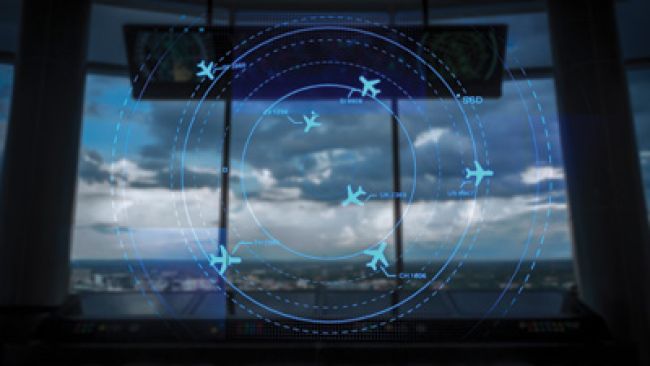
Lessons Learned from the Tenerife Airport Disaster
On March 27, 1977, two 747 passenger jets crashed on a runway on the Spanish island of Tenerife, killing 583 people. It remains one of the worst disasters in aviation history.
Human performance has evolved as a valuable incident prevention strategy in the utility and contractor industry. If you have studied human performance and safety management, you will see how the right training could have prevented the Tenerife incident. The purpose of this article is to explain the details of the Tenerife airport disaster and then draw lessons that can help crews in the utility industry work even more safely.
Perhaps the first thing you should know is that Jacob Veldhuyzen van Zanten – who piloted the Dutch KLM 747 that was involved in the crash – had served as a role model for other airline pilots. He was considered the best of the best. Having moved up to top management at KLM Royal Dutch Airlines, he was even the head of safety for the company. However, van Zanten had a problem: His revered skill and knowledge made him think he knew better, which ultimately was a major factor in the Tenerife crash.
Sequence of Events
Four hours before the crash, the KLM 747, originating from the Netherlands, and a Pan Am 747 out of Los Angeles were both approaching Gando Airport on the Canary Islands off the western coast of Africa. Shortly before landing, a terrorist incident forced both flights to be diverted to the much smaller Los Rodeos Airport on Tenerife, the largest of the Canary Islands. This diversion caused many issues, including the KLM flight being in danger of exceeding its duty-time limits. Air traffic control (ATC), shorthanded since it was a Sunday, was forced to handle a considerable amount of traffic. The airport quickly became congested, with planes being parked on the taxiway and pilots using unconventional means to move their planes around. Further, patches of thick fog had begun drifting across the airfield, causing visibility issues.
The collision occurred when the Pan Am airliner was rolling at one end of the runway while the KLM 747 was taking off at the other end of the runway. It killed everyone on board the KLM flight and most of those on the Pan Am airliner, leaving only 61 survivors.
The primary cause of the accident was determined to be KLM pilot van Zanten’s decision to take off after making assumptions about messages received from ATC; he believed he had the clearance to do so. While much of the emphasis following the crash was on improving radio communications through standardized phraseology, the greatest change came about when the aviation industry established crew resource management – which I’ll explain a little later – that addresses the root cause of the accident.
Time Pressure
One of the issues that factored into this horrendous accident was that KLM had recently put in place strict duty-time limits to prevent crew fatigue. However, doing so produced unintended consequences. As revealed in flight-deck recordings from just prior to the crash, van Zanten was feeling pressure to get the plane off the ground. If he failed to do so in a timely fashion, it would be his responsibility to find accommodations for all the crew members and all the passengers on board, which would have been inconvenient and expensive. Things also would be thrown off schedule the next day in Amsterdam. He felt he must get the plane off the ground. Does any of this sound familiar? Have you or any of your co-workers ever put production ahead of safety to save money or save face?
A Communication Breakdown
At the airport that day, three different languages were being spoken by ATC and airline crew members: Dutch, English and Spanish. Eight minutes before the crash, the Pan Am aircraft was driven onto the runway while the KLM aircraft was taxiing on the runway. However, the Pan Am captain had told the first officer two times that he was not comfortable getting on the runway because of the dense fog. The captain’s protests went unheard because the first officer was busy on the radio. Even with his concerns that something wasn’t right, the captain opted to begin taxiing.
As the Pan Am jet headed down the runway, the crew was instructed by ATC to turn onto the taxiway at the exit “third to the left.” That would have caused the 747 to make an unconventional and difficult turn backward, which was not specified by ATC. On the other hand, the fourth exit was a standard 45-degree turn, so the Pan Am crew figured this was what ATC must have meant, especially since the crew had noticed that the first exit was closed.
In the final minute before the crash, key misunderstandings occurred, and three-way communication was abandoned. Further, two radios were keyed at exactly the same time, causing a loud, shrill noise for four seconds, long enough for the KLM crew to miss a critical transmission to hold off on taking flight.
So, what can we learn from this? For starters, three-way communication and mutual understanding are paramount where safety is concerned. Workers must be trained on and demonstrate understanding of their company’s communication protocols. They also must stop what they’re doing if they don’t understand what’s being communicated to them or if they’re unsure about any aspect of the task they’re about to perform.
This disaster also begs the question: Did ATC ask the Pan Am crew to make that difficult turn off the runway because they lacked the appropriate skills to execute their job? Every day, they dealt with small planes that could easily perform that maneuver. But on that fateful day, ATC staff was asked to do something they had little to no experience doing: handle a number of large planes.
Whether it’s planes or electric lines, those in charge must always ask, have our workers been trained on and demonstrated competency in the task they’re being asked to perform? In the utility business, just because a worker is a journeyman for a utility or contractor doesn’t mean they’re competent to safely perform all the tasks that another employer would expect from their employee. Gaps assessments and appropriate training are critical to work-site safety.
Crew Resource Management
I referenced crew resource management earlier, so let’s take a closer look at that now. On the ground in Tenerife, van Zanten ordered the plane fueled to its limit. The flight-deck recorder indicated that the first officer objected to the heavy fuel load, but van Zanten cut him off. The first officer hardly spoke again before the crash. In the moments before impact, the Pan Am pilot tried to veer away to avoid a collision while van Zanten tried to pull up the KLM airliner. In the end, the KLM flight struck the Pan Am plane just behind the flight deck. Investigators believe that had a lesser amount of fuel been put in the plane, it may have cleared the ground soon enough to avert disaster.
When a worker speaks up for safety in a reasonable way and the leader fails to listen or flexes their muscle, the wrong leader is in place. An investigation uncovered the dysfunctional cockpit environment that van Zanten had created, and the aviation industry was determined to fix the problem. Airline industry executives understood that it was going to take a while to turn the ship, but they knew they needed to begin somewhere. They went about it by developing and implementing crew resource management, which is a set of training procedures delivered to employees working in jobs where human error can be catastrophic.
Think about how this could apply to the utility industry. If we focus on solid technical and human performance training – delivering good decision-making skills to our employees – imagine the progress we could make in 10 years.
Results Motivate Behavior
Regardless of how long you’ve worked in the utility industry, you’ve no doubt heard time and again that taking shortcuts is one thing you should never do. But certain, immediate, high-impact results drive human behavior. A positive outcome, such as cutting down the amount of time it takes to perform a task, is a strong motivator to continue taking that shortcut. If a potentially poor outcome – such as discipline or the chance that an incident might occur – does not equal or exceed the gain of saving time, a worker is likelier to take the shortcut. In the Tenerife airport disaster, van Zanten didn’t want to exceed the duty-time limits in place. In choosing to take flight, he felt the gain would be immediate, certain and high-impact, so potentially negative outcomes seemed insufficient to neutralize the temptation.
Summary
We’ve explored several of the parallels between this disaster and how similar issues arise in our day-to-day work, but there are too many to discuss in just one article. My recommendation is to discuss the Tenerife airport disaster at your next safety meeting. Explain the history of the incident and then ask open-ended questions to prompt a group conversation. This historic tragedy offers us many learning opportunities, and we’d be wise to take advantage of them.
About the Author: Dwight Miller began working on the line crew 35 years ago and has dedicated his last 13 years to safety and training. He currently serves Ohio’s Electric Cooperatives as director of safety training and loss prevention, where he is committed to promoting a culture where lineworkers think, integrity is held high and safety is non-negotiable.
- I’ve Got Your Back: Lessons in Socio-Biomimicry
- Lessons Learned from the Tenerife Airport Disaster
- Safe Transportation of Leaking Transformers
- Safety Success During an Insulating Boom Flashover
- A Practical Review of the C2-2017 National Electrical Safety Code
- Is it Maintenance or Construction?
- August-September 2020 Q&A
- Decision Making: Make Balanced Decisions and Avoid Biases