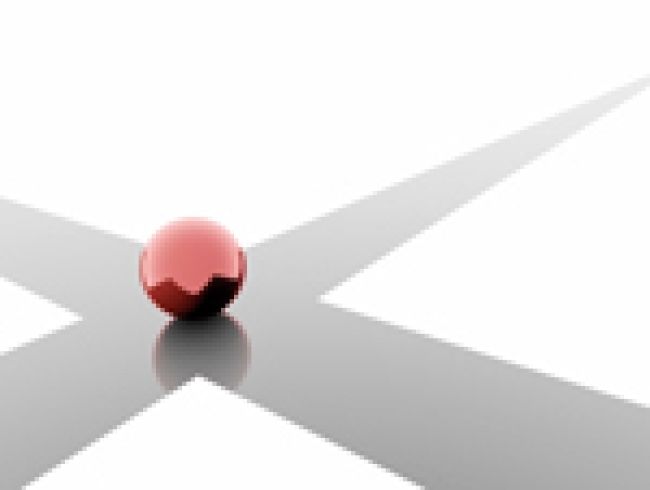
The Intersect: A Practical Guide to Work-Site Hazard Analysis
A hazard is essentially a condition or activity that, if left uncontrolled, may result in an accident or a serious injury. To effectively identify hazards, the observer must develop a means of recognizing a hazard exposure. What I see repeatedly in the field are hazard lists like “wear PPE, stay out of the bite, watch for cars, cover up well.” What I don’t see is an effective approach to identifying hazards. I had occasion to investigate a 4-kV contact in a metal-clad breaker where the worker brushed his hand against a control power transformer that had not been identified or tested. For three days he had his head in the cabinet, unaware that the primary leads for the transformer had been moved from the load side to the high side of the breaker contacts. For three days his pre-job hazard analysis entries included “check for voltage.” He survived, but not because of his hazard analysis.
Hazard Analysis in the Workplace
Hazard analysis has one goal: prevent incidents by identifying and remediating hazards. There are many ways to perform hazard analysis and this is just one. The intent of the guide is instead to provide a process for any observer of any skill level to recognize situations that are, or can become, hazards in the workplace. Once a hazard is recognized, the observer can take immediate action to remediate it or, if necessary, seek guidance through appropriate resources to deal with the issue.
The Intersect
Known as “The Intersect,” the method used in this guide breaks down hazard analysis into three simple intersecting elements. This simple process provides a methodical approach that aids any observer in an effective job or task hazard analysis.
How to Identify Hazardous Conditions
With the exception of those persons specifically trained in workplace safety, most observers performing a hazard analysis will not know all of the rules for a safe workplace. Unless you have spent many hours studying safety practices and regulations, your knowledge of the rules will be limited. If you approach a safety evaluation based on rules, but with a limited knowledge of those rules, your focus will be on those issues that you may be familiar with to the exclusion of other areas you may not be familiar with.
Safety rules are a compendium of knowledge formalized as a training and prevention resource. Safety rules play a critical role in preventing incidents. Whether the person performing a job hazard analysis is a seasoned safety professional trained in evaluation protocols or a craft worker with a handbook, job hazard analysis begins the same way – with the identification of hazards. Given a little guidance, most craft persons will intuitively identify potential hazards using general concepts even though they may not know rules specific to the situation.
The Intersect Between Worker, Tools, Task and Environment
The reasoning behind The Intersect is creation of a methodical approach using general concepts to enhance effectiveness of the process. In its most simple form, the conceptual observer looks at the points of intersect of worker, tools, task and environment to identify conflicts. Those points of The Intersect are where flesh meets threat. A methodical approach using intersects creates points of focus in a work space, allowing even the untrained observer to identify hazards.
The Intersect Between Worker and Tools
Human intelligence has overcome the limitations of the human body, producing tools to perform tasks. Tools are extensions of the human body, but they lack feeling, emotion and worst of all, safety sense. Tools are usually hardened human extensions that use amplified or concentrated force to perform a particular task.
Look at the tools the worker is using. Whether they are power or nonpower hand tools, The Intersect question is, “What is it about this tool that can hurt the worker using it?” Here are several suggestions typical of tool hazard exposures:
• Do tools throw off flying debris? If so, face shields or goggles may be required.
• Have tools been altered from their original design?
• Do tools have exposed cutting, burning, penetrating or abrasive components? If so, protective gloves may be required.
• Do the tools in use produce any forms of radiation such as ultraviolet light, heat or magnetic energy? Barriers may be required.
• Does use of the tool produce dust or fumes? Respirators may be required.
• Are tools in use designed for the task?
• Does manipulation of the tool produce unreasonable stress on the operator that may result in injury over a prolonged period?
• Is there special training required to use the tool?
• In using the tool, can the tool be dislodged from the work, exposing the worker to injury?
• Is there any hazard to the worker from energy supplying the tool?
• Does using the tool endanger bystanders?
• If the tool requires maintenance or adjustment, is the operator properly trained to perform those operations safely?
The Intersect Between Worker and Task
Workers must be qualified to perform a task. Qualification is a function of training and/or experience. While a task has its own goal, each task is a constituent act toward accomplishing a defined goal or job. We make this differentiation because a frequent error in task analysis is the failure to break down the tasks to effectively perform a hazard analysis. For instance, a job is installing cable in a trench. That job is completed by effectively executing a series of tasks that might include inspecting equipment, unloading equipment, operating a trencher, unloading materials, fueling equipment, setting up barricades, gluing PVC, excavating by hand, installing shoring, setting up a puller, pulling cable, installing a junction box, making terminations and so on. Tasks usually require decision-making, order or process, and human activity that may interface with tools or equipment. Examination of The Intersect between worker and task begins with qualification and moves through order, process and activity. The Intersect question is, “What is it about this task that can hurt the worker performing it?”
Here are several suggestions typical of task-related hazard exposures:
• Is there special training required?
• Are there manufacturer’s procedures to be followed?
• Are there physical or repetitive stresses created by the task?
• Are there position or line-of-fire concerns?
• Does the task create hazardous exposures requiring protective procedures?
• Does the task create hazardous exposures requiring PPE?
• Does the task create hazards to others nearby?
The Intersect Between Worker and Environment
There are many components to concerns about the worker’s environment. Environment might concern weather at some workplaces or confined conditions in another. Environment can be affected by chemicals, noise, dust or radiation. Environment can also be affected by construction equipment or traffic on nearby streets. Some environments are fairly safe, such as a well-appointed workstation in an ergonomic environment. Other environments – for example, power plants – contain high voltages, airborne contaminants or pressurized systems that by their very nature create exposure to the worker. Using visual borders, such as extended as opposed to close proximity to the worker, helps to manage the task of examining the environment. The Intersect question is, “What is it about the work environment that can hurt the worker?”
The Extended Environment
Housekeeping or extended hazards may not necessarily be in your control. In large-site work spaces there are a host of activities that may use energy or chemicals, or produce hazardous byproducts that could become a threat to workers. In construction there are often other crafts or companies at work. They may perform work or use processes or equipment that you or your workers are unfamiliar with, creating unusual exposures. While their safety program is not under your control, injury to your workers is. It is reasonable to extend your observation of the workers’ environment into the realm of the other crafts. Look for hazards such as:
• Hazards of slips, trips or falls, particularly rough or slick walking surfaces
• Other crafts working above your workers
• Transfer or use of chemicals, solvents or flammables in the work area
• Partially completed work that leaves drop-offs near your work areas
• Material handling or other crafts swinging loads
• Use or moving of equipment in the area around your workers
Close Environment
Moving from the extended environment inward, observe the worker’s close work space. Begin at the worker and scan outward into the work space.
Close environment hazards are those such as exposed electrical systems, mechanical threats, heat, cold, fumes, and sharp or penetrating hazards.
• Within the worker’s area, are there objects that will penetrate, trip, nip, crush, burn or otherwise injure?
• What factors in the worker’s environment drive the need for PPE?
• What environmental conditions within control of the worker are hazardous?
• What environmental factors outside the control of the worker are hazardous?
Work-site hazard analysis is the singular most effective way to prevent incidents that injure workers. It does not matter how much experience, training or expertise a worker possesses – without hazard analysis and remediation, incidents will happen. Task hazard analysis is the tool that makes dangerous jobs safe. Whether it’s craft-related or safety-related, planning is the mark of a professional. Plan your work, work your plan. It’s very simple: When it comes to preventing injuries, it really hurts to be wrong.
About the Author: After 25 years as a transmission distribution lineman and foreman, Jim Vaughn has devoted the last 15 years to safety and training. A noted author, trainer and lecturer, he is director of safety for Atkinson Power. He can be reached at jim.vaughn@atkn.com.