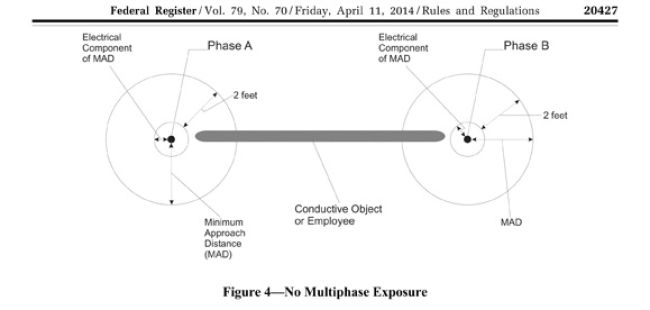
Train the Trainer 101: Practical MAD and Arc Flash Protection
Author’s Note: Before we get to the article, I want to thank the members of Incident Prevention’s editorial advisory board for their help in assembling this installment of “Train the Trainer 101.” They help me keep my head on straight, especially when I have ideas that are way outside the box. Even though I am also on the board, they still hold me to high standards of accountability and accuracy. These folks are a great asset to iP and make better writers of everyone who contributes to the publication.
Over the past year, iP subject matter experts have fielded many questions about how to meet the minimum approach distance (MAD) and arc flash (AF) rules published by OSHA in the 2014 final rule regarding 29 CFR 1910.269 and 1926 Subpart V. The questions about MAD came from a variety of perspectives, but they were primarily submitted by contractors trying to facilitate the information transfer now required by 1910.269(a)(3) and 1926.950(c). Without information about a system’s fault characteristics, the contractor cannot determine MAD, either by calculation or via the tables in 1910.269 Appendix B and Appendix B to 1926 Subpart V. That means the contractors must fall back on the sometimes absurd provisions of alternative tables R-7 through R-9. In my work for a contractor, we have found that those alternative tables can make some work – particularly transmission work – very difficult, if not impossible, especially when faced with compact lattice structures or old construction standards on wood poles. For AF programs, that lack of information may be overcome effectively by experienced guesswork, but compliance by guesswork cannot be defended when the compliance safety and health officer asks how you determined the AF compliance requirements.
With utilities, especially those that don’t have diverse and well-staffed specialty engineering departments, the questions we receive are about interpreting the requirements. Obviously there are consulting firms out there, some of which are associated with iP, that can help with the technical issues. But here we can discuss some of the more practical issues that will help to relieve confusion.
It’s About Exposure
The most frequent issue is understanding exposure, which is the first question that has to be answered. If there is no exposure, there is no practical purpose for some of the actions utilities and contractors take. I am aware of a utility whose engineer, concerned with his understanding of the rules and personal liability, said all exposures were Category 4. I am pretty sure that will cover any AF exposure, but I foresee heat stroke in the utility’s future.
If you have very little or no AF exposure, you may be able to use a don-and-doff program in which workers only suit up when the exposure exists. This could be the practical solution for a small sticking muni or co-op with an $800,000 operations budget that is trying to decide what to cut to get the $20,000 for an AF protection program. You may be able to provide arc protective gear and don it on the rare occasion there will be an AF hazard. Of course, it’s not as easy to do as it is to write. Such a program requires a realistic and defensible assessment of the workplace exposures and training. That training has to ensure the employee understands when he or she must use AF protective equipment and must include demonstration and accountability as elements to ensure the effectiveness of such a program. This type of don-and-doff AF program is not appropriate everywhere. Larger utilities and utilities that glove have much more frequent exposure, and the opportunity to mix up and confuse exposures can lead to workers not using the appropriate protective gear when there are AF exposures.
Characterizing Exposure
Simply being in the vicinity of energized systems does not mean you have an AF exposure. You may have an electrical exposure that requires MAD, but we will discuss that a little later on. There are a couple ways to understand and even reduce AF exposures in the workplace. One is found in the standard itself. The note to paragraph 1910.269(l)(8)(iv)(C) states, “This paragraph [regarding requirements for AF protective clothing] does not apply to conductors that are capable of carrying, without failure, the maximum available fault current for the time the circuit protective devices take to interrupt the fault.” As an example of where this would apply, our company has a client that insisted our foundation subcontractor wear AF shirts and pants to install a concrete pad 20 feet below aluminum tube bus in a substation. There was no exposure based on the OSHA note above. Instead of wearing lightweight long-sleeve tees and lightweight pants, the subcontractor was required to buy and the crew was required to wear heavier AF clothing in 115-degree weather. That wasn’t very practical given that the risk of heat illness was compounded by clothing to protect against an AF exposure that did not exist. Appendix E to 1910.269 has lots of information regarding determination of exposure in the workplace.
Another process is practical design using new technologies to reduce the levels of incidental flash energy. In the August 2015 issue of iP, Samy Faried wrote an article, “Arc Flash Mitigating Technologies and the OSHA Final Rule” (see http://incident-prevention.com/blog/arc-flash-mitigating-technologies-and-the-osha-final-rule), that explained how fast-acting relays can lower AF. In the same way, procedures and work methods can lower or even eliminate risks. I mentioned sticking earlier in this article, and the last time I mentioned it in a previous “Train the Trainer 101,” there were lots of comments. Yes, I’m a gloving lineman and I know the practical benefits of gloving, but sometimes it seems like only old guys like me won’t hesitate to stick a job that has high risks associated with the proximity to the phases created by gloving. However, the reality is that – and those sticking states and companies will tell you the same thing – line work can still be done by sticking, and it is a practical solution for AF exposure mitigation. Sticking should be considered for the toolbox when it comes to risk mitigation methods.
I have one last comment on exposure. AF pants haven’t received much discussion, but there are some issues. Some of my colleagues disagree with me, but I interpret the standard as requiring AF protection based on exposure. I also believe that if no AF exposure exists below the waist, there is no requirement for AF protective pants. I think OSHA writes with consistency and specificity, and the language regarding AF exposure is consistent and specific – you protect where there is exposure. I haven’t read a rule in the AF-related regulations written like the rubber glove rule, which specifically states that if you wear gloves, you must also wear sleeves with specified exceptions (see 1910.269(l)(4)(i)). I may be way off on this point and I look forward to reader feedback on the issue.
Regarding arc protective pants, keep in mind there are no AF work pants currently on the market rated over Category 2. Where there is exposure – such as when digging or working around fault-prone cables, open underground installations or bottom-vented gear – and you have a determined the exposure exceeds Category 2, a suit or layers are required. However, that alone may not protect a wearer. If AF heat is at the feet, the heat will rise inside the AF clothing in a chimney effect. That heat stays in the clothing to devastating effect. I’ve now seen it twice and it is not pretty.
AF protection is not as simple as point, click and issue. It takes planning, understanding, diligence and sometimes practicality to safely, comfortably and economically produce the desired effect – protection of the employee from all risks.
Minimum Approach Distance
MADs changed a lot in the final rule. The biggest reason was estimation of risks associated with voltage transients created by new technologies in high-speed switching, in particular with systems over 72 kV. Voltage transients can result in voltage rise several times the normal voltage of the system. Persons or equipment in or near the air gaps on those systems affect the insulation value of the gaps. Lab testing has shown that compromising the air gap in the presence of transients can result in flashover that could endanger workers. MAD rules are not yet settled, and tables and processes may change as utilities and consensus partners continue studying the phenomena behind transients, the realities of risks associated with transients and transient controls.
Still, while MAD rules have created compliance issues for contractors and utilities, they have also created opportunities. Recently a contractor colleague sent me a MAD table created by a utility. In some cases, the MADs in the table were less than the old MADs we worked with, which were from the legacy tables that existed prior to the 2014 OSHA final rule. My colleague was concerned the MADs were wrong. The fact is that now that the OSHA standard allows for individual utilities to perform an engineering analysis to determine MAD, some of the calculated exposures can be less than the new MAD tables or even the legacy tables we have worked from for years.
Ultimately, we must either compute MAD using engineering analyses or the precalculated tables provided. The rules and appendices are found in 1910.269(l)(3) for general industry maintenance operations, including 1910.269 Appendix B, and in the construction standard mirror rules, 1926.960(c)(1) and Subpart V Appendix B. You can also use the MAD calculator found at www.osha.gov/dsg/mad_calculator/mad_calculator.html.
The rules are still difficult to work through and sometimes the practical aspects that help us comply with those rules get lost in the language. Following is discussion about a couple of the issues readers write to us about as they are trying to sort out the language of the rules.
Multiphase Exposure
Multiphase exposure is kind of like enclosed space. With enclosed space, if you cannot determine that the space meets the exceptions to be considered enclosed, it must be determined to be confined or even a permit-required confined space. On three-phase systems, you must determine by the criteria whether a three-phase system can be worked as a single-phase exposure. It’s pretty easy to say there is a multiphase exposure with a three-phase system. If you simply treat all exposures as three-phase, or as multiphase and use the alternative tables to determine your MAD, you better prepare to buy longer sticks, especially in the transmission voltages with the multipliers for 3.0 transients.
Fortunately, OSHA clearly explained what constitutes a multiphase exposure, even though it might be hard to find. Below 72 kV, if all phases are uncovered and there is a potential multiphase exposure, the MAD is computed at the nominal system voltage. However, if the phases not being worked can be covered using cover rated for guarded phase to ground, the exposure for the purposes of MAD is now computed at the phase-to-ground voltage for the phase being worked.
Be careful; if your system is 46 kV and phase to ground is 23 kV, you cannot use cover rated at 25 kV guarded phase to guarded phase/18 kV guarded phase to ground to claim you have a phase-to-ground exposure. The phase you are working on is not guarded, so the cover used on the other phases has to be rated for the phase-to-ground voltage. Covering to eliminate multiphase exposure also requires the approach to conductors for cover-up to maintain the appropriate MAD. Covering the other phases allows you to use the MAD for the phase-to-ground voltage. For unguarded phases, OSHA explained multiphase exposure in the preamble.
On page 20426 of the preamble to the final rule (see www.gpo.gov/fdsys/pkg/FR-2014-04-11/pdf/2013-29579.pdf), OSHA provided an explanatory reference for phase-to-phase exposure. The agency cited a September 27, 2005 letter of interpretation to IBEW President Edwin Hill that included a graphic explaining multiphase exposure (see below). Understanding the MAD is the combination of the air-insulating electrical component plus the inadvertent movement component, multiphase exposure exists when a worker or a conductive object can simultaneously breach the electrical component of the MAD of two energized objects at different potentials. Keep in mind that those distances could be affected by conductor movement and other conditions expressed in this section of the preamble to the final rule. It is also worth noting here that those two electrical potentials may not necessarily be opposite phases of the same system, but could also be different potentials between two systems of different voltage. That is the case with transmission and distribution underbuilds.
Above 72 kV, there is no portable insulation to isolate the second phase. Another important condition is noted in table R-7. Phase-to-phase exposure can only be applied from the table if there is no insulating object that can breach the electrical components of large conductive objects between the phases. Insulating and large conducting objects, even if they are rated for the voltage or outside the respective MADs, change the electrical conductive quality of the air and can reduce the protection normally afforded by the phase spacing.
Portable Protective Air Gaps
There is an old technology that is returning to transmission live-line work. Portable protective air gaps (PPAG) essentially are resistors installed near the work location across an insulating string at an adjacent structure. PPAGs are engineered to spark-over during a surge, reducing the level of transient voltage that can occur at the work site. Limiting the voltage transient reduces flashover risks and allows calculation of shorter MAD values during live-line work at insulator strings. The currently available PPAGs are for 115-kV systems and above. The problem is that there is the increased risk of an unwanted circuit trip affecting system reliability. However, the technology in both gaps and relaying is getting to the point where calculations can be very reliable. If the utility trusts the calculations and can accept the increased risk of an inadvertent trip, it is sometimes more preferable than switching and the issues associated with an outage.
Finally, as with AF, exposure is the determining factor with MAD. Transient voltages are the issue with the increased MAD distances; they are generally caused by switching. If switching technologies can be employed that reduce transients during the work period, the calculated lower MAD distances can be utilized.
About the Author: After 25 years as a transmission-distribution lineman and foreman, Jim Vaughn has devoted the last 17 years to safety and training. A noted author, trainer and lecturer, he is director of safety for Atkinson Power. He can be reached at jim.vaughn@atkn.com.
Editor’s Note: “Train the Trainer 101” is a regular feature designed to assist trainers by making complex technical issues deliverable in a nontechnical format. If you have comments about this article or a topic idea for a future issue, please contact Kate Wade at kate@incident-prevention.com.