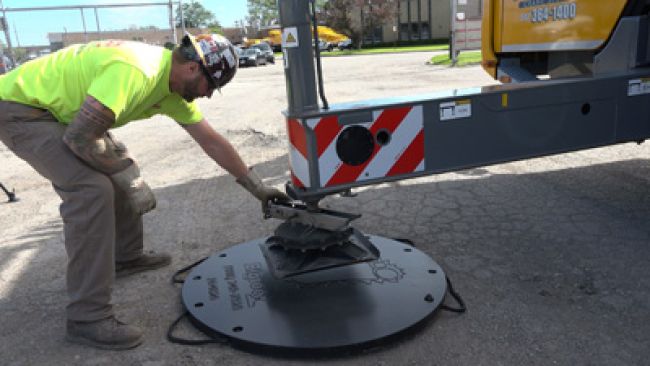
The Safe Use of Outrigger Pads for Equipment Stability
An outrigger pad is a safety tool that can be used with any equipment that has outriggers, down jacks or stabilizers. It is a must for stability when a piece of equipment – such as a crane – lifts loads or personnel aloft. This article will provide an overview of outrigger pads, including how to use them safely and what kinds of pads are available on the market today.
The Basics
Outrigger pads are placed on the ground under the equipment’s outrigger, shoe, float or foot. The size and thickness of the outrigger pads to be used should be selected based upon the type of equipment, soil conditions of the work site and type of lift being performed.
When working with outrigger systems, it’s important to understand that the point of contact between an outrigger and the ground is quite small. Because of the pressure of the outrigger, the ground underneath may shift, be displaced or collapse if an outrigger pad is not used. If any of those things happen, there is the potential for the equipment to shift or tip the load, which could lead to the equipment toppling over. In fact, approximately half of crane lifting accidents are caused by improper use of outriggers.
Outrigger pads were created to stabilize equipment so that the ground below doesn’t shift and equipment doesn’t topple over. Stability is dependent upon the equipment’s footprint and center of mass. The footprint is the total area enclosed by the support structure of the equipment. The center of mass is the point at which the equipment would balance if it were set on top of a single point to support it. If the center of mass is on the edge of the footprint or outside of it, the equipment will topple. There are two ways to provide extra stability. The first is to use a counterweight to help shift the center of mass back over the footprint. The second is to make the footprint bigger with an extendable outrigger system.
All cranes have counterweights, but there is a limit to how heavy they can be due to transportation and setup considerations. As noted earlier, the ground can only sustain so much pressure before it gets displaced or collapses. Even if you can transport a crane to the work location, there is no guarantee the ground conditions will be stable enough to set up and hold the crane. Because of that, it is essential for the stability of the equipment to use retractable outriggers to extend the crane’s footprint. After deploying the outrigger system, installing outrigger pads underneath the outriggers will expand their point of contact with the ground and displace the pressure from the equipment through the outrigger pad to the ground.
Six Important Points
As with any safety tools, outrigger systems and outrigger pads must be used according to the instructions of their manufacturers. In addition, keep the following six points in mind when working with an outrigger system.
1. Proper setup and leveling are critical to the appropriate function of any style of outrigger system. The operator is required to follow the manufacturer’s chart regarding the allowable level and grade percentage when setting up the equipment. If the level is incorrect, the equipment’s lifting capacity will be reduced.
2. Prior to setting up, try to acquire recent soil conditions for the work area. Knowing the ground-bearing capacity will help workers determine what type of outrigger pad is the best fit for the equipment that will be used. OSHA 29 CFR 1926.1402, “Ground conditions,” states the following in paragraph 1926.1402(b): “The equipment must not be assembled or used unless ground conditions are firm, drained, and graded to a sufficient extent so that, in conjunction (if necessary) with the use of supporting materials, the equipment manufacturer’s specifications for adequate support and degree of level of the equipment are met. The requirement for the ground to be drained does not apply to marshes/wetlands.” Per 1926.1402(a)(2), “supporting materials” refers to blocking, mats, cribbing, marsh buggies, or similar supporting materials or devices.
For those who do not work in construction, ASME B30.5-3.2.1.5(i) regarding mobile and locomotive cranes states that “[b]locking under outrigger floats, when required, shall meet the following requirements: (1) sufficient strength to prevent crushing, bending, or shear failure; (2) such thickness, width, and length, as to completely support the float, transmit the load to the supporting surface, and prevent shifting, toppling, or excessive settlement under load …”
3. Check for current locates and know where utilities are overhead and underground. Maintain proper clearances around overhead power lines. It’s an absolute must to find out the known voltage of the overhead power lines and determine the minimum approach distance for qualified and unqualified personnel.
4. Outrigger pads must not be used to bridge any gaps or span any voids.
5. The maximum lift capacity of the equipment must be known, which includes understanding how to follow the load chart. Be sure to factor in not only the load being lifted but the rigging being used to lift the load as well. A key to safe lifting work is employing qualified personnel who know how to read load charts and have been trained to run the equipment. A strong job briefing prior to work also is a must.
6. Understand that different pieces of equipment have different outrigger systems. Workers will need to understand how to set up those systems on each piece of equipment they work with. Following are short descriptions of some common outrigger systems found on today’s equipment.
- An out-and-down or vertical pressure outrigger system is very common on 40-ton cranes and above.
- A-frame or 45-degree outrigger systems are common with bucket trucks and digger derricks.
- You will find combination units with both A-frame and out-and-down outrigger systems on many boom cranes, from 30 tons on down.
- Down jacks typically are found on trailers and heavy-haul equipment.
A Rule of Thumb
A known ground-bearing capacity may not be available for every job site or equipment setup. And in a number of industries – including line work, tree trimming and some crane work – determining the capacity may not be practical, particularly during storm response work. To address the issue, I suggest following a rule that I learned from my father and have been using for more than 20 years. An outrigger pad should be at least three times the square surface area of the outrigger shoe or float, provided you are working on Grade A soil conditions. As soil conditions worsen, continue to create a bigger footprint using outrigger pads and cribbing. After the equipment is set up and level, or within the manufacturer’s grade tolerance, and outrigger pads have been deployed, make a dry run of the boom. Use a spotter to ensure the outrigger pads are not shifting, sliding or sinking into the ground. Then check to see that the equipment is still level or within grade. If any issues are identified, stop and stow the boom. Now is the time to add cribbing, blocking or more outrigger pads. The pads should be built to support the maximum load of the pick or lift; to displace the weight of the equipment while keeping the equipment level; and to help the crew work safely.
A Variety of Pads
Outrigger pads are built in different lengths, widths, thicknesses and shapes. When it comes to shapes, there are pros and cons depending on what you choose. For example, because large square outrigger pads have a large surface area, they are not as easy to move around on the job site as round outrigger pads, which usually can be rolled into position by one person but have less surface area.
In terms of the materials used to build outrigger pads, I have found only three – American custom composite, premium birch and American steel – that I believe should be used when personnel are aloft or with any critical pick or lift with a load of 10,000 pounds or more.
American custom composite has 3,000 psi and maintains its value for a lifetime. This material is engineered to perform in the most extreme conditions and typically will outlast the equipment it is being used with.
Used in the field since 1991, premium birch has been battle-tested in the harshest conditions with some of the largest equipment. These outrigger pads have a typical life span of 10 years.
American steel crane mats are built with high-grade steel and will outlast the equipment they are being used with.
Conclusion
As with any tool of the trade for line construction and maintenance, outrigger pads must be inspected before each use or setup. After the setup, perform a dry run with a spotter to inspect the outriggers and outrigger pads. Check the equipment level, and then you’re ready to move forward with the job.
About the Author: Jeff Steiner is co-owner of Bigfoot Construction Equipment (www.outriggerpads.com). Prior to leading the company, he served in the U.S. Army and spent nearly 20 years as a journeyman lineman. Reach him at jeff@outriggerpads.com.