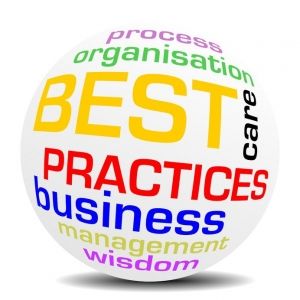
Using Best Practices to Drive Safety Culture
During the years that I have worked with power companies as a safety and training consultant, I have seen a lot of missed opportunities to create a strong safety culture. Most of us have a keen eye for what the next best practices for compliance may be, and we are good at implementing them, but we don’t always utilize their true potential to drive change, drive culture and really make a difference.
Let’s take a look at an example and walk through the missed opportunities to which I am referring. The written job briefing is a well-known best practice that is often used, but do all of yours consist merely of a check-the-box-and-sign-it type of document, or do they require the crew to perform comprehensive job hazard analyses? Is anyone checking to see that the job briefings are not only complete, but that they are done to a standard that equips and stretches your crew to recognize and mitigate the hazards on their jobs? When you visit a crew on a job site, do you ensure a briefing has been completed before the work begins? Do you go back to the job briefing in the case of an incident or accident and review it while analyzing the root cause? If failure to recognize and mitigate a hazard resulted in an incident or accident, are you coaching your employees to avoid a similar situation in the future? Are you disciplining them for failing to meet the standard you set for the job briefing?
Setting the Standard
The old model of a foreman sitting on a job with five to 10 guys all day long is not how most of us operate anymore. A foreman may have as many as six two-man units scattered across multiple counties. Therefore, we must equip our employees to be stronger safety leaders of their own groups. They must have proper hazard recognition and mitigation planning skills. We are pushing more and more responsibility for on-the-job decision-making down to crew levels to achieve the operational readiness and effectiveness we need. However, training alone will not help us reach this goal. It’s imperative that we drive change and culture by setting a standard for performance and assigning true ownership in these responsibilities. Once this standard has been defined, you must hold employees accountable for performance that adheres to the standard. It is only then that we really begin to reap the true benefits of the best practice.
In regard to accountability, I feel it is necessary to point out that it is very important to ensure that when we coach or discipline, we do it in a way that is edifying to the employee and the company. Discipline that is not intended to teach people and improve their skills is retribution, and it will take away from all the work you have done up to this point. When you have a team that is committed and actively engaged, it can be difficult at times to not let your emotions become frayed when you have to modify unwanted behaviors. You have to work hard in this area to control emotions. It is sometimes helpful to allow the leadership team to spend a day or two analyzing the situation to determine the best approach to discipline.
It Starts at the Top
So, where do we begin the journey to creating a team that is actively engaged and focused on driving a strong safety culture? It must start at the top and work its way down, utilizing executives, managers and frontline supervisors. Equipping frontline supervisors with the proper knowledge and tools, in my opinion, is where the need is the greatest since they will be the ones to deliver and sell these safety culture concepts to the crews.
Utility industry organizations, including Incident Prevention (www.incident-prevention.com) and the Utility Safety & Ops Leadership Network (www.usoln.org), offer direction, networking, and training for supervisors and safety leaders. I encourage you to find and utilize these educational opportunities to help equip your workers. You and your leadership team need to act as a cohesive unit to build a strong safety culture at your company and on your crews. When you and your leadership team work together to convey clear and precise expectations, and when you are committed, actively engaged and foster an environment of ownership and accountability, you become a force that will change and drive a strong safety culture. Let’s get serious about saving lives. Stay safe!
About the Author: Tim D. Self, CUSP, is the director of operations for the Institute for Safety in Powerline Construction. He has more than 25 years of experience working as a lineman, trainer and safety manager.