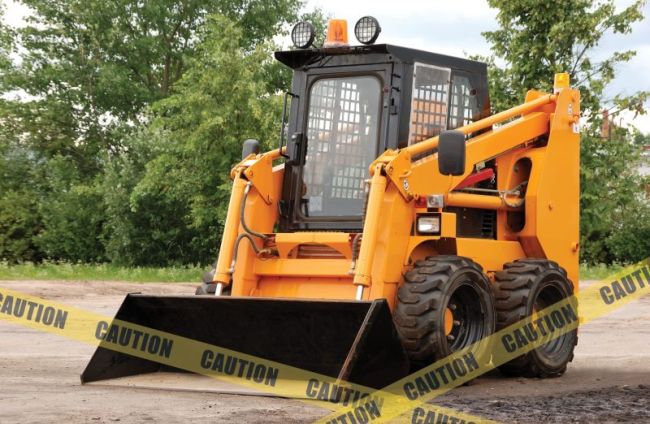
Skid-Steer Loaders: Hazard Awareness and Recommended Safety Practices
Training is an essential component of safely operating and maintaining these machines.
In 2009, OSHA published a safety and health information bulletin in part because of the seriousness of injuries that have occurred with skid-steer loaders (see www.osha.gov/sites/default/files/publications/shib011209.pdf). Similarly, NIOSH published an alert in December 2010 in response to the hazards and serious injuries that have occurred with these machines (see www.cdc.gov/niosh/docs/2011-128/default.html).
In their published documents, the two agencies aim to make employers and employees aware of the need to review and follow manufacturer instructions regarding proper use of skid-steer loaders. Both documents emphasize the importance of conducting training on the operation, inspection, maintenance and testing of the machine’s safety devices. This article also provides an overview of the hazards involved with the use of skid-steer loaders as well as recommended practices to keep employees and the public safe.
Risk Factors
When working with skid-steer loaders, workplace environmental risks include the material-handling method; pinch-point actions; overhead moving/falling objects; work surfaces; facility and work-site layout conditions; weather conditions; catch points; puncture, shear-point and flying-object actions; illumination; and sound level.
Human performance hazards include misjudgment; position inappropriate for the task; insufficient/lack of written work practices; equipment inappropriate for the operation; safety devices removed or inoperable; defective equipment used; unacceptable material-handling actions; and hazardous energy control procedures ignored.
The incident types most associated with skid-steer loaders have involved employees working near the machine; maintenance and repair; mounting/dismounting various attachments; operating, entering and exiting the machine; operator troubleshooting; passengers riding/standing in the bucket; training new operators; and fork attachments errors.
Regarding injuries, the vast majority are the result of bypassing safety interlock systems; failure to wear a seat belt; not controlling hazardous energy; failing to use the manufacturer’s safety bar; and backup alarms not functioning. Other common types include those incurred due to running over bystanders, entrapment and crushing. Entrapment of the operator can occur when a load rolls or drops into the operator compartment. Crushing can happen when the operator or helper is caught between an attachment and the frame of the skid steer. Injuries can also occur during rollover or tip-over incidents, if the front attachment falls off, or if improperly mounting or dismounting the skid steer. Additionally, note that pressurized hydraulic fluid is a hazard; the fluid could be accidentally injected into a person’s body.
OSHA Compliance and Universal Safety Features
A skid-steer loader is a versatile machine capable of utilizing many attachments for a variety of applications, from earthmoving to material-handling. Due to the machine’s versatility, note that the requirements of OSHA’s Powered Industrial Trucks standard (29 CFR 1910.178) do not specifically apply when using fork attachments.
When a loader is used in construction, OSHA 1926.21(b)(2) requires employers to instruct employees in the recognition and avoidance of unsafe conditions as well as the regulations applicable to their work environment to eliminate or control hazards.
In general industry, the skid-steer loader is covered by 1910.147 in situations where service and maintenance are performed that require compliance with OSHA’s control of hazardous energy (lockout/tagout) standard. Further, OSHA’s General Duty Clause can be imposed where there is a recognized hazard and the employer does not take reasonable steps to eliminate or mitigate that hazard.
The universal safety features of a skid-steer loader include the seat belt for operator restraint; a falling object protective structure (FOPS); a rollover protective structure (ROPS); an interlock control system; a lift-arm safety bar; and side screens. The seat belt prevents the operator from being thrown about inside or ejected from the skid-steer loader’s compartment. The FOPS and ROPS protect the operator from injuries due to falling objects and accidental rollovers. Most machines are equipped with a pulldown armrest (seat bar) that may be used to interlock the machine’s control system; this is not a substitute for the seat belt. The interlock control system typically consists of a safety interlock switch that activates to prevent inadvertent movement of the machine’s controls when the operator is not seated in the proper position. The lift-arm safety bar is intended to prevent unintentional dropping of the lift-arm during service and maintenance. Side screens provide the operator with protection by restricting the ability to put their hands, arms or head in the path of a moving lift-arm. The screens also block material from striking the operator. Additionally, a good skid-steer loader will have both a horn and backup alarms, which can warn people around the machine of its movement.
In the OSHA and NIOSH publications identified at the beginning of this article, analysis of fatalities revealed the following contributory factors: bypassing a variety of different safety interlock system components; failure to wear a seat belt; lack of proper hazardous energy control (i.e., not using the lift-arm safety bar); removal of side screens; and inoperable warning devices. Typically, employees were found pinned and crushed by lift-arms and attachments because controls were operable from a non-seated position. Some employees were also ejected and crushed during tip-overs or rollovers because they weren’t wearing their seat belt or exceeded the skid-steer loader’s operational capacity.
Recommended Safety Practices
To help minimize the hazards associated with skid-steer loaders, sufficient training is needed to make owners and operators aware of these machines’ dangers. Employers must communicate and effectively enforce work rules, including prohibiting employees from disabling or bypassing safety equipment (e.g., safety interlock systems). Further, employers must ensure compliance regarding hazardous energy control procedures, such as using the lift-arm safety bar, as well as ensure the safe practice of removing and replacing machine guarding components. Employers shall also mandate that employees use a seat belt at all times when operating a skid-steer loader and that they know the machine’s operational capacities.
The following are highly recommended safety practices to effectively operate and maintain skid-steer loaders:
- Train personnel on the proper inspection, use, maintenance and repair of skid-steer loaders.
- Train supervisory personnel to identify hazards, such as safety systems that have been bypassed or disabled or that require maintenance.
- Train operators and workers who service the loaders to read and follow the manufacturer’s operating and service procedures provided in the operator manuals and on the loaders’ warning signs.
- Develop a daily checklist of inspection necessities.
- Prior to operating the equipment, inspect the skid-steer loader to ensure that all safety systems are functioning properly.
- Always lower the bucket or attachment so that it is flat on the ground when entering and exiting the machine.
- Do not attempt to activate the skid-steer loader’s controls from outside the operator’s compartment.
- Do not leave the operator’s seat while the machine’s engine is running.
- Never attempt to activate the machine’s controls unless properly seated with the seat belt fastened and the seat bar lowered.
- The operator shall keep all body parts inside the cab while operating a skid-steer loader.
- Never modify, bypass, disable or override safety systems. Similarly, never operate equipment in which safety systems have been modified or are not working properly.
- Equipment with modified or malfunctioning safety systems should be taken out of service until repaired or replaced.
- Never permit riders on the skid-steer loader, in the bucket or attachment, or in the operator’s compartment unless the compartment is designed to accommodate a second person.
- Always keep bystanders a safe distance away from the work area.
- Use the machine’s horn to alert others near the machine.
- Stop operating the loader if a bystander or spotter is too close or has been lost from sight.
- Establish and follow a routine maintenance and inspection program in accordance with the manufacturer’s recommendations.
- Never attempt maintenance or other work while a lift-arm is raised without using an approved lift-arm support device.
- Attachments should be removed when lift-arms are raised and suspended for service and maintenance.
- Replace removed protective guards and shields after repairs or other service.
- For maximum stability, travel and turn with the bucket in the lowest position possible.
- Never exceed the manufacturer’s recommended rated load capacity for the machine.
- Operate on stable surfaces only.
- Avoid traveling across slopes; travel straight up or down with the heavy end of the skid-steer loader pointed uphill.
- Slow down in wet environments.
To minimize the occurrence and severity of injuries associated with skid-steer loaders, employers and employees must recognize and understand the hazards of operating this versatile machine. Employers and supervisors should ensure that proper inspection and maintenance of safety interlock devices is conducted regularly and that the willful bypass or disregard of those devices is not tolerated. In addition, operators should be trained in the control of hazardous energy, front- and rear-axle weight distribution, center-of-gravity concepts, rated operating capacity principles and the machine’s safety symbols.
Conclusion
Training is an essential component of learning safe machine operating principles. In addition to their operator and service manuals, some skid-steer-loader manufacturers offer videos that can assist in the development of a safe and effective operation training program. Manufacturers and their distributors may also offer safety and operational training.
OSHA and NIOSH have recognized the hazards associated with operating skid-steer loaders. Safe practices go a long way in minimizing potentially hazardous situations associated with the operation and servicing of these machines. The best practices to minimize operating risks are to ensure that the equipment is properly maintained; seat belts and interlocks work properly; operators and service personnel know the danger zones; employees know the machine’s limitations; and employers train on and enforce the safe operational rules. Proper training and holding employees accountable are essential aspects of a safe work environment.
About the Author: Charles Keeling, CUSP, is a 35-year safety professional in general industry and construction. He is also a certified New York State Workplace Safety Consultant. Keeling earned a bachelor’s degree in fire and emergency management and currently works with PSEG Long Island conducting safety and regulatory compliance duties. He also serves as the ASSP Region VIII metro area director. Reach him at charles.keeling@pseg.com.
- Solar Backfeed Safety on Distribution and Secondary Circuits
- An Experiment in Crew Member Engagement
- Skid-Steer Loaders: Hazard Awareness and Recommended Safety Practices
- Five Core Capacities for Sustainable Safety Excellence
- Switching and Tagging
- Ruling Spans and Proper Conductor Sag
- April – May 2024 Q&A
- Receiving Feedback