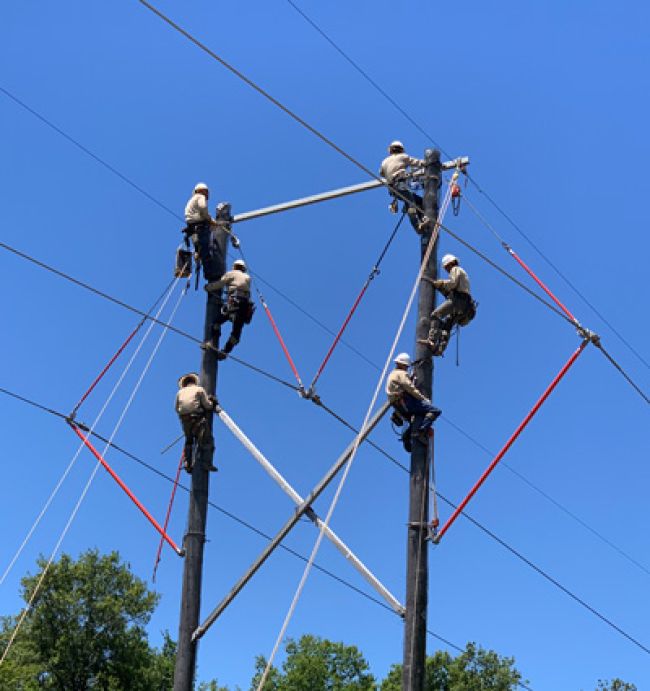
What are OSHA’s Training Requirements?
In our first article in this series (see https://incident-prevention.com/blog/when-osha-electric-power-safety-standards-apply), we discussed how to apply OSHA’s electric power standards. This article will review OSHA 29 CFR 1910.269 and 1926 Subpart V training requirements relating to qualified and unqualified employees.
To determine training requirements, you must first ask the question, are my employees exposed to electric power system hazards? If so, the training portion of the OSHA electric power standards should apply.
OSHA requires all employees to be trained in the safety-related work practices, safety procedures and emergency procedures that pertain to their job assignments. This includes employees performing covered work, as discussed in the first article of this series, and employees who access areas restricted to qualified employees in order to perform nonelectrical work.
Examples of employees who access restricted areas include an employee spraying herbicide around underground enclosures, a warehouseman delivering substation equipment inside an energized substation, and a maintenance employee replacing “Danger” signs inside an energized substation. Each of these nonelectrical employees has potential electrical hazards and risks associated with their job tasks that must be identified. Unfortunately, nonelectrical employees are many times exposed to unknown electrical hazards, such as step and touch potentials they do not know exist, which emphasizes the importance of effective training.
Risk Assessments
OSHA requires the employer to assess the degree of risk associated with each job task and provide training appropriate for the exposure. Determining the degree of risk is subjective, so it is extremely important for organizations to have a structured process. The process must ensure employees can recognize hazards and take reasonable measures to avoid or adequately control them. A communication technician installing a new phone line inside an energized substation does not have the same electrical exposure risk a substation technician does when troubleshooting electrical equipment. At a minimum, the communication technician would need to know what is safe and not safe to touch; the nominal voltage of exposed parts in the work area; minimum approach distances as well as the skills and techniques to maintain those distances; how to recognize and properly use protective equipment to provide protection for their safety; and how to recognize electrical hazards, plus the skills and techniques to control or avoid those hazards.
Many organizations use a job hazard analysis (JHA) or other similar method to develop procedures to reduce or eliminate hazards. A well-developed JHA examines each step of a job, identifies existing or potential hazards with each step, and determines the appropriate abatement strategies to remove or reduce the hazards identified in each step. JHAs also can be used to determine if your job training content is appropriate for retraining when an employee has not performed a specific job task within the previous year.
Demonstrated Proficiency
OSHA requires employees to demonstrate proficiency in their work practices before training can be considered complete. Although OSHA does not require training to be documented, it is always a good practice to document training and completion of demonstrated proficiency. Caution should be exercised when employees are substituted in jobs that they are not qualified to perform. Take, for example, a meter technician who responds to a trouble call with a lineman. The meter technician would not have to be qualified to the same level as the lineman, but they would have to meet qualification requirements and demonstrate proficiency as it relates to line work, including but not limited to emergency procedures such as pole-top or bucket rescue.
Qualified Employees
It is important to remember that a job title does not qualify an employee to perform work within OSHA standards. Employees must be able to demonstrate proficiency based on the work performed.
OSHA’s definition of a qualified employee is a worker who is knowledgeable about the construction and operation of the electric power generation, transmission and distribution equipment involved, along with the associated hazards.
Additionally, a qualified employee must be able to distinguish exposed live parts; be able to determine the nominal voltage; understand minimum approach distances and how to maintain them; know special precautionary techniques; understand how to use PPE as well as insulating, shielding and insulated tools; be capable of recognizing electrical hazards with the exposure risk; and know how to control or avoid those electrical hazards.
Qualified vs. Unqualified
Employees can be qualified for some tasks and unqualified for others. Qualification requirements are based on the job tasks performed. Examples include a meter technician installing a new meter, a service technician connecting a new service, a relay technician reprogramming a relay, a lineman re-conductoring an existing energized line and a distribution operator performing a SCADA operation. Each of these employees performs different electrical job tasks with different hazards. A distribution operator does not typically perform field work, but they regularly de-energize and energize electrical systems via SCADA operations. Each of these jobs requires specific training that may not look the same.
Retraining
OSHA considers tasks that are performed less than once a year to necessitate retraining before work begins. Additional retraining also is required when an employee is not complying with safety-related work practices, when new technology or new equipment is introduced into the workplace, and when employees must engage in work practices not normally performed within their regular job duties.
Conclusion
When determining if employees are required to be trained, consider whether they have exposure to electrical system hazards. If so, employees need to be trained based on their level of exposure. Training must include skills, hazards, risk exposure and required safe work practices to be performed to ensure their safety.
We hope you will join us for the third part of this series, in which we will discuss job briefings, risk assessments and the importance of effective job planning.
About the Authors: Pam Tompkins, CUSP, CSP, is president and CEO of SET Solutions LLC. She is a 40-year veteran of the electric utility industry, a founding member of the Utility Safety & Ops Leadership Network and presently serves on the USOLN executive board. Tompkins worked in the utility industry for over 20 years and has provided electric power safety consulting for the last 20 years. An OSHA-authorized instructor, she has supported utilities, contractors and other organizations operating electric power systems in designing and maintaining safety improvement methods and strategies for organizational excellence.
Matt Edmonds, CUSP, CIT, CHST, is vice president of SET Solutions LLC. A published author with over 15 years of safety management experience, he also is an OSHA-authorized instructor for general industry and construction standards. Edmonds provides specialty safety management services for electric power organizations throughout the U.S. He has been instrumental in the development of training courses designed for electric power organizations, including OSHA 10- and 30-hour courses and SET Solutions’ popular OSHA Electric Power Standards Simplified series.
About OSHA Electric Power Standards – Simplified: Topics in this series are derived from SET Solutions’ popular OSHA electric power course offered through the Incident Prevention Institute (https://ip-institute.com). The course is designed to help learners identify standard requirements and to offer practical ways to apply the standards.
*****
- What are OSHA’s Training Requirements?
- A Lineworker’s Three Safety Superpowers
- Leading Change Through Faith, Hope and Tough Love: Part II
- Are You Using Your Five Senses to Stay Safe?
- Trailers, Brakes and Common Usage Errors
- Lone Worker Limitations
- December 2020-January 2021 Q&A
- Assessments: Highlights and Implementation