Articles
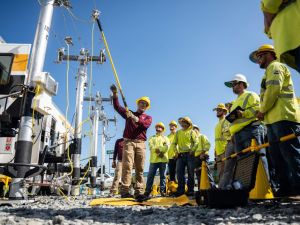
The Evolution of Personal Protective Grounding: Part 2
Part 1 of this article began with discussion of the first American power systems, when lineworkers initially encountered the hazards of working on de-energized lines (see https://incident-prevention.com/blog/the-evolution-of-personal-protective-grounding-part-1/). This led to early personal protective grounding (PPG) efforts using trial and error. We also reviewed Charles Dalziel’s contributions toward a greater industry understanding of dangerous current levels.
In short, Part 1 confirmed the need for PPG as a key lineworker safety precaution. In this second and final part, we will review…
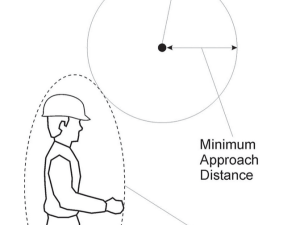
‘Avoid Contact’: Correctly Understanding the MAD Without a Distance
For decades, air has been used to effectively and inexpensively maintain phase-to-phase and phase-to-ground clearances of overhead distribution and transmission power lines and electrical equipment. Air’s extremely high resistance offers excellent protection against the passage of current. The greater the nominal system voltage, the greater the air gap required to prevent a flashover and short-circuiting.
Due to its dielectric properties, air is also used to protect workers from electric shock. Incident Prevention readers who work in the electric utility industry are familiar with the term…
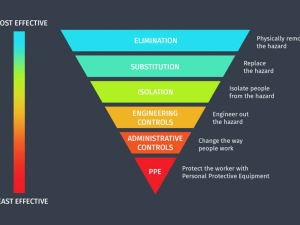
Rethinking Arc Flash Labels for PV Projects
Arc flash labels are a commonplace requirement for photovoltaic (PV) projects. However, arc flash studies and the resulting labels are sometimes treated as check-the-box exercises. In my experience as an engineer, I have found that questions are rarely asked regarding integration of PV arc flash labels into a safe, effective operations and maintenance plan. Engineers who charge by the man-hour can generate these labels all day long, yet they aren’t the ones tasked with donning PPE to perform hot work. A fundamental link is missing in terms of safety.
Essentially, arc flash labels provide e…
Safety By Design: Implementation and Operation
The first four articles in this six-part series outlined the significance of an organizational safety management system (SMS) that involves all employees. They emphasized effective risk mitigation through a well-developed plan for continuous improvement, with a focus on human and organizational performance.
This article highlights critical operational processes that must be thoroughly assessed and refined to support organizational safety. Every operational unit must take proactive ownership of its safety protocols and practices, actively integrating safety measures into all aspects of its…
Addressing the Elephant in the Room
There is an elephant in the room that plays a role in the safety culture of our industry. That elephant needs to be exposed, even though it’s going to be tough to do.
Based on a less-than-official count, 12 to 14 lineworkers have lost their lives on the job over the past six months. The estimate is “less than official” because no dependable central recordkeeping authority exists other than OSHA, and OSHA can’t post an incident until they have either closed the investigation or formally cited the employer.
Some of you reading this have experienced a co-worker being killed on the job. In…
Accuracy Above All: Authoring Articles for iP Magazine
For over 17 years, I have had the distinct privilege of writing for Incident Prevention magazine. I am genuinely honored that iP continues to publish my articles. My first column was about the four principles of distribution cover-up. At last count, I had written and submitted more than 100 articles over the years. During that time, many of my industry associates have also expressed interest in contributing to the magazine. To them and anyone else who wants to share their industry knowledge, I have and will always recommend contacting Kate Wade, iP’s editor, at kwade@utilitybusinessmedia.com…
October-November 2025 Q&A
Q: We hear lots of opinions about whether a lineworker can lift a hot-line clamp that has a load on it. There is a rule that says disconnects must be rated for the load they are to break. We’ve been doing it forever. Are we breaking an OSHA rule or not?
A: We have answered this question before, but it won’t hurt to revisit it and use this opportunity to explain how OSHA analyzes a scenario to determine if it’s a regulatory violation. Most objections to operating a hot-line clamp (HLC) under load are based on 29 CFR 1910.269(l)(12)(i), which states that the “employer shall ensure that devic…
Verbal and Physical Triggers
Think before you act.
That may be the single best piece of timeless wisdom we ever receive, especially when it comes to safety. And while it’s a simple concept, it’s not always our natural response, potentially presenting difficulties during job execution and task performance.
Keeping in mind that safety tools are designed to give us time to think, focus our attention properly and help us maintain positive control of our tasks, we must identify actions and conditions that indicate the need for them. These actions and conditions are verbal and physical triggers that can be used as remind…
Mistakes Are Inevitable: Choose to Invest in Recovery Capacity
When past winters were settling in, my family always took comfort with homemade cocoa. Last winter, one instance of preparing the hot beverage turned into a lesson about the nature of mistakes and the importance of planning for them. As my children worked together in the kitchen, one of my older daughters inadvertently spilled cocoa on one of her favorite sweaters. I stepped in, ready to help, and decided to soak the stained sweater in our utility sink as part of the cleaning process.
Filling the sink took longer than anticipated, so I left the room to tend to another task – and briefly lo…
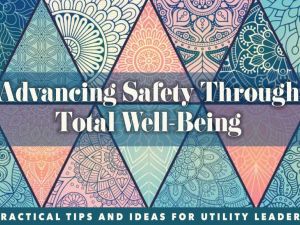
Advancing Safety Through Total Well-Being: Practical Tips and Ideas for Utility Leaders
Over the past 50 years, the electric utility industry has developed and implemented robust engineering controls, detailed work procedures and focused training to reduce injury and fatality rates among workers. However, the total well-being of the worker is another critical safety factor that utility organizations often don’t address.
Well-being encompasses physical health as well as mental, emotional and social dimensions that can significantly influence an individual’s capacity to make sound decisions, maintain situational awareness and successfully mitigate risks. Workers bring their who…
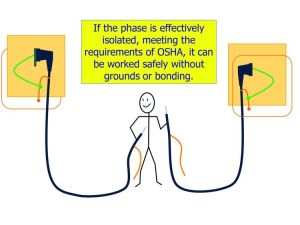
Equipotential Grounding for URD Work
I have written about grounding for the protection of employees numerous times in Incident Prevention magazine, addressing both the law and other issues. Let’s begin this installment with the understanding that “grounding for the protection of employees” – which is the phrase OSHA uses – means establishing an equipotential zone or EPZ. The purpose of grounding is to trip circuits. Grounding for the protection of employees can only be assured if it is arranged in an equipotential manner, preventing the worker from being exposed to a hazardous difference in potential. That’s the bottom line, and…
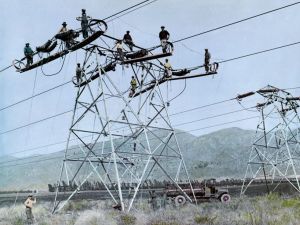
The Evolution of Personal Protective Grounding: Part 1
Personal protective grounding, or PPG, is arguably the most critical safety procedure affecting contemporary lineworkers. Over time, it has evolved to include numerous significant elements that contribute to the success of today’s comprehensive methods and procedures.
To adequately address these elements, this article will be presented in two parts. Part one, which you are now reading, covers PPG’s early years. Part two – scheduled to be published in the October-November issue of Incident Prevention – will cover the critical testing and development that led to the methods and procedures cu…
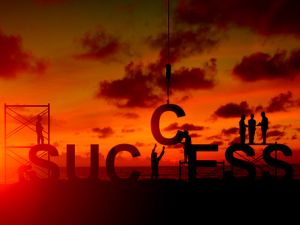
Safety By Design: Human and Organizational Performance
The first three articles in this six-part series addressed the critical nature and value of an organizational safety management system (SMS) that engages all employees and effectively mitigates risks through a developed plan for continuous improvement. This article focuses on human and organizational performance (HOP), an operational philosophy that utility organizations must incorporate into their SMS to achieve organizational safety success.
Over the years, traditional safety programs have primarily focused on managing employees, often overlooking the crucial systems designed to support…
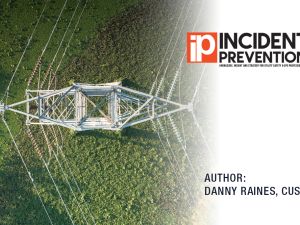
Clearing Up Confusion About Host-Contractor Relationships
In my consulting work, I’ve found there is some industry confusion regarding the relationship between a host utility and an independent contractor company. To help provide clarity, I’m going to kick off this installment of “Voice of Experience” with an overview of each party’s obligations from an OSHA perspective.
A contract employee performs work covered by a signed agreement between the host utility and the contractor company. The host’s construction coordinator must work with contract employees on the host’s system. The host must also provide training for the tasks contract employees ar…
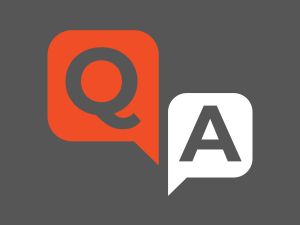
August-September 2025 Q&A
Q: If a crew is setting a steel pole between energized phases (69 kV), would the 3.29-foot minimum approach distance found in OSHA Table 6 apply, or should we defer to the 15-foot clearance?
A: Setting poles is new construction that OSHA covers in 29 CFR 1926.960, Table V-5, “Alternative Minimum Approach Distances for Voltages of 72.5 kV and Less.”
There is cover rated up to 72 kV phase to phase, so for a 69-kV system, cover can be used. Without cover, an electrical crew can use the 3.29-foot MAD for phase to ground. If cover is not used and a conductive object could enter the electrica…