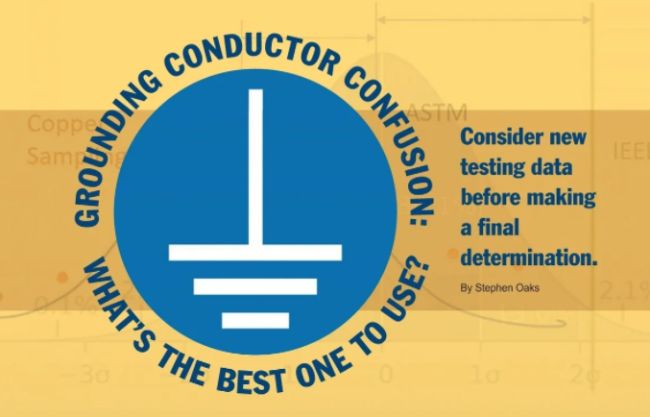
Grounding Conductor Confusion: What’s the Best One to Use?
Consider new testing data before making a final determination.
Consider new testing data before making a final determination.
Proper grounding is both a life-and-death matter and an operational imperative. But many questions remain about grounding. Some of the most frequently asked include:
- Why do some designers, utilities and contractors use one type of grounding conductor while others use a different type?
- If copper and aluminum carry power through transmission and distribution lines, then why not use them everywhere, including for grounding?
- What is the best grounding conductor?
The grounding conductor selection process should include both of the following steps:
- Use the recommendation from Section 9 of the National Electrical Safety Code, which states that choosing a conductor to satisfy a ground fault will be sufficient for lightning as well. This is due to the much shorter duration of the lightning’s high-current pulse.
- Remember that fault currents travel quickly compared to typical AC continuous currents. High current at high speed creates substantial heat. Such heat must be managed by the conductor more efficiently than typical transmission and distribution line currents.
Commonly Used Conductors
Now, let’s examine the conductors most commonly used for grounding in the U.S.: copper; copper over welded steel; aluminum; aluminum conductor steel reinforced; and galvanized steel. We’ll begin with the least frequently used conductor and move on to those more frequently used.
Galvanized Steel
Galvanized steel wire and cable are low cost but correspondingly low in conductivity. The galvanized material (zinc) melted onto steel does not last due to micro cracks, pitting that allows moisture to separate the zinc from the steel and could set up stray voltage conditions. This cable isn’t a good conductor and isn’t recommended for grounding in utility applications.
Aluminum Conductor Steel Reinforced
What about aluminum strand wrapped over steel strand? This is universally used in the transmission of high voltage throughout the U.S. However, that’s because we send relatively low-current continuous alternating current through these power lines. For grounding, we need a conductor that can manage rapid temperature rise in 500 milliseconds – likely the longest fault clearing time – or fewer. Aluminum’s melting point is 1,220 degrees Fahrenheit, while copper’s is 1,980 and steel’s is 2,500. In most power-conducting circuits, aluminum is electrically sufficient, but it does not handle the heat typically created by fault currents or lightning. Based on metal melting points, and considering the high heat created by high current, it makes more sense to select copper or copper over steel.
Copper-Clad (Welded) Steel
This bimetallic conductor has been in use since the 1930s for rural electrification. At that time, it was specifically utilized for its strength and to reduce copper reliance – World War II needs for copper in radios came first – in carrying power to farms. It is often considered a lower-grade grounding conductor compared to copper due to the IEEE 80 formula that is applied equally to both copper and copper-clad steel. This IEEE 80 formula, created in 1980 for lack of test data, is inappropriate since the two types of conductors are not the same. New fault-current testing performed at Powertech Labs in British Columbia has shown that one manufacturer’s copper-welded steel conductors outlast the IEEE 80 formula comparisons to stranded copper cable. I’ll address more on this recent testing a little later in this article.
All-Copper Stranded Cable
This is the most common conductor used by utilities in the U.S. It’s interesting to note that the majority of Canadian utilities use copper-weld steel conductors – a bonding of copper laid on steel, producing a stronger conductor – and not solid copper for most of their grounding conductor applications. Copper stranded cable or wire has the electrical superiority and highest fusing current of the discussed conductors for the same-size conductor as copper-clad steel. It is for this reason that all-copper is frequently used by U.S. utilities. However, this does not consider longevity of use or what may be the better choice today, which I will further explain.
Q&A
Before we get to that, however, let’s first address the questions I listed at the beginning of this article and what can be learned from new fault-current testing.
1. Why do U.S. utilities use different grounding conductors instead of a single standard?
Often, the reason depends on prior experience, present concerns and conditions (e.g., theft and reliability), availability and/or cost. After World War II, the use of copper tended to be preferred due to its relatively low cost and good availability. However, starting in 2004, the price of copper began to increase, making it a precious, street-tradeable commodity. Copper also became a tradeable commodity on metals exchanges, which raised its price about another 30% beyond copper’s industrial value. When the Great Recession occurred, the price of copper went from about $2 per pound to $4.50 per pound. This led to a significant and dangerous problem of copper theft from utility structures throughout North America. As recently as October 2021, copper hit a new high of $4.73 per pound.
This high price of copper and the associated theft probability have created a renewed interest in alternatives to all-copper grounding wire/cable. For these reasons, I am predicting a shift away from all copper to copper-weld steel for most utility grounding applications (i.e., poles and substation grids/risers). Please note that I realize this statement may be confusing for readers. My intent is to suggest that not all manufacturers will achieve the same results that were seen at Powertech Labs. Copper-weld steel comes in a form where copper strands are combined with steel, but for the purposes of this article, that is not the material recommended for grounding. The copper strand added to steel strand that you are thinking of is for rural electric use, not grounding. It is too much of a cost increase for the strand combination when copper bonded on steel is less costly and doesn’t require separated copper strands to provide current-carrying capability.
2. If aluminum-clad steel-reinforced cable is readily available, then why not use it for grounding, too?
As indicated earlier, aluminum has a significantly lower melting point than copper. This becomes particularly concerning with lightning, which is much higher current at a much higher frequency and therefore more likely to melt the aluminum. This makes aluminum a poor grounding conductor, compromising the reliability of the circuits where it is installed. Regardless of availability, aluminum or ACSR should not be used for grounding applications.
3. What is the best grounding conductor for utility applications?
This must be answered so designers or operations personnel install a long-term, reliable and safe grounding conductor. Proper grounding is a critical component of any circuit and needs appropriate consideration. Let’s establish criteria for optimizing a grounding conductor:
- Longevity of service has become more important lately due to some utility system failures. Replacement maintenance has become increasingly expensive and tends to be delayed as risk management versus cost issues are addressed at some utilities. This suggests the need for component/material longevity in the design specifications for new circuits.
- Reliability goes hand in hand with longevity. We need a conductor that is performance-ready over the service life duration.
- The conductor should be electrically sufficient to carry a fault current and a lightning strike. Sizing the conductor usually solves for this issue. However, all too often, operations staff oversize all copper wire/cable to feel safe with fault currents. This not only costs more, but it puts the circuit at risk of theft and breakage. Such a decision may be regretted when grounding is not available due to broken or missing wire/cable.
Testing Data
To better understand how to select the optimal grounding conductor, let’s review some of the testing done at Powertech Labs. At present, they have the highest current-capable test facility in North America.
Over a three-year period starting in 2018, Powertech tested various copper wire/cable and copper-weld steel conductors at fault-current levels according to IEEE 80 guidelines/tables. Various connectors were tested with the conductors. In most cases, the fuse point was at the connector-to-conductor interface. A further discussion outside of this article could examine the connector-to-conductor interface issues that resulted from this test sequence.
Following are two key learning points from the Powertech Labs testing:
- The fuse limits and cross-sectional areas for all copper conductors were significantly less than the IEEE 80 Table 6 values that engineers expect and use in their calculations. This suggests designers should allow for extra safety margins from IEEE Table 6 due to lower actual fuse currents in today’s available solid copper. See Figure 1.
- IEEE 80’s formula for copper and copper-clad steel is not applicable to copper-clad steel. One belief for the longer fusing currents of copper-welded steel is that the steel’s melting point is a “heat sink” to the copper outer layer. Adding copper’s electrical conductivity to steel’s melting point provides longer-than-expected fault-current-carrying times. See Figure 2 for IEEE 80 test data results and Figure 3 for visual proof of a conductor exceeding the IEEE 80 limit during a test (intact, albeit white hot).
The electrical tests aside, we also need to consider other factors, such as strength and theft. Strength of a conductor can be an issue if it is placed under the soil’s surface (e.g., in substation grids). The rolling of heavy trucks has broken conductors, substantially changing the grid resistance. Wind and earth movement forces on pole connections suggest that torsional forces can weaken, breaking conductors over time. The worst grounding conductor is the one that is not connected. So, strength of conductor should be considered for longevity. Note the table in Figure 4 that compares copper to copper-weld-steel break loads.
After decades of use, copper-weld steel has been an effective theft deterrent, as it remains where copper has been removed by thieves. If the possibility of theft exists on a circuit or grid, copper-weld steel offers a long-term likelihood of being there when a fault or lightning occurs.
So, finally, to answer the question about the best conductor, I leave it to each operation’s responsible person to make the final determination. There is now more test information to consider about all copper and copper-clad steel for grounding conductors. Today, doing it the “same old way” is not necessarily the best or safest long-term strategy.
About the Author: Stephen Oaks, B.S., MBA, has been a subject matter expert on ground conductors and copper theft for the past 14 years. His 30-year career in technical product applications engineering has included wire/cable, batteries, graphics software and semiconductors. Oaks has presented at CEATI, IEEE, NREA and various safety conferences. He is an independent contractor for his company, Pacific Management Partners Ltd.
- February – March 2022 Q&A
- From My Bookshelf to Yours: ‘Extreme Ownership’
- Using PPE to Bolster Safety Resilience
- Safety Advancements in the Line-Clearance Industry
- ANSI A92.2: 2022 Changes and Training Requirements
- Grounding Conductor Confusion: What’s the Best One to Use?
- The End of a Career
- Safety Signs and Sign Policy