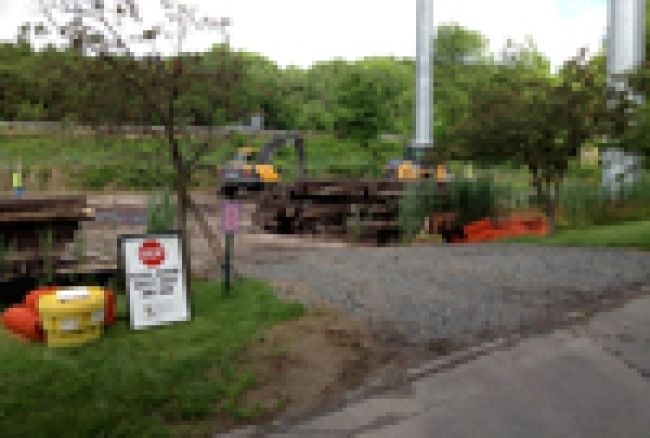
Raising the Bar, Lowering the EMR
Today, many contracting companies in the maintenance and construction industries are facing mounting pressure from utility owners to rethink their health, safety and environmental (HSE) cultures and work practices, which in turn can lower their common HSE indicators. Those companies that fail to meet client demands often find themselves excluded from bid lists while they search for a catalyst of cultural change. In this article, we will explore how Supreme Industries – a contracting company that specializes in right-of-way (ROW) clearing, environmental and sedimentation controls, access roads building, site development and ROW restoration – lowered its experience modification rate (EMR) from 1.12 to 0.64 in just three years.
What is an EMR?
“The EMR is developed by the National Council on Compensation Insurance, which acts as a repository of workers’ compensation loss experience and payroll information that insurance carriers use to calculate the cost of workers’ compensation insurance,” said George Males, vice president and loss control consultant for Lockton Companies, the world’s largest privately owned, independent insurance brokerage firm.
A good EMR is anything less than 1.00, according to Males. “The significance of maintaining a good EMR shows that a policyholder has something going right in their operation, that being little or no losses, but also a safety culture within that operation to stop losses before they happen through safe work practices, training and hazard assessments,” Males stated. “Needless to say, any policyholder with a significant credit in their EMR speaks volumes on their progressive methods and safe work practices.”
The Short Answer
How did Supreme Industries lower its EMR from 1.12 to 0.64 in three years? The short answer is that the company took three major steps:
1. Planning: The HSE program and operational mindset were revamped from the ground up.
2. Training and empowering: Workers were taught hazard recognition and mitigation, and they were expected to use this training to take action.
3. Evaluation: Field work was audited, emergency preparedness drills were conducted, and lessons learned and opportunities for improvement were communicated.
The Longer Answer
Supreme Industries was started by Kevin Boucher in 1982 with a couple chain saws, a skidder and a truck. “In the early days there were times when I would have to work all day with the guys cutting and skidding, and then I would have to load and haul wood by myself often until as late as 1 a.m., only to repeat the process for days and weeks on end,” Boucher recalled.
Like many young companies with young and seemingly indestructible leadership and workers, Supreme got the job done by any means necessary. However, as it matured, lessons were learned – often the hard way, with varying costs of tuition. “I think every company has to go through a growth and development process,” Boucher said. “For Supreme, safety moved to the center stage around 2008 when our clients started reviewing our work practices and EMR and began to demand that we rethink our safety philosophy and change our corporate culture. So that’s what we did. The command for change came from me, but the initiative was spearheaded by the next generation of Supreme leaders – my sons, Gavin and Nathan – and it resulted in the development of several HSE initiatives and the addition of a dedicated project-level safety professional to coach the workers in safe work practices and hazard recognition.”
Additionally, in early 2010, after several corporate planning sessions about how to best capitalize on project-level safety gains, as well as an intensive candidate search, a corporate safety leader was hired. Since then, numbers indicate that there has been an increased level of HSE awareness among workers, fewer incidents, and more efficient and profitable production in the field.
Corporate HSE leadership attributes the reduction of Supreme’s EMR rate and the overall success of the company to true collaboration between the HSE department and corporate and field managers to develop an HSE program. Everyone worked together to train and coach the program in the field. Without a group effort – dynamic personalities to market and sell our program to supervisors and workers, champions to support us from the top, professional field HSE managers and workers in the field who bought what we were selling – the program would have failed.
Cultural Improvement
In order to lower Supreme’s EMR, the company had to improve its culture. It did this by developing an HSE model that consists of the following components:
Provide Value-Added Training
All workers, supervisors and managers are trained to recognize hazards, mitigate risk and react appropriately during an emergency. This is accomplished through the following training programs:
• New hire and project-specific orientation.
• OSHA construction outreach:
o 30-hour for all supervisors.
o 10-hour for all workers.
• Driver training using the Smith System.
• First aid, CPR and AED with advanced trauma and lifesaving supplements.
• OSHA disaster-site worker 15-hour outreach.
• American Traffic Safety Services Association flagger certification.
• Hazardous waste operations and emergency response.
• Environmental spill prevention and remediation procedures.
Plan the Work
Project and HSE managers review all contractual requirements to facilitate the safe execution of the work with minimal impact on the environment and inconvenience to the surrounding community.
Assess Hazards and Mitigate and Communicate Risk
The project superintendent and HSE department review the work to determine the project-specific hazards, including environmental hazards of the work area. This leads to the development of work guidelines that are communicated to employees and visitors verbally and/or in writing by means of:
• Job hazard analysis (JHA) – A collaborative development between field and HSE managers, JHAs explain safe work practices for routine tasks and are communicated to workers during orientation, annual training and pre-work job briefs. JHAs consist of the following information:
o Description of the work.
o Steps associated with accomplishing the work.
o Potential hazards and likely situations.
o Recommended safety procedures for the given hazard or situation.
• Job safety analysis (JSA) – Developed by the field site supervisor, JSAs document and communicate to workers and visitors a description of the work to be performed, the hazards of the planned work and risk mitigation requirements with the following information:
o Date that the work is to be performed.
o Time that the JSA was initially reviewed with the work crew and visitors.
o Work area emergency response location.
o Identification of the JSA leader and the site supervisor.
o Description of the work to be performed.
o Applicability of JHAs to the work being performed.
o Description of abnormal/nonroutine operating risks that are not covered by applicable JHAs.
o Required PPE for the work to be performed.
o Visitor precautions; these are simple precautions for those who may not be familiar with the work being performed.
o Signature of compliance.
o Notation of incidents or near misses that occurred during the day.
• Site walk – Conducted by the field site supervisor before work begins, a site walk documents and communicates to workers and visitors the physical hazards and environmental risks of the area in which the work is to be performed. Additionally, a second site walk is conducted after work is secured for the day to ensure that the area is free of hazards that could be encountered by members of the public who may attempt to enter the unattended work site during nonworking hours. The following questions are asked during site walks:
o Are widow makers – hanging tree limbs – inspected and removed before and after work?
o Is the JSA and site walk documentation posted for review by workers and visitors?
o Is there evidence of overnight site tampering?
o Are overhead and underground utilities identified?
o Is public protection required/established and inspected before and after work?
o Has all equipment been inspected?
o Are environmental controls required/functional and inspected before and after work?
o Is work being conducted in wetlands, culturally sensitive or other work restrictive areas, and are work requirements met?
o Are encroachments identified?
o Are toilet facilities and water provided?
• Site-specific JSA – In the event of nonroutine work, or routine work being conducted in a nonroutine physical environment, a site-specific JSA is developed by the HSE department in collaboration with the site supervisor and workers to mitigate risk to employees, visitors and the environment.
• Work site entrance warning sign – A warning sign is placed in a prominent location near the entrance of the work site that communicates the following notifications:
o The area is a Supreme Industries’ work site.
o Only authorized personnel are permitted on the work site.
o Applicable JHAs, JSAs, site walk documents and/or site-specific JSAs must be reviewed and requirements noted in each document met and agreed to by signature prior to entry into the site.
o All work site entrants must check in and out with the work site supervisor.
Prepare for Emergency Response
Supreme Industries never proceeds with work in any area where it anticipates an emergency will occur, but it does plan for emergency response at every work site in the following ways:
• The physical location is noted on the JSA so it can be rapidly provided to EMS personnel.
• Workers are provided with first aid and advanced lifesaving trauma kits, environmental spill kits and fire extinguishers, and are trained to properly inspect and use them.
Assess HSE Effectiveness While Working
Workers continually evaluate their work environments and exercise stop-work authority when working conditions present unexpected or unplanned risks to workers, visitors or the environment. When work is stopped, a stand-down meeting is conducted, work site hazards are reassessed, risk mitigation plans are modified or developed to include the unexpected hazard, and the modified or new work plans are communicated to workers and visitors. If the risk associated with the hazard cannot be immediately mitigated, the work will not resume until it is.
HSE Auditing and Coaching
All field supervisors and project managers conduct HSE audits and coach workers to ensure that there is no gap between corporate HSE philosophy and field HSE practice.
“This is how we dropped our EMR from 1.12 to 0.64,” Boucher said. “Staying vigilant and empowering workers to own their work environment is how we’ll maintain it and maybe even reduce it further in the future.”
Future Plans
Supreme plans on continuing growth in its current markets and expanding in two directions:
1. Disaster recovery through helping municipalities and states clean up after nature deals them a blow.
2. Going green(er) via reducing our generation’s environmental footprint by expanding our current waste reduction facilities to include the introduction of biomass waste that returns nutrients back into the environment. Additionally, Supreme is pursuing the use of new technology capable of transforming contaminated wood – such as railroad ties and telephone poles – and other construction debris into environmentally safe fuel that would help reduce our country’s dependence on foreign oil.
About the Author: Jesse Hardy, CUSP, is the director of HSE compliance for Supreme Industries. He has 20 years of experience developing and delivering value-added education that leads to cultural change. Hardy is also a recipient of the National Safety Council’s 2012 Rising Stars of Safety award. Inquiries regarding Supreme’s HSE success can be directed to jhardy@supremeindustries.com.