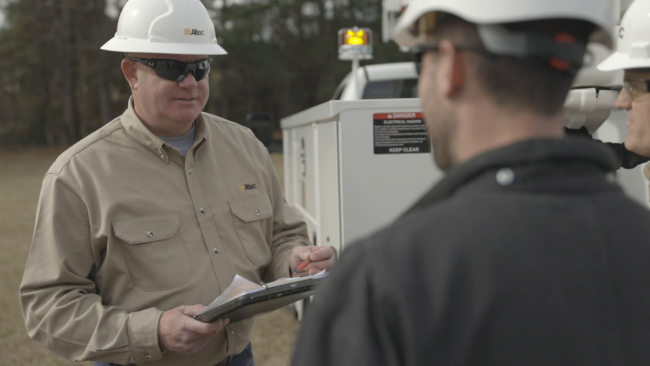
ANSI A92.2: 2022 Changes and Training Requirements
Here’s what owners and operators should know about upcoming updates to the standard.
Here’s what owners and operators should know about upcoming updates to the standard.
Updates are coming to the ANSI A92.2 standard, titled “American National Standard for Vehicle-Mounted Elevating and Rotating Aerial Devices.” Your most common piece of powered equipment soon will have new or revised requirements for design, manufacturing, testing, training and operation. These new requirements go into effect in August of this year.
First, let’s cover some of the most notable changes, and then we’ll look at some often misunderstood training requirements.
Manufacturers must now consider the structural effects of operating on slopes up to the unit’s maximum allowable slope, not just at 5 degrees. This change follows the industry trend toward units capable of operating beyond the traditional 5-degree limit.
Along with higher unit slope capabilities come changes in stability testing requirements. Units must still be tested on a 5-degree slope in the direction of least stability. However, if the unit has allowable slope limits greater than 5 degrees, it must also be tested on its maximum allowable slope.
Controls for positioning the platform must have an unlocking or enabling device to prevent inadvertent movements.
ANSI has also added a requirement that the platform level must remain within 5 degrees of initial leveling while the boom structure is raised or lowered.
Synthetic rope must have an average breaking strength of at least five times the working load. This addition mirrors the requirement in A10.31, the ANSI standard for digger derricks.
Category C and D units with a conductive, articulating lower boom above rotation must have a chassis insulating system. This refers to the fiberglass section of the lower boom. Although not previously required, most if not all manufacturers have already installed them.
If a unit has upper controls with high electrical resistance, those controls shall be tested periodically at a one- to 12-month interval. This was previously a “should be tested” requirement.
The entity performing periodic electrical tests must document each test and provide a certified report to the owner upon request. ANSI A92.2 now contains a specific listing of reportable test details.
Manufacturers now have the option to provide one set of manuals in an electronic format. They must still provide at least one printed set along with the electronic copies.
Updated Ownership Requirements
Updating ownership records with the manufacturer is very important. This gives the manufacturer current contact information for sending equipment bulletins. Dealers and installers have a newly added responsibility to notify the manufacturer of the name and address of the new owner when a unit changes hands. A further requirement exists for dealers or installers to notify the new owner of their responsibilities under A92.2.
ANSI A92.2 now defines a “service entity” as a person or entity whose business is inspecting, testing, maintaining or repairing aerial devices or mobile units. This is significant because service entities also have requirements under the standard, including the responsibility to properly train maintenance personnel to repair and operate the equipment.
A major structural inspection shall be performed after the first 15 years of service, and every 10 years after that, or as directed by the manufacturer. This is a significant new requirement for owners. The major inspection must include a periodic inspection, level-surface stability testing, and a detailed inspection for structural deformations, broken members and cracked welds. Any damage must be repaired or replaced before returning the unit to service.
There has long been a requirement for operators to use appropriately rated and tested insulating devices when handling energized lines. It is a common misconception that fiberglass jibs are insulating. Unless jibs are rated and tested for the voltages involved, they must be considered conductive. For this reason, A92.2 requires the use of insulating devices – such as link sticks or insulating jib inserts – for this work. These devices provide protection from energizing the boom tip through the jib and winch rope.
In the upcoming revision, this requirement now falls on both the user and the operator. The user is the entity with custodial control of the unit, whether that’s an employer, dealer, installer, lessee, lessor or operator. Adding the user to this responsibility expands accountability beyond the operator for performing live-line conductor-handling tasks safely.
A primary purpose of ANSI A92.2 is to standardize industry safety requirements, so when purchasing any A92.2-compliant device, you have assurance that a basic standard of safety is designed into each unit. This ultimately protects the personal safety of everyone in contact with the unit.
Training Requirements
As manufacturers innovate new features, such as fall protection lanyard detection sensors and advanced boom load monitoring systems, operators need to know how those features work, what protections they may offer, and how to inspect and test them before use. Unfortunately, many operators use new equipment without proper training. Lack of operator familiarity with complex equipment leads to increased risk for everyone on the job site.
Nearly everyone in the utility industry knows that training is important, yet the vast majority of A92.2 equipment owners have no idea where the operator training requirements come from. Fortunately, that’s easy to answer.
First, OSHA. They require employers to properly train employees to recognize and avoid hazards. However, OSHA provides very little detail on what constitutes proper training for A92.2 aerial devices. By interpretation letter (see www.osha.gov/laws-regs/standardinterpretations/1992-10-23-0), OSHA explained that they “use the ANSI requirements to help establish what the industry practice is in regard to operator qualifications.” Translation: Employers need to look to ANSI A92.2 for operator training requirements that comply with OSHA’s requirement to train. A92.2 defines operator training requirements and details what training topics to cover when training someone for the first time or when training someone on a new piece of equipment.
ANSI A92.2 lists two main training categories. The first is general training. All operators must receive general training, which includes classroom information about safety topics and hazards related to operating aerial devices. General training also requires an operator to demonstrate hands-on proficiency in actual operation under the direction of a qualified person. Although not specified, general training should be refreshed periodically, and a five-year cycle is consistent with other industry certifications.
Familiarization is the second training category. Operators must be familiarized with any unfamiliar units before operating them. A manufacturer’s in-service demonstration is not operator training. A typical in-service does not satisfy familiarization requirements and certainly does not fulfill the wider general training requirements.
Through proper familiarization, operators learn about the location of the manuals, purpose and function of all controls, safety devices and unit operating characteristics. Of course, this also includes learning about any new features. To complete their familiarization, operators must achieve proficiency through actual operation of the unit.
ANSI A92.2 also directs retraining if an accident or a near-miss occurs, or when a training need is observed. It would be appropriate to follow the general training requirements when retraining an operator since a qualified person must evaluate their proficiency in safe unit operation.
Simply put, general training is an “every operator, once” requirement and familiarization is an “every operator, specific units” requirement. OSHA expects to see documentation that both types of training occurred, and they will certainly expect the training program to meet the ANSI standard.
Filling the Training Gap
Many employers already have trainers on staff who handle new-hire and recurring training. As apprentices come in from formal, entry-level training programs, these in-house trainers may focus on teaching essential work methods and other qualification skills, leaving an unintentional gap in their basic operator training program. Assumption or ignorance fills this gap and creates eventual hazards for all involved.
Often, the void in basic operator training programs is only recognized when an accident occurs and the resulting investigation reveals that an untrained operator did not know or follow the manufacturer’s guidance for operating the equipment. There are industry training resources that can help fill the gap. Some manufacturers offer in-person general training and specific-unit online familiarization courses to get operators started on the right training path. Train-the-trainer courses can also assist employers in developing their own qualified person to direct in-house operator training.
Conclusion
Although ANSI A92.2 training requirements are the same industry-wide, each employer must craft a compliant solution that fits their needs. The manufacturer is a good resource to help build the solution since A92.2 requires manufacturers to develop and offer training materials that aid in operating the unit. If you have an Altec unit, you can visit www.altecsentry.com. Whether you’ve got questions about training or the A92.2 standard in general, feel free to contact the Altec Sentry training department to start the discussion.
About the Author: Phil Doud is the Sentry safety program manager for Altec. Reach him at phil.doud@altec.com.
- February – March 2022 Q&A
- From My Bookshelf to Yours: ‘Extreme Ownership’
- Using PPE to Bolster Safety Resilience
- Safety Advancements in the Line-Clearance Industry
- ANSI A92.2: 2022 Changes and Training Requirements
- Grounding Conductor Confusion: What’s the Best One to Use?
- The End of a Career
- Safety Signs and Sign Policy