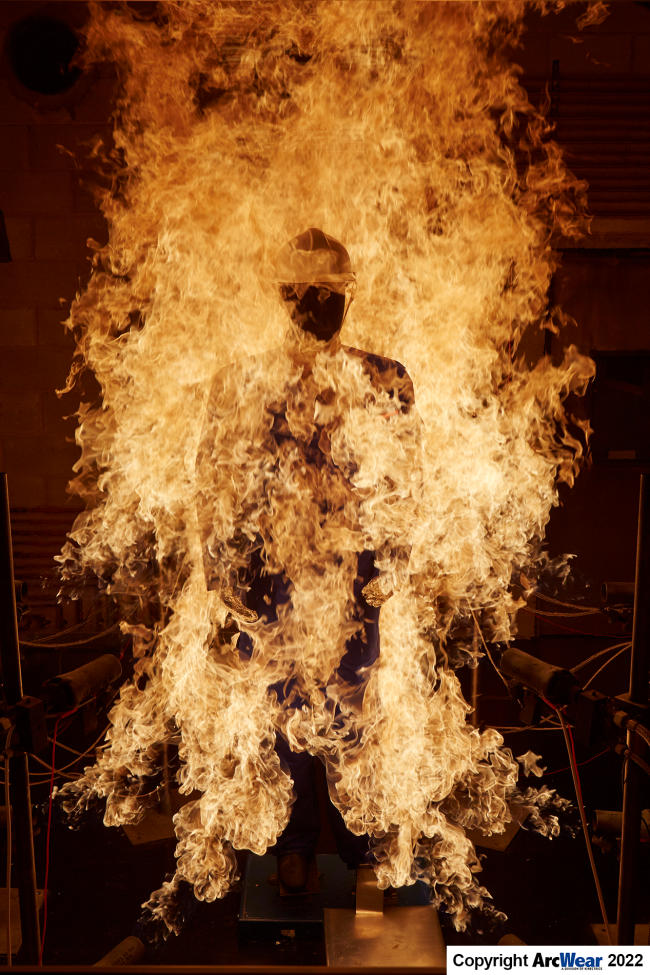
Thermal Protection for Electrical Work
Subject matter experts provide an update on recent changes and emerging research in the thermal protective world.
Thermal protective apparel for electrical work appears to have reached a point of inflection from “What needs to be done?” to “How can it be improved?” Looking at the safety standards recently approved for publication, the most basic requirements of specimen preparation (e.g., number of test shots, statistical analysis methods) all remain unchanged. However, there have been some changes and emerging research in the thermal protective world, which is the basis for this article.
FR vs. AR
First, it is important to understand the terms “flame resistant” (FR) and “arc rated” (AR). FR has a substantially greater market share in utilities and commercial industry compared to AR, as “FR” is a generic term that is defined differently by various specifications. For example, FR protective apparel may be certified to NFPA 2112, “Standard on Flame-Resistant Clothing for Protection of Industrial Personnel Against Short-Duration Thermal Exposures from Fire” (2023 is the latest edition). To receive certification, apparel must be tested; one test method is the ASTM D6413 vertical flame test. This is a standard test method used in FR and AR workwear, but it is not used as a standalone method to determine compliance (see https://e-hazard.com/false-safety-labeling-is-this-fr-or-arc-rated-look-at-this-melting-rainwear-from-regal-rainwear-in-golden-ms/). ASTM D6413 requires a specimen to be exposed to a small, candle-like flame to determine the material’s behavior as measured through after-flame time and char length. It is a commonly used quality control method and precursor to large-scale test methods. The large-scale method used in NFPA 2112 is ASTM F1930, which is a flash-fire simulation on an instrumented mannequin. ASTM F1930 exposes standardized coverall specimens to a flash fire using propane burners for three seconds. By capturing the temperature and time data points, the total heat flux or energy transfer can be determined to predict theoretical burn injury. The tested products that meet all the requirements of NFPA 2112 certification are sometimes referred to as “flash fire rated.”
The specification for AR clothing – ASTM F1506 – also includes the ASTM D6413 vertical flame test. This requires test specimens to be evaluated for flammability before and after laundering prior to arc testing, which prevents costly arc flash testing on specimens that are likely to fail. To comply with ASTM F1506, a fabric must first be assigned an arc rating by testing according to ASTM F1959, among several other test requirements. Since the FR market is substantially larger with more manufacturers and even more available products, it is easy to forget that both flash fire-rated and AR apparel are flame resistant, but not all FR apparel is arc rated (see www.arcwear.com/blog/arc-rated-ar-vs-flame-resistant-fr-understanding-the-difference/). Due to branding and workwear styling (i.e., apparel that looks safe for electrical work), nothing prevents an uninformed person from buying FR garments that lack the necessary testing required to ensure that said garments are certified AR. It is imperative that project managers and safety specialists plan for such errors and stay aware of relevant specifications applicable to their hazards.
Garment Labeling
The easiest way to differentiate between AR and FR is to look at the garment’s label. If it mentions an arc rating in cal/cm2 as well as compliance with ASTM F1506, then it is AR.
ASTM F1506 recently published the 2022 edition with a notable change to the labeling requirement. During the construction of AR apparel, manufacturers may use different fabrics in certain areas. Consider the fabric under the arms, for example, that facilitates mobility. Previous versions of the standard, in 6.4.7.1, required that the arc rating for each area be designated. In the newly published 2022 edition, section 6.4.7.2 requires that a single arc rating be assigned to the entire garment, and that arc rating must be aligned with the portion of the garment with the lowest rating.
The ASTM F1506 standard requires that garments be labeled with the following: “This garment meets all the requirements of F1506.” The intention is to show compliance with the standard that was followed and enforced at the time of manufacturing. However, some manufacturers choose to amend the label to state F1506-XX, where XX is the edition, such as 22 or 20a. The standard does not require a complete product recall if F1506 changes; instead, a quality management system used by the manufacturer must be established to facilitate conformance for new products. This must occur within 12 months of the new standard issue date as per section 9, “Product Conformance.”
Compliance and Longevity
How does a small-scale shopper, like a single end user who purchased a single AR ensemble, verify the garment’s compliance?
ASTM F1506 requires that the manufacturer’s details be included on the garment, which is the easiest method by which an end user can contact the manufacturer concerning the product. Usually, name brands treat compliance issues with sufficient vigor to protect their brand’s reputation; therefore, purchasing a name-brand garment often ensures that it complies with the standard.
Many question the longevity of AR apparel that complies with ASTM F1506. Is there an expiration date on garments? Should a seldom-used flash suit system be discarded once it reaches a certain age?
There are two factors to consider when deciding whether to discard an AR garment. First, a user must determine if the thermal performance of the garment has deteriorated over time. Scientific research does not support deterioration. Furthermore, laboratories have reclaimed used daily workwear and performed arc exposure tests; the arc rating of the used garments was similar to the arc rating before heavy wear. However, variables such as fabric type, care, environmental conditions and contamination may produce different results. Some users have decided to follow NFPA 1851 for firefighters’ apparel and retire their garments after 10 years from the date of manufacture. This decade-long replacement plan aligns more with the revision cycle of that standard than the performance of the AR fabric – and such decisions should be made with caution. If the manufacturer’s care and use instructions are combined with common-sense laundering techniques, it is possible that a mechanically sound garment may exceed 10 years of service. Even stains such as grease can be washed out under a hot water cycle. Avoid bleach and fabric softener containing liquid or powder detergents, and dry on low-heat settings. The failure of an AR fabric, or a reduction in its arc rating, is most often due to the structural weaknesses of the garment; frays and tears are typical indicators for replacement.
Technological advancements are the second factor a user must consider before retiring AR apparel. Today, a 60-plus-cal/cm2 flash suit weighs approximately the same as a 40-cal/cm2 flash suit from 10 years ago. A moisture-wicking AR base-layer T-shirt keeps a user cooler than a standard 100% cotton inner T-shirt. Factoring in inflation, these advanced products cost the same for a top-in-class product compared to 10 years ago. However, users must be cognizant of the fact that visors and face shields – like hard hats – have limited lifespans. It is recommended that these be replaced every two to five years depending on use and environmental conditions. Speak to manufacturers about their recommendations. The ASTM F2178 standard committees are considering such changes in future revisions.
Ensemble Testing and Specification
Another development is the testing and specification of fully integrated ensembles, especially those using different layers and components (e.g., rainwear over a flash suit). ASTM F2621 provides a means for testing such complete ensembles, but ASTM F1506 does not require full ensemble testing. Now, a new standard is being developed to bridge these gaps. This standard, which will likely be titled “Performance Specification for Arc-Rated Ensembles,” emerged in 2019 and is expected to go to ballot within the next year. It will consider the integration of various components of multi-layered, multi-component ensembles – such as a utility worker performing live work using a flash suit in wet weather – and reference the test methods discussed in both ASTM F1959 and ASTM F2621. The chair of the task group developing the standard aims to address the following: after-flame for higher-rated multi-layered specimens; FR performance requirements for the various layers in a specimen; and sample preparation for multi-layered specimens.
Low-Voltage Hazards
Manufacturers should be acknowledged for their relentless role in developing lightweight, comfortable, stylish yet functional apparel. It is commonplace to see contractors and staff utilizing AR apparel as work uniforms, a vast improvement from a decade ago. Workers failing to don head, face and hand protection when interacting with live equipment is also a common observation. Historically, standards did not cover voltages below 240V AC (three-phase and single-phase) and 300V DC, believing these were non-hazardous voltages for electrical arc flash, so no additional PPE was required. However, studies show that arcs at these low levels are not only sustainable but capable of igniting non-AR apparel.
Power utilities offer great resources for high-voltage applications (>600V), but audits illustrate lesser compliance when it comes to low-voltage hazards. One reason could be the focus of ArcPro software and the NESC Part 4 on higher-voltage systems. However, Appendix E to OSHA 1910 Subpart R remains clear that IEEE 1584 shall be used for arc flash energy calculations below 15 kV. Proper labeling offers a solution by informing utility staff of low-voltage arc flash hazards due to the wide variances of arc flash energies at low voltage (<600V). It is recommended to seek advice from experts in the field for best practice labeling techniques. There are several online resources concerning arc flash labeling, including this video from Jim Phillips, P.E.: www.youtube.com/watch?v=Cxx8kAmM_BY.
In closing, utilities must address the potentially life-threatening arc flash hazards at low voltages. This may be required in warehouses, administration buildings and even substation secondary plant systems.
About the Authors: Zarheer Jooma, M.S., P.E., is a partner at e-Hazard (https://e-hazard.com). He performs electrical workplace safety training, consulting, arc flash engineering studies, electrical accident investigations and electrical safety audits. Jooma is a member of the IEEE 1584-1:2021 Working Committee and Ballot Resolution Committee, ASTM F18 – Electrical Protective Equipment for Workers and IEC TC78 – Live Working. He has also contributed to the NFPA 70E standard.
Brian Shiels, M.S., is the service line manager for ArcWear (www.arcwear.com), a division of Kinectrics. His professional experience includes quality management as well as the development and testing of thermal protective clothing and equipment. Among other responsibilities, Shiels is a director on the ASTM International Board of Directors. He earned his master’s degree from North Carolina State University.
Stacy Klausing, M.S., is the PPE project manager at ArcWear (www.arcwear.com). Her professional experience includes project management in testing laboratories, testing and evaluating fabric related to PPE, and execution and management of an ISO 17025-accredited quality system. She earned her master’s degree from the University of Kentucky and is a Six Sigma Green Belt from North Carolina State University.
- The 8 Habits of a Highly Effective Safety Culture
- Advancing Workforce Skills Using Simulation-Based Training
- Thermal Protection for Electrical Work
- From My Bookshelf to Yours: ‘No Compromise’
- Understanding Wind Speed Limitations on Utility Equipment
- The Importance of Proper Coverup: Two Real-Life Tales
- OSHA Electric Power Standards – Simplified