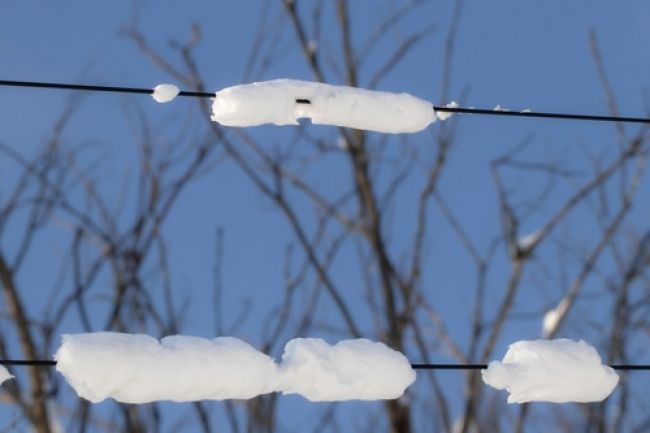
Ruling Spans and Proper Conductor Sag
The cold winter weather of recent months has prompted many conversations about proper sagging and tension on transmission and distribution conductors. Improper sagging and excessively high tension on conductors – past their rated breaking strength – have caused unscheduled system outages, but such outages can be avoided by using the correct loading factors. The system will not fail when the correct tension and sagging factors are used, even in the coldest air.
Before we talk about calculating proper sag and tension, I want to share some relevant personal history. I remember the days when I first entered this industry. That was prior to OSHA’s existence and before we had much of the information that we have today regarding properly sagging conductors. At the time, I had never heard of a “ruling span,” and I didn’t know how that affected the method of determining correct sag on conductors. The work direction I received early in my career was, “Get all you can, three more clicks and make it up.” Of course, I was working in the South, and rarely did it get cold enough to damage the system, even when we sagged conductors too tightly. Back then, the appearance of the sag was thought to be the most important part. If it looked good, it would work fine.
As time marched on, the conductors became larger, and the weather seemed colder each winter. Then things started happening that we couldn’t explain, and no one ever gave us the details of the science behind proper sagging.
For example, there were times when the temperature would drop to 10 degrees Fahrenheit or lower. Insulators would break, pole-tops would break on dead-end poles, and conductors would literally pull out of dead-end clamps. In January 1984, the temperature dropped to -5 degrees in Macon, Georgia. At 1 a.m., there was a “C” suspension with a 379-ACSR conductor on a 45-foot Class 3 pole that had a 4-inch curved washer pull through the pole. The pole broke and dropped all three phases in the middle of a highway. At the same time, I was on a trouble call a few miles away, and a set of 1200-amp gang switches on 750-AAAC conductor pulled the switch apart and dropped everything on the ground. Other trouble cases that night were also the result of improper sagging. All the reconductoring to larger conductors had occurred the summer before. The larger conductors were installed and sagged in July. The ambient temperature that July was always in the 90s, and the conductor sagged in at around 2,100 pounds.
Factfinding
So, what is the science behind the sometimes-destructive results of improper sagging and tension levels?
Well, what we were told back then – that “tight looks better” – was not actually the best-case scenario. In those days, I worked with linemen and supervisors who had no clue as to why all this was happening. They thought they knew how conductors should be sagged, but they never really understood the reasoning.
First and foremost, the size of the conductor, the length of the spans and the temperature the day the conductor is installed play an important role in how and at what tension the conductors are to be at final sag. Most of the previously mentioned failures were destined to occur at some time in the future; the only missing ingredient was the weather causing the conductors to fail due to improper installation.
We all want the system to look good after a job is complete. Improperly sagged conductors look ugly and can cause unnecessary outages. Today I see more conductors with too much slack or “baggy sag,” as it is sometimes referred to. I admit I still like to see a tighter pull.
Elevation of the total pull is another factor to consider. The final sag for equal tension may have to be made at both ends if the tensioner is set up on level ground, there is a mile or so of conductor to be installed, and the elevation changes near the beginning or end of the pull. This adds time to the job, but it is time well spent.
One example I can share dates back to when I was a training crew supervisor in the 1980s. A job we were working on involved installing 5,000 feet of 750 AAAC. I asked the crew to use a dynamometer to set tensions at the calculated pounds. It was about 85 degrees that day, and the tension strength was calculated to be around 1,200 pounds per phase conductor. The problem was that two-thirds of the pull was uphill, and the dead-end was a short downhill to an existing junction pole where we were going to tie the new circuit into the grid. Sagging occurred, and when we went to the other end (the short end), the sag was affected by the weight of the uphill pull. So, we had to catch off all three neutral and re-sagged phases to achieve the calculated tension. The short end was several hundred pounds off on the dynamometer. Also, the new conductor was underbuilt on existing transmission poles with wood poles in between to maintain around 250- to 275-foot spans of the conductor. We completed the job by adding 10% to the final sag calculation to make it look good, which did not exceed the total rated breaking strength of the 750-AAAC conductor. The 4/0 ACSR neutral always tends to look slack after calculations and initial sagging, so adjustments are needed for looks only. Personally, I hate to see curls still in the conductor after it is installed and in the air.
Conclusion
Most companies now have a specification book for overhead line construction, and articles can be found online that go into greater detail about the span length, temperature at installation and tension levels that should be applied to the final sag. The initial sag the day of the pull should be very close, and the final calculations should be made the next day and then verified using a dynamometer to ensure that they are correct. The “creep” back and forth in rollers/blocks will work itself out to near balance a few hours after the initial sag is applied. The articles I mentioned above offer much more explanation than we have space to detail here.
I dearly loved the training supervisor position for the few years I had that responsibility, and we turned out some excellent linemen from those crews. Most continued their career with the same company, and many are now finishing up careers as supervisors or engineering assistants.
In closing, one of the worst statements I see on social media and hear in other conversations is, “It will work, and I can’t see it from my house.” True craftspeople will take the time to do the work right, and when you drive past it in the future, the work will look the same as it did when it was installed. The circuit I mentioned earlier is still in place, and the sag is still as it should be today, some 30 years later. Again, it is worth the time to do it right.
About the Author: Danny Raines, CUSP, is an author, an OSHA-authorized trainer, and a transmission and distribution safety consultant who retired from Georgia Power after 40 years of service and now operates Raines Utility Safety Solutions LLC.
- Solar Backfeed Safety on Distribution and Secondary Circuits
- An Experiment in Crew Member Engagement
- Skid-Steer Loaders: Hazard Awareness and Recommended Safety Practices
- Five Core Capacities for Sustainable Safety Excellence
- Switching and Tagging
- Ruling Spans and Proper Conductor Sag
- April – May 2024 Q&A
- Receiving Feedback