Jesse Hardy, CSP, CIT, CUSP
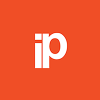
Jesse Hardy, CSP, CIT, CUSP
4 Questions for Continuous Improvement
As Jim, the owner of the company, walked the job site with the head of safety and quality, he said, “You know, we’ve made big gains in safety, quality and production, even as we’ve grown over 200% the past couple of years, but things have plateaued, and I don’t know what to do.” This may […]
Strategies to Handle Workplace Conflict
“Jack, the people issues are just getting to be too much,” the foreman said. “If it’s not the landowners and members of the public throwing fits and coming into the work zones, it’s our own people getting into conflicts. At best it’s a distraction that steals our focus, and at it’s worst it becomes violent.” […]
Avoid Injury When Lifting and Moving Objects
The foreman looked up and asked, “Jim, how are you feeling today?” Jim limped over and replied, “I’ll be OK, my back just goes out on me from time to time. I hurt it in my 20s, and it’s never been the same since. It comes and goes.” The foreman agreed, “Yeah, we always lifted […]
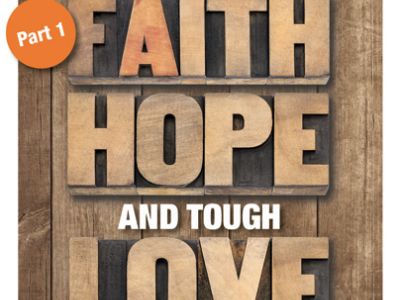
Leading Change Through Faith, Hope and Tough Love: Part II
As we discovered in the first part of this two-part series (see https://incident-prevention.com/blog/leading-change-through-faith-hope-and-tough-love-part-i), people are fallible, sometimes lessons aren’t learned, and improvements aren’t always made. This can leave leaders and team members feeling frustrated or apathetic because they don’t know how to right the ship. The simple truth is that your team should be able […]
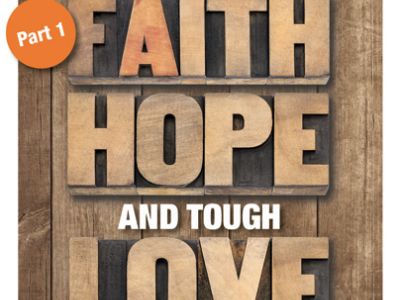
Leading Change Through Faith, Hope and Tough Love: Part I
The operations director stood before his direct reports, boiling over with anger. “Here we are again!” he said. “Still plagued with the same production, quality and safety issues – problems that we’ve cussed, discussed and created improvement plans for over and over again. I don’t know what’s wrong with you and your people, but we’re […]
Drug and Alcohol Awareness on the Job Site
It was a beautiful spring day when the call came in. “Jess, we need you out here. I’ve already called 911. One of the guys just died in the port-a-john. I think it’s an overdose. He’s a young guy who seemed healthy, and there’s a bottle of Percocet on the floor by his feet.” Yes, […]
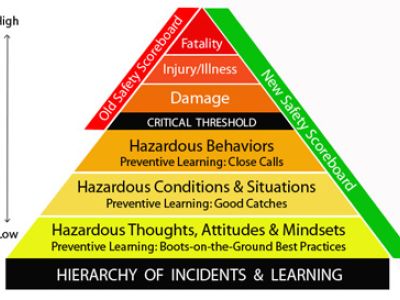
The Hierarchy of Incidents and Learning: Part II
The contractor’s executive team sat across the table from the client’s construction leadership. It was the client’s director who spoke first. “Let’s ensure everyone is on the same page,” he said. “Over the past six months, you’ve had numerous quality, production and schedule issues, an environmental noncompliance, two injuries and a utility contact that caused […]
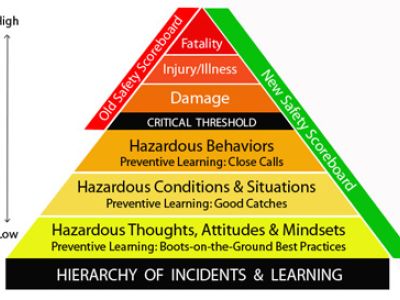
The Hierarchy of Incidents and Learning: Part I
You just want to do the job right and go home unharmed today, but things don’t always go as planned, incidents happen, and the lessons your team learns don’t always change the way you’ll do the job tomorrow. This can leave you feeling frustrated and helpless to improve the things that keep your team from […]
Battling Fatigue on the Job Site
The operator stared at the CAT 349 excavator that lay half in the trench. The cab had been partially crushed when the operator’s side of the trench wall had collapsed as he straddled it with the excavator’s tracks. “I don’t know, Jess,” he said to me. “It just seemed like the thing to do at […]
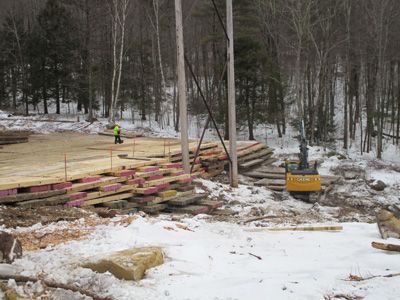
Overcoming Conflict on the Right-of-Way
A news helicopter circled overhead as the two ambulances left the job site. The deputy sheriff looked at the superintendent and said, “Tell me again, how did this happen?” The superintendent removed his safety glasses with a sigh as he surveyed the devastation left behind by the 345-kV contact. “Well, we had to set up […]