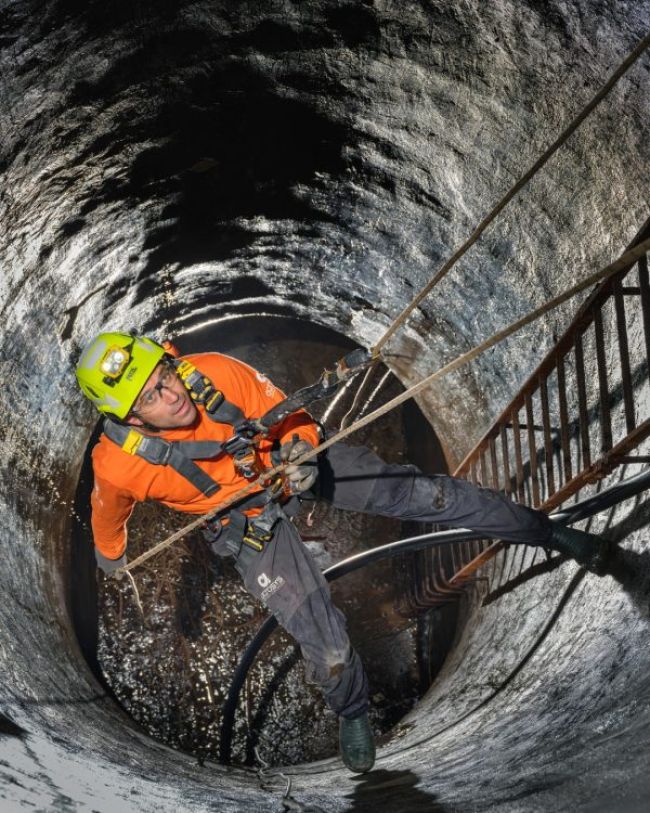
6-Step Method for Safety Harness Inspections
These inspections aren’t an inconvenience or a formality – they’re a literal matter of life and death.
Your PPE can protect you if it’s in good working order and used properly, and this is especially true of fall protection gear. All gear should be inspected before use because a deficiency can be dangerous. Damaged or defective equipment should be immediately removed from service, as should equipment that’s been used in a fall. Anything that compromises the ability of the gear to protect someone from a future fall is a potential risk.
Harnesses and safety lanyards cannot be repaired; any damage to them means the entire unit is too dangerous to use. During inspections, the components of a fall protection harness must be in perfect working order before the harness is donned and used for working at heights. It’s helpful to think of this type of equipment as having several parts rather than it being one piece of equipment, so focus on inspecting different areas for damage rather than the unit as a whole. An OSHA-specified competent person should inspect your equipment in this manner during an annual inspection, and it’s a good idea for you to do the same – every time – before you don your gear and get to work. Follow these six steps when inspecting your fall protection equipment as well as when deciding to remove it from service.
1. Check the Product Labeling
Ensure that you’ve read and understand the instructions for your harness before use. Even if you’ve lost the instructions that came with your harness, the odds are that you can download a copy from the manufacturer’s website. As for the harness itself, it must have the following information on a legible tag (note: if the information is illegible or missing, remove the harness from service):
- Model
- Date of manufacture
- Manufacturer name
- Limitations
- Warnings
2. Look at the Fall Indicator
The fall indicator is an important feature of a fall protection harness and one of the very first things you should inspect before using the harness. The indicator will either be deployed or not. If the indicator has been tripped, the harness was likely used in a fall event and must be removed from service. Depending on the brand or type of harness, the indicator may be a stitched section that rips on impact, or it may be an exposed color-coded flag. Even if everything else looks fine and passes your inspection, at this point, the safety harness has fulfilled its purpose by helping to keep someone safe. It can no longer be used.
3. Examine Webbing and Stitching
When you’re inspecting the webbing, grab it in your hands and bend it; this will allow you to check both sides for damage and cuts. This kind of damage generally doesn’t show up easily without a close visual inspection and a little more handling. Areas that see a lot of friction, such as where buckles or D-rings rub against the harness and can cause abrasions or fraying, will need special attention. When looking at the webbing, you should look for cuts, broken fibers, deterioration, modifications, fraying, uneven thicknesses, and shiny or hard spots. Stitching damage will usually appear in the form of missing, pulled or cut stitches, as well as anything hard, shiny or discolored.
4. Inspect Metal Hardware
Check buckles, grommets, D-rings and all other metal components. They should be free of damage, alterations and contamination – think along the lines of deep rust, corrosion, sharp edges, cracks, wear and deformation. Even if it isn’t extensive, there’s still the potential for damage that compromises the equipment. In this case, set the harness aside at the very least. The D-rings should freely pivot, and the buckles should connect and adjust properly.
5. Clean and Store Your Gear
A great time to assess your gear for damage is while cleaning and storing it. Proper cleaning and storage can keep your fall protection equipment in better shape for longer. Washing it can clear it of potential contaminants that can degrade your safety harness’ fibers and metal components. You can spot-clean your safety harness by wiping off the surface dirt with a sponge full of water. If the dirt is a bit deeper than a surface wash will take care of, water and a mild detergent are sufficient. Use the water and detergent before wiping, dry the gear with a clean cloth and hang it up to dry fully.
Neat storage can prevent harnesses from accidental damage, such as exposure to harmful contaminants or any bending, twisting or accidents. Store harnesses away from excessive heat, sunlight and steam as neatly as possible. Storage areas should be clean, dry, cool and dark. Avoid subjecting harnesses to fumes, heat, direct UV light, sunlight, corrosive materials and batteries. Dust, dirt, oils and moisture can also degrade your harness, so keep the area free of those potential contaminants.
6. Find Anything Questionable?
If anything comes up during your inspection that causes you to take your gear out of use – including the damage mentioned above – it needs to be destroyed immediately. Even gear that looks 100% OK but is past its manufacturer-recommended service life should no longer be used. Don’t work with it, and don’t leave it somewhere another worker could mistakenly pick it up and use it. When discarding equipment, it should be rendered unusable and destroyed; cut the straps on the harnesses and the hooks off lanyards, making them impossible to put on or use.
There are types of retractable lifelines that can be sent to the manufacturer or an authorized service and repair center once they’re removed from service. These places are qualified and equipped to test your equipment, rebuild it with new internal components and return it to you ready to use again. This is not a project you can do yourself, and this option is not available for all retractable lifelines and fall protection equipment. Do your research and ask your manufacturer or service center for more information.
Conclusion
Your safety harness inspection is crucial to your business and must be done right. Inspections aren’t just an inconvenience or a formality; they’re a literal matter of life and death, and the time and money spent are worth it so that your workers have a better chance of going home unharmed at the end of the day. OSHA standards specify that a competent person must perform your annual equipment inspection – this is a person who is well-trained and knows exactly what to look for. Note that this annual inspection doesn’t mean you can get away with neglecting inspections for the rest of the year. Everyone should assess their own safety harness before starting work for the day to ensure it is safe for use.
For more information on your safety harness, talk to the manufacturer or your trusted vendor. The manufacturer will know their products the best, will have instructions and other details readily available, and can answer your more specific questions about safety and equipment. Vendors such as authorized dealers are also a good resource because the odds are that they believe in what they sell and can answer questions about it. You might even be able to get warranties or other benefits when buying through a vendor. Staying informed and attentive will help you keep yourself and your co-workers safe.
About the Author: Rick Pedley is the president and CEO of PK Safety (https://pksafety.com).
- From My Bookshelf to Yours: ‘Who Moved My Cheese?’
- 6-Step Method for Safety Harness Inspections
- A Targeted Approach to Safety Gap Analysis
- Crash Analysis: A Personal Story
- Electrical Protective Equipment and Live-Line Tools
- Ground Gradient Step Potential and PPE
- Increasing Safety Through Underground Integrity Management
- Influencing Crew Safety