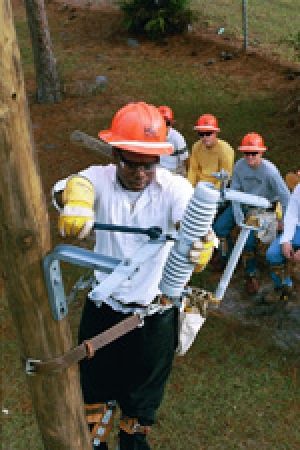
Formal vs. On-the-Job Training
I have been doing a lot of training and evaluation work over the past few years, and I have started to notice a trend. The workers who have had a formal in-depth training experience have a better perspective about the theories behind why they are performing certain tasks. Workers that are trained on the job are good at the tasks, but do not really understand why they perform the tasks that way.
The Formal Training Process
Let’s look at the training process that goes with a formal program. The worker is trained – via both classroom and hands-on training – on theories of electrical functions, work techniques and safety precautions. This process gives the worker a better understanding of line work in general. The program is structured to take a worker from zero to full knowledge. Since it is structured, the worker benefits from the experience of the people that were instrumental in assembling the course curriculum.
Now let’s look at on-the-job training (OJT) only. The worker is trained in the task they are going to perform. They are not exposed to classroom instruction. As such they have to rely on the experience and knowledge of the person instructing them. If the person who is instructing the worker has very little experience in line work, they can only bring the pupil to their level.
Where the Problem Lies
This is where the problem lies. In the evaluations I have performed, I find that the OJT worker does not understand many of the reasons why procedures are performed. For instance, they do not understand the phrase “second point of contact” while gloving primary voltage. When I see these situations during my evaluations, I try to coach OJT workers as to the reasons why we perform certain procedures. They have the intelligence to understand, but lack the proper information. People only break safety procedures for two reasons: either will or skill. Once I explain to them the whys of the procedure, they normally receive it well. The hardest ones to get onboard are the more senior people who do not want to accept new information. These are the “will” workers. They have been trained a certain way, and just do not want to follow the new procedure. This is because they only know the way they were taught. Their supervisors are also at fault because they do not enforce certain safety procedures. They may not understand the procedures either or they may put production above all else.
Do you see where this is going?
You can only teach to your level of understanding. Every fatality I have investigated revealed that at least three to five safety procedures or policies were broken. When interviewing the rest of the workers in the center, sometimes I find the entire workforce operates the same way. In most cases I find a lack of understanding.
To have an informed and safe workforce, employees must be trained. OJT is good for tasks, but the addition of basic theory, either classroom or computer-based, will make a more well-rounded worker. People will understand why certain procedures must be followed, and will be less likely to violate safety rules and procedures because of the additional training.
About the Author: Rick Tobey, CUSP, president of Tobey Safety Training and Consulting, has spent 46 years in the electrical line work business. He provides training across the country, and is an associate of the Institute for Safety in Powerline Construction and T&D PowerSkills. For more information, visit www.tobeysafety.com or send an email to tobey2@nehp.net.