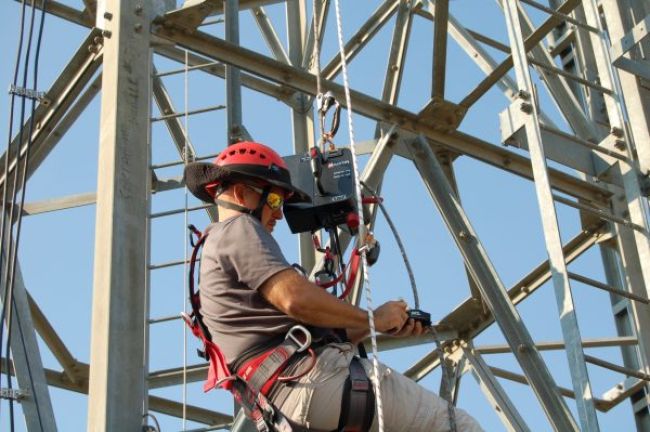
Powered Ascenders in the Utility Space
Image courtesy of Ronin Revolution Corp
Due to the nature of the job, lineworkers may be required to climb several hundred feet – perhaps multiple times per day – just to get to work. Studies show that reducing worker fatigue has a significant effect on lowering the number of on-the-job incidents. And recent advancements in battery technology plus fierce competition in the powered ascender space have made these devices more common in the workplace. But what exactly is a powered ascender, and how can it help reduce worker fatigue?
The concept of powered rope-climbing assist devices has been around for decades. Commercially available and modified home-built units began appearing on job sites in the 1990s. Original units were modified two-cycle engines adapted to rudimentary capstan hoists. Until recently, many offerings were either exceptionally expensive or consisted of a modified descent device run off an electric drill. Contemporary units maintain a similar design ethos, with nearly all systems designed in such a manner that the mainline rope runs over a powered drum or sheave. Thanks to the recent advancements in electric motors and batteries, there is now a proliferation of reasonably priced, well-engineered ascenders made of quality materials that are durable, safe and effective. Though hardly inexpensive, their cost can be recovered in about a year or less. Still, why would someone choose to introduce powered ascenders into their fall protection system? And what user training is required before implementation?
Manufacturers and Options
There are several manufacturers of electric and gas-powered ascenders; most are larger manufacturers of fall protection safety equipment, but there are also a couple manufacturers whose work is dedicated solely to ascenders. Each manufacturer offers several different versions of their ascenders, some geared toward search and rescue, some geared toward hoisting equipment and others geared toward tactical applications. The fundamental differences between these units are the rate of ascent and the capacity. Most industrial ascenders offer variable throttle and will allow users to ascend a fixed rope at approximately 2 feet per second. The industrial ascender is at least twice as fast as climbing using traditional methods.
This article focuses on those ascenders specifically intended to hoist people to the job site, whether it’s above or below ground. At the time of this article’s publication, powered ascenders range in cost from several thousand dollars up to $10,000 or more for some specialized models. Regardless of make or model, each ascender is designed to work as part of a system in addition to the existing redundant backup or fall-arrest system. In many cases, existing climbing equipment will be sufficient for the system, although specific consideration should be given to harnesses, ropes and backup systems to ensure that none of them interferes with the other components.
The initial cost of investment is affected by the individual device, its features and the components that are included; the more expensive options generally ship with more bells and whistles. These can include a Bluetooth remote, a hard-sided transport case and charging provisions, and some even have powered reverse. Typically, these devices fall into two broad categories: units powered via electricity stored within a battery and units powered by a small, two-cycle gas engine.
Electric units have several key benefits over gas-powered devices, which have led them to become the preferred option; that’s also due in part to recent improvements in lithium-ion battery technology. This battery chemistry allows for greater energy capacity in a much smaller footprint relative to older battery technology. Further, this battery style allows for shorter charge cycles and thus less downtime. Generally speaking, these units offer smooth, quiet, efficient operation. This efficiency combined with high-capacity batteries allows users to ascend up to 350 feet of rope on a single charge, although most units offer hot-swappable battery function, which enables the user to remove a discharged battery and replace it with a fully charged battery at any point of ascent, with special consideration given to dropped-object prevention; this can provide nearly limitless range. Additionally, many electric units offer the ability for remote control – a handy feature for an injured worker – which can be used to return the device unloaded or control the device from a remote location. Lastly, these electric units may be suitable for use for indoor or underground hauling, lifting or access operations depending on the hazards present and the device certification/design parameters.
Meanwhile, gas-powered ascenders have nearly unlimited range and can be refueled with standard premixed gas and oil. They can also be less expensive initially as they do not require additional chargers or extra batteries. But combustion engines are noisier and produce harmful emissions as well as significantly more vibration. For workers solely operating outside, these issues are likely not of much concern, but they prevent the use of gas-powered ascenders underground and indoors when there’s insufficient ventilation.
Regarding electric ascenders, the initial investment – including multiple batteries for larger jobs – can be significant. And as with any electric device, the time to fully charge a depleted battery should be taken into account, with sufficient spares available to complete the task at hand. Range, lift capacity and rate of ascent will likely be affected by extreme temperatures and should be considered when purchasing spare battery capacity. Batteries should be stored per manufacturer recommendations and isolated from extreme weather, shocks and falls.
Addressing Uncertainty
Perhaps the biggest challenge with any powered ascender is the transfer from one mainline to another or movement beyond a significant deviation between the mainline and its anchorage. Though rare and technically feasible, completing a midline transfer or moving past significant deviation requires considerable training, plus preparation and some additional equipment.
And while consensus standards and dedicated training programs are beginning to surface, many safety managers have reservations about these innovative devices – and rightfully so. As with any new technology, the burdens of training and safe use in the workspace are on the employer. Most manufacturers offer basic product orientation, which is analogous to the walk-through when purchasing a new car. The salesperson will typically provide basic instruction for the user regarding controls, loading rope, replacing batteries and adding fuel. Unlike basic product orientation, some professional fall protection training companies have developed dedicated training programs that provide much more detail and background knowledge, similar to a formal driver’s education program in the previous analogy. Certified training is often delivered in a combination of lecture and hands-on learning. Quality programs will begin with a lecture-based model and provide the user detailed training specific to each component of the powered ascender system; topics typically include relevant standards, product design, intended use, rescue considerations, ancillary equipment, anchorage considerations, backup devices and component inspection. This session should then be followed by hands-on training led by a qualified instructor. Further, reputable training organizations will discuss planning for rescue and/or emergency operations. The majority of rescue techniques will be relevant for aboveground work and may include self-rescue, pick-off, skate block and lower from above. It almost goes without saying that other options will be viable, but each scenario should be tailored to the specific job environment and hazards present. Each solution will require dedicated preparation, pre-planning, the necessary gear and at least one competent rescuer.
In a certified training environment, each skill will be based on specific learning objectives and benchmarked against clearly defined standards. These skills will first be demonstrated by a qualified instructor who will coach students. Upon successful completion, students will receive formal documentation of successful skills demonstration that employers can then track in their preferred safety management system. Completing certified training will ensure that all users have received fundamental education on the device and its intended use. Once workers complete basic training, it is important to integrate this instruction into the employer’s holistic safety program, with specific attention paid to new considerations raised by ascending, descending, hauling, hot-swapping batteries and underground use.
Conclusion
With the variety of options in the powered ascender world, crews have another option for use in difficult access scenarios. There is almost sure to be an effective hoisting and lifting option for every budget and each individual scenario. Though legislation lags behind industrial progress, thankfully multiple dedicated training options exist, several of which are turnkey programs that can easily be incorporated into existing safety policy. And despite the potentially significant upfront cost, those dollars can often be recovered in a year or less. Plus, it’s likely there will be an increase in safety due to reduced climber fatigue, reduced repetitive motion and increased efficiency.
About the Author: Ty Fenton is the general manger of Safety One Training, the U.S. leader in backcountry vehicle operation and fall protection training. He can be reached at ty.fenton@safetyoneinc.com.