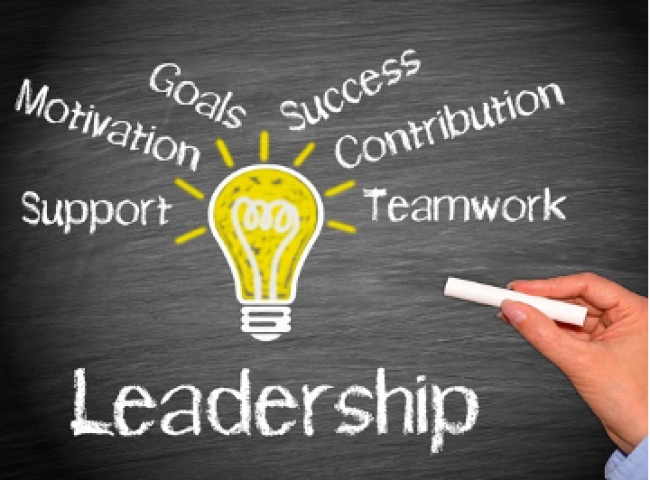
3 Keys to Transforming Safety and Organizational Performance
3 Keys to Transforming Safety and Organizational Performance
Engaging in these activities can help companies manage all types of risk holistically.
Utility organizations have an opportunity to transform their safety and organizational performance by adopting a proven strategy and approach. This approach – which consists primarily of the following three components – requires leaders to think and manage differently while also challenging industry paradigms and assumptions:
- Study and learn from success, not just failure.
- Integrate the organization’s safety and loss prevention system into other existing organizational systems and processes to achieve business goals and objectives.
- Implement a leadership development model with a road map to improve and sustain performance.
Study Failure and Success
Most safety and loss prevention systems/programs in the industry today focus on the prevention of incidents and on learning from failure (e.g., near-miss reporting, investigating workplace incidents and identifying at-risk items during workplace observations). The natural industry assumption is that a reduced number of failures equates to a better safety and loss prevention culture. Certainly, a reduction in failures could be indicative of an effective culture – but it could also be attributed to luck, coincidence, or a work environment that hides or overlooks issues. Organizations should continue to identify and learn from failure because that learning is essential to improving their safety and business performance. However, here is the challenge: As companies continue to reduce their number of failures, there becomes less to study to promote a continuous learning environment.
So, what’s the solution to this challenge? To further enhance performance, organizations should also study success, or how and why activities are performed without error.
Why should success be studied? One reason is that failure occurs much less frequently than success, limiting learning potential. Tasks are successfully performed on a much more frequent basis and better represent how work is typically accomplished.
It also doesn’t make sense to assume the root causes of failure are necessarily different than the root causes of success. These two perspectives should be combined and seen as complementary – not as opposing views to safety and loss prevention. This approach helps to improve human and organizational performance, which positively impacts how work is performed and has implications in terms of process safety, reliability, environmental and regulatory performance, product quality, equipment and property damage, and more – not just personnel safety.
Integrate Systems
Because these complementary views can positively impact all aspects of business performance, this safety and loss prevention approach should be integrated into an organization’s existing systems and processes to better accomplish its goals and business objectives. In particular, organizations should define specific improvement goals related to areas such as workplace injuries, process safety, reliability, environmental and regulatory stewardship, and quality. For example, goals could be to eliminate all recordable workplace injuries, reduce environmental or regulatory issues by 50%, and improve reliability performance by 30%. Then, organizations should define the tasks and activities that have the greatest impact on these goals. By defining these specific tasks and activities, organizations can focus their safety and loss prevention system on these areas to help improve performance. Note: This does not mean that a company’s safety and loss prevention process should not be applied to all tasks and activities, but the organization should focus a significant amount of time on key tasks and activities that can have the biggest impact on their goals and objectives.
Integrating safety and loss prevention into the entire organization does not necessarily come naturally. Most of us have been taught to make complexity more manageable by breaking things down into smaller parts in an effort to understand and manage each part individually rather than collectively. This thinking has resulted in some leaders unintentionally designing organizations that think in silos, not in terms of connections and interrelationships. Many organizations have created safety programs that are separate from their quality management programs, which are different from their reliability programs, and so on and so forth. When employees work within these programs, they are singularly focused on safety, quality or reliability instead of all three. A better, more meaningful approach is for organizations to adopt a process that enables employees to manage all types of risks holistically within their business – not in a piecemeal or programmatic fashion.
In the case of safety and loss prevention, most employees of an organization see these activities and tools as unrelated to – and therefore not integrated into – other parts of the business. For instance, the safety department may engage in pre-shift safety meetings, hazard identification and job briefings. These activities are generally focused only on safety and are not necessarily connected to other aspects of business performance because of their singular focus. But this approach can fragment people’s thinking and lead them to believe that safety and loss prevention are standalone activities. The bottom line is that failing to integrate safety and loss prevention systems within the organization’s other management systems and processes will lead to corporate inefficiencies and an increased inability to accomplish company goals.
Adopt a Leadership Development Process
Integrating safety and loss prevention into an organization may require a change in leadership’s approach and behavior. As it’s been said, leadership and culture are two sides of the same coin. Therefore, organizations should adopt an effective leadership development process as well as a road map that outlines key activities and the skills that all levels of leadership will need to successfully integrate and sustain the safety and loss prevention system.
The development process should include visible leadership and workplace engagement principles that enable leaders to learn more about how work is performed, connect with all levels of the organization, and develop and coach others. This approach will help leaders at all levels identify existing strengths and challenges in their safety and loss prevention process and potential coaching and development opportunities within the chain of command. These activities should give leaders the chance to develop meaningful relationships that facilitate trust and transparency and create an organizational learning environment that encourages collaboration, accountability and information sharing. This process is a critical component of organizational development, especially in highly dynamic and ever-changing organizations.
Because this leadership development process will be new to the organization, leaders will need to keep an open mind and challenge themselves and their direct reports to think, act and manage differently. It is critical for those in leadership positions to assume responsibility for new ways of thinking and managing to lay the proper foundation. Leaders must be deliberate and incorporate these changes into their own behaviors to demonstrate the change they wish to see, even if that means stepping out of their comfort zones. What leaders pay attention to, control and measure communicates what they care about. In other words, they must engage the organization and be willing to show up in public settings at all levels to gauge openness to change; provide compelling reasons for change; illustrate limitations of current efforts and how change is an enhancement; challenge excuses and pushback; address organizational anxiety; show visible support; and discuss the impact of change at all levels.
Conclusion
Learning from success and not just failure, integrating safety and loss prevention into existing organizational processes, and developing a leadership road map for continued improvement and sustainability are key elements in transforming safety and organizational performance. By adopting these three principles, leaders will:
- Help to establish a true learning environment.
- Improve organizational buy-in and trust.
- Enable people to see the value of their activities that enhance business performance.
- Facilitate a development process to help guide, coach, mentor and develop leaders at all levels to systematically sustain performance improvements.
If organizations can follow these key principles, they will help to establish the conditions that can transform safety and organizational performance. Organizations that my colleagues and I have worked with that have adopted this approach have achieved some of the following results:
- $800 million savings in one year for one company.
- Workforce of 25,000+: TRIR: 0.11, DAFW: 0.006.
- 54+ million hours with no lost-time incidents.
- 380+ days without an unplanned stoppage in operations.
- $9+ million reduction in workers’ compensation.
- 54+ million hours with no lost-time incidents for contractor organizations.
- Flawless operational excellence in consecutive years (zero recordable incidents, zero process safety events, maximum reliability performance).
- Workforce of 13,000+: TRIR: 0.09, DAFW: 0.02.
About the Author: Devin Bennett, Ph.D., is a partner with Loss Prevention Systems Inc. (www.lpscenter.net), which assists companies around the world in various industries with safety and loss prevention implementation and sustainability activities. Reach him at devinbennett@lpscenter.net.
- 3 Keys to Transforming Safety and Organizational Performance
- A Historical Review of Workplace Safety in the U.S.
- Electrical Arc Flash and Shock Hazards for Fall Protection Using ASTM F887
- OSHA Electric Power Standards – Simplified | Part 6
- 9 Safety Axioms You Need to Know
- October-November 2021 Q&A
- System Grounding for Worker Protection Against Induced Voltages
- Eating the Elephant