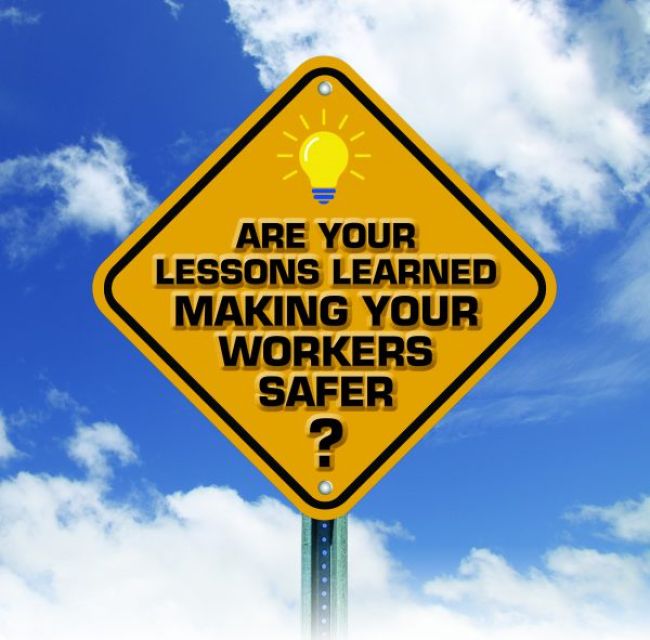
Are Your Lessons Learned Making Your Workers Safer?
Reports of the incident travel like lightning through the company. There are no real details yet, just a statement that at 10 a.m. today, an employee of The Big City Project was seriously injured on the job.
The event soon becomes the subject of coffee break conversations. “We’ve had a lot of serious incidents lately” seems to be the consensus. Upper management holds meetings to discuss the known details of the incident, the information to be released to the workforce and what they’re going to do to stop this trend. Even before the incident investigation can be completed, company-wide stand-downs are held and safety bulletins are created and distributed. The need to act now is present in everyone’s minds. It’s a palpable feeling amidst fear of the next serious incident that hasn’t happened yet.
During the incident investigation, pictures are taken, worker statements are collected, and interviews are conducted. The data is then interpreted, causal factors are identified, and a chart is created to show the flow of the incident. Eventually, lessons learned are drawn from the findings and published, and a process for distributing this information begins. There are still some lingering questions about the incident, but the deadline for the investigation to be completed has now come and gone. Everyone must continue to move forward and work with the information they were able to obtain.
Management develops a list of objectives based on the lessons learned – steps that they believe will lead to fewer future incidents. They’ve done the same thing in the past when they’ve seen trends and have made some progress. Long, bulleted lists of proper methodologies and situational behaviors are generated. Weekly and monthly management meeting agendas are modified to include safety moments, with the intent of creating urgency to remedy the causes of these incidents.
After this flurry of activity, months pass without a serious injury. Meetings are now starting with praise for the diligence of the workforce in curbing the incidents that were occurring. The data shows repeat incidents were on the rise, but now they are tapering off.
But is the reduction in incidents and serious injuries really due to the company’s mitigation efforts? Or is something else at play?
Understanding the Fundamental Attribution Error
As humans, we often attribute our successes or failures to the outcomes that occur after we apply a strategy or process. This is called the fundamental attribution error. Let me give you another example. There’s a story I’ve heard about a flight instructor who believed – based on his personal experience – that praise made his students perform worse while correction made them do better. Every time the flight instructor praised a student for executing an exceptionally good landing, their next landing would be worse, or so it seemed. Every time he corrected a student after performing a poor landing, the next one would be better. However, the reality is that if you study the total number of a student’s landings, that student’s performance typically turns out to be about average. Some of their landings will be better than others, and some will be worse. In statistics, this is called regression to the mean. If a student makes an exceptional landing, regression to the mean dictates that the student’s future landing will likely not be as good.
And so it goes with our safety record. Most of us have an average number of incidents at the company we work for. This includes spikes of repeat incidents and times with fewer incidents. Because of the fundamental attribution error, we often believe that what we do to mitigate future incidents is what’s causing our safety record to improve. And maybe that is the case. But sometimes, regression to the mean will end the streak of incidents because statistically that’s what happens. There is a good chance doing nothing would have led to the same result.
Of course, this does not mean we should do nothing. We should still take action. The easy approach when incidents occur is to discipline or suspend employees, or to otherwise add fear as a driver to change behavior. However, it has been proven that creating fear reduces incident reporting by employees – but not incidents. So, as we investigate and respond to incidents, we must ensure that our responses are meaningful.
For example, more isn’t always better. I have read long laundry lists of things we should pay attention to in order to avoid a repeat incident. These admonitions are based on the belief that to solve the problem, all we have to do is tell workers to be better. But keep in mind that these lists of items are based on the belief that the true root causes of the incident were identified. If there are unanswered questions during an incident investigation, questions that were never asked or any unknown crew dynamics, it is likely that our lessons learned are at least partially speculation. We often continue to find out more about an incident long after the root cause is officially determined.
A More Thoughtful Response
A more thoughtful and targeted response can be much more effective than information overload. Human beings can only hold about five to seven items at a time in our working memory, so a long list of information on a safety bulletin cannot be retained in full. Trying to read and retain such a list can also cause us to drift and think of other, unrelated things. Alternatively, a safety bulletin with only three or four items on it is easily remembered if the information is presented on its own – not with other pages of information that could be distracting.
Further, when we arrive at an incident’s root cause and document our lessons learned, careful thought about actionable lessons produces better results. Final root causes such as “lost focus and concentration, complacency and disregard for PPE” seem like focused conclusions. But without an actionable response, the lessons are just words. An example of actionable lessons learned might be adding a requirement for a worker aloft to verbally communicate with a responsible party below when cutting a tap. The new rule does not allow the critical step to be completed until a response is heard from the party below, such as, “Copy, I see you are in position to cut the tap, and the jumper is installed.” This heightened level of awareness helps focus everyone on the critical step.
Conclusion
Our reactions to incidents can help change future outcomes if we consider both the fundamental attribution error and regression to the mean. Responding in a manner that can effect change by being narrowly focused on an actionable response allows us to better measure our results, which also means that we can do less over time by targeting what works. In short, specific actionable items can help produce better outcomes. Although it may seem counterintuitive, adding pages of rules to our already thick safety manuals may not necessarily be making us safer. Why not try a different approach?
About the Author: Bill Martin, CUSP, NRP, RN, DIMM, is the President/CEO of Think Tank Project LLC. He has held previous roles as a lineman, line supervisor and safety director.
- Managing Risk Through Cognitive Impairment Testing
- Establishing a Comprehensive Ergonomics Program During a Pandemic
- Are Your Lessons Learned Making Your Workers Safer?
- Improving Job Briefings
- August-September 2021 Q&A
- Understanding OSHA’s Rules for T&D Equipment Grounding
- Information Transfer: What’s Needed to Protect Affected Workers?
- Who is Your Customer?