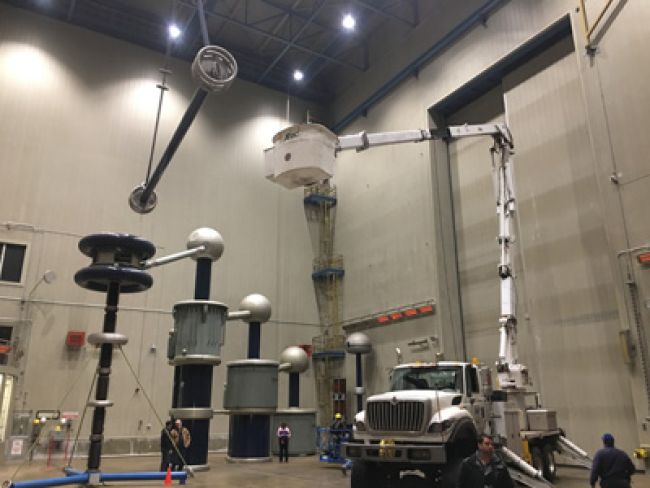
Safety Success During an Insulating Boom Flashover
Salt River Project, or SRP, is a power utility located and operated in the greater Phoenix area. Created as part of the federal Reclamation Act of 1902, it was originally established to help secure a reliable water source to the desert valley. Today, SRP not only provides reliable water – it also supplies reliable power to over 1 million customers, operating and maintaining all of its own assets, including generation, transmission and distribution.
The utility has a successful 500-kV barehand/live-line program that dates back to the late 1970s. In the fall of 2018, SRP experienced a boom flashover event during preparation for 500-kV barehand work. The procedures the utility had developed over the history of its barehanding program, and the crew’s careful execution of those procedures, saw everyone return home unharmed on the day of the incident.
Safety procedures sometimes are developed following an injury or incident that may have occurred a long time ago. In our industry, we often adhere to procedures without having personally witnessed why they exist. The 2018 event is one case where we got to see up close and personal why SRP’s safety procedures are so valuable. We have a very tight-knit group where you don’t just know the crew members; you know their families, too. Our safety culture exists in service to a broader community.
As a 20-year lineman, I feel it is imperative to share these types of experiences in hopes that they will inspire others to do the right, safe thing. When I first entered the trade at the age of 21, the safety culture was much different than it is today. The “just get it done, any way possible” mentality often prevailed over the slower-yet-correct way of doing things. Today, employees of our utility take pride in looking for ways to improve policies and procedures that will increase safety and proficiency. We have adopted this theme: “At SRP, we work safely for our families, our health and each other, including the communities we serve.” The experience I’m about to detail in the remainder of this article highlights how unforgiving energized work can be. It warrants an ongoing reassessment of best practices and an unwavering commitment to execute those practices every time we go to work.
What Happened?
In October 2018, SRP’s Transmission Line Maintenance (TLM) group was tasked with assisting in de-energizing and changing out a bad-order 500-kV disconnect switch. The job was to be performed using barehand procedures to remove energized jumpers from the receiving yard’s bus down to the open 500-kV disconnect. With the jumpers removed, SRP’s Substation Maintenance group could replace the bad-order disconnect. SRP felt strongly that using the barehand procedure would improve the resiliency of the system by eliminating an outage on the west 500-kV bus.
As with any major piece of work, pre-job operational checks needed to be carried out. SRP energized the insulating work platform remotely, without personnel, as the final operational check to ensure that the unit was in proper operational condition before starting work. During this final safety check, the boom experienced a flashover that resulted in a 500-kV phase-to-ground fault over the barehand unit.
What We Did
After the incident occurred, the main objective was to verify the safety of all the crew members. When it was determined that everyone was safe, our focus quickly moved to what had happened. The TLM group not only immediately placed a call to SRP’s Fleet Engineering group but to the bucket truck manufacturer as well. The manufacturer performed an on-site investigation that yielded little information. SRP also did an internal investigation using the knowledge and expertise of its various departments and an independent third-party investigator. The TLM group began an extensive review of all our barehand standard operating procedures, and SRP also enlisted the assistance of a third-party expert to review and identify any areas that could be improved. In all cases, the results provided no significant findings. These initial reviews helped to verify that the procedures the crew followed that day were in line with industry best practices.
Next, SRP decided to continue to dig deeper in hopes of identifying the root cause of the flashover. We sent the bucket truck in its post-flashover state to Bonneville Power Administration’s (BPA) high-voltage test lab in Vancouver, Washington. Using a laboratory-controlled setting, the goal was to recreate the incident that occurred in Arizona. A team of SRP employees, BPA engineers and Electric Power Research Institute subject matter experts exposed the bucket truck to a variety of worst-case scenarios. The vehicle passed every test needed to certify its use for 500 kV, even in its compromised condition following the flashover. It was not possible in the BPA laboratory to replicate the field incident.
At the completion of the BPA testing, SRP shipped the truck to the manufacturer’s facility for a complete teardown. Piece by piece, the unit was taken apart, and the manufacturer inspected each piece individually for flaws and defects. Once again, the investigation turned up no significant findings.
What We’re Doing Differently
To date, SRP hasn’t established a definitive root cause for the flashover incident. Based on the manufacturer’s specifications, the truck met all the appropriate criteria and was deemed to be in good operating condition. A yearlong investigation and many conversations with experts have reinforced our belief in and commitment to following good policies and procedures. Even though the incident could not be recreated, the TLM group identified four additional procedural steps to use moving forward. These additional actions are intended to help mitigate the risk associated with barehand work.
- Create a checklist similar to the checklist used in the aviation industry prior to the pilot taking flight. The crew is expected to use this checklist each and every time barehand work is performed. The majority of the checklist items were previously followed, but we did not have all the items listed in one location.
- Increase our safety factor by not using an insulating boom shorter than 14 feet to conduct barehand work.
- Prohibit barehand work in humidity greater than 60%.
- Reduce our leakage current meter threshold setting by 60% to provide earlier warning for crew members in case the leakage current increases rapidly.
What We Learned
How could a 500-kV flashover event like this end with no injuries? It all stems from SRP’s 40 years of experience in barehand/live-line work and crews following well-established procedures and safety guidelines. In this incident, the truck saw nearly 65,000 amps of fault current without catching fire. Parts and pieces blew off the truck, yet they all landed within the safety perimeter that we created around the unit, in accordance with SRP’s existing procedures.
Ultimately, strict commitment to our procedures kept crew members safe even when the unexpected and unthinkable happened. Everyone on the crew that day was committed to “doing it right.” This commitment to established policies and procedures allowed us to fail safely, which was the key to protecting all employees. It is very easy in our day-to-day operations to take shortcuts from time to time. My belief is that you never know when an incident like this may occur. Therefore, you cannot afford to take the day off or use shortcuts. You need do the job right every time.
While there are still no obvious reasons or conditions that led to this incident, one thing is clear: SRP’s procedures and the crew’s commitment to following them sent everyone home safely when it counted. Even though there are still many questions about the cause of this incident, we view it as a safety success and plan to continue looking for opportunities to improve in the future.
About the Author: Jace Kerby has spent 20 years as a journeyman lineman and currently serves as the manager of the Transmission Line Maintenance group at Salt River Project.
- I’ve Got Your Back: Lessons in Socio-Biomimicry
- Lessons Learned from the Tenerife Airport Disaster
- Safe Transportation of Leaking Transformers
- Safety Success During an Insulating Boom Flashover
- A Practical Review of the C2-2017 National Electrical Safety Code
- Is it Maintenance or Construction?
- August-September 2020 Q&A
- Decision Making: Make Balanced Decisions and Avoid Biases