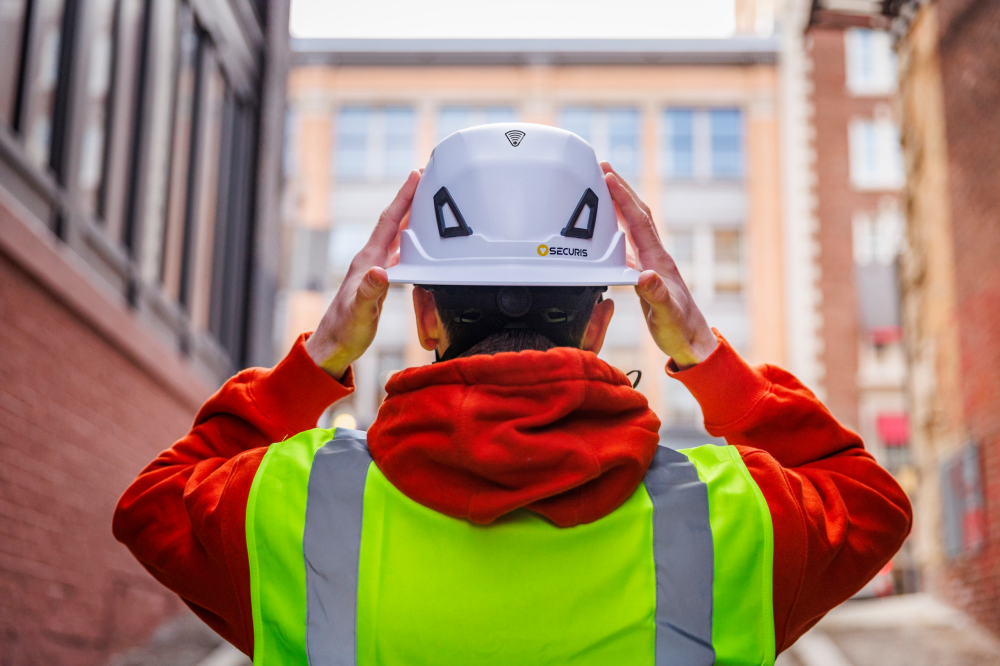
Industrial Helmets with Smart Safety Technology
Twiceme Technology, the digital safety standard for jobsites and adventures, has named Securis, a Velotec Sports industrial head protection brand, as its latest PPE partner. Securis will integrate Twiceme’s smart safety technology into its entire product line, enhancing safety for industrial workers and streamlining organizational safety management. Velotec Sports introduced the Securis brand in 2023 after […]
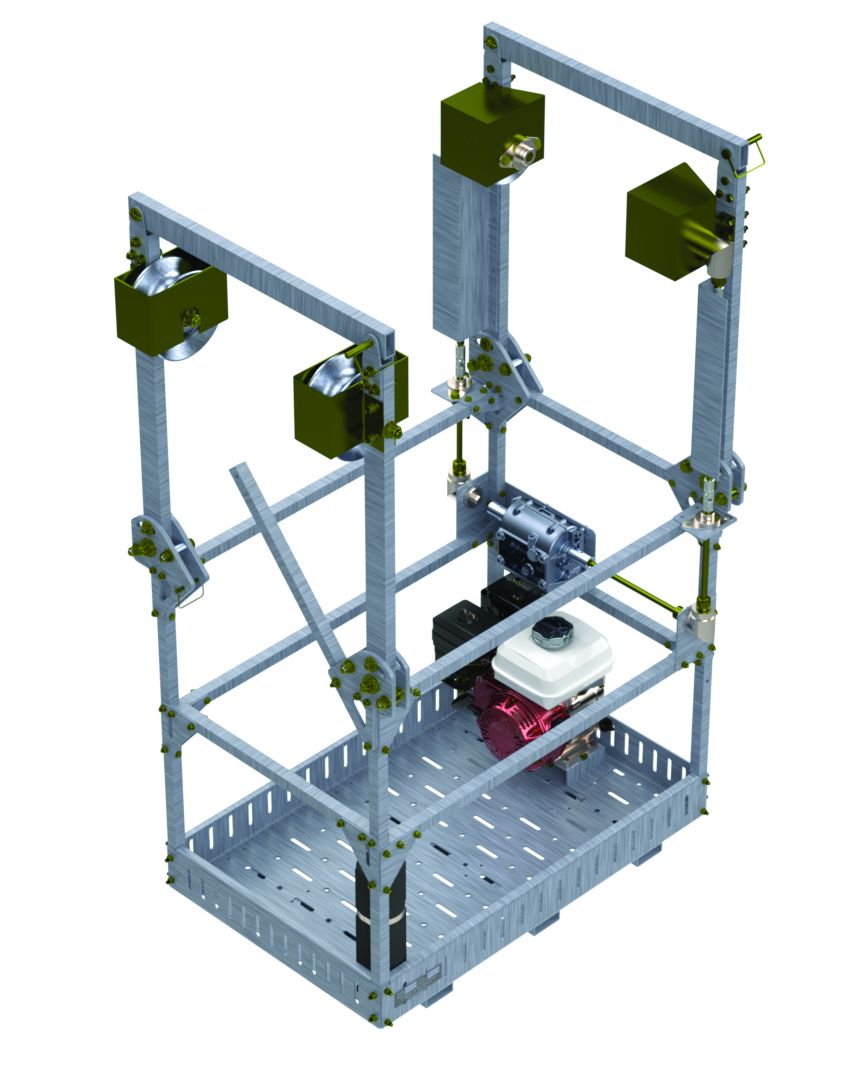
Double Bundle Line Cart
LineWise now offers a Horizontal Double Bundle Line Cart, available in a gas-powered or non-powered version. Designed for use on horizontal bundles spaced 18 inches apart, the new line cart offers a safe, specially engineered mobile platform for performing line inspection and maintenance on transmission lines. The Horizontal Double Bundle Line Cart offers a 400-pound […]
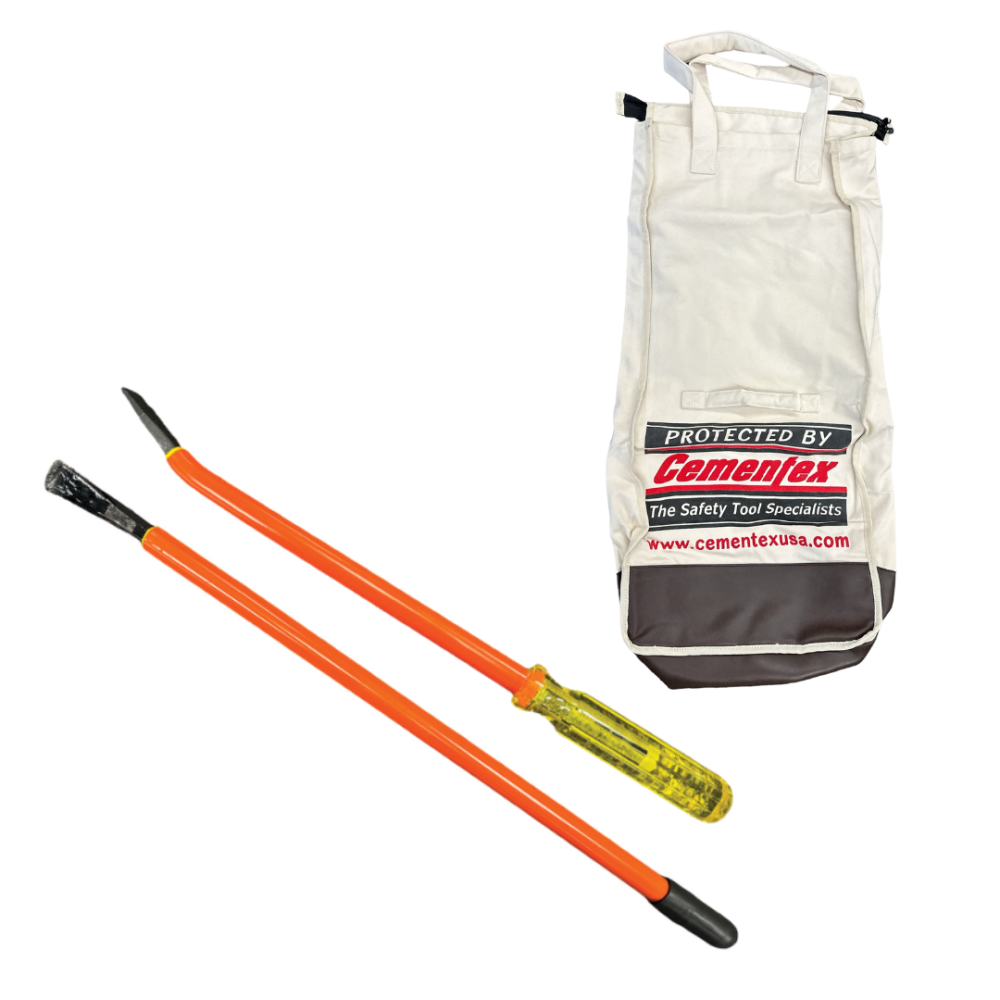
Double-Insulated Pry Bars
Cementex’s double-insulated pry bars, engineered with the company’s industry-leading insulation technology, provide the leverage required to pry open whatever is being worked on while maintaining a barrier against electrical hazards. The signature orange-over-yellow insulation offers clear visual safety indication, allowing users to both quickly identify wear and maintain compliance with stringent safety standards. Manufactured in […]
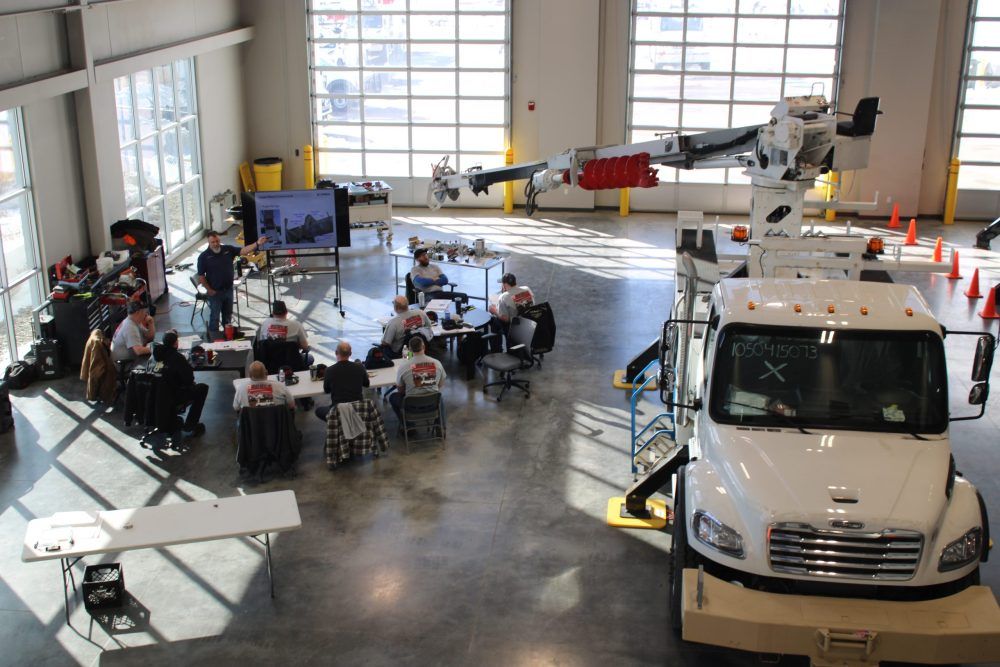
Customizable Training and Tech Tips
Terex Utilities offers a variety of training opportunities that can be customized to fit customers’ needs. Training available to service personnel includes both hands-on and online opportunities. Maintenance training workshops are for mechanics working on Terex digger derricks and bucket trucks. Subjects and activities covered in these workshops may include understanding and using load charts; […]
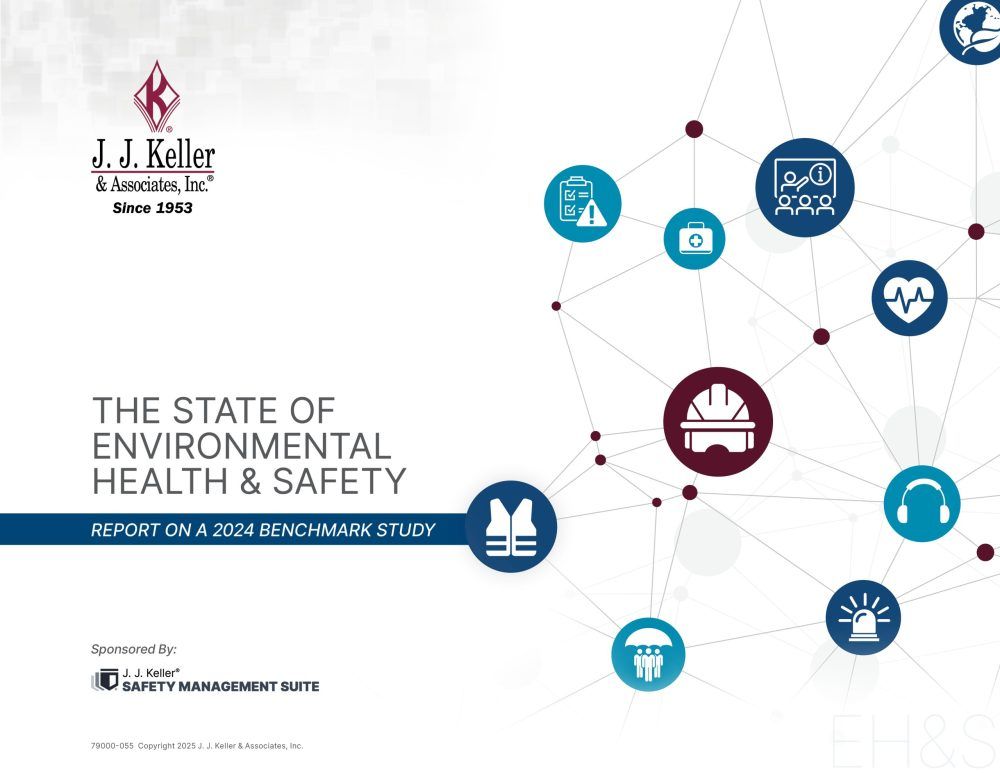
Benchmark Study on the State of EHS
J. J. Keller & Associates Inc. recently released a report for its inaugural “State of Environmental Health & Safety” benchmarking study, conducted by the J. J. Keller Center for Market Insights, the company’s collaborative research arm. The study is aimed at gaining a deeper understanding of how safety professionals perceive safety within their organizations and […]
Utility Safety Podcast: Deep Dive: Bucket Truck Safety: OSHA Standards and Other Considerations Written by Danny Raines, CUSP
In this episode, we unpack the vital safety standards, OSHA regulations, and field-tested insights that govern bucket truck operations in the electric utility industry. Based on the article “Bucket Truck Safety: OSHA Standards and Other Considerations” by Danny Raines, CUSP, we dive into key differences between Class A and Class B trucks, daily control tests, […]
Silencing the Noise: Creating a Culture of Actionable Safety and Synchrony with Bill Martin, CUSP
In this episode of our Actionable Safety series, host Nick talks with Bill Martin and Kate Wade about moving beyond “safety noise” to create real, lasting change on the job. They dive deep into achieving buy-in through synchrony, overcoming defensiveness, and translating safety theory into real-world practice. With stories from climbing Mount Kenya to lessons […]
Utility Safety Podcast: Deep Dive: Bucket Truck Safety: OSHA Standards and Other Considerations Written by Danny Raines, CUSP
In this episode, we unpack the vital safety standards, OSHA regulations, and field-tested insights that govern bucket truck operations in the electric utility industry. Based on the article “Bucket Truck Safety: OSHA Standards and Other Considerations” by Danny Raines, CUSP, we dive into key differences between Class A and Class B trucks, daily control tests, […]
5 Core Components of a Well-Developed Storm Response Plan
Electric utilities are part of the backbone of modern society, providing essential power to homes, businesses, emergency services providers and more. But this critical service is vulnerable to extreme weather events that can cause massive disruptions, damage infrastructure and jeopardize public safety. Due to the frequency and severity of such events, it is more important […]
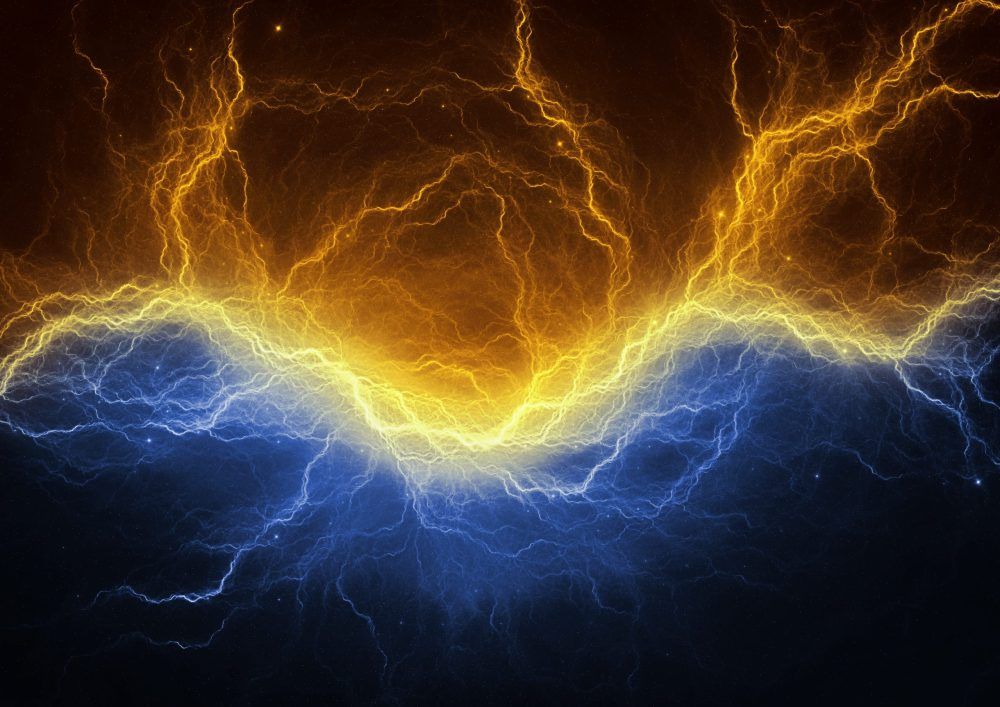
Variabilities in Electrical Arc Flash Protection
Rather than overcomplicating PPE decisions, invest time in safety through design to minimize the likelihood of an arc event.
Accuracies are synonymous with safety and science. While many perceive that electrical safety needs to be highly exact, this article aims at creating awareness of why sticking to the basics is effective. But before we delve into variability in electrical engineering, safe electrical work practices and electrical PPE, here is a brief story my second-year […]
Industrial Helmets with Smart Safety Technology
Twiceme Technology, the digital safety standard for jobsites and adventures, has named Securis, a Velotec Sports industrial head protection brand, as its latest PPE partner. Securis will integrate Twiceme’s smart safety technology into its entire product line, enhancing safety for industrial worker…
Double Bundle Line Cart
LineWise now offers a Horizontal Double Bundle Line Cart, available in a gas-powered or non-powered version. Designed for use on horizontal bundles spaced 18 inches apart, the new line cart offers a safe, specially engineered mobile platform for performing line inspection and maintenance on transmission lines.
The Horizontal Double Bundle Line Cart offers a 400-pound capacity with a single person occupancy limit, and it includes a foldable seat for operator comfort. Constructed of strong, lightweight aluminum alloy, the cart is bolted together, so there are no welded seams to crack. For ad…
Double-Insulated Pry Bars
Cementex’s double-insulated pry bars, engineered with the company’s industry-leading insulation technology, provide the leverage required to pry open whatever is being worked on while maintaining a barrier against electrical hazards. The signature orange-over-yellow insulation offers clear visual s…
Customizable Training and Tech Tips
Terex Utilities offers a variety of training opportunities that can be customized to fit customers’ needs. Training available to service personnel includes both hands-on and online opportunities. Maintenance training workshops are for mechanics working on Terex digger derricks and bucket trucks. Su…
Benchmark Study on the State of EHS
J. J. Keller & Associates Inc. recently released a report for its inaugural “State of Environmental Health & Safety” benchmarking study, conducted by the J. J. Keller Center for Market Insights, the company’s collaborative research arm. The study is aimed at gaining a deeper understanding of how safety professionals perceive safety within their organizations and the overall state of safety in today’s workplaces.
Conducted from November 18 to December 2, 2024, the online survey was open to individuals responsible for environmental health and safety. The study reflects J. J. Keller’s…
Utility Safety Podcast: Deep Dive: Bucket Truck Safety: OSHA Standards and Other Considerations Written by Danny Raines, CUSP
In this episode, we unpack the vital safety standards, OSHA regulations, and field-tested insights that govern bucket truck operations in the electric utility industry. Based on the article “Bucket Truck Safety: OSHA Standards and Other Considerations” by Danny Raines, CUSP, we dive into key diff…
Silencing the Noise: Creating a Culture of Actionable Safety and Synchrony with Bill Martin, CUSP
In this episode of our Actionable Safety series, host Nick talks with Bill Martin and Kate Wade about moving beyond “safety noise” to create real, lasting change on the job. They dive deep into achieving buy-in through synchrony, overcoming defensiveness, and translating safety theory into real-w…
Utility Safety Podcast: Deep Dive: Bucket Truck Safety: OSHA Standards and Other Considerations Written by Danny Raines, CUSP
In this episode, we unpack the vital safety standards, OSHA regulations, and field-tested insights that govern bucket truck operations in the electric utility industry. Based on the article “Bucket Truck Safety: OSHA Standards and Other Considerations” by Danny Raines, CUSP, we dive into key diff…
5 Core Components of a Well-Developed Storm Response Plan
Electric utilities are part of the backbone of modern society, providing essential power to homes, businesses, emergency services providers and more. But this critical service is vulnerable to extreme weather events that can cause massive disruptions, damage infrastructure and jeopardize public saf…
Opinion
Industrial Helmets with Smart Safety Technology

Kate Wade
Double Bundle Line Cart

Kate Wade
Double-Insulated Pry Bars

Kate Wade
Customizable Training and Tech Tips

Kate Wade
Video
Industrial Helmets with Smart Safety Technology
Twiceme Technology, the digital safety standard for jobsites and adventures, has named Securis, a Velotec Sports industrial head protection brand, as its latest PPE partner. Securis will integrate Twiceme’s smart safety technology into its entire product line, enhancing safety for industrial…
Featured Topics
Industrial Helmets with Smart Safety Technology
Twiceme Technology, the digital safety standard for jobsites and adventures, has named Securis, a Velotec Sports industrial head protection brand, as its latest PPE partner. Securis will integrate Twiceme’s smart safety technology into its entire product line, enhancing safety for industrial worker…
Double Bundle Line Cart
LineWise now offers a Horizontal Double Bundle Line Cart, available in a gas-powered or non-powered version. Designed for use on horizontal bundles spaced 18 inches apart, the new line cart offers a safe, specially engineered mobile platform for performing line inspection and maintenance on transmi…
Double-Insulated Pry Bars
Cementex’s double-insulated pry bars, engineered with the company’s industry-leading insulation technology, provide the leverage required to pry open whatever is being worked on while maintaining a barrier against electrical hazards. The signature orange-over-yellow insulation offers clear visual s…
Customizable Training and Tech Tips
Terex Utilities offers a variety of training opportunities that can be customized to fit customers’ needs. Training available to service personnel includes both hands-on and online opportunities. Maintenance training workshops are for mechanics working on Terex digger derricks and bucket trucks. Su…
Benchmark Study on the State of EHS
J. J. Keller & Associates Inc. recently released a report for its inaugural “State of Environmental Health & Safety” benchmarking study, conducted by the J. J. Keller Center for Market Insights, the company’s collaborative research arm. The study is aimed at gaining a deeper understanding o…
Utility Safety Podcast: Deep Dive: Bucket Truck Safety: OSHA Standards and Other Considerations Written by Danny Raines, CUSP
In this episode, we unpack the vital safety standards, OSHA regulations, and field-tested insights that govern bucket truck operations in the electric utility industry. Based on the article “Bucket Truck Safety: OSHA Standards and Other Considerations” by Danny Raines, CUSP, we dive into key diff…
Industrial Helmets with Smart Safety Technology
Twiceme Technology, the digital safety standard for jobsites and adventures, has named Securis, a Velotec Sports industrial head protection brand, as its latest PPE partner. Securis will integrate Twiceme’s smart safety technology into its entire product line, enhancing safety for industrial workers and streamlining organizational safety management.
Velotec Sports introduced the Securis brand in 2023 after a decade in outdoor protective headgear and will embed Twiceme chips into the shell of its Type II safety helmets. By partnering with Twiceme, Securis will enable its users to upload work-related documents and medical information to speed certification tracking and response times in the case of an emergency. First responders can immediately access critical data – including personal contacts, medical conditions and allergies – by scanning the Twiceme symbol on the back of a helmet during emergencies.
Securis helmets with Twiceme will be available starting in July 2025. www.securisprotect.com, www.twiceme.com
Double Bundle Line Cart
LineWise now offers a Horizontal Double Bundle Line Cart, available in a gas-powered or non-powered version. Designed for use on horizontal bundles spaced 18 inches apart, the new line cart offers a safe, specially engineered mobile platform for performing line inspection and maintenance on transmission lines.
The Horizontal Double Bundle Line Cart offers a 400-pound capacity with a single person occupancy limit, and it includes a foldable seat for operator comfort. Constructed of strong, lightweight aluminum alloy, the cart is bolted together, so there are no welded seams to crack. For added safety, the line cart has a toe board around the floor and two safety bars positioned over the conductors.
Customers can choose a gas-powered or non-powered version of the line cart. The non-powered model requires workers to manually pull themselves along the conductors to move the cart. The gas-powered version includes a 3.2-horsepower gasoline engine to propel the cart. The engine drives two of the cart’s four wheels and comes with a throttle control to adjust speed. It has a transmission with reverse and two forward gears for excellent control.
An optional tow bar assembly is offered for the non-powered Horizontal Double Bundle Line Cart. This helps to maintain balance and alignment of the cart on the conductors. It also allows lineworkers to pull the cart from ground level using a tow rope. https://line-wise.com
Double-Insulated Pry Bars
Cementex’s double-insulated pry bars, engineered with the company’s industry-leading insulation technology, provide the leverage required to pry open whatever is being worked on while maintaining a barrier against electrical hazards. The signature orange-over-yellow insulation offers clear visual safety indication, allowing users to both quickly identify wear and maintain compliance with stringent safety standards.
Manufactured in the U.S. with both American and globally sourced materials, Cementex double-insulated pry bars are tested to 10,000 volts and rated for live use up to 1,000 VAC/…
Customizable Training and Tech Tips
Terex Utilities offers a variety of training opportunities that can be customized to fit customers’ needs. Training available to service personnel includes both hands-on and online opportunities. Maintenance training workshops are for mechanics working on Terex digger derricks and bucket trucks. Subjects and activities covered in these workshops may include understanding and using load charts; performing periodic inspections; troubleshooting PTO issues; changing the direction of a pump; and performing a leakage test on outriggers. The Master Mechanic Learning Center is an online training platform covering inspection, dielectric principles, hydraulic troubleshooting and other service issues.
Since 2012, Terex Utilities has published Tech Tips to answer frequently asked questions. Tech Tips address a single repair or replacement topic with step-by-step instructions and graphics. In 2024, customers downloaded these tips almost 15,800 times. Terex Tech Tips are continuously updated and expanded, so the company recommends checking back often to see what’s been updated. Topics cover a wide range of content, with some specific to Terex Utilities models and others that are more general in nature. Sign up for Tech Tips and stay updated on the latest Terex workshops and training on the company’s website. www.terex.com/utilities/en/support/technical-support/tech-tips/sign-up
Benchmark Study on the State of EHS
J. J. Keller & Associates Inc. recently released a report for its inaugural “State of Environmental Health & Safety” benchmarking study, conducted by the J. J. Keller Center for Market Insights, the company’s collaborative research arm. The study is aimed at gaining a deeper understanding of how safety professionals perceive safety within their organizations and the overall state of safety in today’s workplaces.
Conducted from November 18 to December 2, 2024, the online survey was open to individuals responsible for environmental health and safety. The study reflects J. J. Keller’s ongoing mission to protect people and the businesses they run because, by identifying the challenges faced by EHS professionals, it becomes possible to foster improvements within the industry. www.jjkellersafety.com/resources/whitepapers/ehs-benchmark-study-2024
Industrial Helmets with Smart Safety Technology
Twiceme Technology, the digital safety standard for jobsites and adventures, has named Securis, a Velotec Sports industrial head protection brand, as its latest PPE partner. Securis will integrate Twiceme’s smart safety technology into its entire product line, enhancing safety for industrial worker…
Double Bundle Line Cart
LineWise now offers a Horizontal Double Bundle Line Cart, available in a gas-powered or non-powered version. Designed for use on horizontal bundles spaced 18 inches apart, the new line cart offers a safe, specially engineered mobile platform for performing line inspection and maintenance on transmi…
Double-Insulated Pry Bars
Cementex’s double-insulated pry bars, engineered with the company’s industry-leading insulation technology, provide the leverage required to pry open whatever is being worked on while maintaining a barrier against electrical hazards. The signature orange-over-yellow insulation offers clear visual s…
Customizable Training and Tech Tips
Terex Utilities offers a variety of training opportunities that can be customized to fit customers’ needs. Training available to service personnel includes both hands-on and online opportunities. Maintenance training workshops are for mechanics working on Terex digger derricks and bucket trucks. Su…
Industrial Helmets with Smart Safety Technology
Twiceme Technology, the digital safety standard for jobsites and adventures, has named Securis, a Velotec Sports industrial head protection brand, as its latest PPE partner. Securis will integrate Twiceme’s smart safety technology into its entire product line, enhancing safety for industrial worker…
Double Bundle Line Cart
LineWise now offers a Horizontal Double Bundle Line Cart, available in a gas-powered or non-powered version. Designed for use on horizontal bundles spaced 18 inches apart, the new line cart offers a safe, specially engineered mobile platform for performing line inspection and maintenance on transmi…
Double-Insulated Pry Bars
Cementex’s double-insulated pry bars, engineered with the company’s industry-leading insulation technology, provide the leverage required to pry open whatever is being worked on while maintaining a barrier against electrical hazards. The signature orange-over-yellow insulation offers clear visual s…
Customizable Training and Tech Tips
Terex Utilities offers a variety of training opportunities that can be customized to fit customers’ needs. Training available to service personnel includes both hands-on and online opportunities. Maintenance training workshops are for mechanics working on Terex digger derricks and bucket trucks. Su…
Most Popular
Consider new testing data before making a final determination.