line work. Industry pioneers navigated the unknown with limited PPG knowledge, equipment and procedures. Through trial and error, more effective grounding methods gradually emerged, laying the foundation for essential safety practices. These hard-earned lessons continue to underscore PPG’s critical role in protecting lineworkers.
In the second part of this article, we will explore critical testing that deepened the industry’s understanding of PPG. As tool companies became more actively involved, they contributed to the development and refinement of grounding techniques. Discussion will include key advancements and their importance in ensuring the safety of today’s lineworkers.
About the Author: Alan Drew began his power industry career in 1959. While working for a local utility company, he earned a bachelor’s degree in electrical engineering. Drew was hired as the general superintendent for Clallam County Public Utility District in 1991. He moved to Boise, Idaho, in 1998, where he became an instructor with Northwest Lineman College and advanced to the position of senior vice president of research and development. He is a lifetime member of IEEE and a 2008 International Lineman Museum Hall of Fame inductee. Drew’s most recent accomplishment is writing “The American Lineman,” a book that honors the evolution and importance of the U.S. lineman. He retired in 2020 and is now a part-time technical consultant for Northwest Lineman College.
Sidebar: Line Terminal Ground Switches
In the 1920s, numerous companies began developing substation transmission-line ground switches and disconnects. They were primarily used to ensure the rapid operation of protective devices and to ground lines subjected to induction from adjacent lines. In many cases, line crews used ground switches as protective grounds. This practice was gradually eliminated as real-world experience demonstrated the improved safety of protective grounds at or near the worksite.
Safety By Design: Human and Organizational Performance
The first three articles in this six-part series addressed the critical nature and value of an organizational safety management system (SMS) that engages all employees and effectively mitigates risks through a developed plan for continuous improvement. This article focuses on human and organizational performance (HOP), an operational philosophy that utility organizations must incorporate into their SMS to achieve organizational safety success.
Over the years, traditional safety programs have primarily focused on managing employees, often overlooking the crucial systems designed to support them. Employees are expected to consistently make the right choices and adhere to safety rules 100% of the time, relying on the training they have received and the rules they must follow. When incidents occur, these employees may frequently be blamed; they are presumed to have been equipped with all the necessary tools and training to work safely yet opted not to utilize them. This scenario resembles a “Mission: Impossible” movie plot in which employees fail to “accept” their mission. While such a perspective is rarely accurate, many organizations continue to use a blame-centric model to tackle operational upsets, focusing on individual faults rather than improving organizational systems that empower and support employees.
HOP Overview
After discovering HOP, I was excited to learn more because it offered a fresh perspective that resonated with me. HOP enhances communication and understanding between employees and organizations, particularly in high-risk environments. It emphasizes the importance of grasping the reasons behind human errors and focuses on building resilient safety systems to support employees when they make mistakes. Rather than viewing human error as a failure to follow rules, HOP encourages us to recognize the underlying causes of mistakes and take action to address them.
The philosophy also encourages organizations to view errors as opportunities for learning and growth. Employees must recognize that mistakes are a normal part of life; this mindset helps to create safer work environments and fosters continuous improvement and innovation.
ASSP GM-Z10.100-2024, “Guidance and Implementation Manual for ANSI/ASSP Z10.0-2019 Occupational Health and Safety Management Systems,” introduces the five HOP principles and describes the importance of a learning and improving culture within a new view of safety. Here is a list of the principles, which are highlighted in Chapter 2, “Understanding the Workplace: The New View of Safety.”
- People will make mistakes.
- Error-likely situations are predictable.
- All human actions are influenced by the context in which they occur.
- Operational upsets can be avoided.
- How we respond to failure matters.
Principle 1: People will make mistakes.
In my consulting work, I sometimes ask senior leaders if they have made mistakes. The question is usually met with chuckles and agreements that everyone makes mistakes. That is when I drive home the point, highlighting that employees regularly make decisions that directly affect them and the organizations they work for. Often, these decisions must be made during high-risk work activities under significant pressure, when a mistake can be devastating. This first HOP principle becomes easier to understand when we consider all the dynamic forces involved in decision-making and recognize that humans are inherently imperfect.
Viewing mistakes as learning opportunities is key to fostering a positive company culture that promotes individual and organizational growth. While eliminating every error may not be realistic, organizations must aim to reduce the number of mistakes that result in unacceptable consequences. This emphasizes the importance of addressing human error in risk mitigation plans, which was discussed earlier in this series.
Principle 2: Error-likely situations are predictable.
“If you had only asked me, I could have told you that would happen.” Have you heard employees in your organization make that statement? It is not uncommon for people to sense potential problems yet fail to take action to resolve and learn from them.
An “error-likely situation” refers to an environment in which the likelihood of making mistakes increases when specific actions or tasks are being performed. The concept, defined in Volume 1 of the U.S. Department of Energy’s “Human Performance Improvement Handbook,” is linked to error precursors or error traps. These conditions increase the risk of making mistakes and usually exist before any errors occur. By identifying and removing such traps, we can minimize jobsite mistakes.
While it may be tempting to stick to familiar routines – especially if your organization has not experienced any serious injuries or fatalities – leaders must recognize that employees possess valuable insights that can influence the likelihood of errors. The key is to develop operational processes designed to identify and address error traps before, during and after work. By focusing on both task-related and individual factors throughout the work process, organizations can reduce the risk of mistakes and continuously improve their ability to predict and mitigate errors.
Principle 3: All human actions are influenced by the context in which they occur.
Numerous organizations face significant challenges with this principle relative to organizational culture. One real-life example is members of a work group who adhere to safety rules when the “safety guy” is present but revert to their usual unsafe practices once he leaves. This behavior indicates that the work group’s decision-making is influenced by an organizational culture that undervalues safety, directly affecting how work is performed.
It is essential to recognize that our environment and circumstances greatly impact our behavior and decision-making processes. Organizations must proactively identify and rectify the gaps in their operational control structures that support safety processes. These gaps can severely impede employees’ ability to make timely decisions, compromising safety and productivity. By fostering a culture of safety and continuously evaluating and improving operational controls, organizations can empower their employees and enhance overall performance. Prioritizing these improvements protects the workforce and contributes to the organization’s long-term success and sustainability.
Principle 4: Operational upsets can be avoided.
The most effective way to prevent operational upsets or disruptions is to learn from the work being carried out. It is crucial to acknowledge that opportunities for learning and growth occur daily as tasks are performed during regular operations. Many organizations focus solely on incidents, missing valuable chances to improve. An organization with a strong culture is more likely to thrive when it is not constantly in crisis mode, trying to address past issues.
The second chapter of ASSP GM-Z10.100-2024 identifies the importance of learning from daily work. Potential learning events highlighted in the standard include:
- Tasks that employees mostly do well but that are not always successfully completed due to the challenges involved.
- Tasks with issues being reported by employees.
- Tasks that have gone exceptionally well.
- Tasks involving the successful implementation of new designs, processes or procedures.
- Tasks that resulted in serious injuries or fatalities.
Our industry utilizes various initiatives and tools to learn from work – such as after-action reviews, observations, job hazard analyses and learning teams – which are essential for identifying issues. However, organizations must also act when they recognize improvement opportunities. Positive action fosters cultural growth, while a lack of action can cause the existing culture to crumble.
Principle 5: How we respond to failure matters.
An organization’s responses to operational upsets can make a considerable impact on company culture. Positive responses encourage a culture of learning and improvement. They also help employees feel empowered to grow in their commitment to safety. Negative or punishing responses cause fear and anxiety, potentially stifling employee creativity and growth. This kind of environment can erode trust and lower morale, ultimately pushing an organization’s strong culture toward possible extinction.
Some companies face challenges in deciding how to respond, often delaying the process for weeks or even years. Remember that a lack of response or a delayed response can be just as devastating as punishing behavior, preventing any opportunity for improvement.
Summary
Integrating HOP principles into an SMS is essential to fostering a culture of trust, learning and continuous improvement. By shifting from a blame-focused approach to one that acknowledges and addresses the underlying factors that influence human behavior, organizations can build more resilient systems and empower employees to engage more meaningfully in safety efforts. Recognizing that mistakes are inevitable and often predictable, leaders must proactively identify risks and implement effective solutions. Ultimately, how an organization responds to failure defines its safety culture and determines its ability to grow stronger from every challenge it faces.
About the Author: Pam Tompkins, CUSP, CSP, is president and CEO of SET Solutions LLC. She is a 40-year veteran of the electric utility industry, a founding member of the Utility Safety & Ops Leadership Network and past chair of the USOLN executive board. Tompkins worked in the utility industry for over 20 years and has provided electric power safety consulting for the last 25 years. An OSHA-authorized instructor, she has supported utilities, contractors and other organizations operating electric power systems in designing and maintaining safety improvement methods and strategies for organizational excellence.
Clearing Up Confusion About Host-Contractor Relationships
In my consulting work, I’ve found there is some industry confusion regarding the relationship between a host utility and an independent contractor company. To help provide clarity, I’m going to kick off this installment of “Voice of Experience” with an overview of each party’s obligations from an OSHA perspective.
A contract employee performs work covered by a signed agreement between the host utility and the contractor company. The host’s construction coordinator must work with contract employees on the host’s system. The host must also provide training for the tasks contract employees are expected to perform. Further, the host’s management team determines all personal protective equipment to be used, the supervisory oversight required, and training and work schedules.
One exception is that a host utility should not record contract employee illness and accident data on their OSHA log; that should be captured in the contractor’s log. Also note that contract worker benefits must be supplied through the contractor company.
There is a risk of tort lawsuits if these obligations aren’t met. In addition, if a contract employee working on a host utility system is significantly injured or killed, OSHA’s 1999 Multi-Employer Citation Policy (see www.osha.gov/enforcement/directives/cpl-02-00-124) could come into play. The host and contractor company are responsible for managing the job together to prevent accidents and monitor employee activities.
Four employer roles are defined by the 1999 OSHA policy. The host utility or contractor company may be considered an exposing employer (employees are exposed to a hazard) or a creating employer (the employer caused a hazardous condition that violated an OSHA standard). A controlling employer has general supervisory authority over the worksite, including the power to correct violations or require others to fix them. A correcting employer has oversight to stop and correct work if noncompliance or unsafe practices are observed. Per OSHA 29 CFR 1910.269(a)(3)(iii), the contract and host employers shall coordinate their work rules and procedures so that all employees are adequately protected.
Construction Coordinator: A Critical Role
Based on the information above, it is obvious that either or both the host utility and contractor company can be held accountable and responsible for all jobsite employees. For example, an on-site construction coordinator who doesn’t put a stop to unsafe work practices could be cited for failure to do so as OSHA views an employer’s silence as consent for the unsafe work to continue.
This means host utilities must employ highly qualified, trained individuals as construction coordinators and ensure they fully understand system and equipment grounding principles. For instance, not all companies require employees to wear sleeves when performing energized work, but to comply with 1910.269(l), they must have an exceptional coverup, insulation and isolation program to enable safe work on exposed energized conductors and equipment.
Construction coordinators should visit jobsites at unannounced times when work is in progress. A coordinator who is on-site every day could give the impression that the host utility is “supervising” the job, which has the potential to become deeply problematic if an incident were to occur in which a worker sustained severe injuries or worse. Among other things, such circumstances can increase the likelihood that contract employees will file civil tort cases against host utilities.
Typically, a construction coordinator engages in two primary functions. The first is quality control, or confirming that the contractor is doing their work as well as can be expected while adhering to the host utility’s contract specifications. Quality control also requires the coordinator to verify that all work complies with applicable local, state, Department of Transportation and OSHA rules and regulations.
Second, to successfully manage a multiemployer project, the construction coordinator must fully understand the contents of the signed contract between the host utility and contractor company. Readers should note that if the host utility requires contract employees to engage in specific work practices that exceed the minimum OSHA requirements found in 1910.269, those practices must be described in the contract. If the contract does not reference specific practices, the OSHA standard provides the basic requirements to be met.
Let’s say a construction coordinator offers workers advice or suggestions regarding safe work methods that are purely the coordinator’s opinion (i.e., not found anywhere in the rules or contract). This is a red flag that the employer must address once it’s recognized. If an incident were to occur due to a coordinator’s misinformation, the investigation would involve the host utility and contractor company and include a review of any instructions or corrections the coordinator made. Both parties could face OSHA citations, and the host utility might even end up with a tort liability case filed against them.
I’ve occasionally discovered this when working with industry clients. A construction coordinator provides a suggestion or direction to employees about how to complete a task, but it’s not considered the best practice, or maybe they offer up incorrect work practices based on personal experience or procedures written by the host utility that conflict with regulatory requirements. These instances often occur due to erroneous interpretations of industry regulations, underscoring my earlier point that utilities must employ highly qualified, trained individuals as construction coordinators.
From Policy to Law
During preamble meetings when the 2014 OSHA regulatory updates were being developed, contractor companies shared one of their primary concerns – that host utilities sometimes failed to provide them with all the safety-related information they needed to comply with OSHA regulations on host systems. The choice was made to adopt language from the 1999 Multi-Employer Citation Policy into law. Found at OSHA 1910.269(a)(4), the rule details information that host utilities must provide to contractor companies, stating the following: “Existing characteristics and conditions of electric lines and equipment that are related to the safety of the work to be performed shall be determined before work on or near the lines or equipment is started. Such characteristics and conditions include, but are not limited to, the nominal voltages of lines and equipment; the maximum switching-transient voltages; the presence of hazardous induced voltages; the presence of protective grounds and equipment grounding conductors; the locations of circuits and equipment, including electric supply lines, communication lines, and fire-protective signaling circuits; the condition of protective grounds and equipment grounding conductors; the condition of poles; and environmental conditions relating to safety.”
Conclusion
I hope I have helped to clarify some of the industry misunderstandings regarding host utility and contractor relationships and responsibilities. If you have related questions not addressed here, feel free to reach out to me (rainesafety@gmail.com) or email Incident Prevention’s editor, Kate Wade (kwade@utilitybusinessmedia.com). We will help you find the answers you need to best protect your workforce.
About the Author: Danny Raines, CUSP, is an author, an OSHA-authorized trainer, and a transmission and distribution safety consultant who retired from Georgia Power after 40 years of service and now operates Raines Utility Safety Solutions LLC.
Learn more from Danny Raines on the Utility Safety Podcast series. Listen now at https://utilitysafety.podbean.com!
August-September 2025 Q&A
Q: If a crew is setting a steel pole between energized phases (69 kV), would the 3.29-foot minimum approach distance found in OSHA Table 6 apply, or should we defer to the 15-foot clearance?
A: Setting poles is new construction that OSHA covers in 29 CFR 1926.960, Table V-5, “Alternative Minimum Approach Distances for Voltages of 72.5 kV and Less.”
There is cover rated up to 72 kV phase to phase, so for a 69-kV system, cover can be used. Without cover, an electrical crew can use the 3.29-foot MAD for phase to ground. If cover is not used and a conductive object could enter the electrical component air gap for both adjacent phases of the 69-kV system, the 3.94-foot phase-to-phase MAD would apply.
MAD applies when work is being done by a qualified electrical crew and an electrically trained, qualified operator. The standard clearance applies when the crew members and equipment operator aren’t qualified.
OSHA’s rule states that no employee shall approach closer than the MAD unless they are insulated by gloves or the energized part is insulated by cover. You can choose either option. In the example you provided, cover is preferred because of the issues with load control. Of course, another option is spreading phases to increase space. There is no cover rated for system voltages above 69 kV, so isolation for 115 kV and above is the method to use.
Q: We are a small utility with few resources seeking guidance about layering arc-resistant PPE garments to achieve greater protection. We have some exposures in pad-mounted switching calculated at Category 4, and we understand the following:
- Layering two garments does not result in a simple mathematical combination of their individual arc ratings.
- Only testing can truly determine the protection of two garments worn together.
- The gold standard is to match garment ratings with assessed hazards.
With that said, it seems logical that two AR garments worn together would yield higher-level protection. My question is, can we layer Category 3 sweatshirts and medium-weight jackets over Category 2 shirts for tasks with arc risks greater than the rating of the Category 3 garments? Because we’re ideally looking for price deals, we don’t restrict garment procurement to one manufacturer. That makes testing each layer combination impractical and far outside our budget. Do you have any thoughts or suggestions?
A: It might be justifiable and worthwhile to partner with just one garment vendor to meet your obligation to your employees. Combination testing is required to ensure worker protection levels. A manufacturer is unlikely to offer their lab results with a competitor’s product, and in your case, because you buy garments from various manufacturers, every purchase would be subject to a category value change. By opting to partner with a sole vendor, you gain access to information and support regarding layering designs and values.
As to your Category 4 URD exposures, the use of longer shotguns and sticks can move exposed workers farther from the source of an arc flash and may provide a way to keep exposures at Category 2. It’s the same with substations. Switching procedures can usually keep technicians far enough away that they rarely exceed Category 3, but we yield to your source calculations.
The bottom line is that you’re right. OSHA states that you cannot assume the combined arc thermal performance value, or ATPV, of layered materials because, as you said, they are not 1:1. If you’re layering garments made by more than one manufacturer to achieve a certain ATPV, OSHA’s expectation is that you tested the layers together using the industry-required standardized testing. On the other hand, if you’re layering garments from the same manufacturer, they have either already tested or will test the layers to identify the combined APTV.
Q1: Something came up during a grounding scenario that I’d never questioned before. Does OSHA require a visually verifiable air gap? Our answer to this was yes, absolutely, no question about it – it’s a widely agreed-upon best practice. But we have a utility customer who told us an open is verified by checking for the absence of voltage. Can you explain the correct approach?
Incident Prevention also received a second, related question from another reader.
Q2: We are working through the question of requiring a visual open on equipment owned by a big customer of ours. OSHA 1910.269(m), “Deenergizing lines and equipment for employee protection,” states that the employer must ensure disconnects, jumpers and other means are open. Having a visual open has always been the company procedure. In reading the regulation, however, I am struggling to understand what OSHA is saying. I think part of it is checking for lack of voltage, but the other part is having a visual on the contacts, whether that’s an open-air gap on a disconnect or one through a window on underground equipment. A camera that shows an internal target wouldn’t meet what I believe to be true. Can you help?
A: OSHA’s rules are open-ended, or what’s referred to as “performance based”; they state what must be accomplished. The employer decides how they will meet those expectations. A voltage check meets the requirement to ensure the facility is de-energized. The OSHA standard does not use the term “visual open” as a requirement. Whatever we decide to do, the procedure and solution employed to protect the worker must be defensible. We accomplish that by engaging in common industry practices.
In most cases, a visible open is only the beginning of protection for the worker. Ensuring that the open remains open and can’t inadvertently be closed is the second – and probably most important – part, especially where there are no “locks” that can be used to ensure an open switch stays open. Typically, the third part is having a written policy and/or training for those who rely on the open for their protection.
The OSHA rule calls out switches, disconnectors, jumpers and taps, and it requires the means to be inoperable. The standard doesn’t differentiate between untap and tape back or total removal. Jumper removal meets the obligation to be inoperable. The rule also requires tagging of the inoperable means, which must conclude with ensuring that no one with the capability could come by and replace a missing jumper. It’s the same with removing a barrel; you still tag for the highly unlikely but not impossible event that someone could come by with an extendo stick and a spare barrel.
The bottom line is that the open was created for worker protection and therefore must be tagged.
Most utilities frown on an open disconnect in an enclosure where the disconnect isn’t visible. For that reason, numerous manufacturers now offer view ports for visual observations of open contacts. A view port can be coupled with a locking or blocking mechanism, which is the second part (noted above) that ensures open contacts can’t be inadvertently closed.
Q: When and why did the industry begin using red for L1, white for L2 and blue for L3? Doesn’t the National Electrical Code standardize the colors on 240 volts (i.e., L1: black, L2: red and L3: blue) and 480 volts (L1: brown, L2: orange and L3: yellow)? Also, is there a different color code once you get above 480 volts?
A: Power-line installations are not subject to the National Electrical Code. We use the “X” and “H” 1/2/3 designations common to transformers, which are standardized in transformer consensus standards. In a single phase, X2 is a neutral bushing, but the conductor itself is usually bare past the bus jumper from the transformer. When we put notations in a customer’s meter, we typically use magic marker to label a 1/2/3 and rotational direction. We don’t color-code our line-side conductors; we use voltmeters.
The NEC does not designate phase colors, except the neutral being white or gray and ground wires being green or bare copper. The color conventions – red, black, orange, brown, and blue and yellow – are exactly that: conventions common to the electrical industry. So, what is required? If you put orange on one end of phase B, the other end of the same conductor must also be orange.
The purpose of using colors is to ensure workers can properly note phase rotation during the initial hookup. With single-phase, it doesn’t matter whether one is red or black or whether they’re the same at the other end. With three-phase, color was originally used to designate the high leg for open delta. Other colors have simply caught on, inspired by tape manufacturers and companies, like Brady, that make labels for wire.
Do you have a question regarding best practices, work procedures or other utility safety-related topics? If so, please send your inquiries directly to kwade@utilitybusinessmedia.com. Questions submitted are reviewed and answered by the iP editorial advisory board and other subject matter experts.
Your Response Matters … A Lot
How you respond to other people and events matters. It matters a lot. Your responses – both as a leader and a member of the TEAM (Together Everyone Accomplishes More) – impact every part of your life, including culture, relationships and safety.
Let’s start with this: “Responding” is a task. To perform the task well, we need tools that give us time to think, help us focus our attention and assist us in controlling our work, emotions, risk tolerance and decision-making. Now, keeping in mind that good tools help us work better and great tools help us think better, we’re going to discuss a great tool that will help optimize our response to any event.
When discussing principle one (“Take 100% responsibility for your life”) in his book “The Success Principles,” Jack Canfield offers up one of the most powerful tools I have ever learned to use: Event + Response = Outcome, or E + R = O. Essentially, this equation tells us that because we have little to no control over daily events (e.g., circumstances, people, timing), we must focus on our ideal outcomes and then influence those outcomes through our responses. Principle one concludes with a very powerful message: Pay attention … your results don’t lie.
To illustrate how the E + R = O tool works, think about driving near another vehicle whose driver has road rage. That driver’s actions are beyond your control, but your response to the situation is not. Pause to define your outcome (e.g., I want to arrive at my destination safely and on time) and you’ll likely choose not to engage with the other driver. That’s an excellent use of the tool.
What would happen during the same event if you were to respond differently? Maybe you don’t pause and have an emotional response, or perhaps you define your outcome as wanting to engage with the driver to get back at them. Either response would escalate the event and potentially result in a much different outcome, such as violence or a vehicle accident.
E + R = O or A B C D E?
In Chapter 1 of “The 7 Habits of Highly Effective People,” author Stephen R. Covey provides insight about being proactive. He writes about our Circle of Influence (how you respond) and our Circle of Concern (events happening to and around you). We can add a Circle of Control, which encompasses our responses, emotions and decisions. The test is simple. Events occur within your Circle of Concern. You either E + R = O or you A B C D E (accuse, blame, complain, defend and deny, and make excuses). If you A B C D E, you are spending too much time focused on events in your Circle of Concern. If you pause, define your outcome and respond appropriately, you are using the E + R = O tool well.
Let’s walk through how the tool works during a common event that can have a huge impact on safety, culture and relationships: I make an error. Do I respond by hiding it? Do I voluntarily report the error? If I report it, how will my leaders and organization respond? Will I be punished or ignored, or will my error be shared so we can apply lessons learned? As Doug Hill – a retired lineworker, safety culture champion and trainer for the Incident Prevention Institute – often says, “You can name and blame, or you can learn and improve. You can’t do both.”
The same principle applies to success. How you respond to success matters a lot. Think about someone exercising stop-work authority. How you respond to that also matters a lot, as do your responses to unsafe acts and conditions. And here’s one more thing that matters a lot: your responses to multiple events that happen each day, such as participating in a job briefing, attending a training session or teaching a class. Look for opportunities to respond well. If you don’t like the TEAM performance you’re seeing, spend more time evaluating your responses and less time focusing on events.
Conclusion
The primary value of the E + R = O tool is that using it gives you time to think. Pausing between the event and your response allows you to focus your attention. Make a habit of practicing this tool during simple events in low-risk environments so you can use it well when you really need it. The next time you encounter a challenging person or situation, ask yourself, “What is my desired outcome?” Once you have defined that with extreme clarity, the approach to handling the person or situation should become obvious, improving the likelihood that you will achieve your desired outcome.
E + R = O helps us with life skills. Employing this tool can enhance culture, safety, relationships, emotional intelligence and decision-making. To maximize its value, however, you must first be trained to use it properly.
About the Author: David McPeak, CUSP, CIT, CHST, CSP, CSSM, is the director of professional development for Utility Business Media’s Incident Prevention Institute (https://ip-institute.com) and the author of “Frontline Leadership – The Hurdle” and “Frontline Incident Prevention – The Hurdle.” He has extensive experience and expertise in leadership, human performance, safety and operations. McPeak is passionate about personal and professional development and believes that intrapersonal and interpersonal skills are key to success. He also is an advanced certified practitioner in DISC, emotional intelligence, the Hartman Value Profile, learning styles and motivators.
About Frontline Fundamentals: Frontline Fundamentals topics are derived from the Incident Prevention Institute’s popular Frontline training program (https://frontlineutilityleader.com). Frontline covers critical knowledge, skills and abilities for utility leaders and aligns with the Certified Utility Safety Professional exam blueprint.
Webinar: Your Response Matters
September 3, 2025, at 11 a.m. Eastern
Visit https://ip-institute.com/frontline-webinars/ for more information.
Disable Reclosing to Heighten Worker Protection
In utility line work, safety is built on layers. Each layer is essential; ideally, if one fails, another layer will prevent alignment of all the holes in James Reason’s proverbial Swiss cheese.
Recently, while preparing a training presentation focused on switching procedures, de-energization and grounding, I found myself thinking through the process backward and forward. I considered the moment a line is still energized, imagining the scenarios that could unfold for a troubleman or line crew. Then I thought forward again, this time to the crew working behind an open switch, between grounds and in an equipotential zone.
One question kept surfacing: If grounding is meant to protect us in the event of re-energization, why don’t we always disable reclosing on the circuit we’re working? OSHA requires blocking remote supervisory control during de-energized and grounded work, but disabling reclosing is not mandated. That’s a critical gap in our safety net.
A Hidden Risk
Automatic reclosing is designed to restore power after temporary faults, such as a tree brushing a line. But when a line is intentionally de-energized and grounded for maintenance, any re-energization attempt could be catastrophic. If reclosing is left enabled, the breaker will attempt to reclose multiple times – even into a grounded fault – before finally locking out.
With reclosing disabled, time delays are removed, even on the first relay. Here’s how it works:
- The breaker trips on the first fault, typically within three to eight cycles depending on settings and voltage.
- No reclosing attempts are made.
- The circuit locks out immediately and remains de-energized.
Immediate lockout significantly reduces the risk of unexpected re-energization and ensures the line stays safely out of service until it is manually restored.
Why Does This Matter for Workers?
Grounding is not a guarantee of safety during high-energy fault events. Reclosing into a grounded line can:
- Cause arcing, equipment damage and violent whipping of ground jumpers.
- Expose workers to dangerous step and touch potentials.
- Lead to failure of personal protective ground jumpers due to excessive fault energy.
The longer the system continues to reclose, the greater the energy delivered into the fault. This could exceed the capacity of protective grounds, leaving the line energized and workers exposed.
The Hazards of Multiple Reclosing Attempts
The first reclosing attempt typically uses a fast-acting protection curve to quickly clear transient faults. However, second and third attempts often rely on slower inverse time-delay curves, allowing more time for faults to clear naturally. This results in:
- Longer energized durations.
- Increased energy delivered into the fault.
- Greater arc flash risk.
- Elevated likelihood of ground jumper failure, which could result in the line remaining energized.
- Higher potential for injury or death.
Remember, reclosing’s job is to remove the fault. If the fault is a grounded line with personnel present, reclosing works against us – not for us.
Final Word
Workers are exposed to increased risk as repeated reclosing attempts lengthen time delays, making the act of disabling reclosing when working on grounded lines not just a best practice but a potentially lifesaving act.
About the Author: Ben Browne, CUSP, has over 20 years of global experience in electric utility safety, risk management and sustainability leadership. He currently serves as the safety and environmental manager for S&C Electric Co.
Utility Safety Podcast – Industrial Athletes – Keeping Utility Workers Safe in Extreme Heat
In this special Incident Prevention Utility Safety Podcast episode for Extreme Heat Awareness Month, host Kate Wade welcomes Dr. Kevin Rindal of Vimocity and Scott Head of DragonWear to share essential strategies for preventing heat stress among utility workers.
They dive deep into how extreme heat affects the human body, why utility workers are especially vulnerable, and how modern flame-resistant (FR) clothing technology can dramatically improve comfort, safety, and productivity in the field.
Drawing on sports medicine principles, real-world utility experience, and advanced FR fabric design, this conversation is packed with actionable advice for safety leaders, crew trainers, and frontline workers alike.
Contact our guests – Dr. Kevin Rindal and Scott Head: kevin@vimocity.com and scott@dragonwear.com.
Subscribe to Incident Prevention Magazine – https://incident-prevention.com/subscribe-now/
Register for the iP Utility Safety Conference & Expo – https://utilitysafetyconference.com/
Key Takeaways:
-
Utility workers are industrial athletes who need to manage hydration, acclimatization, and recovery like pro athletes do.
-
Early signs of heat stress include confusion, irritability, and poor coordination—workers and supervisors need to spot these quickly.
-
Modern FR clothing is engineered to wick moisture, provide stretch, offer UV and arc-flash protection, and even manage odor—reducing distractions and injuries.
-
Dynamic warm-ups, proper hydration strategies, and electrolyte management are critical for heat adaptation.
-
Safety leaders should equip crews with a “toolbelt” of resources: high-performance clothing, hydration plans, training, and real-time site monitoring for evolving heat risks.
3 Q&As from the Episode:
Q1: What actually happens to the body during heat stress?
A: Blood flow shifts from the brain and core to the skin to cool off, reducing cognitive sharpness. Early signs include confusion, irritability, and clumsy movements—critical warnings for supervisors to watch for.
Q2: How can clothing reduce heat stress risk?
A: Advanced FR garments like DragonWear’s Pro Dry Tech shirts use multi-fiber designs to wick moisture, offer stretch for movement, provide UV/arc-flash protection, and even manage odor—keeping workers cooler, drier, and focused.
Q3: What can crews do to prepare for working in extreme heat?
A: Start hydration the day before, sip water with electrolytes throughout shifts, do dynamic warm-ups to prime blood flow, and plan shaded breaks. Avoiding sugary or dehydrating drinks is also essential.
#UtilitySafetyPodcast #HeatStressPrevention #FRClothing #WorkerSafety #ExtremeHeatAwareness #DragonWear #IndustrialAthlette #Lineworker #OSHA
Industrial Helmets with Smart Safety Technology
Twiceme Technology, the digital safety standard for jobsites and adventures, has named Securis, a Velotec Sports industrial head protection brand, as its latest PPE partner. Securis will integrate Twiceme’s smart safety technology into its entire product line, enhancing safety for industrial workers and streamlining organizational safety management.
Velotec Sports introduced the Securis brand in 2023 after a decade in outdoor protective headgear and will embed Twiceme chips into the shell of its Type II safety helmets. By partnering with Twiceme, Securis will enable its users to upload work-related documents and medical information to speed certification tracking and response times in the case of an emergency. First responders can immediately access critical data – including personal contacts, medical conditions and allergies – by scanning the Twiceme symbol on the back of a helmet during emergencies.
Securis helmets with Twiceme will be available starting in July 2025. www.securisprotect.com, www.twiceme.com
Double Bundle Line Cart
LineWise now offers a Horizontal Double Bundle Line Cart, available in a gas-powered or non-powered version. Designed for use on horizontal bundles spaced 18 inches apart, the new line cart offers a safe, specially engineered mobile platform for performing line inspection and maintenance on transmission lines.
The Horizontal Double Bundle Line Cart offers a 400-pound capacity with a single person occupancy limit, and it includes a foldable seat for operator comfort. Constructed of strong, lightweight aluminum alloy, the cart is bolted together, so there are no welded seams to crack. For added safety, the line cart has a toe board around the floor and two safety bars positioned over the conductors.
Customers can choose a gas-powered or non-powered version of the line cart. The non-powered model requires workers to manually pull themselves along the conductors to move the cart. The gas-powered version includes a 3.2-horsepower gasoline engine to propel the cart. The engine drives two of the cart’s four wheels and comes with a throttle control to adjust speed. It has a transmission with reverse and two forward gears for excellent control.
An optional tow bar assembly is offered for the non-powered Horizontal Double Bundle Line Cart. This helps to maintain balance and alignment of the cart on the conductors. It also allows lineworkers to pull the cart from ground level using a tow rope. https://line-wise.com
Double-Insulated Pry Bars
Cementex’s double-insulated pry bars, engineered with the company’s industry-leading insulation technology, provide the leverage required to pry open whatever is being worked on while maintaining a barrier against electrical hazards. The signature orange-over-yellow insulation offers clear visual safety indication, allowing users to both quickly identify wear and maintain compliance with stringent safety standards.
Manufactured in the U.S. with both American and globally sourced materials, Cementex double-insulated pry bars are tested to 10,000 volts and rated for live use up to 1,000 VAC/1500 VDC. Available in 12-inch and 36-inch options to suit various applications, they can tackle a range of diverse and demanding challenges. The technology also empowers customers to easily meet requirements such as OSHA safety-related work practices, the NFPA 70E standard and CSA Z462. Backed by a lifetime guarantee on mechanical parts and a two-year guarantee on insulation, these pry bars are built to last. www.cementexusa.com
Customizable Training and Tech Tips
Terex Utilities offers a variety of training opportunities that can be customized to fit customers’ needs. Training available to service personnel includes both hands-on and online opportunities. Maintenance training workshops are for mechanics working on Terex digger derricks and bucket trucks. Subjects and activities covered in these workshops may include understanding and using load charts; performing periodic inspections; troubleshooting PTO issues; changing the direction of a pump; and performing a leakage test on outriggers. The Master Mechanic Learning Center is an online training platform covering inspection, dielectric principles, hydraulic troubleshooting and other service issues.
Since 2012, Terex Utilities has published Tech Tips to answer frequently asked questions. Tech Tips address a single repair or replacement topic with step-by-step instructions and graphics. In 2024, customers downloaded these tips almost 15,800 times. Terex Tech Tips are continuously updated and expanded, so the company recommends checking back often to see what’s been updated. Topics cover a wide range of content, with some specific to Terex Utilities models and others that are more general in nature. Sign up for Tech Tips and stay updated on the latest Terex workshops and training on the company’s website. www.terex.com/utilities/en/support/technical-support/tech-tips/sign-up
Benchmark Study on the State of EHS
J. J. Keller & Associates Inc. recently released a report for its inaugural “State of Environmental Health & Safety” benchmarking study, conducted by the J. J. Keller Center for Market Insights, the company’s collaborative research arm. The study is aimed at gaining a deeper understanding of how safety professionals perceive safety within their organizations and the overall state of safety in today’s workplaces.
Conducted from November 18 to December 2, 2024, the online survey was open to individuals responsible for environmental health and safety. The study reflects J. J. Keller’s ongoing mission to protect people and the businesses they run because, by identifying the challenges faced by EHS professionals, it becomes possible to foster improvements within the industry. www.jjkellersafety.com/resources/whitepapers/ehs-benchmark-study-2024
Utility Safety Podcast: Deep Dive: Bucket Truck Safety: OSHA Standards and Other Considerations Written by Danny Raines, CUSP
In this episode, we unpack the vital safety standards, OSHA regulations, and field-tested insights that govern bucket truck operations in the electric utility industry. Based on the article “Bucket Truck Safety: OSHA Standards and Other Considerations” by Danny Raines, CUSP, we dive into key differences between Class A and Class B trucks, daily control tests, fall protection, and the nuances of operating near energized lines. You’ll learn why dielectric testing matters, how improper tool placement can lead to serious hazards, and what often-overlooked basics can prevent catastrophic incidents. Whether you’re in utility operations, safety management, or just curious about what keeps linemen safe, this is your shortcut to understanding critical compliance.
Gain practical takeaways, understand real-world challenges, and walk away with a new appreciation for the safety systems behind the power grid.
Read the article: https://incident-prevention.com/blog/bucket-truck-safety-osha-standards-and-other-considerations/
Key Takeaways:
-
OSHA 1910.67 is the foundational standard for bucket truck safety.
-
Daily lift control tests and proper bucket stance are mandatory safety practices.
-
Class A (barehand) and Class B (gloving) trucks serve different functions and require different protective strategies.
-
Fall protection is a non-negotiable requirement—fall distance and impact risk must be minimized.
-
Misconceptions about insulation and inadequate cover-up procedures are common contributors to incidents.
3 Podcast Questions and Answers:
Q1: Why is OSHA 1910.67 considered the backbone of bucket truck safety?
A1: Because it outlines non-negotiable requirements such as daily lift control testing, safe bucket operation, and movement restrictions—all of which are essential to preventing falls and electrocution.
Q2: What’s the key difference between Class A and Class B bucket trucks?
A2: Class A trucks are designed for direct contact with high-voltage lines and rely on the boom’s insulation, while Class B trucks require full cover-up and rubber glove protection due to lower insulation properties.
Q3: What unsafe practice is commonly observed and highlighted in the article?
A3: Moving trucks with elevated booms without proper exemption, and workers failing to properly cover energized parts—both of which dramatically increase risk.
Subscribe to Incident Prevention Magazine – https://incident-prevention.com/subscribe-now/
Register for the iP Utility Safety Conference & Expo – https://utilitysafetyconference.com/
Danny Raines, CUSP, is an author, an OSHA-authorized trainer, and a transmission and distribution safety consultant who retired from Georgia Power after 40 years of service and now operates Raines Utility Safety Solutions LLC.
#UtilitySafety #BucketTruckSafety #OSHAStandards #LinemanSafety #ElectricalUtilityWork
Silencing the Noise: Creating a Culture of Actionable Safety and Synchrony with Bill Martin, CUSP
In this episode of our Actionable Safety series, host Nick talks with Bill Martin and Kate Wade about moving beyond “safety noise” to create real, lasting change on the job. They dive deep into achieving buy-in through synchrony, overcoming defensiveness, and translating safety theory into real-world practice. With stories from climbing Mount Kenya to lessons learned in the utility industry, they explain how empathy, respect, and clear communication are essential for building a culture where safety improvements take hold. Listen in for practical strategies on fostering trust, testing new ideas without fear, and removing barriers that block true team alignment. If you’re ready to rethink compliance culture and help your crew take meaningful action, this episode is for you.
Subscribe to Incident Prevention Magazine – https://incident-prevention.com/subscribe-now/
Register for the iP Utility Safety Conference & Expo – https://utilitysafetyconference.com/
✅ Key Takeaways
-
Safety success depends on synchrony: Teams need shared purpose and alignment to move beyond noise and see real change.
-
Empathy and respect matter: You don’t have to like everyone you work with, but respecting them enables effective collaboration.
-
Defensiveness is a barrier: Recognize and manage defensive reactions to open the door to candid discussion and feedback.
-
Test and evaluate constantly: Progress requires trying new approaches and learning from all outcomes, not just repeating old rules.
-
Culture change is leadership’s job: Leaders must remove barriers to buy-in, making space for collective learning and growth.
3 Questions and Answers
Q1: What does “synchrony” mean in safety culture?
A: Synchrony is getting everyone on the same page, working toward a shared goal. It’s like a football team running plays in sync or an orchestra staying in tune—it ensures teams work together efficiently and safely.
Q2: How can leaders encourage buy-in from crews?
A: By removing barriers to participation, listening to feedback, and creating a culture where workers can test and evaluate new ideas without fear of judgment. Buy-in emerges naturally in an environment of trust and shared purpose.
Q3: Why is reducing “defensiveness” so important on the job?
A: Defensiveness blocks communication and critical thinking. By pausing before reacting, crews can shift from compliance mode to discovery mode—enabling safer, smarter decisions on the ground.
#SafetyCulture #UtilitySafety #LeadershipDevelopment #TeamworkMatters #ActionableSafety
Utility Safety Podcast: Deep Dive: Bucket Truck Safety: OSHA Standards and Other Considerations Written by Danny Raines, CUSP
In this episode, we unpack the vital safety standards, OSHA regulations, and field-tested insights that govern bucket truck operations in the electric utility industry. Based on the article “Bucket Truck Safety: OSHA Standards and Other Considerations” by Danny Raines, CUSP, we dive into key differences between Class A and Class B trucks, daily control tests, fall protection, and the nuances of operating near energized lines. You’ll learn why dielectric testing matters, how improper tool placement can lead to serious hazards, and what often-overlooked basics can prevent catastrophic incidents. Whether you’re in utility operations, safety management, or just curious about what keeps linemen safe, this is your shortcut to understanding critical compliance.
Gain practical takeaways, understand real-world challenges, and walk away with a new appreciation for the safety systems behind the power grid.
Read the article: https://incident-prevention.com/blog/bucket-truck-safety-osha-standards-and-other-considerations/
Key Takeaways:
-
OSHA 1910.67 is the foundational standard for bucket truck safety.
-
Daily lift control tests and proper bucket stance are mandatory safety practices.
-
Class A (barehand) and Class B (gloving) trucks serve different functions and require different protective strategies.
-
Fall protection is a non-negotiable requirement—fall distance and impact risk must be minimized.
-
Misconceptions about insulation and inadequate cover-up procedures are common contributors to incidents.
3 Podcast Questions and Answers:
Q1: Why is OSHA 1910.67 considered the backbone of bucket truck safety?
A1: Because it outlines non-negotiable requirements such as daily lift control testing, safe bucket operation, and movement restrictions—all of which are essential to preventing falls and electrocution.
Q2: What’s the key difference between Class A and Class B bucket trucks?
A2: Class A trucks are designed for direct contact with high-voltage lines and rely on the boom’s insulation, while Class B trucks require full cover-up and rubber glove protection due to lower insulation properties.
Q3: What unsafe practice is commonly observed and highlighted in the article?
A3: Moving trucks with elevated booms without proper exemption, and workers failing to properly cover energized parts—both of which dramatically increase risk.
Subscribe to Incident Prevention Magazine – https://incident-prevention.com/subscribe-now/
Register for the iP Utility Safety Conference & Expo – https://utilitysafetyconference.com/
Danny Raines, CUSP, is an author, an OSHA-authorized trainer, and a transmission and distribution safety consultant who retired from Georgia Power after 40 years of service and now operates Raines Utility Safety Solutions LLC.
#UtilitySafety #BucketTruckSafety #OSHAStandards #LinemanSafety #ElectricalUtilityWork
5 Core Components of a Well-Developed Storm Response Plan
Electric utilities are part of the backbone of modern society, providing essential power to homes, businesses, emergency services providers and more. But this critical service is vulnerable to extreme weather events that can cause massive disruptions, damage infrastructure and jeopardize public safety. Due to the frequency and severity of such events, it is more important than ever for electric power organizations to have a comprehensive storm response plan in place.
I’ve consistently been involved in storm response planning throughout my career, both as a lineman and a safety specialist. I’ve helped to restore power, oversee field operations and support logistics teams. In short, I’ve seen firsthand the necessity of a well-developed, effectively executed storm response plan to manage service disruptions, protect employees and the public, and maintain trust with stakeholders and regulatory agencies.
Based on my 26 years of field experience, a comprehensive storm response plan will address the following five areas of concern.
1. Downtime and Service Continuity
Safely minimizing the duration and impact of power outages is the primary objective of a good storm response plan. The plan should outline preparation, response and recovery protocols that will enable utility crews to respond efficiently. For example, response times may be considerably reduced by pre-staging crews and equipment near the area expected to be impacted by a storm.
Without a storm plan in place, utilities are forced to react instead of responding, which can cause delays and the inefficient use of resources. Every hour of downtime can potentially threaten lives and cost local economies millions of dollars, especially when outages affect vital services and/or vulnerable populations. A storm response plan helps to ensure that restoration work proceeds in a logical, prioritized, well-coordinated manner.
2. Employee and Public Safety
Restoring power in storm conditions is complex and poses hazards to those charged with the task; workers can potentially be exposed to live wires, unstable structures, hazardous debris and generator back-feed. They must be adequately trained for their assigned roles and adhere to rigorous safety protocols for their protection. These protocols safeguard lives while also helping employers avoid costly liabilities and reputational damage.
3. Regulatory Compliance and Risk Management
Some regulators require utility organizations to develop and maintain storm response plans, and they may audit a utility’s performance after a major weather event. Proof of a documented storm plan that has been successfully tested demonstrates compliance and reduces the risks of penalties and increased regulatory oversight.
A storm response plan is also an integral part of an electric utility’s broader risk management strategy. In part, that’s because insurance providers and investors often look for evidence of disaster preparedness. A utility with strong contingency plans in place increases its likelihood of securing favorable insurance rates and maintaining investor confidence, even after a major weather-related disruption.
4. Mutual Aid and Resource Acquisition
During severe, widespread weather events, no single utility has enough personnel or equipment to handle all the damage wrought. Entering into mutual-aid agreements with other utilities, contractors and industry vendors will help to ensure timely assistance is available when needed.
A comprehensive storm response plan will detail how to request line and vegetation management resources and damage assessment personnel to more efficiently manage outages and create a scalable model. Thus, it is important for utilities to consider the off-system vendor contracts or agreements that must be made.
Planning ahead allows for the optimized use of internal assets and off-system resources. Among other things, it enables utilities to do their best to ensure that fuel, vehicles and repair materials are stocked and accessible to workers. Logistical components like these can make the difference between typical recovery times and prolonged outages.
5. Post-Storm Assessments
A robust storm response plan will include a post-event review process. Once power has been restored to a utility’s customers, the organization should conduct a comprehensive assessment of its response, including a timeline review, to identify what went well and document areas for improvement. Regularly review and update storm response plans to incorporate lessons learned from these assessments.
On a related note, utility organizations should conduct storm response drills throughout the year. These drills – in combination with post-storm assessments – create a process of continuous improvement that can help utilities adapt to evolving threats, become more resilient, and reinforce an organizational culture of safety, preparedness and accountability.
Conclusion
It’s a must for today’s electric utilities to develop, implement, and regularly review and update a well-structured storm response plan. The protocols and policies detailed in such a plan provide indispensable guidance to help responding personnel safely act with speed, precision and confidence. Should you have questions about developing a plan for your organization, feel free to contact me directly at kcoffey@atkenergygroup.com. I’m happy to help you find the resources you need.
About the Author: Kirk Coffey, CUSP, is the director of business development for ATK Energy Group. Over the past 26 years, he has gained a reputation for his commitment to improving organizational safety and efficiency in the electric utility industry.
Variabilities in Electrical Arc Flash Protection
Accuracies are synonymous with safety and science. While many perceive that electrical safety needs to be highly exact, this article aims at creating awareness of why sticking to the basics is effective.
But before we delve into variability in electrical engineering, safe electrical work practices and electrical PPE, here is a brief story my second-year engineering physics professor shared when I was in school: A person stands in the center of a boxing ring; their soulmate stands in the corner. The person in the center is only allowed to walk toward their soulmate in discrete steps defined by exactly halving the distance between the two. The physicists witnessing this agree that it will be impossible for the distance between the two to ever reach zero. The engineers understand that they can eventually get as close to their soulmate as needed for a happily ever after.
Electrical Engineering
A post on Stack Exchange (https://electronics.stackexchange.com/questions/256283/what-does-the-us-power-supply-waveform-look-like) shows that 120 volts can actually be a 110-volt sine wave with a peak of 149 volts (see Picture 1), and even this varies between the home and the workplace (see Picture 2). The 110-volt equivalent (DC) – or root mean square – presents a 149-volt peak while a 122-volt equivalent presents a 165-volt peak (i.e., the measured empirical data differs from the theoretical conversion from root mean square to peak).
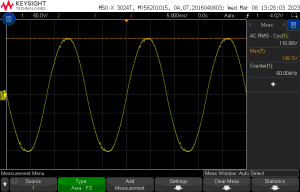
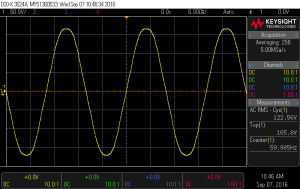
Voltages fluctuate in our homes, workplaces, large industrial plants and the power grid. These fluctuations may occur due to large motors, planned and unplanned outages, and time of day. Like voltages, currents also fluctuate. As little as a 1-amp current fluctuation can be the difference between a breaker tripping in 0.4 milliseconds or 0.4 seconds or even 4 seconds.
Current that flows during an electrical fault is known as short-circuit or fault current. Fault current is greatly influenced by the fault type. Leaving grounds on a circuit will generate close to the maximum short-circuit current that the system can deliver; this is called a bolted fault. If a worker accidentally slips a tool between conductors, an arc flash may occur. Arc flash is the plasma created between the conductors due to the breakdown of air. The arcing fault has more impedance than the scenario with the bolted fault containing the grounds and may propagate. Each of these scenarios influences the magnitude of the (arcing) fault current and the protective device operating time. Higher impedances produce lower short-circuit current, resulting in a longer trip time. So, it is impossible to predict the actual, real-life arc flash energy.
To cater to all these variabilities in fault current and protective device operating times, both the maximum and minimum fault currents and the associated protective device tripping times are considered. The fault currents and associated trip times are two key inputs used to estimate the arc flash hazard/incident energy (or arc flash energy). Some software can determine a wide range of combinations of these parameters and select a worst-case value. However, while science tries to model the incident energy as close to reality as possible, there are too many variables to call arc flash energy calculations “exact.” The IEEE 1584-2018 model used laboratory tests to create a statistically representative set of equations. The probability is extremely high that the real energy will be lower than the calculated energy, while the probability of predicting the actual energy is extremely low. This is exactly what any scientific committee would aim to achieve in a safety standard.
Forensic investigations and a literature review indicate that real-life accidents have produced lower energy levels than were predicted by the IEEE 1584-2018 calculations. Experience in the field shows that (1) the calculated incident energy is the worst case and (2) end users have no reason to believe that the true arc flash energy will exceed calculated values.
Variabilities in Work Practices
The distance from the arc source to the worker is highly variable. In practice, tasks such as removing a cover for thermal imaging and troubleshooting place the worker farther away than the 18-inch working distance for low voltage (208 volts to 480 volts) that is recommended in IEEE 1584-2018. During the development of the engineering equations, the working distance equivalency varied between 15 and 36 inches, helping to provide a worst case. Variability in the working distance is not only influenced by the position of the worker; research has demonstrated that in certain high-voltage applications, the arc has the potential to move, yielding a lower incident energy exposure to the worker than theoretically calculated (see https://ieeexplore.ieee.org/document/7439799). Here is a final note on working distance: The optimal worker position is to stand to the side of equipment, outside the line of fire and away from potential projectiles when possible (see https://ieeexplore.ieee.org/document/9188321).
Variability also occurs with PPE garments, specifically the materials used and how the gear is worn. Most workers prefer loose-fitting garments to allow for dexterity. This is quite different from how fabric is tested; when rated, it is firmly placed on the test panel. Secondly, although standards do not allow non-arc-rated layers to count toward the total protection level, most natural fibers will add a margin of protection. Arc-rated inner layers, when tested in combination, can potentially offer great gains in protection. It is extremely important to note that both OSHA and voluntary consensus standards prohibit the use of low-melting synthetic fabrics. The fit of the fabrics (tight vs. loose) can offer marginal protection that cannot be quantified. So, looseness and layering – including the type of layering – is another area in which variability works in favor of employee protection.
Fabrics, Test Methods and Assembled Garments
The arc ratings provided on garment labels are calculated using either ASTM F1959 or IEC 61482-1-1 A. The test to calculate an arc rating is not performed on a finished garment; it is done on the raw fabric material or material system used to construct the garment. Clothing design often results in significant portions of garments possessing multiple protective layers. Pockets, plackets, storm flaps, overlaps and similar items create these multilayer (i.e., more protective) areas.
In recent months, end users have had concerns about information stemming from retesting of various competitive products purchased from major reputable manufacturers. In nearly every case, retesting resulted in arc ratings lower than those listed on product labels. ASTM F1506 does not require retesting; however, when it is conducted, variations in arc ratings are not surprising or concerning to a trained eye. Numerous factors can create arc rating variability, such as natural variability in textile manufacturing, weight, finishing procedure and fabric color. Although there is no hard and fast rule, the general trend is that darker colors tend to produce slightly higher arc ratings than the same fabric in lighter colors. These differences may result in minor rating variations, but they very likely do not impact practical protection levels. In fact, even when many of these variables are removed, there can still be wide variations in results. One study that included 26 different arc ratings of the same fabric over several years found results to range from 8.3 to 13 cal/cm2. Each of the 26 arc ratings is a valid rating and could potentially be used to label the product.
Finally, consider the conservative nature of arc ratings. A rating is generated from a fabric tightly held against a sensor assembly. In contrast, a properly fitting garment incorporates a certain amount of ease, adding an insulating air layer between the garment and the skin, as mentioned earlier.
Concluding Remarks
Research and incident investigations show that workers are protected when arc flash incident energy calculations are correctly performed, arc-rated PPE is procured through reputable suppliers and end users dress to the correct levels. There is no literature indicating that any of the following activities will benefit worker safety or expose the employer to undue risk: padding the calculated numbers; being concerned with the intricacies of fabrics and batches; and repeatedly testing and retesting garments.
Employers that use and comply with OSHA and ASTM standards and NFPA 70E help to create a safe working environment. Employees who adhere to the safety rules do the same. Rather than overcomplicating arc-rated PPE decisions, our time is better invested in safety through design to minimize the likelihood of an arc event. All risk-based decisions should be driven by an understanding that variability is embedded in every aspect of electrical arc flash protection.
About the Authors: Zarheer Jooma, P.E., is a partner at e-Hazard (https://e-hazard.com). He has convened and chaired arc flash safety standards and is a member of both ASTM F18 and IEC TC 78. Jooma performs electrical network design, arc flash studies, electrical safety training, incident investigations and auditing. He is the technical paper review chair for two IEEE journals and chair for the IEEE Electrical Safety Workshop 2025.
Brian Shiels is the service line manager for the ArcWear (https://arcwear.com) division of Kinectrics and a leading expert in the testing and development of arc-rated clothing. His professional experience includes quality management as well as the development and testing of thermal protective clothing and equipment. Among other responsibilities, Shiels is a longstanding member of a variety of standards development organizations, including ASTM, NFPA, AATCC and ISO. He earned his master’s degree in textile chemistry from North Carolina State University, with a special focus on protective clothing.
Stacy Klausing, M.S., is a senior project manager at ArcWear. Her professional experience includes project management in testing laboratories, testing and evaluating fabric related to PPE, and execution and management of an ISO 17025-accredited quality system. She earned her master’s degree from the University of Kentucky and is a Six Sigma Green Belt from North Carolina State University.
From Risk to Reliability: Improving Rope Safety in Energized Environments
The tools and equipment employed by electrical workers must possess the necessary insulating properties to ensure user safety. One such tool, dielectric rope, can be overlooked as a component of electrical safety, but modern standards and rigorous testing protocols are transforming the way this type of rope is designed, used and maintained.
The transition from use of traditional synthetic ropes (e.g., double-braided polyester or polypropylene with wax or overlay finishes) – which can absorb contaminants and moisture, thereby significantly reducing their insulating properties – to dielectric ropes represents a paradigm shift in safety. Just as hot sticks, fiberglass-reinforced plastic (FRP) tools and arc-rated PPE are subjected to strict maintenance and testing protocols, dielectric ropes must be treated with the same level of scrutiny and care. These ropes are increasingly being used as FRP tool replacements as they can offer lower weight and cost as well as greater flexibility in length and load-bearing capacity.
The remainder of this article will explore relevant global safety standards, the growing industry shift toward insulating rope with verified dielectric properties, and proper maintenance and handling practices to help ensure long-term dielectric rope safety in high-voltage environments.
Key Global Standards
Dielectric rope must undergo rigorous testing to confirm its ability to withstand high voltages, resist contamination and maintain insulating properties over time. These standards outline the requirements for dielectric tools and equipment, including rope:
- IEC 62192:2009: “Live working – Insulating ropes”
- ASTM F1701-12: “Standard Specification for Unused Rope with Special Electrical Properties”
- IEEE 516-2021: “IEEE Guide for Maintenance Methods on Energized Power Lines”
- NFPA 70E and CSA Z462 (arc flash standards)
Misleading Claims and Real-World Testing
For decades, standard synthetic ropes have been assumed to be nonconductive based on their material composition. Real-world testing, however, has demonstrated that these traditional ropes can absorb moisture, dirt and other contaminants, turning them into potential electrical conductors.
Further, lack of awareness and regulation in this area has resulted in the following:
- False marketing of some ropes, claiming that they are dielectric or insulating even though they have never been rigorously tested.
- Erroneous assumptions that test results from one diameter of dielectric rope apply to every diameter.
- Exposure of traditional ropes to water, mud and oil, compromising their insulating properties.
- Dielectric ropes being treated, handled, maintained, tested and inspected differently than hot sticks and FRP tools.
Dielectric Ropes as Part of an Electrical Safety System
A true dielectric rope is designed, tested and maintained like other insulating tools. This means:
- As with any tool used in energized or potentially energized environments, a dielectric rope should be routinely tested in dry and wet conditions to validate its insulating properties and fitness for use.
- All rope must be properly stored, cleaned and handled to prevent contamination.
- It is critical to perform a visual and electrical inspection of individual ropes prior to each use.
- Electrical workers must be trained to recognize the risks of using non-dielectric or contaminated ropes.
Industry Adoption: 6 Common Barriers
As dielectric rope technology advances and global standards become more defined, a growing number of utilities and contractors are adopting these ropes as part of their high-voltage operations. Yet industry-wide adoption continues to be slowed by six common barriers.
1. Resistance to change. Some safety managers and field supervisors still operate under the belief that conventional synthetic ropes are good enough, largely because serious incidents involving conductive ropes are rare or undocumented. This perspective overlooks the risks to human safety posed by contamination and environmental degradation of synthetic rope. In other words, just because a rope has not failed yet does not necessarily mean it is safe to use.
2. “We work de-energized, so we do not need dielectric rope.” OK, but what about the risks of induction and accidental re-energization from lightning strikes and switching errors? In several documented instances, ropes were accidentally energized during what was thought to be de-energized work. Utility customers who use improperly installed generators during power outages can unintentionally cause reenergization unbeknownst to the utility. The best approach is to treat all systems as potentially energized and use the safest possible ropes and other tools for the job at hand.
3. “We work in a mostly dry climate, and we never work when it rains, so we do not need to test our dielectric ropes in wet conditions.” Wet testing is the only way to identify tool contamination during periodic testing. Additionally, tools that perform well under wet testing conditions can offer greater protection against poor storage conditions, not just high humidity and rain events.
4. Incorrect assumptions about new technology. Employers and employees might assume that utilizing dielectric ropes requires special tools, training or operational changes. This misconception can lead to the false belief that dielectric ropes are niche products rather than necessary tools for hazardous, everyday tasks. In reality, numerous dielectric ropes are engineered for compatibility with standard hardware and work practices while offering enhanced safety margins.
5. Financial hurdles and reactive safety cultures. High-performance dielectric ropes are often more expensive than standard ropes, especially when testing and inspection are factored in. Initial cost sensitivity could preclude employers from fully considering the potential human, legal and other costs should a rope-related failure occur on the job. While some companies use serious accidents or near-misses as catalysts for change, today’s high-performing organizations are embracing preventive investment.
6. Administrative complexity. The prospect of navigating new standards can be daunting. Procurement and safety officers may feel burdened by the process of incorporating new specifications. But the fact is that today’s dielectric rope standards align well with existing safety frameworks used for FRP tools, insulating gloves and arc flash PPE.
Best Practices for Use and Maintenance
Whether your organization is already using dielectric ropes or still investigating their safety benefits, here are the best practices users and potential users should be aware of. In addition, always be sure to review and adhere to rope manufacturer instructions and guidelines.
1. Verify compliance with recognized standards.
- Ensure dielectric ropes fully comply with local governing standards and/or regulations.
- Request test reports and certification from rope suppliers that confirm lot traceability and leakage current performance.
2. Store and maintain ropes like other insulating tools.
- Recondition dielectric ropes after use by placing them in a clean, well-ventilated, low-humidity room or trailer, avoiding exposure to contaminants.
- Thoroughly inspect, clean and test each rope between uses.
- Transport ropes in sealed containers or protective bags.
3. Inspect ropes before each use.
- Visually inspect dielectric ropes for cuts, abrasions and dirt buildup. Damaged ropes must not be used.
- Perform periodic dielectric testing to ensure continued insulation.
4. Train workers.
- Educate crews about the risks of using non-dielectric ropes near energized or potentially energized systems.
- Provide workers with training on the specific dielectric ropes they will use, including handling protocols, which should be similar to those for hot sticks and FRP tools.
Conclusion
Assumptions that traditional synthetic ropes are nonconductive have been proven incorrect. Today, the electric utility industry is shifting toward the use of tested, standardized dielectric ropes. By adopting globally recognized standards, training employees on proper maintenance procedures and treating dielectric ropes as critical equipment, organizations can better prevent incidents, injuries and near-misses on their worksites.
About the Author: Patrick Barry is the vice president of commercial operations for Barry Cordage Ltd. He has 12 years of experience in the rope industry, with a specialized focus on utility and helicopter operations. Professionally certified by the Industrial Rope Access Trade Association, Barry has delivered global best practices training to operators in the commercial and military sectors. Recently, he has been a guest presenter for the EPRI Live Working Task Force and numerous public utilities, sharing insights on dielectric safety and innovative rigging solutions.
Built In, Not Bolted On: Using Safety to Drive Operational Excellence
Employers in the electric utility industry are currently working on initiatives in various areas of their businesses, including safety, quality, production, leadership, and human and organizational performance (HOP). These are important programs, but it’s unlikely they’ll fully achieve their intended objectives if employees don’t have a firm grasp on how these various aspects of work impact one another – and the ideal order in which they should be addressed.
As someone who has spent a great deal of time studying HOP and teaching its principles to others, I understand that part of the philosophy is building an organizational system that enables employees to complete their work using processes that make sense to them, are easy to follow and can be done by virtually anyone with the appropriate skill set.
It’s important to recognize, however, that safety should be the first consideration in any work we do and any initiative we develop and roll out. Additionally, safety-motivated workers are more likely to ensure adherence to organizational system protocols when there’s someone or something at stake for them, whomever or whatever that might be.
Examining Safety Culture
Here’s a personal story to help you better understand where I’m going with this.
Years ago, I was asked to attend some lean training, which centered on continuous organizational improvement to minimize waste and maximize efficiency or value. The lean philosophy places a great amount of emphasis on standardization, production and quality.
I consider myself a safety culture champion who primarily concentrates on the human aspect of safety, including motivating people to see the value in doing the right things for the right reasons. When employees are effectively motivated, safety becomes much more than basic compliance to avoid trouble with regulators, safety leaders and your direct supervisor. Compliance should never be the only thing your workforce focuses on; instead, strive for continuous improvement.
Consider a lineman’s PPE, for example. The type and rating of the gear to be used must be determined by the hazards the lineman could be exposed to in the work area. Typically, we strictly adhere to PPE protocols when we know we’re being observed in the field, but that’s not necessarily the case every day. If a worker sometimes dons the incorrect PPE or improperly wears the right equipment, or if another employee must tell them to use it, that’s an indication the worker does not see PPE’s value. A worker who does see the value will ensure they’re correctly wearing the right gear based on their hazard exposure.
Essentially, an employer can create the best work rules, policies and procedures the world has to offer, but to truly have a shot at being effective, they must be easy for employees to understand and follow. When no one is around to observe field employees, peer-to-peer support will be the voice of leadership. Will your workers make the right choices?
Speaking Up for Safety
So, why am I telling you all this? Because I want you to understand that an organization must create this type of culture on some level to successfully move forward in addressing quality, production and other aspects of the business.
That brings us back to the lean training story I’d started to share. The trainer was a former Toyota employee who spoke in part about establishing standards to improve production, which he said would improve quality. I asked him where safety fit into the process, to which he replied, “You must be one of the safety people who I was told would be in this training. I want you to know that safety is a given for this process, not for the individual parts.” In other words, according to the trainer, safety protocols are required to comply with rules and regulations, but they have no effect on production or quality outcomes.
That was an interesting statement. But then things got really interesting.
Seeing the conversation as an opportunity to appeal to everyone in the room, I stood up and asked various other trainees to tell me who or what they valued most in life. The majority said they cared most about their families, pets or free time away from work. These responses helped to underscore the point I wanted to make.
Next, I asked everyone to imagine building a child’s bicycle, perhaps as a birthday gift. The child would ride the bike to school and pedal around their neighborhood, so I explained that we’d want to carefully assemble it to minimize the risks of breakdowns and injuries, particularly when the child would be riding in areas with vehicle traffic. Caring about someone, I said, means you want to ensure their continued safety. Because you care about the child whose bike you’re building, it’s highly likely that you’ll follow the assembly directions (rules) so that the bike works properly or fails safely (quality) when the child is riding it (productivity). In short, I told the class that making safety a true organizational value – not just a priority – will motivate employees to adhere to standards, build with quality and be more productive.
The room was silent when I finished speaking and sat down. I knew it might appear that I was giving the training instructor a hard time, but that wasn’t my intent. I wanted to help him understand that in terms of achieving common organizational goals, it’s significantly more impactful to view and approach the various aspects of business operations – including safety – as one entire interrelated group or system rather than in silos.
As I fielded some of the instructor’s questions, I could feel senior leaders in the room beginning to understand my point. They began discussing the potential development of a system to help the workforce understand each aspect of the business and what’s needed to continuously improve operations.
Again, as I noted earlier, part of the HOP philosophy is creating an organizational system that enables employees to complete their work using specific processes. By creating clear policies and procedures that are easy to follow, workers who see their value will likely abide by them – even when no one is watching.
Conclusion
Have you ever wondered why we can always find time to do a job over again but never time to do it correctly the first time around? What I’ve presented in this article can help organizations conduct safer, more efficient operations without having to do rework.
Here’s one final thought: HOP is about learning and improving, not blaming others or mandating retraining every time a failure occurs. Keep in mind that learning from success is just as important as learning from failure, if not more so; after all, we succeed far more often than we fail. When we discuss our successes – always being sure to include the people closest to the work – our conversations tend to be more positive and productive, empowering us to better identify improvement opportunities when evaluating safety, standards, quality and productivity each day. Let’s challenge ourselves to continue finding ways to improve business operations for the greater good of the entire workforce.
About the Author: Doug Hill, CUSP, is a retired lineworker and safety culture champion with nearly 40 years of utility industry experience. For the last 12 years, he’s represented the Michigan State Utility Workers Council in electric operations safety. Among other activities, Hill currently delivers training through the Incident Prevention Institute. Reach him at doug@utilitybusinessmedia.com.
Safety By Design: Safety Management System Planning
In the first two parts of this six-part series, I discussed the importance of creating and implementing a safety management system (SMS) that actively involves all employees. This part will focus on (1) identifying and prioritizing an organization’s safety needs based on specific hazards and risks and (2) developing a plan with clear objectives and targets to meet those needs. Without a solid plan, it’s difficult to assess whether the SMS is effective and adds value to your organization.
Early in my career, I didn’t fully grasp the significance of having a safety plan. I often experimented with new safety trends without understanding what the organization I worked for would gain from them or how success would be measured. Much like a New Year’s resolution, proclaiming you are going to create positive change in the workplace is far less challenging than designing and executing a plan to hold yourself accountable, measure your progress and adjust when things aren’t going well. Many New Year’s resolutions fail due to lack of measurable plans; the same is true with safety.
ANSI/ASSP Z10-2019, “Occupational Health and Safety Management Systems,” defines “planning” as identifying and prioritizing safety issues, establishing goals and objectives for improvement, and creating implementation plans with resource allocation. The planning process consists of four main steps:
- Identifying occupational health and safety (OHS) issues within the organization, including hazards, risks, system deficiencies and improvement opportunities.
- Prioritizing identified OHS issues based on their importance to the employer.
- Establishing OHS objectives to improve the effectiveness of safety initiatives and reduce risk.
- Creating an OHS implementation plan that specifies tasks and responsibilities to meet those objectives.
Identifying OHS Issues
A thorough assessment of your organization’s current safety performance is needed to uncover any gaps that require attention. This means identifying the resources and protocols in place, considering whether there are missing OHS elements that could enhance employee safety, and evaluating which initiatives will foster a safer work environment. These insights will help you make more informed decisions to better protect your workforce.
Lagging Indicators
Some organizations look to the absence of injuries and illnesses to measure their safety performance. However, OSHA recordable and lost-time rate charts (i.e., lagging indicators) will not directly correlate past performance to future outcomes. Further, when lagging indicators are used in meetings to illustrate an organization’s level of safety success, it can be tough to secure senior leader buy-in for required safety processes and initiatives. That’s because lagging indicators are weak metrics that shouldn’t be used as an organization’s only safety performance measure.
In my role as a consultant, I’ve encountered employers with thousands of man-hours and no lost-time incidents. Yet after completing field observations that included employee engagement, I’ve often been amazed that injuries and fatalities hadn’t occurred given the number of missing or misaligned safety initiatives that supported high-risk work. We must acknowledge that sometimes we’re simply lucky when nothing goes wrong – and we all know luck runs out eventually.
Safety Gap Analysis
Conducting a safety gap analysis is the first step in assessing an organization’s current state of safety. This systematic review compares existing safety measures and practices to desired or required standards, with the goal of identifying both gaps in the current system and opportunities for improvement. I recommend these resources to assist employers in the development of a gap analysis protocol that’s based on industry best practices:
- ASSP GM-Z10.100-2024, “Guidance and Implementation Manual for ANSI/ASSP Z10-2019 Occupational Health and Safety Management Systems.”
- ASSP GM-Z10.101-2019, “Guidance Manual: Keep Your People Safe in Smaller Organizations.”
An important part of the safety gap analysis is evaluating what I call the “look of safety,” which involves strategically identifying hazards, assessing their risk levels and implementing appropriate controls. Because hazards in electric power systems present great risk, they must be recognized based on the actual work performed rather than just planned or theoretical work. According to ASSP GM-Z10.100-2024, many organizations overlook that hazards are not static; rather, they’re dynamic and constantly changing. To identify gaps in any safety processes that were developed solely based on planned or theoretical work, it’s crucial to conduct field observations and maintain open communication with employees.
Understanding how work is performed in the field allows organizations to gain deeper insights into employees’ daily challenges, which can lead to innovations that enhance operational success. In the second part of this series, I explained how middle managers can hinder safety initiatives. These managers play a crucial role in understanding how work is planned versus how it is executed, as well as how employees’ decisions impact their work. Often, middle managers develop job plans based on a limited perspective that can become skewed if they don’t regularly visit job sites to observe work practices. This should be carefully considered during any safety gap analysis.
Prioritizing OHS Issues
Once gaps have been identified, they may indicate the need for changes in culture, resources, leadership styles, behaviors, systems and equipment, or other areas. To facilitate meaningful improvement, employees at all levels of the company must openly and honestly address the analysis results. One of my ongoing recommendations is to initially focus on operational improvement opportunities that will provide the greatest rewards in terms of risk mitigation.
Recently, while presenting the results of a gap analysis, a senior leader asked me, “Are we doing anything right?” The identification of safety gaps calls attention to organizational weaknesses. Acknowledging these weaknesses can feel challenging to leaders, yet doing so is essential to accurately assess risk levels. Senior leaders must define the organization’s risk tolerance and work with middle managers to develop implementation plans for operational improvements.
Systems Thinking
It’s also crucial to adopt a systems-thinking approach when prioritizing safety issues. This is a more comprehensive, effective way to manage risks as it focuses on how various system components interact with and influence one another to create a safe environment. The approach involves looking at the big picture, recognizing complex relationships and learning how decisions made in one part of the system can impact other system parts. Applying this approach can address operational challenges that don’t adequately support employee safety, helping to resolve numerous OHS issues.
Establishing OHS Objectives
Setting objectives that are specific, measurable, actionable, realistic and time-oriented (SMART) is an essential, powerful practice to improve organizational safety. Improvement occurs when company leaders track, monitor and evaluate these objectives. Chapter 8 of ASSP GM-Z10.100-2024 provides an excellent example of how to use SMART objectives when planning and setting goals.
Leading indicators promote ongoing improvement by highlighting deficiencies in the SMS and prompting necessary adjustments. Key performance indicators (KPIs), emphasized throughout this series, should be considered one of the most important elements of an effective SMS. KPIs are leading indicators that enable an organization to identify, measure and address issues within the OHS objectives before a significant injury or illness can occur. By monitoring KPIs and other leading indicators, organizations can uncover and correct weaknesses in procedures and unsafe employee behaviors before harm can happen.
Overall, tracking and addressing leading indicators is needed to create a safer work environment and enhance organizational effectiveness. Chapter 17 of ASSP GM-Z10.100-2024, “Metrics and Measurements,” is a good resource to learn more about using them.
Creating an OHS Implementation Plan
An OHS implementation plan outlines an organization’s strategy and process to create and maintain a safe work environment. Once SMART objectives have been established, the implementation plan should cover the following aspects at a minimum: strategy; communication of the plan; implementation of each objective; a timeline; an accountability process; assigned KPIs; and a method for tracking continuous improvement. Regularly evaluating and improving the plan is key to ensuring its effectiveness.
Summary
An effective SMS begins with a solid foundation: planning. Organizations must first perform a gap analysis to understand their current state of safety; then prioritize OHS issues based on risk; and finally establish realistic improvement objectives and an implementation plan supported by strong leadership and systems thinking.
Lagging indicators alone are insufficient to measure safety performance. Instead, leading indicators and continuous monitoring of key performance metrics should drive safety decisions. Implementation plans must be strategic, measurable, and integrated into the organization’s culture and operations.
Ultimately, achieving safety excellence requires more than regulatory compliance. With thoughtful planning and a commitment to continuous improvement, organizations can develop safer, more resilient work environments.
About the Author: Pam Tompkins, CUSP, CSP, is president and CEO of SET Solutions LLC. She is a 40-year veteran of the electric utility industry, a founding member of the Utility Safety & Ops Leadership Network and past chair of the USOLN executive board. Tompkins worked in the utility industry for over 20 years and has provided electric power safety consulting for the last 20-plus years. An OSHA-authorized instructor, she has supported utilities, contractors and other organizations operating electric power systems in designing and maintaining safety improvement methods and strategies for organizational excellence.
OSHA-Compliant Employee Training
“Yes, we are OSHA compliant. Our apprentice lineworkers are trained and certified by a local line school, which guarantees that the training they deliver meets OSHA standards. Every six months, we send the apprentices to the school for two weeks of hands-on training. They also take online classes in between the hands-on sessions; the online classes are delivered via a learning management system (LMS) operated by the school. It takes two years for an apprentice to complete the program. If the apprentice passes the written and practical exams delivered through the LMS, the line school then certifies them.”
Before I go any further, I want to clarify my position. I support line schools and third-party training providers – in fact, I am a training provider. I have been a third-party resource for many years, training in every area of lineworker skills. A problem arises, however, when employers assume their third-party training resource is responsible for all aspects of employee training and certification.
If you think the scenario described in the first paragraph sounds like a reasonable way to provide quality training to apprentices, you are not alone. The reason many employers use third-party trainers is twofold: they don’t see training as their core business, and they lack the resources to create robust training programs.
There is nothing wrong with using a third-party resource to provide training for your personnel. But it’s important to keep in mind that although a third-party resource may have flashy advertisements and an impressive sales pitch, that doesn’t guarantee they will provide competent training – and OSHA knows that. That’s why the agency states the following in 29 CFR 1910.269(a)(2)(viii): “The employer shall ensure that each employee has demonstrated proficiency in the work practices involved before that employee is considered as having completed the training required …”
True Training or Checking the Box?
I typically categorize training as either the check-the-box variety or true training. Some employers, lacking resources to adequately deliver training, hire a third party to relieve themselves of that obligation. Check-the-box training leaves all the training solely up to the third party. The employer then believes their employees are certified, with the paperwork to prove it. Often, the issue is that because the third-party organization has stated that it is a professional lineworker training provider, the employer assumes the organization is competent to train their employees.
There’s another, more obvious reason to question third-party training, especially when you consider the scenario in this article’s opening paragraph. In that two-year scenario, an apprentice would only receive 640 hours of actual training; traditional line apprenticeships consist of 7,000 to 8,000 hours of on-the-job training. Here’s something else to know: With traditional apprenticeships, the employer documents an apprentice’s performance in the workplace, thereby meeting OSHA’s requirement to ensure demonstrated skills proficiency.
At this point, you may be asking why completing a third-party line school’s training doesn’t equate to demonstrated proficiency. It’s because OSHA holds the employer singularly responsible for the welfare of the worker – not the third party. The agency does not want to create an accountability issue by allowing the employer to transfer their responsibility to an unaccountable entity. OSHA cannot cite a training organization because that organization is not the employer.
OSHA’s intent is to ensure that the employer verifies employee skills via the demonstration model even when utilizing a third-party training resource. In joint apprenticeship training programs, each apprentice carries a skills record with them; a qualified person, designated by the employer, observes the apprentice and signs their record. Weekend schools at joint apprenticeship yards provide third-party training. Often, those yard trainers and supervisors are employed by the same organization as the apprentices. Observing skills demonstrations under such conditions meets OSHA’s requirements. Skills learned at the weekend school are also demonstrated on the job and logged in the apprentice’s training record.
The same would apply to an apprentice sent to a line school for two weeks every six months. Upon the apprentice’s return, crew members would document demonstration of the skills training received at school in the apprentice’s skills record. Verifying a skills demonstration doesn’t have to happen right away; it can take place anytime in the six-month period before the next training session begins.
I want to make another clarification here: OSHA does not regulate technical skills proficiency. The agency regulates safety relative to those skills. They don’t care if the single-phase transformer you hang on a pole is crooked – only that you don’t injure yourself or someone else while hanging it.
Certification
Now let’s talk about certification. In my work as a trainer, I offer certificates to trainees who successfully complete their sessions; these documents certify their participation. But the standard upon which a certification is based can be problematic. To earn any certification, specific criteria must exist for a candidate to satisfy. When OSHA requests an employee’s training records, the agency is holding the employer accountable for certifying that the employee was qualified to perform the tasks assigned to them.
The power-line industry has been trying to establish a universal training certification standard for decades, but that hasn’t happened yet. Each one of the many training schools and apprenticeships across the U.S. develops its own outline of skills that trainees must learn and successfully demonstrate before they can be considered a lineworker, substation or meter tech, or any other skilled craft worker. Five different trainers in five different parts of the country will create five different lists of these skills. The U.S. Department of Labor publishes skilled craft standards, but none of them are for lineworkers – which is why OSHA very clearly instructs employers to ensure that their employees are trained and qualified to safely perform their assigned tasks.
An Ethical Duty
How does the OSHA regulation regarding employee qualification affect employers that aren’t under the agency’s jurisdiction? Employers have an ethical duty to protect employees. No one in any company wants to see an employee hurt or killed on the job. We protect employees by training and informing them about the skills they need and the workplace hazards to be avoided. We also acknowledge that under workers’ compensation laws, the employer has strong liability protections known as the “workers’ compensation bar.” But in every state to different degrees, that bar can be overcome where an employer did not meet the degree of care due to the worker. So, even if an employer doesn’t fall under OSHA’s jurisdiction, they still must protect themselves against civil actions by maintaining a robust training program that meets conventional or common utility standards. If you are an employer under OSHA’s jurisdiction, you also must be able to defend your training program to avoid the costly fines levied by the agency for noncompliance.
Note that non-OSHA municipal employers are subject to the National Electrical Safety Code, also known by its standard number, IEEE/ANSI C2. Here’s the C2 standard for a qualified person: “Having been trained in and having demonstrated adequate knowledge of the installation, construction, or operation of lines and equipment and the hazards involved, including identification of and exposure to electric supply and communication lines and equipment in or near the workplace.”
The ANSI C2 and OSHA standards are aligned and have identical requirements for personnel training based on training outcomes.
I’ve spent 50 years working in this industry and currently serve as a work methods and training consultant who’s been defending employers as a litigation expert for 20 years. Employers in our industry must have policies and procedures in place that align with OSHA’s qualified worker requirements. Each employer also must be able to defend its interpretation of those requirements. Many can’t do it. This is something I come across in almost every OSHA and civil litigation case I work on. Whether it’s General Industry (1910.269) or Construction (1926 Subpart V), the requirements are the same. If an employer assumes a journeyman’s ticket is proof of qualification, they have made a mistake. The employer’s duty is not met by third-party certification alone under the employee qualifications standard. Look closely at the wording from both OSHA and ANSI C2 and you will find the phrase “demonstrated proficiency.” OSHA has consistently ruled that “demonstrated” means the employer must create a program in which employees are observed and measured against performance expectations specified by the employer where no such formal performance standard exists. OSHA’s most recent definition is from 2018 regarding crane operator qualification under 1926 Subpart CC, “Cranes and Derricks in Construction.”
Regarding qualification, OSHA wrote the following: “This rule continues to require operator training. It likewise clarifies and continues the employer duty to evaluate operators for their ability to safely use equipment. Just as an employee’s driver’s license does not guarantee the employee’s ability to drive all vehicles safely in all conditions an employer may require, crane-operator certification alone does not ensure that an operator has sufficient knowledge and skill to safely use all equipment. The record makes clear that employers need to evaluate operators and provide training when needed to ensure that they can safely operate cranes in a variety of circumstances. Similarly, and also consistent with many employers’ current practices, employer evaluation of a crane operator’s experience and competency with respect to the particular equipment assigned is essential to ensuring the safe operation of cranes on construction sites. This final rule accordingly continues the common-sense requirements that employers train operators and assess their competence and ability to work safely” (see www.osha.gov/laws-regs/federalregister/2018-11-09).
The Bottom Line
The employer must have a program that satisfies the requirement to ensure employees demonstrate the necessary skills to safely perform their work. It doesn’t matter who does the training; it can be delivered through a private line school, a joint apprenticeship program or an in-house program. If an employer chooses to hire a lineworker with previous certifications, the requirement is the same. The employer must either test or observe the new employee and ensure that they demonstrate the skills necessary to work safely. For employees who require training, the program must ensure that they are qualified to safely perform their tasks through a combination of training, verification and demonstration.
About the Author: After 25 years as a transmission-distribution lineman and foreman, Jim Vaughn, CUSP, has devoted the last 28 years to safety and training. A noted author, trainer and lecturer, he is a senior consultant for the Institute for Safety in Powerline Construction. He can be reached at jim@ispconline.com.
Bucket Truck Safety: OSHA Standards and Other Considerations
I receive numerous and varied questions about the safe use of bucket trucks in electric utility operations, so in this installment of “Voice of Experience,” I am going to share with you the OSHA standards you need to know as well as some things I have discovered during observations and audits of field crews.
First, it is important to recognize that there is a substantial difference between Class A barehand bucket trucks and the Class B trucks used in gloving distribution. Class A barehand trucks are used for precisely that type of work; to protect employees, OSHA requires grounding the vehicles using the best available ground (see OSHA 29 CFR 1910.269(p)(4)(iii)(C)). The boom is the insulating barrier between the bucket that is directly connected to the energized transmission voltage being worked on and any difference of potential. Before employees can use the equipment, a leakage test must be performed by measuring the intentional contact between the bucket and the energized conductors for five to eight minutes. Booms must be dielectrically tested at least once every 12 months in accordance with ANSI A92.2, “American National Standard for Vehicle-Mounted Elevating and Rotating Aerial Devices,” although some companies conduct more frequent tests. Note that hydraulic tool circuits and material-handling jibs must also be tested if they could contact energized conductors.
An employee inside a bucket is required by OSHA to wear fall protection equipment. The equipment must be rigged so that the employee cannot free-fall more than 6 feet nor contact any lower level if ejected from the bucket (see 1926.502(d)(16)).
Regulatory FAQs
I have seen photos on social media that fail to meet even the simple requirements I have mentioned so far. Because workforce safety depends on rule compliance, I have created the following list outlining the six OSHA bucket truck regulations that I am most frequently asked to discuss in my consulting work. It is critical for employers and employees to both understand and apply each of them as required.
1. OSHA 1910.67, “Vehicle-mounted elevating and rotating work platforms,” is the standard that details the agency’s rules concerning bucket trucks.
2. Per 1910.67(b)(2), “Aerial lifts may be ‘field modified’ for uses other than those intended by the manufacturer, provided the modification has been certified in writing by the manufacturer or by any other equivalent entity, such as a nationally recognized testing laboratory, to be in conformity with all applicable provisions of ANSI A92.2-1969 and this section, and to be at least as safe as the equipment was before modification.”
3. Per 1910.67(c)(2)(i), “Lift controls shall be tested each day prior to use to determine that such controls are in safe working condition.”
4. Per 1910.67(c)(2)(iv), “Employees shall always stand firmly on the floor of the basket, and shall not sit or climb on the edge of the basket or use planks, ladders, or other devices for a work position.”
5. Per 1910.67(c)(2)(viii), “An aerial lift truck may not be moved when the boom is elevated in a working position with men in the basket, except for equipment which is specifically designed for this type of operation in accordance with the provisions of paragraphs (b)(1) and (b)(2) of this section.”
6. Per 1910.67(c)(2)(xii), “Before moving an aerial lift for travel, the boom(s) shall be inspected to see that it is properly cradled and outriggers are in stowed position, except as provided in paragraph (c)(2)(viii) of this section.”
I still have pictures in my files of crews moving trucks without cradling the buckets, sometimes with workers still in those buckets. OSHA 1910.67(c)(2)(viii) specifically prohibits moving a truck when an employee is working in the basket, with limited exceptions. Paragraph 1910.67(b)(2) prohibits equipment owners and users from modifying a bucket, boom and/or truck without the manufacturer’s approval. In reality, many organizations have asked for and received manufacturer exemptions, resulting in revised policies that allow employees to ride in a bucket for short distances (e.g., pole to pole when reconductoring and clipping in a new conductor) provided that (1) booms are properly cradled; (2) the employee is facing the direction of travel; and (3) the vehicle operator maintains a slow, reasonable speed while observing the area for hazards.
Class B Trucks
Class B bucket trucks differ from Class A trucks in that, typically, the bucket is not intentionally connected to the energized distribution voltage being gloved. Most Class B buckets have an insulating liner that provides an extra layer of protection between the employee and any nearby energized parts. On its own, a fiberglass bucket offers very little protection from the surrounding primary voltage and energized parts. All energized equipment and/or conductors must be properly covered for the purposes of worker safety, including any potentially conductive parts of the bucket.
The booms and buckets on Class A and B trucks must be kept clean and dry to prevent tracking to the vehicle frame on the ground. All non-dielectric trucks, digger derricks, cranes and other equipment must be grounded according to 1910.269(p) and barricaded to protect employees from hazardous step and touch potentials. Booms and buckets should be cleaned and waxed according to manufacturer recommendations.
Insulating booms and buckets are common conversation topics during field interviews and crew discussions. Class B buckets do not insulate employees from electrical contacts; that is why we use rubber gloves and protective cover. Less experienced workers sometimes think that buckets undergo dielectric testing, but that is incorrect – only the booms are tested. So, any potentially conductive items in or on the bucket must be isolated from all energized parts; otherwise, employees risk accidental contact or an arc flash between two potentials.
It seems that it is becoming more common for lineworkers to hang metal tools and other objects over the exterior side of a bucket for their convenience. This is an unsafe practice that has resulted in many incidents, including contacts on primary distribution voltages. The best and safest practice is to ensure no conductive items are hanging outside the bucket when working in energized or potentially energized areas.
Often, Class B buckets are used by substation crews or transmission crews in high-induction areas in and around substations. Potential differences between an employee in a Class B bucket and the bus or equipment they are working on can pose issues. Extra-high-voltage substations in particular can be very uncomfortable – this is something I have heard from crews across the country. Two rarely used alternative methods exist that can balance these differences for workers standing in Class B buckets. In the first method, the worker stands on a ground mat and connects to the grounded bus. The second method involves using a connected system ground from the basket to the grounded bus.
Conclusion
I want to emphasize here that one of the most common contributing factors to bucket-related incidents is failure to properly cover all energized parts and conductors, including second points of contact and potential differences in the immediate work area.
Lastly, if you would like to review an example of an aerial device operating bulletin, please reach out to me at rainesafety@gmail.com. I will send you one that can be adapted to your company’s policies.
About the Author: Danny Raines, CUSP, is an author, an OSHA-authorized trainer, and a transmission and distribution safety consultant who retired from Georgia Power after 40 years of service and now operates Raines Utility Safety Solutions LLC.
Learn more from Danny Raines on the Utility Safety Podcast series. Listen now at https://utilitysafety.podbean.com!
June-July 2025 Q&A
Q: Can you direct us to information regarding “fuzzing” or “noisy tester” voltage detectors? We’ve heard that with noisy testers, there’s potential for both false negatives (no voltage is detected although it’s present) and false positives (voltage is indicated where none exists). We’ve also heard a noisy tester can be triggered by induction on a de-energized line, creating confusion in the field. Years ago, our company stated that noisy testers shouldn’t be used. We haven’t been able to find any justification as to why the company made this decision. Can you help us out?
A: There is backing for such a policy. IEEE 1048, “IEEE Guide for Protective Grounding of Power Lines,” is where you can find details on voltage detection methods. Noise or fuzzing has always been considered an unreliable practice by that standard, but it’s still widely used in distribution. In the 2003 edition of IEEE 1048, Chapter 8 stated that fuzzing or using noisy detection was unreliable under 69 kV. In IEEE 1048-2016, the most recent edition, detection methods are found in Chapter 7. The 2016 edition warns that noisy testers and fuzzing are considered unreliable, but it doesn’t cite any specific voltages compared to an electronic voltage detector (tic-tracer style), an indicating voltmeter or a phasing meter.
Q: Earlier versions of the OSHA standard included distances and locations for installing grounded travelers during conductor pulls in energized environments, such as crossing or running on the same structure as energized circuits. We’re a small utility that doesn’t build feeders very often, but we’re currently planning for a pull and can’t find that information. Would you be able to point us in the right direction?
A: In the agency’s 2014 final rule updating both 29 CFR 1910.269 and 1926 Subpart V, OSHA deleted many of the location and spacing requirements for grounded travelers. In Chapter 5 of IEEE 524-2016, “IEEE Guide for the Installation of Overhead Transmission Line Conductors,” you’ll find guidance on grounding and bonding traveling conductors to protect workers from step and touch potential; construction of tensioning and pulling site grids; and effective grounding along the length of the pull and at snubbing and splicing sites. The language you remember from OSHA’s pre-2014 standard can be found in paragraph 5.5.3.1 of IEEE 524-2016.
Q: What are the standards for dielectric testing of a bucket truck for line clearance? I can’t find any when I review ANSI A92.2. Also, when does an insulating insert need to be replaced?
A: Information about electrical testing of booms begins on page 42 of ANSI A92.2-2021, “American National Standard for Vehicle-Mounted Elevating and Rotating Aerial Devices.” AC testing is described in 5.4. Chassis insulation system (lower insert) testing is described in 5.4.2.4. There is no requirement to periodically replace the insert or “bucket liner,” as it’s referred to in the standard.
Like booms, liners are subject to periodic testing. Test intervals are established by the owner following the guidelines published in 8.2.2. The test procedure is found in 5.4.2.5. Replacement is required only if a liner is damaged or the leakage value exceeds the standard’s limits. A bucket liner that’s been in use and exposed to the sun for several years can chip away at the fold over the bucket lip.
By the way, liners are not mandated for Category B gloving buckets. Gloves and/or hot sticks are the primary forms of protection for workers in these buckets. According to design and use standards, a fiberglass bucket is not considered insulating because it is subject to environmental contamination hazards but cannot be periodically tested. A bucket can be considered insulating provided it is emersion tested like a liner per the A92.2 standard. Insulating rubber gloves that are periodically electrically tested, inspected and air tested before use, like hot sticks, are a worker’s primary means of protection. Use of a liner creates a secondary electrical barrier, just as the boom is a secondary barrier.
Q: Our substation work group members have a question about an open jumper for a clearance point. There’s a long-standing practice of fully removing a jumper (outside MAD) and calling it incomplete construction that doesn’t need a tag. But if the jumper were rolled back and mechanically secured, it would be considered a clearance point that requires a tag. Now, we do use “incomplete construction” for newly built and reworked substations when the conductor is missing or has been moved from the substation rack to the first pole out. OSHA 1910.269(m)(3)(ii) calls out switches, disconnectors, jumpers, taps and other means. We’ve interpreted this to mean that any jumper or tap – whether it’s completely removed or mechanically secured – requires a tag stating that employees are working/do not operate. Can you provide any further clarification?
A: You’re almost there. If the action to isolate/de-energize is for the safety of workers, the standard requires a do-not-operate tag. You referenced the correct rule – 1910.269(m)(3)(ii) – in your question.
As you also noted, the rule calls out switches, disconnectors, jumpers and taps, and then it requires the means to be inoperable. The standard does not differentiate between an untap and a tap-back or total removal.
Jumper removal may be interpreted by some as necessary to meet the “inoperable” requirement, but anyone who can disconnect a jumper is just as capable of installing one.
The rule requires tagging those means that have been made inoperable to indicate that employees are at work. The final step in the tagging process is to ensure that no one can replace a missing jumper, just as with removing a barrel. Tag for this unlikely – but not impossible – occurrence.
The bottom line is that an open, by any means, is created for the protection of workers and therefore requires a tag.
Q: How does OSHA use consensus standards during employer inspections?
A: Consensus standards are developed by industry groups. These groups form committees to perform research and formulate production, design, performance and functional standards for industry-specific equipment and procedures. In other words, group members reach a consensus about relevant information that they then publish. OSHA either adopts a consensus standard or references it in the agency’s standards. You can find the adopted General Industry standards at 1910.6 and those for Construction at 1926.6.
The purpose of adopted standards is found at 1910.6(a)(1)(i), where OSHA states that they “have the same force and effect as other standards in this part. Only the mandatory provisions (i.e., provisions containing the word ‘shall’ or other mandatory language) of standards incorporated by reference are adopted as standards under the Occupational Safety and Health Act.” This is easily understood.
It works a bit differently with Appendix G to 1910.269 and Appendix G to 1926 Subpart V, both titled “Reference Documents.” Although OSHA uses that title, the documents listed in these appendices are consensus standards that the agency has included as compliance tools for employers. As of the 2014 final rule, OSHA no longer uses adopted consensus standards in 1910.269 and 1926 Subpart V. Since they are no longer adopted, the consensus standards are not citable, nor do they hold the same weight as OSHA rules – but there is a good reason to know what they say. These standards contain procedural knowledge applied throughout the utility industry; as a result, there are certain responsibilities attached. Part of OSHA’s criteria for citations is evidence that an employer knew a hazard existed and that remediation was available. Frequently, reference standards inform OSHA’s decisions to issue General Duty Clause citations. If an employer uses an alternative procedure that protects the employee as well as a reference standard outlines, there is nothing to fear.
You are expected to follow the mandatory (“shall”) provisions of adopted consensus standards. You don’t have to meet the requirements of a reference document, but you should know what those requirements are. If you receive a General Duty Clause citation and there is no direct OSHA standard that applies, the citation will likely contain language from the related consensus standards.
Note that in Canada, provincial occupational health and safety (OHS) agencies may adopt various consensus standards – such as those from IEEE, ANSI, CSA and CAN/ULC – either entirely or in part. OHS authorities can enforce those adopted standards and issue citations based on them. They can also use reference documents to support their reasoning, but they can’t issue citations directly based on such materials.
Do you have a question regarding best practices, work procedures or other utility safety-related topics? If so, please send your inquiries directly to kwade@utilitybusinessmedia.com. Questions submitted are reviewed and answered by the iP editorial advisory board and other subject matter experts.
Prioritize Safety Now So It Becomes a Value Before It’s Too Late
We typically excel at safety – after an incident. My question is, can we get it right before an incident occurs? And if so, how? Keeping in mind that you probably learned a stove could be hot by touching one as a child, let’s consider another question: Is it possible for us to develop safety-related values or are we doomed to learn the hard way?
Take a look through the events and incidents listed below. Understanding why those individuals now use human and organizational performance (HOP) tools (e.g., checking; verification; say it out loud; event + response = outcome; step-by-step place-keeping) – even if they don’t know HOP terminology – may provide insight into how much they inherently value safety, work methods and procedures.
A man who takes a picture of his kitchen stove every morning … after almost burning down his house.
Most of us wearing safety glasses while trimming the grass … after that rock hit our face.
Trainers confirming building access and contact numbers … after getting stuck in the rain and having to play lost puppy to get in the door.
Most of us following the instructions when assembling a piece of furniture … after taking it apart and starting over.
Learning the rental car controls before leaving the rental lot parking space … after shifting into neutral on the interstate while trying to turn up the radio and driving in the dark when the automatic lights didn’t turn on.
A surgeon writing their initials on your left shoulder before surgery … after they operated on the wrong shoulder.
And here’s one more to consider: Parents who install covers on electrical outlets … before their first child is born.
The events and incidents listed above could lead us to conclude that we often learn things the hard way and that most safety lessons will be learned through undesired situations. Yet they could also help us understand that the events and incidents we learn from don’t have to involve serious injuries or fatalities and that caring makes us value safety.
Safety as a Core Value
Valuing safety means that it’s always important. Prioritizing safety means that it’s sometimes important; we add “but fors” and “except whens” to the standard for our comfort and convenience. For instance, most people will tell you it’s wrong to text and drive. They believe they value that standard. The problem is that if you ask them if they’ve ever texted while driving, they’ll say yes. “Don’t text and drive” becomes “Don’t text and drive but for emergencies or short messages” or “Don’t text and drive except when there is no other traffic and it’s a straight road.”
Parents, motivated by caring – which is defined in C5 safety leadership as preventing harm and encouraging growth – typically get it right. They anticipate hazards like sharp furniture corners and energized electrical outlets and acknowledge that their children will trip, stick their fingers in sockets and make other errors. That’s why they teach, train, coach and protect. The corners are cushioned and the outlets covered long before an incident happens, and often before the child is born.
Practicing HOP Tools
We can learn to care more about our own safety and the safety of our TEAM (Together Everyone Accomplishes More); that’s a topic for another time. We can also view errors as opportunities and use them to practice HOP tools that will serve us well.
Try this out sometime: Stop in your driveway, watch the garage door hit the ground and say, “Garage door down.” You’ll quickly learn that saying it out loud changes your cognition, giving the HOP tool value, and hopefully you’ll use it at work.
When you travel, develop a packing list that allows you to check off each item as it goes in the suitcase. You’ll quickly learn that checking and step-by-step place-keeping ensure success, giving the HOP tools value, and hopefully you’ll use them at work.
Before you send an important email, proofread it and then ask someone else to do the same. You’ll quickly learn that checking and verification ensure that conditions are correct before critical steps are performed, giving the HOP tools value, and hopefully you’ll use them at work.
The next time you feel rushed, stop and ask yourself why you’ll have time to do the work again but don’t have time to do it correctly right now. You’ll quickly learn E + R = O and that pausing between an event and your response to define your ideal outcome will lead to a better response, giving the HOP tool value, and hopefully you’ll use it at work.
The point is to practice HOP tools in low-risk environments. Practice doesn’t make perfect; perfect practice makes perfect, and if you don’t practice using these tools while performing simple tasks in simple situations, you won’t be able to use them effectively when they’re really needed.
Conclusion
You are going to learn about safety and how to use HOP tools that give you time to think, focus your attention and control your work. These are not choices. One choice you do have, however, is whether to learn about safety and HOP tools because you were involved in an incident or because you care enough to practice them.
I’ll close with this statement made by the CEO of a utility company when kicking off a recent Frontline training class: “We are going to make safety a value and will adjust our priorities to meet that value.” That’s something every utility organization should aspire to.
About the Author: David McPeak, CUSP, CIT, CHST, CSP, CSSM, is the director of professional development for Utility Business Media’s Incident Prevention Institute (https://ip-institute.com) and the author of “Frontline Leadership – The Hurdle” and “Frontline Incident Prevention – The Hurdle.” He has extensive experience and expertise in leadership, human performance, safety and operations. McPeak is passionate about personal and professional development and believes that intrapersonal and interpersonal skills are key to success. He also is an advanced certified practitioner in DISC, emotional intelligence, the Hartman Value Profile, learning styles and motivators.
About Frontline Fundamentals: Frontline Fundamentals topics are derived from the Incident Prevention Institute’s popular Frontline training program (https://frontlineutilityleader.com). Frontline covers critical knowledge, skills and abilities for utility leaders and aligns with the Certified Utility Safety Professional exam blueprint.
Webinar: Prioritize Safety Now
July 9, 2025, at 11 a.m. Eastern
Visit https://ip-institute.com/frontline-webinars/ for more information.
Utility Safety Podcast – Visual Intelligence for a Safer Grid: The Future of Utility Inspections
In this episode, Incident Prevention’s Kate Wade sits down with Kaitlyn Albertoli, co-founder and CEO of California-based Buzz Solutions, to explore how visual intelligence is helping utilities uncover hidden risks and modernize critical infrastructure. Kaitlyn shares how Buzz Solutions’ platforms—PowerAI and PowerGuard—use AI-driven insights to streamline inspections, enhance grid reliability, and reduce operational costs. They also discuss the challenges of adopting new technologies, bridging the field-office communication gap, and what utility safety professionals can expect in the next 5 to 10 years. This conversation is essential for those interested in data-driven decision-making, infrastructure safety, and the future of AI in the energy sector.
To reach Kaitlyn directly, email her at kaitlyn@buzzsolutions.com or connect via LinkedIn: www.linkedin.com/in/kaitlyn-claire-albertoli/
Key Takeaways:
-
Buzz Solutions uses AI-powered visual intelligence to help utilities identify risks and improve inspection accuracy.
-
Their platform PowerAI analyzes images from drones, helicopters, and field crews to prioritize maintenance and reduce operational costs.
-
Integration with GIS and asset management systems makes implementation efficient and less disruptive.
-
Buzz’s tools support storm prep, wildfire mitigation, and long-term grid modernization.
-
Education and communication are key to AI adoption across all levels of a utility organization.
Questions & Answers
Q1: What problem does Buzz Solutions aim to solve for utilities?
A: Buzz helps utilities manage and analyze vast visual datasets, allowing them to spot infrastructure issues early, prioritize repairs, and eliminate data silos.
Q2: How does PowerAI differ from general AI tools?
A: PowerAI is a purpose-built platform that uses machine learning for visual inspection analysis, making it highly specific to the utility industry’s unique needs.
Q3: What concerns do utilities have about AI adoption?
A: Many worry AI could replace jobs or be unreliable, but Buzz focuses on “visual intelligence” to support—not replace—field experts and improve safety decisions.
Q4: Can this technology help prevent wildfires or major outages?
A: Yes, by analyzing infrastructure degradation and identifying high-risk components early, utilities can proactively address threats before they escalate.
Q5: How can utilities ensure smooth adoption of Buzz’s solutions?
A: Success hinges on integrating into existing workflows, gaining buy-in from field users, and automating data flow into GIS and asset management systems.
Subscribe to Incident Prevention Magazine – https://incident-prevention.com/subscribe-now/
Register for the iP Utility Safety Conference & Expo – https://utilitysafetyconference.com/
#UtilitySafety #VisualIntelligence #GridModernization #AIinUtilities #UtilitySafetyPodcast #InfrastructureInnovation
Built In, Not Bolted On with Doug Hill, CUSP – Rethinking Job Briefs – Why the End of the Day Matters Most
In this episode of Built In, Not Bolted On, host Doug Hill challenges traditional thinking around job safety practices. He explores the effectiveness of pre-job briefs, mid-day check-ins, and post-job reviews, emphasizing how learning from experience—especially at the end of the day—can dramatically improve safety outcomes. Drawing inspiration from aviation and military after-action reviews, Doug outlines how three simple questions can spark a culture of continuous improvement and safer work environments.
✅ Key Takeaways
-
Pre-job briefs are essential—but post-job briefs may hold even more value in fostering continuous improvement.
-
A “mid-day check-in” helps adjust controls based on changing conditions like weather or job scope.
-
Successes should be analyzed as deeply as failures to uncover replicable best practices.
-
Three core post-job questions—What went well? What didn’t? What can we learn?—drive future safety improvements.
-
Brief, honest conversations at the end of the day can improve the next day’s job planning significantly.
Q1: Why is the post-job brief considered more valuable than the pre-job brief by aviation professionals?
A1: Because post-job briefs provide real-time insights and lessons learned from completed tasks, which shape better, more informed pre-job briefs the following day.
Q2: What are the three questions Doug recommends asking during a post-job brief?
A2: 1) What went well? 2) What didn’t go well? 3) What can we learn to improve for the future?
Subscribe to Incident Prevention Magazine – https://incident-prevention.com/subscribe-now/
Register for the iP Utility Safety Conference & Expo – https://utilitysafetyconference.com/
#UtilitySafety #SafetyCulture #AfterActionReview #WorkplaceSafety #JobBriefing #ContinuousImprovement
Utility Safety Podcast – Deep Dive – The Good Shepherd – Leading with Safety and Trust
In this episode, we explore what an ancient shepherding metaphor can teach us about modern safety leadership. Inspired by The Good Shepherd, an article written by David McPeak, CUSP, CIT, CHST, CSP, CSSM for Incident Prevention magazine, we unpack how the timeless relationship between shepherd and sheep mirrors the dynamic between safety leaders and their teams. Through the lens of the C5 Safety Leadership Model—Competence, Commitment, Caring, Courage, and Credibility—we break down what it truly takes to earn trust, lead effectively, and create a culture of protection and performance. Whether you’re guiding a crew or shaping safety policy, this episode will challenge you to reflect on your leadership response and deepen your impact.
Read the article: https://incident-prevention.com/blog/the-good-shepherd/
Key Takeaways:
-
The C5 Safety Leadership Model offers five foundational qualities: Competence, Commitment, Caring, Courage, and Credibility.
-
Leadership is not about authority—it’s about earned trust and interdependence, just like a shepherd and their flock.
-
Real courage in safety often shows up in small but meaningful moments, like speaking up or making difficult calls.
-
Caring is the heart of effective safety leadership—it fuels the other four C’s.
-
Credibility is fragile; it’s earned through consistent action, not job titles.
Questions and Answers:
Q: What does a shepherd-sheep analogy teach us about safety leadership?
A: It highlights the interdependent relationship between leaders and teams—just as sheep need guidance and protection, teams rely on leaders who are competent, committed, caring, courageous, and credible.
Q: What is the most important trait in the C5 model?
A: While all five are critical, the episode emphasizes that Caring sits at the center—without genuine care, the other traits lose their power.
Q: How can a leader build trust in their team?
A: By consistently demonstrating the five C5 traits. Trust is earned through action, particularly in how leaders respond to challenges, errors, and opportunities.
Q: Why is credibility considered the foundation of the C5 model?
A: Because without credibility, leadership influence breaks down. Teams follow leaders they trust, not just those with authority.
Subscribe to Incident Prevention Magazine – https://incident-prevention.com/subscribe-now/
Register for the iP Utility Safety Conference & Expo – https://utilitysafetyconference.com/
#SafetyLeadership #TrustAndSafety #UtilitySafety #C5Model #ServantLeadership #WorkplaceCulture
About the Author: David McPeak, CUSP, CIT, CHST, CSP, CSSM, is the director of professional development for Utility Business Media’s Incident Prevention Institute (https://ip-institute.com) and the author of “Frontline Leadership – The Hurdle” and “Frontline Incident Prevention – The Hurdle.” He has extensive experience and expertise in leadership, human performance, safety and operations. McPeak is passionate about personal and professional development and believes that intrapersonal and interpersonal skills are key to success. He also is an advanced certified practitioner in DISC, emotional intelligence, the Hartman Value Profile, learning styles and motivators.
About Frontline Fundamentals: Frontline Fundamentals topics are derived from the Incident Prevention Institute’s popular Frontline training program (https://frontlineutilityleader.com). Frontline covers critical knowledge, skills and abilities for utility leaders and aligns with the Certified Utility Safety Professional exam blueprint.
Vault Maintenance Dewatering System
Andax Industries has introduced the Vault Maintenance Dewatering System (VMDS), an innovative solution for sediment and water filtration. Designed for electric utility, construction, industrial and environmentally sensitive projects, the VMDS captures hydrocarbons and sedimentary contaminants with its oil-selective absorbent inner core, allowing clean, filtered water to pass through.
The VMDS is ideal for applications requiring both sediment control and oil spill management, helping to ensure compliance with environmental regulations by filtering water runoff and preventing pollutants from entering storm drains, rivers and other waterways.
Built with durable materials, the system is designed to withstand harsh industrial conditions. It connects seamlessly to a standard 2-inch cam lock discharge hose. The VMDS is user-friendly, low-maintenance and available in custom sizes to accommodate various discharge pipe dimensions. www.andax.com/vmds
Utility Safety Podcast – ⚡️Time for Change⚡️ with Brent Jeffries, Bill Martin CUSP, Kate Wade
April 16, 2024
In this episode of the Utility Safety Podcast we dive into the idea that now is the Time for Change!
We have with us Editor of iP Magazine, Kate Wade, Brent Jeffries from Bierer Meters & William Martin from Think Tank Project, LLC.
⚡️Time for Change⚡️ The solution to change is time. Allow: Time to consider the plan Time to share concerns Time to discuss options Time to fail safely
Subscribe to Incident Prevention Magazine – https://incident-prevention.com/subscribe-now/
Register for the iP Utility Safety Conference & Expo – https://utilitysafetyconference.com/
73 min. with Brent Jeffries, Bill Martin CUSP, Kate Wade
Train The Trainer 101 – What’s Missing in Your Training? by Jim Vaughn, CUSP
April 1, 2024
This podcast dives into a critical issue within the lineman industry: outdated training methods and their consequences. Veteran safety expert Jim Vaughn argues that traditional training methods, which often rely on the experience of veteran lineworkers, can miss crucial safety updates and best practices.
The episode explores how social media trends like “TikTok linemen” showcasing unsafe work practices expose these gaps in training. Vaughn emphasizes the importance of trainers staying current on industry standards and proper procedures to ensure the safety of future generations of lineworkers.
Read the article here – https://incident-prevention.com/blog/whats-missing-in-your-training/
Register for the iP Utility Safety Conference & Expo to hear Jim Vaughn speak – https://utilitysafetyconference.com/
Utility Safety Podcast – Your Electric Reality – Brent Jeffries, VP of Field Operations/Safety Instructor for Bierer Meters
March 15, 2024
This podcast is about electrical safety and building a strong line crew culture. The guest speaker, Brent Jefferies, discusses his experience training line workers and his efforts to improve safety in the industry. He has observed that there is a lack of teamwork and communication among line crews, which can lead to accidents.
He believes that line crews should be more like sports teams, where everyone has a common goal and works together to achieve it. He also believes that line workers should feel comfortable speaking up if they see something unsafe.
Here are the key points:
- Brent Jefferies trains line workers on electrical safety and tool usage.
- He observes that many crews lack teamwork and communication.
- Jefferies believes line crews should function more like sports teams.
- Line workers should feel empowered to stop work if they see something unsafe.
- The ultimate goal is for everyone to work as a linecrew/lineteam.
Reach out to Brent – brent@bierermeters.com
Check out ECOS – https://electriccultureofsafety.com/
Subscribe to Incident Prevention Magazine – https://incident-prevention.com/subscribe-now/
Register for the iP Utility Safety Conference & Expo – https://utilitysafetyconference.com/
51 min. with Brent Jeffries
Utility Safety Podcast – Learning about T&D Powerskills – Jerry Havens, COSS
February 19, 2024
We got to sit down with Jerry Havens from T&D Powerskills to discuss their new LMS 2.0 and learn about the history of T&D through current day and how the program has evolved.
You can reach Jerry to find out more at:
Email: jerry@tdpowerskills.com
Cell: 318-880-2259
Website: https://www.tdpowerskills.com/
Subscribe to Incident Prevention Magazine – https://incident-prevention.com/subscribe-now/
34 min. with Jerry Havens
Utility Safety Podcast – Diving into Everything Outrigger Pads with Eric Steiner from Bigfoot
January 30, 2024
Bigfoot Construction Equipment is a family-owned American manufacturer of outrigger pads, used to stabilize heavy equipment like cranes and concrete pumps. They offer both wood and composite pads, with custom sizes and capacities available. Their products are veteran-made and prioritize safety and strength.
Eric Steiner, the marketing director, discussed the company’s history, product range, and commitment to safety and sustainability. He also highlighted the challenges of raising awareness about the importance of outrigger pads and Bigfoot’s efforts to overcome them through collaboration with industry standards boards and educational initiatives. Overall, the podcast emphasizes the role of Bigfoot in ensuring safe and efficient operation of heavy machinery.
Visit Bigfoot here – https://outriggerpads.com/
Email Eric – erics@outriggerpads.com
Subscribe to Incident Prevention Magazine – https://incident-prevention.com/subscribe-now/
19 min. with Eric Steiner
iP Magazine – A Dive Behind the Pages with Managing Editor – Kate Wade
December 22, 2023
In today’s special episode we interview the managing editor of Incident Prevention Magazine, Kate Wade. Kate explains about our editorial board and some behind the scene exclusives. We go into a host of topics as we get to spend some time talking about what she sees as future trends in the utility industry and what changes she has seen in the industry over the last 15 years.
Interested in writing an article for iP Magazine?
Email: kwade@utilitybusinessmedia.com
Make sure to join us at the iP Utility Safety Conference & Expo coming in Orlando, FL
May 21-23, 2024
Register Here: https://utilitysafetyconference.com/
28 min. with Kate Wade
Special Episode: iP Utility Safety Conference – San Diego, CA Nov 7-9, 2023 – Are You Registered?
October 16, 2023
iP Utility Safety Conference & Expo – San Diego, CA
Are you registered for this premier utility safety conference? https://utilitysafetyconference.com/
NOVEMBER 7 – 9, 2023
TOWN AND COUNTRY RESORT – SAN DIEGO, CA
JOIN US FOR 3 DAYS OF EDUCATION, NETWORKING & PRODUCT DISCOVERY
The iP Utility Safety Conference & Expo brings together leading safety and operations minds from across the country for three days of education and networking. If you’re a utility safety or operations professional, this is a can’t-miss event. Come together to gain education, insight & knowledge that will help you and your organization achieve new levels of safety success. Register today to get your all-access pass to three jam-packed days of education, networking, product discovery and more!
Your all-access pass includes:
- Unlimited access to 3 days of keynote presentations, roundtables and educational sessions
- Bussed transportation to and from an exciting tour of San Diego Gas & Electric’s state-of-the-art training facility
- Complimentary transportation to and admission into a fun welcome reception including dinner and plenty of networking opportunities
- Complimentary breakfast at the kickoff keynote session
- Complimentary lunches all three days of the event
- Unlimited access to the Expo Hall
- Complimentary coffee, tea and pastries to start the second and third day of the event
Train the Trainer – Jim Vaughn, CUSP – Training Users on Aerial Lifts
August 14, 2023
Listen to Jim Vaughn, CUSP talk about his article in iP Magazine on Training Users on Aerial Lifts.
Read the article – https://incident-prevention.com/blog/training-users-of-aerial-lifts/
Subscribe to iP Magazine free – https://incident-prevention.com/subscribe-now/
Reach out to Jim – jim@ispconline.com Jim’s LinkedIn – https://www.linkedin.com/in/jimvaughncusp/
47 min. with Jim Vaughn.
Special Episode – USOLN Board Chair – Jeff Clemons, CUSP
May 23, 2023
In this special episode we talk with the USOLN Board Chair, Jeff Clemons. We discuss a host of topics including how the USOLN was formed, some USOLN member benefits, and about their coveted CUSP Program that is the only utility specific credential in the industry. Jeff is a wealth of knowledge and works for San Diego Gas & Electric!
Visit www.usoln.org to find out more!
24 min. with Jeff Clemons.
Special Episode – iP Utility Safety Conference & Expo Presents SafetyPalooza in Schaumburg, IL May 9-11, 2023
March 22, 2023
Register for the Conference Today – Click to Register
The iP Utility Safety Conference & Expo brings together leading safety and operations minds from across the country for three days of education and networking. If you’re a utility safety or operations professional, this is a can’t-miss event. Come together to gain education, insight & knowledge that will help you and your organization achieve new levels of safety success.
Download the Brochure – Click here
16 min. with Carla Housh and David McPeak, CUSP and Melissa Housh from Utility Business Media
Special Episode – Crash Analysis: A Personal Story – Jim Vaughn, CUSP
February 22, 2023
Jim Vaughn, CUSP tells us a powerful story of beating the odds by following your training. This powerful message Jim shares with the community really puts a focus on why we train, and how it can save lives.
Read Jim’s article in the December 2022/January 2023 issue of Incident Prevention Magazine .
10 min. with Jim Vaughn, CUSP
Special Edition – What’s New In Tools from the iP Utility Safety Conference & Expo Glendale, AZ 2022
January 5, 2023
The iP Utility Safety Conference & Expo brings together leading safety and operations minds from across the country for three days of education and networking. If you’re a utility safety or operations professional, this is a can’t-miss event. Come together to gain education, insight & knowledge that will help you and your organization achieve new levels of safety success. www.UtilitySafetyConference.com
JOIN US FOR 3 DAYS OF EDUCATION, NETWORKING & PRODUCT DISCOVERY.
Visit https://utilitysafetyconference.com/ to learn more.
25 min. with Kurt Moreland, Associate Publisher with Incident Prevention
Special CUSP Edition – Want To Be One? Ask One!
November 16, 2022
Learn from a current board member and active Certified Utility Safety Professional (CUSP) credential holder Rod Courtney, and the current CUSP Program Director Shawn Talbot talk about common questions about the credential and USOLN.
Visit www.usoln.org to learn more about becoming a CUSP.
23 min. with Rod Courtney, CUSP & CUSP Program Director Shawn Talbot, CAE
Special Episode: Discussing the new Utility Leadership Book ”Frontline Incident Prevention — The Hurdle” with Author David McPeak, CUSP
August 29, 2022
In this special episode, we sit down with the Director of Professional Development for the Incident Prevention Institute, David McPeak, to discuss his new second book, called Frontline Incident Prevention — The Hurdle. Listeners will learn all about why the book is such an impactful and insightful read for anybody who is a utility safety leader or aspiring leader!
If you’d like a copy of the book, you can get it today at Frontline Incident Prevention- The Hurdle
Contact David McPeak at david@utilitybusinessmedia.com
29 min. with David McPeak, CUSP
Special Episode: Talking Lineworker Training & Safety with Tim Vassios
December 15, 2021
Incident Prevention went to Indianola, Iowa to check out a brand new training facility that the Missouri Valley Line Constructors just built to help train tomorrow’s lineworkers on how to safely do the work. In this podcast, Tim Vassios tells us all about how the training process works and why safety is such a vital part of it.
20 min. with Tim Vassios
Special USOLN Episode: An Interview with the Very First CUSP All-Star, Denver DeWees from Farmington Electric
July 29, 2021
In this episode, we sat down to chat with Denver to learn more about the process of becoming a CUSP and how it has helped him achieve more in his career as a utility safety professional.
20 min. with Denver DeWees
Tailgate Topics Podcasts
Tailgate Topics – The Dangers of Distraction: Staying Focused in High-Risk Utility Work by Scott Perrin
In this episode of Tailgate Topics, host Rod Courtney is joined by Nick from Utility Business Media to discuss one of the biggest safety risks in the utility industry—distractions. Inspired by Scott Perrin’s article, The Dangers of Distraction: Staying Focused in a High-Risk Environment, this conversation dives into how mental drift, complacency, fatigue, and technology impact workplace safety.
Read the article: https://incident-prevention.com/blog/the-dangers-of-distraction-staying-focused-in-a-high-risk-environment/
From distraction-related vehicle accidents to the role of fatigue and stress in high-risk environments, this episode explores real-world examples and practical strategies for reducing workplace hazards. Tune in to learn how small changes in awareness and environment can help prevent serious injuries and fatalities in the utility industry.
Key Takeaways:
✔️ Distractions are unavoidable, but they can be managed.
✔️ Fatigue, complacency, and stress increase the risk of accidents.
✔️ Cell phones and modern technology are major workplace distractions.
✔️ Taking scheduled breaks and staying mindful can improve focus and safety.
✔️ Vehicle accidents due to distracted driving are a growing financial burden for utilities.
✔️ Simple steps, like identifying distractions and using hands-free devices, can help reduce risk.
Subscribe to Incident Prevention Magazine – https://incident-prevention.com/subscribe-now/
Register for the iP Utility Safety Conference & Expo – https://utilitysafetyconference.com/
#UtilitySafety #WorkplaceDistractions #SafetyCulture #HighRiskJobs #FatigueAwareness #ComplacencyKills #DistractionFreeWork #UtilityWorkers
Tailgate Topics – Power Restoration Triage and Delta Systems – William Martin, CUSP, RN, NRP, DIMM
August 25, 2023
In this episode of Tailgate Topics, Rod Courtney, CUSP interviews William Martin, CUSP, RN, NRP, DIMM ON his article in Incident Prevention Magazine titled “Power Restoration Triage and Delta Systems”
Important points in the article cover –
- The importance of triage in power restoration: Triage is a way of prioritizing outages so that the most critical ones can be restored first. This is important because it helps to minimize the impact of the storm on businesses, homes, and public safety.
- The different types of triage systems: There are a number of different triage systems that can be used for power restoration. The best system for a particular situation will depend on the factors involved, such as the size and complexity of the outage, the availability of resources, and the severity of the weather conditions.
- The unique challenges of triaging delta systems: Delta systems are more common in rural areas and small communities. They pose unique challenges for triaging because they can create low-voltage conditions that can damage customer equipment.
- The insights of experts in the field: We’ll hear from experts in the field of power restoration to get their insights on how to do triage effectively. This will include tips on how to prioritize outages, how to choose the right triage system, and how to deal with the unique challenges of delta systems.
About the Author: Bill Martin, CUSP, NRP, RN, DIMM, is the president and CEO of Think Tank Project LLC (www.thinkprojectllc.com). He has held previous roles as a lineman, line supervisor and safety director.
Read the article – https://incident-prevention.com/blog/power-restoration-triage-and-delta-systems/
Register for the iP Utility Safety Conference & Expo to hear Bill & Rod Courtney speak – https://utilitysafetyconference.com/
Tailgate Topics – Discuss Drug & Alcohol Awareness on the Job Site – Jesse Hardy, CSP, CIT, CUSP, PCC
June 13, 2023
In this episode Rod covers with Jesse a host of job site issues that relate to drugs and alcohol. This is a very great subject to review with your team and pay attention to on the job site.
You see, this isn’t a “they have a problem” sort of problem – it’s a “we have a problem” sort of problem. It’s the kind of problem that we need to talk about for the sake of you and your family, your company, our industry and our nation.
To share feedback about this podcast, reach out to Jesse Hardy at jessehardy@yahoo.com or our Host Rod Courtney at rod.courtney.usoln@gmail.com
View Jesse Hardy’s article here.
39 min. with Jesse Hardy, CSP, CIT, CUSP
Tailgate Topics -Strategies to Handle Workplace Conflict – Jesse Hardy, CSP, CIT, CUSP
February 7, 2023
Listen to our 2nd installment into our new series “Tailgate Topics hosted by Rod Courtney, CUSP” titled “Strategies to Handle Workplace Conflict” Written by Jesse Hardy, CSP, CIT, CUSP.
“Jack, the people issues are just getting to be too much,” the foreman said. “If it’s not the landowners and members of the public throwing fits and coming into the work zones, it’s our own people getting into conflicts. At best it’s a distraction that steals our focus, and at it’s worst it becomes violent.”
The superintendent replied to the foreman, “I hear you, Billy. Let’s come up with a plan on how to deal with this.”
Three Important Questions
In this month’s Tailgate, we’re going to review answers to three important questions related to workplace conflict and violence, and then we’ll look at how to deal with three areas of conflict in ways that lead to the best possible outcome based on the situation.
View Jesse Hardy’s article here.
33 min. with Jesse Hardy, CSP, CIT, CUSP
Tailgate Topics -Avoid Injuries While Lifting and Moving by Jesse Hardy
October 4, 2022
This new series hosted by Rod Courtney, CUSP will dive deeper into each article from our Incident Prevention Magazine’s section called “Tailgate Topics”. In this episode Rod interviews Jesse Hardy on avoiding injuries while lifting and moving in his Tailgate Topics article in the Aug/Sep issue of Incident Prevention Magazine.
View Jesse Hardy’s article here
17 min. with Jesse Hardy, CUSP
Voice of Experience Podcasts
Voice of Experience: Battling the Storm – Hurricane Season Lessons for Linemen with Danny Raines, CUSP
In this powerful episode of the Utility Safety Podcast: Voice of Experience, veteran lineman and safety consultant Danny Raines, CUSP, shares hard-earned lessons from decades of storm response—from Hurricane Katrina to ice storms in Georgia. With hurricane season in full swing, Danny offers real-world guidance on preparing for storm duty, understanding system hazards, and staying mentally and physically resilient in the face of chaos. Whether you’re a new lineworker heading out on your first storm or a seasoned pro, this episode delivers critical insights to keep you safe, sharp, and storm-ready.
Key Takeaways:
-
Preparation is Everything: Danny emphasizes the importance of personal checklists, including meds, hygiene, and weather-appropriate gear.
-
Test and Verify: Don’t assume equipment is de-energized—especially with the increase in generators, solar, and battery backups.
-
Mental & Physical Fatigue is Real: After 14–18 days, exhaustion sets in, increasing the chance of errors. Know your limits.
-
Find a Mentor: For new linemen, a trusted mentor can be a lifeline during complex storm work.
-
Storm Hazards Go Beyond Electricity: Environmental dangers like snakes, alligators, and aggressive customers add to the challenge.
3 Questions & Answers:
Q1: What’s one of the most overlooked parts of storm prep?
A: Personal medications. Many new crew members forget that pharmacies may be closed or destroyed post-storm, making it impossible to refill critical prescriptions.
Q2: Why is it so important to “test and verify”?
A: With so many modern power sources—from Honda generators to solar panels and battery storage—assumptions can be fatal. Always check for voltage, even on lines you think are isolated.
Q3: How long can a lineworker realistically stay sharp on storm duty?
A: According to Danny, the magic number is around 14–18 days. After that, physical fatigue and mental exhaustion dramatically increase the risk of mistakes and injuries.
You can read the current magazine at Incident Prevention Magazine.
Subscribe to Incident Prevention Magazine – https://incident-prevention.com/subscribe-now/
Register for the iP Utility Safety Conference & Expo – https://utilitysafetyconference.com/
The Voice of Experience with Danny Raines podcast is produced by the same team that publishes Incident Prevention. It delivers insights based on Danny’s regular column in the magazine, also called the Voice of Experience. To listen to more episodes of this podcast, as well as other podcasts we produce, visit https://incident-prevention.com/podcasts. You can reach Danny at rainesafety@gmail.com
Purchase Danny’s Book on Amazon – https://a.co/d/556LDvzc
#UtilitySafety #StormResponse #LinemanLife #HurricanePrep #ElectricalSafety #DannyRaines #CUSP #Lineworkers #StormWork
Voice of Experience – Checkup from the Neck Up: Preventing Utility Work Mistakes
In this episode of Voice of Experience, Danny Raines, CUSP discusses the critical importance of mental awareness and focus in utility work. Using real-life accident investigations, he explores why experienced professionals sometimes repeat dangerous mistakes and how a “checkup from the neck up” can prevent incidents. From miscommunication in substations to lack of hazard recognition, this episode is packed with insights to improve safety culture and accountability in the field.
Key Takeaways:
- The Importance of Mental Awareness: How small lapses in judgment can lead to catastrophic accidents.
- The Role of Dedicated Observers: Why having a second set of eyes can prevent mistakes.
- Lessons from Incident Investigations: Real-world case studies of preventable accidents.
- Following Procedures & Training: Why workers revert to unsafe practices despite training.
- Taking Accountability: Leadership’s role in enforcing safety and stopping unsafe work.
The Voice of Experience with Danny Raines podcast is produced by the same team that publishes Incident Prevention. It delivers insights based on Danny’s regular column in the magazine, also called the Voice of Experience. To listen to more episodes of this podcast, as well as other podcasts we produce, visit https://incident-prevention.com/podcasts. You can reach Danny at rainesafety@gmail.com
Purchase Danny’s Book on Amazon – https://a.co/d/556LDvz
#UtilitySafety #LinemanLife #WorkplaceSafety #IncidentPrevention #ElectricalSafety #SafetyCulture
Voice of Experience with Danny Raines, CUSP – Test, Verify, Prevent – Lessons from the Field
Join Danny Raines, CUSP, as he shares critical lessons learned from the field in this episode of The Voice of Experience. Danny dives into real-world incidents, including a tragic fatality and a near-miss, emphasizing the importance of testing and verifying in the utility safety industry. With decades of experience, Danny provides actionable insights to prevent accidents, improve safety protocols, and foster a culture of vigilance among utility professionals.
Key Takeaways:
1.Testing and Verifying Saves Lives: Never assume safety; always verify conditions to prevent catastrophic incidents.
2.Human Error Is Inevitable: Acknowledge that mistakes happen and take proactive steps to minimize risks.
3.The Power of Speaking Up: Encourage crews to challenge unsafe practices and prioritize safety over production.
4.Importance of Job Briefings: Thorough planning and hazard identification are critical to mitigating risks on-site.
4 Questions to learn from this podcast with Answers:
Q1: What is the primary cause of unsafe practices in the field?
A1: Assumptions and rushing to complete tasks often lead to neglecting crucial safety checks, like testing and verifying.
Q2: Why is “speaking up” vital in utility safety?
A2: It prevents potential accidents by addressing hazards early. Crew members should challenge unsafe practices without fear of backlash.
Q3: How can utility workers improve safety culture?
A3: By consistently practicing thorough job briefings, hazard identification, and compliance with safety regulations.
Q4: What role does leadership play in utility safety?
A4: Leaders must ensure oversight, provide proper training, and foster a culture where safety is prioritized over production.
You can read the current magazine at Incident Prevention Magazine.
Subscribe to Incident Prevention Magazine – https://incident-prevention.com/subscribe-now/
Register for the iP Utility Safety Conference & Expo – https://utilitysafetyconference.com/
The Voice of Experience with Danny Raines podcast is produced by the same team that publishes Incident Prevention. It delivers insights based on Danny’s regular column in the magazine, also called the Voice of Experience. To listen to more episodes of this podcast, as well as other podcasts we produce, visit https://incident-prevention.com/podcasts. You can reach Danny at rainesafety@gmail.com
Purchase Danny’s Book on Amazon – https://a.co/d/556LDvzc
#UtilitySafety #WorkSafe #CUSP #LinemanSafety #IncidentPrevention #SafetyLeadership
Voice of Experience with Danny Raines, CUSP – Are You Looking Out a Window or Into a Mirror? A New Perspective on Utility Safety
In this episode, safety consultant Danny Raines, CUSP, reflects on critical issues facing the utility industry, including safety practices, training gaps, and the persistent challenges of electrical fatalities. Danny delves into the importance of adhering to safety protocols, fostering a culture of accountability, and embracing innovation in personal protective equipment (PPE). Through stories from his career, Danny emphasizes the life-saving significance of vigilance and teamwork in high-risk environments.
Key Takeaways:
1.Window vs. Mirror Perspective: Evaluate whether you are self-reflective (mirror) or outward-focused (window) in safety practices.
2.“Learn-It-All” Mindset: Embrace a continuous learning approach over the “know-it-all” attitude.
3.The Numbers Don’t Lie: Despite advancements in PPE and training, electrical fatalities remain stagnant, demanding deeper industry introspection.
4.Accountability Saves Lives: The role of dedicated observers and adherence to safety protocols cannot be overstated.
5.A Culture of Safety: Building relationships and fostering open communication among crews enhance workplace safety.
6.Personal Responsibility: Safety isn’t just about individual choices—it impacts families and communities.
You can read the current magazine at Incident Prevention Magazine.
Subscribe to Incident Prevention Magazine – https://incident-prevention.com/subscribe-now/
Register for the iP Utility Safety Conference & Expo – https://utilitysafetyconference.com/
The Voice of Experience with Danny Raines podcast is produced by the same team that publishes Incident Prevention. It delivers insights based on Danny’s regular column in the magazine, also called the Voice of Experience. To listen to more episodes of this podcast, as well as other podcasts we produce, visit https://incident-prevention.com/podcasts. You can reach Danny at rainesafety@gmail.com
Purchase Danny’s Book on Amazon – https://a.co/d/556LDvz
#UtilitySafety #ElectricalSafety #PPEInnovation #LinemanLife #SafetyCulture #DannyRaines
Voice of Experience – Surviving the Storm: Lessons from the Field with Danny Raines, CUSP
In this episode of The Voice of Experience, Danny Raines, CUSP, shares his invaluable insights from decades of storm work as a lineman and utility safety expert. From the devastation of Hurricane Katrina to modern-day storm recovery challenges, Danny takes us through the physical and mental toll of responding to natural disasters. He explains the dangers of backfeeds, the rise of alternative energy sources, and the importance of verifying safety before restoring power. Learn from his firsthand stories, safety lessons, and how the landscape of utility work has evolved over the years. Whether you’re in the utility industry or just curious about storm response, this episode offers a wealth of knowledge from one of the most respected professionals in the field.
Key Takeaways:
- The dangers of storm work: Power restoration involves more than meets the eye, especially with evolving technology like solar panels and generators creating backfeed hazards.
- Mental and physical challenges: Long hours, dangerous conditions, and the emotional impact of storm recovery can lead to severe fatigue and stress.
- Importance of testing and verifying: Danny stresses the importance of safety procedures, especially when dealing with energized systems after a storm.
- Stories from the field: Real-life experiences from Hurricane Katrina and other storms demonstrate the unpredictable nature of storm recovery.
- Utility evolution: Changes in technology, regulations, and community expectations are reshaping the utility industry’s response to natural disasters.
You can read the current magazine at Incident Prevention Magazine.
Subscribe to Incident Prevention Magazine – https://incident-prevention.com/subscribe-now/
Register for the iP Utility Safety Conference & Expo – https://utilitysafetyconference.com/
The Voice of Experience with Danny Raines podcast is produced by the same team that publishes Incident Prevention. It delivers insights based on Danny’s regular column in the magazine, also called the Voice of Experience. To listen to more episodes of this podcast, as well as other podcasts we produce, visit https://incident-prevention.com/podcasts. You can reach Danny at rainesafety@gmail.com
Purchase Danny’s Book on Amazon – https://a.co/d/556LDvz
#UtilitySafety #StormWork #HurricaneKatrina #LinemanLife #BackfeedDangers #MentalHealthMatters #TestAndVerify #PowerRestoration #StormRecovery #AlternativeEnergy #UtilityIndustry #SafetyFirst #DannyRaines #CUSP #ElectricGrid #DisasterResponse
Voice of Experience – Danny Raines, CUSP – Lineman – Lineworker Development
June 3, 2024
Listen to this important episode of this Voice of Experience with Danny Raines!
The speaker, a retired lineman with over 55 years of experience, discusses the importance of proper training and development for lineman. He argues that simply obtaining a journeyman license doesn’t guarantee competency and that true learning happens on the job.
The speaker outlines the different stages of lineman development, starting with basic line skills like climbing poles and tying knots. He emphasizes the importance of safety rules and procedures, and of always testing and verifying everything before starting work.
The speaker also discusses the challenges of troubleshooting electrical problems and the importance of critical thinking and problem-solving skills. He concludes by sharing a personal story about his own journeyman lineman training.
Here are some key takeaways from the description:
- Lineman development is a continuous process that goes beyond obtaining a journeyman license.
- On-the-job training is crucial for developing the necessary skills and knowledge.
- Safety rules and procedures must be strictly followed.
- Critical thinking and problem-solving skills are essential for troubleshooting electrical problems.
Subscribe to Incident Prevention Magazine – https://incident-prevention.com/subscribe-now/
Register for the iP Utility Safety Conference & Expo – https://utilitysafetyconference.com/
The Voice of Experience with Danny Raines podcast is produced by the same team that publishes Incident Prevention. It delivers insights based on Danny’s regular column in the magazine, also called the Voice of Experience.
To listen to more episodes of this podcast, as well as other podcasts we produce, visit https://incident-prevention.com/podcasts.
You can reach Danny at rainesafety@gmail.com.
34 mins. with Danny Raines
Voice of Experience – Danny Raines, CUSP – Ruling Spans and Proper Conductor Sag
May 1, 2024
Listen to this important episode of this Voice of Experience with Danny Raines! Cold weather highlights the importance of proper conductor sag. Improper sag can lead to outages, but using the right calculations keeps the system safe.
Read the article – https://incident-prevention.com/blog/ruling-spans-and-proper-conductor-sag/
Early days: We used to tighten conductors for looks, unaware of factors like “ruling spans.” This worked in mild climates, but led to failures in harsh winters.
The Science: Conductor size, span length, and installation temperature all affect final sag and tension.
Getting it Right: We all want a neat system, but too much slack can cause problems too. Elevation changes and long pulls require extra considerations.
A Case Study: Improper uphill sagging during a long pull forced us to re-sag to achieve proper tension.
The Takeaway: Today, detailed specifications and online resources guide proper sagging. Initial sag should be close, with final adjustments and dynamometer checks following.
Do it Right, Once: True professionals take the time to ensure quality work that lasts. A circuit I worked on 30 years ago still has proper sag – a testament to getting it right the first time.
Register for the iP Utility Safety Conference & Expo – https://utilitysafetyconference.com/
The Voice of Experience with Danny Raines podcast is produced by the same team that publishes Incident Prevention. It delivers insights based on Danny’s regular column in the magazine, also called the Voice of Experience.
To listen to more episodes of this podcast, as well as other podcasts we produce, visit https://incident-prevention.com/podcasts.
You can reach Danny at rainesafety@gmail.com or 770-354-7360.
Subscribe to Incident Prevention Magazine – https://incident-prevention.com/subscribe-now/
The Voice of Experience with Danny Raines podcast is produced by the same team that publishes Incident Prevention. It delivers insights based on Danny’s regular column in the magazine, also called the Voice of Experience.
Read More of Danny’s Articles here
You can reach Danny at rainesafety@gmail.com.
29 mins. with Danny Raines
Voice of Experience – Danny Raines, CUSP – Determining Reasonable Energy Estimates
February 15, 2024
Listen to Danny Raines, CUSP discuss his newest article in iP Magazine about Determining Reasonable Energy Estimates.
Read the article here – https://incident-prevention.com/blog/determining-reasonable-energy-estimates/
Subscribe to Incident Prevention Magazine – https://incident-prevention.com/subscribe-now/
The Voice of Experience with Danny Raines podcast is produced by the same team that publishes Incident Prevention. It delivers insights based on Danny’s regular column in the magazine, also called the Voice of Experience.
Read More of Danny’s Articles here
You can reach Danny at rainesafety@gmail.com.
29 mins. with Danny Raines
Voice of Experience – Danny Raines, CUSP – Ferroresonance
November 2, 2023
Listen to Danny Raines, CUSP discuss his newest article in iP Magazine about Ferroresonance
Read the article here – https://incident-prevention.com/blog/understanding-and-preventing-ferroresonance/
You can also read the current magazine at Incident Prevention Magazine.
Subscribe to Incident Prevention Magazine – https://incident-prevention.com/subscribe-now/
The Voice of Experience with Danny Raines podcast is produced by the same team that publishes Incident Prevention. It delivers insights based on Danny’s regular column in the magazine, also called the Voice of Experience.
Read More of Danny’s Articles here
You can reach Danny at rainesafety@gmail.com.
15 mins. with Danny Raines
Voice of Experience – Danny Raines – Equipotential or Total Isolation
September 27, 2023
Listen to Danny Raines, CUSP discuss his newest article in iP Magazine about Equipotential or Total Isolation.
Read the article here – https://incident-prevention.com/blog/equipotential-or-total-isolation/
You can also read the current magazine at Incident Prevention Magazine.
Subscribe to Incident Prevention Magazine – https://incident-prevention.com/subscribe-now/
The Voice of Experience with Danny Raines podcast is produced by the same team that publishes Incident Prevention. It delivers insights based on Danny’s regular column in the magazine, also called the Voice of Experience.
Read Danny’s Articles here
You can reach Danny at rainesafety@gmail.com.
22 mins. with Danny Raines
Voice of Experience – Danny Raines, CUSP – Understanding Task Specific Training
September 13, 2023
Listen to Danny Raines, CUSP discuss his newest article in iP Magazine about Understanding Task Specific Training.
Read the Article – iP Digital Magazine
You can also read the current magazine at Incident Prevention Magazine.
Subscribe to Incident Prevention Magazine – https://incident-prevention.com/subscribe-now/
The Voice of Experience with Danny Raines podcast is produced by the same team that publishes Incident Prevention. It delivers insights based on Danny’s regular column in the magazine, also called the Voice of Experience.
Read Danny’s Articles here
You can reach Danny at rainesafety@gmail.com.
20 mins. with Danny Raines
Voice of Experience: Danny Raines, CUSP – Lineworkers & Rubber Sleeves – Another Look
July 24, 2023
Listen to Danny Raines, CUSP discuss his newest article in iP Magazine about Lineworkers & Rubber Sleeves – Another Look.
Rubber sleeves are an important safety tool for lineworkers who work with energized electrical equipment. They provide additional insulation and protection from electrical shock, and can help to prevent serious injuries or death.
In the past, some lineworkers did not wear rubber sleeves, but this practice has become increasingly rare in recent years. The OSHA Strategic Partnership Program, which was developed in 2005-2006, encourages the use of rubber sleeves by lineworkers. The program has been successful in reducing the number of electrical incidents and fatalities, and most lineworkers now wear rubber sleeves when working with energized equipment.
OSHA regulations require that lineworkers wear rubber insulating gloves and sleeves when working with energized parts. However, there are some exceptions to this rule. For example, an employee may not need to wear rubber sleeves if the exposed energized parts on which the employee is not working are insulated from the employee.
It is important for lineworkers to be aware of the risks associated with working with energized electrical equipment. Rubber sleeves are an important safety tool that can help to prevent serious injuries or death.
Here are some additional benefits of wearing rubber sleeves:
- They can help to protect the lineworker’s arms from burns and other injuries caused by arc flash.
- They can help to prevent the lineworker from being electrocuted if they come into contact with an energized conductor.
- They can help to reduce the risk of developing electrical shock-related health problems, such as heart arrhythmias and nerve damage.
If you are a lineworker or work in a related field, it is important to wear rubber sleeves when working with energized electrical equipment. Rubber sleeves can help to protect you from serious injuries or death.
The Voice of Experience with Danny Raines podcast is produced by the same team that publishes Incident Prevention. It delivers insights based on Danny’s regular column in the magazine, also called the Voice of Experience.
Read Danny’s Articles here
You can reach Danny at rainesafety@gmail.com.
24 mins. with Danny Raines
Utility Safety Voice of Experience: Danny Raines, CUSP – Lineworkers & Rubber Sleeves
June 19, 2023
Listen to Danny Raines, CUSP discuss his newest article in iP Magazine about Lineworkers & Rubber Sleeves.
Rubber sleeves are an important safety tool for lineworkers who work with energized electrical equipment. They provide additional insulation and protection from electrical shock, and can help to prevent serious injuries or death.
In the past, some lineworkers did not wear rubber sleeves, but this practice has become increasingly rare in recent years. The OSHA Strategic Partnership Program, which was developed in 2005-2006, encourages the use of rubber sleeves by lineworkers. The program has been successful in reducing the number of electrical incidents and fatalities, and most lineworkers now wear rubber sleeves when working with energized equipment.
OSHA regulations require that lineworkers wear rubber insulating gloves and sleeves when working with energized parts. However, there are some exceptions to this rule. For example, an employee may not need to wear rubber sleeves if the exposed energized parts on which the employee is not working are insulated from the employee.
It is important for lineworkers to be aware of the risks associated with working with energized electrical equipment. Rubber sleeves are an important safety tool that can help to prevent serious injuries or death.
Here are some additional benefits of wearing rubber sleeves:
- They can help to protect the lineworker’s arms from burns and other injuries caused by arc flash.
- They can help to prevent the lineworker from being electrocuted if they come into contact with an energized conductor.
- They can help to reduce the risk of developing electrical shock-related health problems, such as heart arrhythmias and nerve damage.
If you are a lineworker or work in a related field, it is important to wear rubber sleeves when working with energized electrical equipment. Rubber sleeves can help to protect you from serious injuries or death.
The Voice of Experience with Danny Raines podcast is produced by the same team that publishes Incident Prevention. It delivers insights based on Danny’s regular column in the magazine, also called the Voice of Experience.
Read Danny’s Articles here
You can reach Danny at rainesafety@gmail.com.
24 mins. with Danny Raines
Utility Safety Voice of Experience: Danny Raines, CUSP – Arc Flash Precautions: A Review
March 9, 2023
Listen to Danny has he walks us through a review on a very important topic: Arc Flash Precautions.
Read Danny’s Article here
You can reach Danny at rainesafety@gmail.com.
30 mins. with Danny Raines
Utility Safety Voice of Experience: Danny Raines, CUSP – Danny Raines, CUSP – Stories from Legends of an Ole’ Lineman
January 13, 2023
This book is a collection of stories from lessons learned and mistakes made as I progressed my career at Georgia Power. Applied for and award a position as “Helper on line Crew immediately after graduating High School and retired after 40 years as Safety Consultant for Distribution and Transmission. for GPC. After Lineman, I was awarded Crew Supervisor, Safety and Training, and finally a Safety Consultant’s position for the company. After retiring from GPC, I founded Raines Utility Safety Solutions and am currently the owner and Principal Consultant. I began his career in the electrical utility industry in June 1967 in Macon, Georgia with Georgia Power Company. Served a short time in the U. S. Army in 1968-69 and is a Viet Nam Era disabled veteran. Returning to Georgia Power worked as a lineman until till1985. Worked as contract coordinator over utility crews and line clearing forestry. In late 1996, Danny entered Safety and Health, promoted to Supervisor, Project Manager, and Corporate Safety Consultant for Distribution and Transmission organizations. Danny retired from Georgia Power on December 1st, 2007, as the Safety Consultant for Distribution and Transmission organizations and founded Raines Utility Safety Solutions, LLC. Danny is currently an Affiliate Instructor at Georgia Tech Research Institute in Atlanta, Ga., an electric utility Subject Matter Expert and Consultant in civil cases, supporting electrical Contractors, Co-Ops, and Municipal utility companies across the US.
You can read the current magazine at Incident Prevention Magazine.
27 mins. with Danny Raines
Utility Safety Voice of Experience: Danny Raines, CUSP – Ground Gradient Step Potential and PPE
December 14, 2022
In this episode, Danny Raines, CUSP talks on why, for various reasons, ground gradient step potential hazards are not always considered or thought to be important. I recently received a call from a large investor-owned utility whose employees had differing opinions about using super dielectric overshoes or work boots when setting a pole in an energized line. Some people are of the opinion that if you cover up the lines with a nominal voltage-rated cover, there is no danger of an energized pole and therefore no chance of ground gradient step potential. I believe the manufacturer’s usage suggestion for any cover is for incidental brush contact by a qualified worker, not a boom truck or pole. There is nothing in ASTM D1050, “Standard Specification for Rubber Insulating Line Hose,” stating that hoses can be used for any means or measures other than a qualified electrical worker’s personal protection from energized conductors. Pole shields are another product believed by many to protect workers on the ground who make indirect contact with energized parts. But unless the company is an electric cooperative and lives by the required Rural Electric Safety Achievement Program, which is part of the annual compliance audit by the company that insures most electric cooperatives, the dielectric testing of Salcor line hoses does not happen. Everything, including pole shields, is rated safety equipment.
28 mins. with Danny Raines
Utility Safety Voice of Experience: Lineman’s Stories from Danny Raines, CUSP in Upcoming Book
August 22, 2022
In this episode, Danny Raines, CUSP clears up his semi-retirement while giving you 2 stories from his new upcoming book labeled “A Lineman’s Story” by Danny Raines (Coming Soon!) . Always a popular educator, Danny is in the process of writing a book about his experience of becoming a lineman and ultimately enjoying his chosen career for over 40 years. Here at Incident Prevention, we are all looking forward to reading what Danny has to say once his book becomes available.
25 min. with Danny Raines
Utility Safety Voice of Experience: Installing Fiber Optic Cable in Electrical Supply Spaces
January 25, 2022
In this episode, Danny offers listeners additional commentary on “Installing Fiber Optic Cable in Electrical Supply Spaces,” which he wrote about in the December 2021-January 2022 issue of Incident Prevention magazine. You can read the article at https://bit.ly/fiberopticinelectrical.
20 min. with Danny Raines
Utility Safety Voice of Experience with Danny Raines: System Grounding for Worker Protection Against Induced Voltages
September 23, 2021
In this episode, Danny offers listeners additional commentary on “System Grounding for Worker Protection Against Induced Voltages,” which he wrote about in the June-July 2021 issue of Incident Prevention magazine. You can read the article at https://bit.ly/systemgrounding.
20 min. with Danny Raines
Utility Safety Voice of Experience with Danny Raines: Overhead Line Work, Then and Now
June 2, 2021
In this episode, Danny offers listeners additional commentary on “Overhead Line Work, Then and Now,” which he wrote about in the June-July 2021 issue of Incident Prevention magazine. You can read the article at https://incident-prevention.com/ip-articles/overhead-line-work-then-and-now.
20 min. with Danny Raines
Utility Safety Voice of Experience with Danny Raines: Who is in Charge of System Operations?
April 19, 2021
In this episode, Danny provides additional views and perspectives from his April-May 2021 column called “System Operations: Who’s In Charge?” You can read this article by going to incident-prevention.com. Let’s join Danny to learn why it’s important to slow down, or even stop work, when something doesn’t seem right about the job.
20 min. with Danny Raines
Utility Safety Voice of Experience with Danny Raines: My Male Breast Cancer Survivor Story
March 5, 2021
American entrepreneur Jim Rohn once said, “Take care of your body; it’s the only place you have to live.” In this episode, we talk about a different type of safety than we usually do—and that safety revolves around personal health and the dangers of a less-talked-about cancer: male breast cancer.
20 min. with Danny Raines
Utility Safety Voice of Experience with Danny Raines: Understanding Lone Worker Limitations
January 26, 2021
Welcome to an all-new podcast based on Incident Prevention magazine’s popular column called the Voice of Experience, written by Danny Raines, CUSP. Danny worked for Georgia Power for 40 years and has been consulting and educating utilities and utility contractors ever since. He’s been one of the most popular speakers at the iP Utility Safety Conference & Expo our annual conferences and at iP Institute’s online webinar education events.
We’re excited to bring Danny’s extensive knowledge and experience to our podcast by launching this Voice of Experience channel. We hope you will join us as Danny provides utility safety and operations professionals like you with impactful insights and observations.
In this episode, Danny talks in greater detail about lone worker limitations, a subject he covered in his column for the December 2020-January 2021 issue of Incident Prevention magazine.This podcast is published by the team at Incident Prevention magazine. Learn more at incident-prevention.com/podcasts.
Utility Safety Solutions Podcasts
Utility Safety Solutions: 2022 FR Update Live From the Expo floor at the Utility Safety Conference & Expo
June 6, 2022
Kurt reports in from the expo floor of the Utility Safety Conference & Expo to provide you with a comprehensive look at what’s new in the FR industry!
20 min. with several FR clothing exhibitors
Utility Safety Solutions: Learn How Intellishift’s Telematics and AI Camera Solutions are Improving Utility Fleet Safety
April 19, 2022
Kurt reports in from the NAFA conference where he met up with Intellishift’s Jordan Kittle to talk all about how the company is making innovative technology solutions that improve utility fleet safety as well as a conversation about a celebrity encounter with LeBron James.
20 min. with Intellishift’s Jordan Kittle
Utility Safety Solutions: Talking Traffic Safety with Traffix Devices
March 24, 2022
Kurt Moreland reports live from the American Traffic Safety Services Association show where he talks all about utility traffic safety solutions with representatives from Traffix Devices. From cones and attenuators to barrels and flashing devices, you’ll learn about tools that can help your team stay safer on the roads. And, the Traffix Devices team even shares an amusing celebrity encounter story involving a famous Dallas quarterback.
20 min. with Traffix Devices team
Utility Safety Solutions: Talking with Telelink about Their Lone Worker Monitoring and Incident Response Solution
February 25, 2022
Kurt Moreland sits down to talk with Laura Fudge from Telelink about how a monitoring and incident response solution for lone utility workers can help increase safety and save lives. They also talk about how the monitoring has been a vital safety solution for Newfoundland Hydro and even have fun talking about a celebrity encounter with Bill Nye, the Science Guy.
20 min. with Laura Fudge
Utility Safety Solutions: Ronan’s Innovative Battery-Powered Ascender Device
January 26, 2022
Join Kurt Moreland on the expo floor at the Tree Care Industry Expo where he talks about an innovative new safety product with Ronin Revolution Company CEO Bryan Bertrand. Learn about how Ronin’s battery-powered ascender device helps utility workers ascend towers and other structures with the ease of a automated hoist device.
20 min. with Bryan Bertrand
Utility Safety Solutions: Talking Safety with Terex Utilities
January 18, 2022
Incident Prevention magazine’s Associate Publisher Kurt Moreland stopped by the Terex Utilities newly expanded and state-of-the-art manufacturing facility to talk with Joe Caywood, the Director of Marketing for Terex Utilities. Joe talks about how Terex is focused on safety for its customers and for its own employees as well as some tails about mountain lion encounters.
20 min. with Joe Caywood
Utility Safety Solutions: Talking about FR Products & Apparel with NASCO
December 2, 2021
On a recent road trip, Incident Prevention magazine’s Associate Publisher Kurt Moreland stopped by the NASCO headquarters to talk FR shop with Andrew Wirts, the Sales & Marketing Director for NASCO. Andrew talks about how NASCO is working to make FR rainwear more comfortable, how they are improving safety for utility workers through better reflective trim placement and even a celebrity-encounter story with John Cougar Mellencamp.
20 min. with Andrew Wirts
Utility Safety Solutions: Celebrating JL Matthews‘ 75th Anniversary
October 5, 2021
In this special episode of Utility Safety Solutions, Kurt talks with Danny Matthews and Jennifer Matthews from JL Matthews to discuss their 75th Anniversary at their celebration event in Fort Worth, Texas.
20 min. with Danny Matthews
Utility Safety Solutions: An Innovative Hard Hat Illumination Device that Improves Visibility & Worker Visibility
August 13, 2021
When it comes to visibility at night, safety is impacted in two ways. Workers have to be able to clearly see what they are working on. And, workers need to be visible to others around them. That’s where the Halo SL comes in, a sleek—yet extremely bright—lamp that snaps right on to a safety helmet. Kurt Moreland sits down with Max Baker from ILLUMAGEAR to talk about the Halo SL and how it improves worksite safety!
20 min. with Max Baker
Utility Safety Solutions: A New Underground Cable Tool that Improves Ergonomics and Efficiency
July 2, 2021
We always love when we see lineworkers out in the field invent new products and solutions that make the job safer and more efficient! This is why Kurt Moreland invited to this episode of the podcast Ben Schwartz from Linehand’s Choice—a lineman who, along with his team, invented an excellent new tool that greatly increases the ergonomic safety and efficiency of working with underground cable.
20 min. with Ben Schwartz
Utility Safety Solutions: Talking About a New RFID Product and a Recent Acquisition
May 27, 2021
Kurt Moreland sits down with Jelco’s Kat Lea to discuss an exciting new radio-frequency identification tag product — EZE Track — which will offer utilities the ability to track all of their products and product records, inspection logs and instruction manuals via cloud-based technology. Kurt and Kat also talk about Jelco’s acquisition of Elk River Inc.
20 min. with Kat Lea
Utility Safety Solutions: An On-Helmet Detector that Alerts Your Workers to Electrocution Hazards
March 5, 2021
The unique aspect about electricity that makes it so dangerous is that, by most accounts, it is not easily detected through one’s sense of sight or sound. In this episode, we sit down with lineman trainer Brady Hansen of Safeguard Equipment, who tells us about an innovative utility safety product designed to act as a “sixth sense” for workers by providing an on-helmet audio/visual alert system for voltage and current detection.
20 min. with Brady Hansen
Utility Safety Solutions: An Innovative New Tool that Removes the Danger of Cutting Underground Primary Cables
February 23, 2021
We caught up with Ryan Berg from Greenlee to learn about their innovative remote cutter tool that puts the worker at a safe distance when cutting primary underground cables. Ryan tells all about the safety aspects of the cutter and many of the other safety initiatives happening at Greenlee–and he’ll even share a tale about his celebrity encounter with a member of popular rock band, Cheap Trick!
20 min. with Ryan Berg
Utility Safety Solutions: Cold Weather Strategies with Ty Fenton from Safety One Training
January 29, 2021
Cold weather is dangerous. Being prepared for extreme weather is vital for utility workers who must endure harshly cold weather. We caught up with Ty Fenton from Safety One Training to get some important insights and strategies on how you can make sure your workers are ready for the conditions.
Utility Safety Solutions is a podcast that provides utility safety and ops professionals with an in-depth look at innovative products, services and strategies that help reduce incidents and increase safety success. Incident Prevention Associate Publisher Kurt Moreland looks for the most exciting and timely solutions happening in the industry right now and sits down to talk with the folks who bring those products to you. Utility Safety Solutions is published by the team at Incident Prevention magazine. Learn more at incident-prevention.com/podcasts.
20 min. with Ty Fenton
Utility Safety in Depth Podcasts
Influencing Safety pt 10 – Is Safety Truly the Utility Industry’s First Priority? with Bill Martin, CUSP
Challenging the Status Quo: Rethinking Safety in the Utility Industry
Is safety truly the utility industry’s first priority? And is it even a real thing, or just a byproduct of something deeper? In this thought-provoking episode of Influencing Safety, Bill Martin, President and CEO of Think Tank Project LLC, joins host Kate Wade to challenge traditional views on safety. They explore the critical role of teamwork, communication, and human connection in fostering a truly safe work environment. Bill shares insights on the psychological factors that influence workplace culture, the hidden impact of mental health, and how shifting our focus from compliance to competency could change the game.
Key Takeaways:
✅ Safety isn’t just about compliance—it’s a byproduct of strong teamwork and communication.
✅ A psychologically safe work environment fosters better decision-making and fewer incidents.
✅ The traditional “safety first” mindset might be limiting our ability to create real change.
✅ Human connection and mental health are critical factors in workplace safety.
✅ Small changes, like pre-job huddles and open conversations, can have a major impact.
Subscribe to Incident Prevention Magazine – https://incident-prevention.com/subscribe-now/
Register for the iP Utility Safety Conference & Expo – https://utilitysafetyconference.com/
#WorkplaceSafety #UtilityIndustry #SafetyCulture #PsychologicalSafety #TeamworkMatters #LeadershipDevelopment #IncidentPrevention #CommunicationIsKey #CUSP #IncidentPrevention
Utility Safety in Depth – Bridging the Safety Gap – The Role of USMWF in Workplace Fatalities
In this episode of Utility Safety in Depth, host Kate Wade sits down with John “Scotty” MacNeill and Rena Harrington to explore the mission of the United Support & Memorial for Workplace Fatalities (USMWF). They discuss the critical role USMWF plays in supporting families affected by workplace fatalities, advocating for stronger safety regulations, and raising awareness in the utility industry. With personal stories, industry insights, and a call to action, this conversation highlights the human impact of workplace safety failures and the importance of proactive prevention.
Key Takeaways:
✔️ The Mission of USMWF: How the organization supports families affected by workplace fatalities.
✔️ Bridging the Safety Gap: Why family members must be involved in post-incident investigations.
✔️ The Power of Storytelling: How sharing personal loss creates real change in workplace safety.
✔️ Advocacy & Legislation: Efforts to improve safety laws at the state and federal levels.
✔️ What Utility Companies Can Do: How organizations can collaborate with USMWF to make a difference.
USMWF’s MISSION
Offers support, guidance and resources to those affected by work-related injuries, illnesses or diseases. Dedicated to sharing lessons learned that leads a movement of change in promoting actions for safe and healthy working conditions. Through the collective voice of families of fallen workers and other activists, we strive for the elimination and controls of workplace hazards– therefore preventing future tragedies.
USMWF’s VISION STATEMENT
USMWF is an organized community of dedicated family member victims, a nationally recognized non-profit leader driving the transformation of the work environment to safe and healthy conditions for all employers and employees – both today and tomorrow.
Read the article in iP Magazine – Read Here
Visit https://www.usmwf.org/ to support The United Support & Memorial for Workplace Fatalities.
Subscribe to Incident Prevention Magazine – https://incident-prevention.com/subscribe-now/
Register for the iP Utility Safety Conference & Expo – https://utilitysafetyconference.com/
#UtilitySafety #WorkplaceSafety #IncidentPrevention #LinemanLife #SafetyAdvocacy #StaySafe #USMWF
From the Olympics to the Utility Field: Dr. Kevin Rindal, DC on Preventing Soft Tissue Injuries
In this episode of the Incident Prevention Utility Safety Podcast, Kate Wade interviews Dr. Kevin Rindal, DC, chiropractor, human performance expert, and co-founder of Vimocity. Drawing from his extensive experience with the U.S. Olympic Swim Team and industrial athletes, Dr. Rindal shares insights on preventing soft tissue injuries, implementing dynamic warmup programs, and securing organizational buy-in for holistic well-being strategies. Learn how utilities can leverage sports medicine principles to enhance safety, reduce costs, and improve workers’ quality of life.
Key Takeaways
- Industrial Athletes and Soft Tissue Injuries: How utility workers face similar physical demands to athletes and the role of dynamic preparation in reducing injury rates.
- Proactive vs. Reactive Approaches: The importance of addressing leading indicators like pain to prevent more significant injuries or reliance on opioids and other pain mitigations.
- Integration with Daily Routines: Methods to seamlessly incorporate warmups, muscle maintenance, and recovery into existing workflows, making it scalable for smaller organizations.
- Leveraging Technology and Gamification: How apps, micro learning, and team challenges foster engagement and create sustainable safety habits.
- Leadership and Culture: The critical role of leadership buy-in at all levels in making safety and well-being programs successful.
Connect with Kevin:
- LinkedIn – https://www.linkedin.com/in/kevinrindal/
- Email – kevin@vimocity.com
Resource Links:
- Short form job-task specific training video | LINK
- Dynamic/ Full-body movement routine (5 min or less) | LINK
- Avoid Slips, Trips and Falls video | LINK
You can read the current magazine at Incident Prevention Magazine.
Subscribe to Incident Prevention Magazine – https://incident-prevention.com/subscribe-now/
Register for the iP Utility Safety Conference & Expo – https://utilitysafetyconference.com/
#UtilitySafety #IndustrialAthletes #InjuryPrevention #Vimocity #WorkplaceWellbeing #DynamicWarmups
Utility Safety In Depth: The 100th Monkey Effect and Human Connection in Safety – Doug Hill, CUSP & Bill Martin, CUSP
In this episode of Utility Safety In Depth, we delve into the fascinating concept of the 100th monkey effect and its implications for safety in the utility industry. Join us as we discuss how collective consciousness and human connection can drive significant improvements in safety culture and outcomes. We’ll explore practical strategies to foster a more caring and supportive work environment, emphasizing the importance of communication, empathy, and mutual respect. Discover how embracing the power of human connection can lead to a safer and more resilient workforce.
Key Takeaways:
- The 100th Monkey Effect: How collective consciousness can influence individual behavior.
- The importance of human connection in safety culture.
- Practical strategies to foster a more caring and supportive work environment.
- The power of communication, empathy, and mutual respect.
- The role of leadership in creating a positive safety culture.
#utilitiesafety #safetyculture #humanconnection #100thmonkeyeffect #workplacewellbeing #safetyleadership #utilityindustry
You can read the current magazine at Incident Prevention Magazine.
Subscribe to Incident Prevention Magazine – https://incident-prevention.com/subscribe-now/
Register for the iP Utility Safety Conference & Expo – https://utilitysafetyconference.com/
Special Series – Influencing Safety Pt. 9 – Beyond the Buzzwords – Creating a Culture of Safety
Are you tired of hearing the same safety jargon without seeing real change? Join Bill Martin, President and CEO of think Tank Project, LLC, and Kate Wade, Editor of Incident Prevention magazine, as they dive deep into the root causes of workplace injuries and fatalities. Discover how to move beyond motivation and empty slogans to create a truly safe and connected work environment.
Key Takeaways from this podcast:
- Importance of Synchronization: The way forward in safety management involves creating a synchronized workforce where everyone is connected on a deeper level. Synchronization allows for better communication and understanding, reducing the chances of injuries and accidents.
- Action Over Motivation: Motivational speeches and slogans alone are insufficient to bring about real change in workplace safety. There needs to be actionable steps that translate motivation into tangible improvements on the ground.
- Understanding Human Behavior: The podcast emphasizes that much of human behavior is automatic, driven by the brain’s need to conserve energy. Safety programs should account for this by focusing on changing automatic behaviors rather than expecting constant vigilance.
- The Role of Leadership: Effective leadership is about asking the right questions and involving workers in safety decisions. Leaders should model the behavior they want to see and create environments that encourage participation and ownership of safety practices.
- Continuous Learning and Experimentation: The podcast suggests that safety improvements should be approached as ongoing experiments, where teams try out new ideas, evaluate their effectiveness, and adjust accordingly.
- Dealing with Resistance: Resistance to change is natural, especially in large organizations with many layers. The podcast highlights the importance of addressing this resistance by aligning everyone around common goals and encouraging openness to new ideas.
- Mental and Emotional Health: Addressing mental health issues, such as addiction and depression, is crucial for creating a safe work environment. A connected and supportive team can help identify and mitigate these risks.
- Practical Applications: The podcast concludes with a call to action—what small, tangible change can be implemented on Monday to make the workplace safer? It’s about translating ideas into real-world actions that have a measurable impact.
#safetyculture #workplaceinjury #safetymanagement #safetyleadership #industrialaccidents #safetytraining #safetytips #safetypodcast #accidentprevention #riskmanagement
You can read the current magazine at Incident Prevention Magazine.
Subscribe to Incident Prevention Magazine – https://incident-prevention.com/subscribe-now/
Register for the iP Utility Safety Conference & Expo – https://utilitysafetyconference.com/
Supporting Safety Professionals: A Conversation with Scott Francis, Technical Sales Manager, Westex, a Milliken Brand
Welcome to Incident Prevention’s Utility Safety Podcast, hosted by Kate Wade, editor of Incident Prevention magazine. In this episode, Kate sits down with Scott Francis, the technical sales manager for Westex, a Milliken brand renowned for pioneering protective textiles since 1941. Scott brings decades of experience in the safety industry, especially in the flame-resistant and arc-rated clothing markets.
During this insightful discussion, Scott shares his expertise on the latest advancements in flame-resistant and arc-rated apparel, the importance of live demonstrations, and how Westex is leading the way in educating safety professionals. He also touches on the challenges of balancing cost and safety standards, and the critical role of comfort in ensuring protective clothing is worn consistently.
Whether you’re a safety manager looking to enhance your PPE program or simply interested in the latest trends in utility safety apparel, this episode is packed with valuable information.
Key Takeaways:
- Impact of Live Demonstrations: Live flash fire and arc flash events leave a lasting impression, helping safety professionals understand the severity of thermal hazards.
- Survivor Stories: Hearing from thermal exposure survivors like Brad Livingston emphasizes the real-life consequences of not wearing proper PPE.
- Education and Training: Westex offers extensive educational resources, including webinars, regional safety conferences, and online materials to keep safety managers informed.
- Balancing Cost and Safety: The competitive landscape in flame-resistant fabric manufacturing drives innovation and helps maintain affordable prices without compromising safety.
- Comfort Equals Protection: Comfortable PPE is more likely to be worn consistently, directly impacting worker safety.
#UtilitySafety #FlameResistantClothing #ArcRatedApparel #PPE #WorkplaceSafety #SafetyPodcast #IncidentPrevention
You can read the current magazine at Incident Prevention Magazine.
Subscribe to Incident Prevention Magazine – https://incident-prevention.com/subscribe-now/
Register for the iP Utility Safety Conference & Expo – https://utilitysafetyconference.com/
Utility Safety in Depth – Special Series – Influencing Safety with Bill Martin, CUSP
Pt. 8 – Live from the iP Utility Safety Conference
June 6, 2024
In the eighth episode of this multipart podcast series, Bill Martin, CUSP, president and CEO of Think Tank Project LLC (www.thinkprojectllc.com), and host Kate Wade discuss a host of topics and what they are seeing in the safety world, and how to change it!
This podcast discusses safety in the utility industry.
Here are the key points: Safety conferences are not leading to a decrease in accidents. Bill Martin, a safety consultant, argues that the safety information is not being translated into actionable steps for workers. Focus on worker-centered safety. Instead of top-down safety initiatives, Bill Martin proposes a worker-centered approach where workers are involved in creating and implementing safety measures. The current safety approach might not consider human biology. Bill Martin argues that safety messages need to consider how the human brain reacts to stimuli in order to be effective. We need to connect with workers on a human level. Bill Martin emphasizes the importance of building relationships and trust with workers to create a safer work environment. Younger generations may hold the key to safety improvements. Bill Martin believes younger generations have the potential to improve safety practices if they are taught how to connect and be curious.
Listen to the other 7 parts of this special series with Bill Martin, CUSP.
To share feedback about this podcast, reach Bill at influenceteamdynamics@gmail.com and Kate at kwade@utilitybusinessmedia.com.
Subscribe to Incident Prevention Magazine – https://incident-prevention.com/subscribe-now/
Register for the iP Utility Safety Conference & Expo – https://utilitysafetyconference.com/
30 min. with Bill Martin, CUSP
Utility Safety in Depth – Five Core Capacities for Sustainable Safety Excellence – Shawn Galloway
May 3, 2024
In this episode, iP’s Kate Wade sits down with Shawn Galloway to dig into his recent iP article, “Five Core Capacities for Sustainable Safety Excellence.” Shawn is the CEO of ProAct Safety – which was founded in 1993 with the sole purpose of helping organizations achieve and sustain safety excellence – and author of several bestselling books, including his latest, “Bridge to Excellence: Building Capacity for Sustainable Performance.” Feel free to reach out to Shawn for further discussion at info@proactsafety.com.
Read the Article – https://incident-prevention.com/blog/five-core-capacities-for-sustainable-safety-excellence/
Subscribe to Incident Prevention Magazine – https://incident-prevention.com/subscribe-now/
Register for the iP Utility Safety Conference & Expo – https://utilitysafetyconference.com/
39 min. with Shawn Galloway
Utility Safety in Depth – An Experiment in Crew Engagement with Bill Martin, CUSP & Cheryl Richardson
April 23, 2024
In this episode, iP’s Kate Wade sits down with Cheryl Richardson, president of New York-based contractor H. Richardson & Sons, and Bill Martin, president and CEO of Think Tank Project LLC, to discuss a new safety initiative they have introduced at H. Richardson. Learn more about the implementation of this project, the impact it’s making thus far, and where it’s going in the future. Cheryl and Bill will be speaking on this topic next month at the iP Utility Safety Conference & Expo in Orlando, Florida, and also be sure to check out Cheryl’s article in the April-May 2024 issue of iP, available at https://incident-prevention.com/blog/an-experiment-in-crew-member-engagement/.
Actionable Safety Podcast – https://utilitysafety.podbean.com/e/utility-safety-in-depth-talking-actionable-safety-with-bill-martin/
Subscribe to Incident Prevention Magazine – https://incident-prevention.com/subscribe-now/
38 min. with Bill Martin, CUSP & Cheryl Richardson
Utility Safety in Depth – ESG: Health and Safety Obstacle or Opportunity? – John Fischer, Duke Energy
March 6, 2024
The podcast highlights the growing influence of ESG (Environmental, Social, and Governance) factors in the utility sector. ESG goes beyond just financial performance, considering a company’s environmental impact, social responsibility, and ethical practices. Investors are increasingly evaluating companies through this lens, pressuring utilities to focus on sustainability, worker safety, and good governance. Interestingly, safety practices themselves align well with ESG goals. This means safety professionals have an opportunity to leverage ESG to advocate for better resources, promote sustainable safety programs, and demonstrate the value of safety in the bigger picture of ESG. By understanding this connection, safety professionals can play a key role in shaping a more sustainable and responsible future for the utility industry.
Read the article here – https://incident-prevention.com/blog/esg-health-and-safety-obstacle-or-opportunity/
Subscribe to Incident Prevention Magazine – https://incident-prevention.com/subscribe-now/
To share feedback about this podcast, reach Bill at influenceteamdynamics@gmail.com and Kate at kwade@utilitybusinessmedia.com.
32 min. with John Fischer, CUSP
Special Series – Influencing Safety, Part 7, with Bill Martin, CUSP
January 23, 2024
Listen to Bill Martin, CUSP as he discusses some of the lessons we can take in the utility industry from some of his recent readings. Kate and Bill dive into a host of issues as we continue this great series of influencing safety!
- Viskontas, I. (2017). Brain Myths Exploded.
- Cialdini, R. (2021). Influence, New and Expanded: The Psychology of Persuasion.
- Sharot, T. (2017). The Influential Mind: What Our Brain Reveals About Our Power to Influence Others.
- Bohns, V. (2021). You Have More Influence Than You Think.
- Kahneman, D. (2011). Thinking, Fast and Slow.
- Gawande, A. (2009). The Checklist Manifesto.
- Gonzales, L. (1998). Deep Survival: Who Lives, Who Dies, and Why.
- De Becker, G. (2021). Survival Signals That Protect Us From Violence (Special Release Edition).
- Klein, G. (2013). Seeing What Others Don’t: The Remarkable Way We Gain Insights.
- Bargh, J. (2017). Before You Know It: The Unconscious Reasons We Do What We Do.
- Paul, A. M. (2021). The Extended Mind: The Power of Thinking Outside the Brain.
- Barrett, L. F. (2020). 7 ½ Lessons on the Brain.
- Clark, A. (2023). The Experience Machine: How Our Minds Predict and Shape Reality.
Listen to the other 6 parts of this special series with Bill Martin, CUSP.
Subscribe to Incident Prevention Magazine – https://incident-prevention.com/subscribe-now/
To share feedback about this podcast, reach Bill at influenceteamdynamics@gmail.com and Kate at kwade@utilitybusinessmedia.com.
55 min. with Bill Martin, CUSP
Special Series – Influencing Safety, Part 6, with Bill Martin, CUSP
November 22, 2023
In the sixth episode of this multipart podcast series, Bill Martin, CUSP, president and CEO of Think Tank Project LLC (www.thinkprojectllc.com), and host Kate Wade discuss some myths of safety live from the iP Utility Safety Conference in San Diego, CA.
Listen to the other 5 parts of this special series with Bill Martin, CUSP.
Subscribe to Incident Prevention Magazine – https://incident-prevention.com/subscribe-now/
To share feedback about this podcast, reach Bill at influenceteamdynamics@gmail.com and Kate at kwade@utilitybusinessmedia.com.
41 min. with Bill Martin, CUSP
Utility Safety in Depth – Harnessing AI with Barry Nelson, the President & CEO of FactorLab
October 24, 2023
Read the article here: https://incident-prevention.com/blog/harnessing-ai-crafting-the-future-of-safety-professionals/
Dive deeper into this article written by BARRY NELSON from FactorLab. Artificial intelligence (AI) has the potential to revolutionize the way safety professionals approach their work. In this article, Barry Nelson, president and CEO of FactorLab, discusses how AI can be used to create a future where work-related risks are minimized, productivity is maximized, and workplaces become more secure and efficient.
One of the most promising applications of AI in safety is in the area of data analytics. AI can be used to analyze large amounts of data from a variety of sources, including safety reports, incident investigations, and employee surveys. This data can then be used to identify patterns and trends that may not be visible to the human eye.
For example, AI can be used to identify specific jobs, tasks, or locations that are associated with a higher risk of accidents. This information can then be used to develop targeted interventions to reduce those risks.
AI can also be used to develop predictive maintenance programs. By analyzing data on equipment performance, AI can identify potential problems before they occur. This can help to prevent equipment failures that could lead to accidents.
In addition to data analytics, AI can also be used to develop new safety training programs. AI-powered training programs can be personalized to the individual needs of each employee. They can also be used to provide real-time feedback and support.
Nelson argues that AI is not a replacement for safety professionals. Instead, he sees AI as a tool that can help safety professionals do their jobs more effectively and efficiently. AI can help safety professionals to identify risks, develop interventions, and train employees.
In conclusion, AI has the potential to transform the way safety professionals approach their work. By harnessing the power of AI, safety professionals can create a future where work-related risks are minimized, productivity is maximized, and workplaces become more secure and efficient.
Sign Up For Your FREE Subscription to IP – https://incident-prevention.com/subscribe-now/
To share feedback about this podcast, reach Kate at kwade@utilitybusinessmedia.com.
37 min. with Barry Nelson
Utility Safety In Depth – Strengthening The Substation Fence – Jim Willis MSc, CMAS, CHS1
June 23, 2023
Listen to Kate Wade interview special guest Jim Willis, MSc, CMAS, CHS1. He is author of the article “Strengthening The Substation Fence” in the most recent June – July issue of Incident Prevention magazine.
People have finally discovered one of the best unkept secrets in America: Our utility systems can be attacked, and it doesn’t take military tacticians to pull it off, fInd out more from the article and this podcast as we take a deeper dive into this!
Sign Up For Your FREE Subscription to IP – https://incident-prevention.com/subscribe-now/
To share feedback about this podcast, reach Jim at jim.willis@indevtactical.net and Kate at kwade@utilitybusinessmedia.com.
19 min. with Jim Ellis
Special Series – Influencing Safety, Part 5, with Bill Martin, CUSP
May 30, 2023
In the fifth episode of this multipart podcast series, Bill Martin, CUSP, president and CEO of of Think Tank Project LLC (www.thinkprojectllc.com), and host Kate Wade discuss how leaders influence their workers like where we are getting it right and where there is room for improvement.
Listen to the other 4 parts of this special series with Bill Martin, CUSP.
To share feedback about this podcast, reach Bill at influenceteamdynamics@gmail.com and Kate at kwade@utilitybusinessmedia.com.
49 min. with Bill Martin, CUSP
Utility Safety in Depth – Josh Moody – Westex: A Milliken Brand – ”3 Sustainability Considerations When Evaluating FR/AR Apparel”
March 22, 2023
Listen to Kate Wade interview special guest Josh Moody, Director of Product Management | Westex: A Milliken Brand who is author of the article “3 Sustainability Considerations When Evaluating FR/AR Apparel” in the most recent February – March issue of Incident Prevention magazine.
Article: Link
Website: www.westex.com LinkedIn: Westex FR Showcase
42 min. with Josh Moody
Special Series – Influencing Safety, Part 4, with Bill Martin, CUSP
February 16, 2023
In the fourth episode of this multipart podcast series, Bill Martin, CUSP, president and CEO of (www.thinkprojectllc.com), and host Kate Wade discuss learned helplessness – what it is, what causes it, and how to break out of the habit.
Listen to the other 3 parts of this special series with Bill Martin, CUSP.
To share feedback about this podcast, reach Bill at influenceteamdynamics@gmail.com and Kate at kwade@utilitybusinessmedia.com.
42 min. with Bill Martin, CUSP
Special Series – Influencing Safety, Part 3, with Bill Martin, CUSP
November 25, 2022
In the third episode of this multipart podcast series, Bill Martin, CUSP, president and CEO of (www.thinkprojectllc.com), and host Kate Wade discuss emotional intelligence – what it is, why it’s so critical to line crew safety and why it should be considered a strength and not a weakness.
To share feedback about this podcast, reach Bill at influenceteamdynamics@gmail.com and Kate at kwade@utilitybusinessmedia.com.
52 min. with Bill Martin, CUSP
Utility Safety in Depth – Advancing Workforce Skills Using Simulation-Based Training
October 20, 2022
CM Labs’ Christa Fairchild and Alan Limoges sit down with host Kate Wade to discuss how equipment simulators can improve efficiencies in worker training, enhance safety, save costs, benefit trainers and more. This interview is based on the article Fairchild wrote for the October-November 2022 issue of Incident Prevention magazine. As a note to listeners, CM Labs will be presenting a session — titled “Training for the Worksite of Tomorrow” — at bauma Forum October 24 beginning at 4 p.m. The company will also be exhibiting in the show’s Canadian Pavilion. Read the article here: https://online.incident-prevention.com/publication/?m=19389&i=763067&p=34&ver=html5
28 min. with CM Labs’ Christa Fairchild and Alan Limoges
Special Series – Influencing Safety, Part 2, with Bill Martin, CUSP
September 12, 2022
In the second episode of this multipart podcast series, Bill Martin, CUSP, president and CEO of Think Tank Project LLC (www.thinkprojectllc.com), and host Kate Wade discuss psychological safety – what it is, why it’s so critical to line crew safety and tactics you can use to create it in a crew environment.
To share feedback about this podcast, reach Bill at influenceteamdynamics@gmail.com and Kate at kwade@utilitybusinessmedia.com.
38 min. with Bill Martin, CUSP
Using a Learning Management System to Augment Lineworker Training with Kenneth Pardue
September 6, 2022
Host Kate Wade welcomes Kenneth Pardue to take a deeper dive into the article that Kenneth wrote for the August/September 2022 issue of Incident Prevention, titled “Using a Learning Management System to Augment Lineworker Training.” In this episode, the two discuss what a learning management system is and how it can be useful in training both apprentices and seasoned journeymen. View the article here: link
18 min. with Kenneth Pardue
Special Series – Influencing Safety with Bill Martin, CUSP
August 3, 2022
In the first episode of this new multipart podcast series, safety consultant Bill Martin, CUSP and host Kate Wade begin with the basics, discussing what influence is, why Martin is so passionate about the topic plus some practical ways to positively influence safety in the workplace.
To share feedback about this podcast, reach Bill at influenceteamdynamics@gmail.com and Kate at kwade@utilitybusinessmedia.com.
20 min. with Bill Martin, CUSP
Talking Heat Illness & Injury Prevention with Mike Starner
May 9, 2022
Utility Safety In Depth host Kate Wade welcomes Mike Starner, CUSP, to take a deeper dive into the article Starner wrote for the April/May 2022 issue of Incident Prevention, titled “Heat Injury and Illness Prevention: Past, Present and Future.” In this episode, the two discuss the impact of climate change on worker safety, OSHA’s proposed rulemaking for heat injury and illness prevention, and more.
20 min. with Mike Starner from National Electrical Contractors Association
Utility Safety in Depth: Discussing Actionable Safety with Bill Martin
April 21, 2022
Host Kate Wade welcomes Bill Martin to take a deeper dive into the article that Martin wrote for the December 2021/January 2022 issue of Incident Prevention titled “Actionable Safety: Modeling Change for Line Crews.” In this episode, the two will discuss stop-work authority, training to prevent incidents, recognizing red flag words, what leaders should be modeling to improve safety and more.
51 min. with Bill Martin of Northline Utilities.
Utility Safety in Depth: Managing Risk Through Cognitive Impairment Testing
November 8, 2021
Often, when the term “cognitive impairment” comes up, most people immediately think about drug or alcohol impairment. And while that is an issue, there are many other things that can impair one’s mental clarity and, in turn, the safety of the job. In this episode, Kate Wade talks to Lee Marchessault of Workplace Safety Solutions and Jeff Sease of Predictive Safety SRP about the different types of cognitive impairments that can impact safety and what can be done to bring awareness to and reduce those impairment issues.
20 min. with Lee Marchessault of Workplace Safety Solutions and Jeff Sease of Predictive Safety SRP
Utility Safety In Depth: What Utilities & Contractors Need to Know About UTV & ATV Safety
May 27, 2021
Utility task vehicles (UTVs) and all-terrain vehicles (ATVs) are becoming increasingly popular transportation options for lineworkers who need to traverse difficult terrain to access work sites. In this episode, Kate Wade talks to Ty Fenton of Safety One Training about what utility and contractor organizations should consider when purchasing, training on and using these vehicles.
20 min. with Ty Fenton
Utility Safety In Depth: Understanding Complacency & How to Overcome It
April 21, 2021
What is the true cause of complacency? How can developing new habits reduce incidents? What is it about our brains that makes us want to take shortcuts? Sharon Lipinski, CEO of Habit Mastery Consulting, will answer these questions and more as she sits down with Incident Prevention magazine’s editor Kate Wade to discuss the biological basis of complacency.
20 min. with Sharon Lipinski
Utility Safety In Depth: Fire Extinguisher Safety Strategies
March 2, 2021
Are your utility workers properly equipped and trained to safely respond to vehicle fires? Fire safety expert Steve Nash will help you uncover the answer to this question and others as he sits down with Incident Prevention magazine’s editor Kate Wade to discuss what your crews need to do to protect themselves and save others.
20 min. with Steve Nash
Do you have insight to share with the utility safety community?
Contact us with your podcast topic and 2-3 learning objectives to be considered for our next podcast episode.
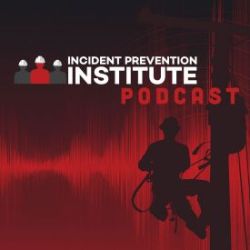