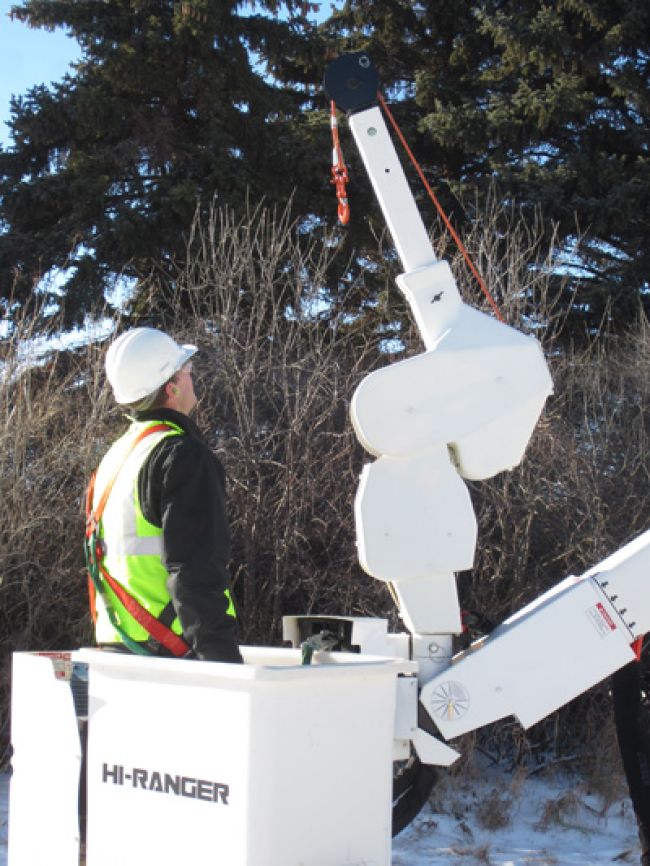
Best Practices for Using Your Aerial Device Jib to Handle Transformers
When it comes to lifting transformers, aerial devices equipped with jibs are one of the handiest tools available to lineworkers. Compared to old methods for transformer replacement – which required workers to climb the pole and use a pulley to manually lift the transformer – using a jib is safer, easier and more productive.
Most aerial devices sold to companies in the utility industry are equipped with jibs. However, not all jibs are the same, and the user should evaluate the type of work to be done when choosing the equipment for the job. Consider whether the tasks are construction or maintenance work on distribution or transmission lines. Before dispatching to the job, workers should know how the lines are situated relative to where the vehicle can be located. In addition, the weight of the load will determine the capacity of the aerial device and jib needed.
In the remainder of this article, we will provide an overview of the four key areas that inform good practice for using jibs: knowing your equipment, inspecting your equipment, knowing the load and understanding proper setup.
Know Your Equipment
There are many different styles of jibs with varying capacities available on different boom and platform configurations, including side mount, underslung, end mount and jibs that rotate with the platform. There also are fixed-length jibs, jibs that can be manually re-pinned to provide various extensions, and jibs with one or more sections that are hydraulically extendable. Some units are designed with the load line above the jib boom and some are below. Other jibs are equipped with sheaves that allow only non-overcenter lifting, while some can do either overcenter or non-overcenter lifting.
Jibs may or may not be insulating (i.e., capable of providing electrical insulation). Terex Utilities does not make insulating jibs, but if you have one that is insulating, the jib must be tested in accordance with OSHA 29 CFR 1926 and ASTM F711 requirements for hot-line tools. Even so, Terex Utilities does not recommend considering jibs as insulating because the jib travels on the unit in a position that collects road debris. Although most jibs are made from nonconductive material, lifting loads can subject them to shock loads, which can cause cracks in the resin surface. Those cracks can absorb contaminants. In addition, as the jib travels in and out on wear pads or rollers, dirt gets embedded in the surface, increasing chances of the jib becoming conductive. Finally, the jib typically is not treated as a hot-line tool for cleaning and inspecting before use. Likewise, the winch line must be considered conductive.
Some jibs or jib-and-winch assemblies can be removed. If the jib is not used daily, and it can be removed, this is a good practice to protect it. Removing the jib has the added benefit of providing crews the ability to get equipment into tighter spaces. However, if the entire jib/winch is removed, any metal that is exposed needs to be covered with nonconductive (insulating) material to reduce the chance of inadvertent electrical contact.
Inspect Your Equipment
The user is required to perform all inspections and maintenance of the jib, winch line, hook and slings at intervals stated in operator’s manuals. Daily inspections of the entire aerial device are required before use. As it relates to the jib, visual inspections must be performed on the jib, its support structure, the hook and safety latch, and the load line.
On the jib, look for damaged components; damage to the gel coat; cracks or corrosion; excessive wear; and any loose, deformed or missing bolts, pins, fasteners, locking devices or covers.
The synthetic rope winch line must be inspected daily for deterioration that could result in loss of strength. Always follow the criteria provided in manuals, from the rope manufacturer or from the Cordage Institute (www.ropecord.com). The following conditions – among others – should be reported to a qualified person to determine if the rope should remain in service: excessive roughness; glossy areas indicating heat damage; flat areas or bumps/lumps indicating internal core damage; frayed strands; discoloration associated with chemical contamination; and stiffness due to embedded dirt or shock-load damage.
Any hooks showing defects must be discarded. It is not permitted to make field repairs of hooks by welding or reshaping them. Among the defects to look for in a daily inspection are a damaged or missing safety latch, cracks or distortions, and corrosion on the hook nut, if equipped.
Know the Load
Knowing how to read the load chart is critical for the safe use and long life of the aerial device. Load charts provide the maximum capacity of the aerial device depending on the boom and jib or load-line positions. These values are not suggestions; they are absolutes. If exceeded, the stability or strength of the unit is compromised. Likewise, the winch capacity cannot be used as an indicator of allowable lifting capacity; the winch must lift the maximum capacity, which may greatly exceed the capacity at your working position. The operator must know the load weight and the boom configurations required through the entire load travel path. The load chart provides capacities at various boom angles, load radii or jib extensions. As the load is positioned farther from the boom tip, the capacity is reduced in most cases. Note that the load chart is based on the maximum capacity of the platform and gives the allowable load on the jib. The load chart will tell if unused platform load can be applied on the jib up to the maximum allowable jib load. Not all aerials will allow this increase in jib load if slimmer workers are in the bucket.
Most aerials have the same capacity over the side as well as the back. If there are restrictions, the information will be provided on the load chart or other labels at the operator station. Terex Utilities designed its Load Alert system to help operators know if the boom condition is near capacity. It monitors and analyzes the truck’s jib and basket capacity and provides visible and audible alarms when an overload has been detected. A monitor display will read “overload” when one occurs, and the background will turn red. The display also shows the actual load amount and will warn when the operator is approaching maximum capacity.
There are a lot of differences in the size, weight and shape of transformers. A 3-kVA transformer weighs just 50 pounds, while higher-capacity transformers can weigh upward of 1,000 pounds. New transformers will include the weight on the unit identification tag, but when removing old transformers, the weight of the load may be unknown. It is a good idea to refer to the brand name, model and type of core to identify the weight. This information usually is available from the transformer manufacturer.
Understand Proper Setup
Set up the truck in a way that positions the jib next to the load and pole. For example, units with side-mounted jibs can be positioned to the side of the pole, but for a unit with a jib that is at the back of the bucket, you’ll likely position the jib alongside you. The farther the jib is extended, the less capacity you will have.
When lifting with a jib, it is important to follow the manufacturer’s limitations on setup. Some aerial devices must be level before lifting the booms from the rest, even when set up on a slope. Failure to properly level may cause the unit to tip or roll over. Level the truck using cribbing. It is possible to stack multiple outrigger pads to gain height as needed. Always position the outrigger foot in the center of the outrigger pad.
Finally, Terex Utilities recommends always using an insulating section or link when working with a jib. The conductor lifter or insulating link must be treated as a hot stick. The clear-span distance of the insulating tool depends on the voltage. Users should follow OSHA 1926.950 to maintain the required minimum clear insulation distances.
Summary
Lifting transformers is one of the everyday tasks conducted by utility crews. Aerial devices equipped with jibs have made this work easier and more productive. In some cases, aerial devices with material-handling capability also can reduce the amount of equipment needed on the job site. Most importantly, they can improve safety when used properly. The next time your crew is tasked with changing out a transformer, consider best practices for equipment selection, inspection, setup and load handling.
About the Authors: Roger Crom began his 40-year career in the electrical utility industry as a lineman in South Dakota. An accident in 2006 that put him in contact with 7,200 volts has fueled his passion for electrical safety training. Crom later became coordinator of compliance and education services for South Dakota Rural Electric Association, and in 2017 he retired from his position as manager of loss control for SDREA. During retirement, he has continued to work as a safety, training and education consultant for the power transmission industry.
Jim Olson, P.E., is senior product engineer for Terex Utilities (www.terex.com/utilities). He has a mechanical engineering background and has been working in design and engineering for aerial devices and digger derricks since 1986. In addition, Olson is registered by the International Fluid Power Society as a mobile hydraulic mechanic and hydraulic specialist and is currently chairman of the NCCCO Digger Derrick Exam Management Committee.
- Wood Pole Fall Restriction Device
- Project Management Safety Certification Program
- Best Practices for Using Your Aerial Device Jib to Handle Transformers
- The Hierarchy of Incidents and Learning: Part II
- Mother Nature vs. FR/AR Clothing
- Arc Flash and Face Masks
- Opinion: Looking to the Future During an Unprecedented Time
- June-July 2020 Q&A
- Motivators: To Improve Performance, Understand What Drives Your Behavior