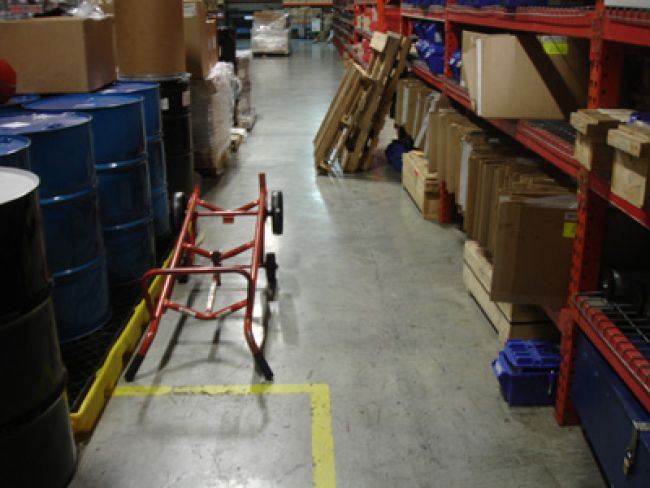
Investigating and Documenting Slips, Trips and Falls
People are affected by gravity at every moment of their existence. There is an ongoing struggle between this planet, which never stops trying to pull things to its center, and humans who are trying not to be overcome by the pull. In the battle against gravity, humans rely on balance, coordination, traction and decision-making. In work environments, employers are responsible for managing hazards; reducing or eliminating hazards that could cause slips, trips and falls; training employees; and investigating incidents to prevent recurrence. The remainder of this article will focus on the investigation and documentation of slips, trips and falls in the utility work environment.
Terminology and Goal
Clear definitions help guide us to clear outcomes, improved safety and reduced risk. People may refer to “slipstripsandfalls” as a single thing, but they are each distinctly different. Slips, trips and falls can occur alone or in combination.
The employer’s goal is to reduce risk of injuries and incidents by maintaining clean, dry, well-lit workplace walking surfaces with appropriate traction that matches the user’s expectations; managing footwear; eliminating trip hazards; avoiding slippery contamination; and training workers.
Traction refers to the friction between a surface and a person’s foot or footwear. It is scientifically described as either a static or dynamic coefficient of friction. Where there is a high-traction surface and high-traction footwear – such as a brushed-finish cement sidewalk and aggressive-tread work boots – it is less likely that a slip will occur. Contamination can change the available traction, such as when there is moisture, oil or ice between footwear and a surface.
A slip occurs when traction is not maintained and there is a loss of control over body position. On a dance floor or the surface of an ice hockey rink, lower traction is desirable. On a basketball court or workplace walking surface, greater traction is desirable. A slip may or may not involve a fall to the surface. If a person has an accurate expectation that a surface has low traction, and the person has good balance and coordination, the person often can compensate by slowing down and taking smaller, closer steps to avoid a slip. When the person is surprised because the actual traction is less than their expectation, a slip often results.
A trip occurs when a person is in motion and the foot or lower leg strikes against something. Body momentum leads to a loss of balance, which may or may not involve a fall to the surface. A stumble may occur as the person alters their gait and attempts to regain their balance. Humans do not normally high-step march but instead swing a leg forward with minimal clearance from the walking surface, so any vertical projection of a quarter-inch or more is considered a trip hazard. People can still trip even if a hazard is in view and well-marked.
There are two types of falls: a fall to the same level and a fall to a lower level. A fall to the same level occurs when a person’s center of gravity moves beyond the point of balance recovery and gravity pulls the body to impact the same surface the person is on. A fall to a lower level involves a fall from the surface the person was on and body impact to a different surface below.
Investigation
Follow a standardized, recognized method to investigate slips, trips and falls. Incident investigation training is available from the OSHA Training Institute Education Centers, National Safety Council, American Society of Safety Professionals and other sources. OSHA has published “Incident [Accident] Investigations: A Guide for Employers,” which is available for free download at www.osha.gov/dte/IncInvGuide4Empl_Dec2015.pdf. The agency strongly encourages employers to investigate all workplace incidents, both those that cause harm and the close calls that could have caused harm under slightly different circumstances. OSHA recommends the following four-step investigation process, using a systems approach to identify underlying root causes:
- Preserve and document the scene.
- Collect information.
- Determine root causes.
- Implement corrective actions.
Documentation
Most companies have a standard incident report for employees or visitors, and a standard first report of injury for employees. Neither form typically captures all the information needed in a slip, trip or same-level-fall investigation. In utility work, the incident may involve a worker, contractor, visitor to utility facilities or pedestrian trying to navigate a work zone.
The initial investigation tends to focus on the “big three”: the walking surface, the footwear and the contaminant. Was the surface clean, dry and clear with adequate traction? Was the footwear sole appropriate for the surface? Was there water, oil, ice, sand, food or dust present? Was the contaminant on the surface or on the footwear? A strong investigation looks well past the big three, especially if a lawsuit is possible.
Structural Issues
Consider structural issues: consult building codes, fire codes, the Americans with Disabilities Act as amended, the Manual on Uniform Traffic Control Devices and OSHA standards to determine if the walking surface complied with applicable standards. Refer to ANSI A1264.1-2017, “Safety Requirements for Workplace Walking/Working Surfaces and Their Access; Workplace, Floor, Wall and Roof Openings; Stairs and Guardrail/Handrail Systems.” Consult ASTM F1637-19, “Standard Practice for Safe Walking Surfaces,” a consensus standard that applies to both new and existing walkways, sidewalks, stairs and other walking surfaces for pedestrians wearing ordinary footwear. For slips, the National Floor Safety Institute’s B101 series of standards addresses coefficients of friction and preparation of traction audit reports.
Environment
Consider the environment where the incident occurred and take photos and/or videos. Did it happen indoors or outdoors? Did weather or precipitation play a role? Were temporary mats deployed and changed properly? Were there loose mats or rugs? What was the lighting like? What was the surface made of, when was it installed and was it consistently the same material throughout? How should the surface have been maintained according to the manufacturer, and how was it maintained? Was there any visible defect, damage or contaminant? Was there wear or deterioration? Was the surface sloped? Were there holes or gaps in the surface or changes in level? Were there any warning signs or indicators of the hazard?
Personal Statements and Footwear
Take the written statement of the person who slipped, tripped or fell, along with the statements of any witnesses. Capture details about what happened before, at the time of and following the incident. How was the person moving? Were they standing, shuffling, walking, striding or running (straight or turning), upslope or downslope? Were they talking, texting, carrying anything, or physically or mentally distracted? Using a cane or other device? Impaired by fatigue, medication or substances? Wearing glasses or contact lenses? Did they see the hazard and try to avoid it? How far did they fall, how did they land and what body parts were injured? Who provided first aid or medical care? Photograph their footwear, including the brand and model, and the condition of the soles.
Organizational Records
Examine organizational records. Have there been previous incidents or complaints related to walking surfaces in that area? What janitorial services affect the surface? When were they last provided? What products were used, and were application instructions followed? Has the surface previously been assessed for a static coefficient of friction and/or a dynamic coefficient of friction using an approved tribometer and measurement process?
Report of Findings
Prepare a report of findings. The corporate safety department and/or corporate attorney should help with preparing the report. For guidance, there are excellent resources in ASTM F1694-14, “Standard Guide for Composing Walkway Surface Investigation, Evaluation and Incident Report Forms for Slips, Stumbles, Trips, and Falls.” Keep all notes, photos, sketches, statements and so forth according to your agency’s records retention policies. Consult legal counsel before altering or discarding any information if a lawsuit is possible.
Updated OSHA Standards
OSHA standards establish minimum legal standards for workplace safety programs. In 2017, OSHA updated general industry walking and working surface standards, and employers now have specific duties and responsibilities. OSHA 29 CFR 1910.22 requires employers to keep walking surfaces clean, orderly, sanitary, dry to the extent feasible and free of hazards. The employer also must inspect, maintain and repair the surfaces.
OSHA 1910.22(d) requires the employer to ensure walking-working surfaces are inspected on two different schedules: regularly and as necessary. Paragraph 1910.22(d) also requires that hazardous conditions on walking-working surfaces be corrected immediately or be guarded to prevent employees from using the surface again until the hazard is corrected or repaired. Once-a-shift inspection at building entranceways may not be enough in a rain or snow event. Ongoing inspection may be required in a cafeteria food line where dropped food items can create slip hazards. Utility truck walking and stepping surfaces should be inspected each shift.
OSHA construction standards 29 CFR 1926.25, 1926.34 and 1926.250 require exit routes, aisles and passageways to be kept clear and in good repair for free and safe movement of employees and equipment.
Suitable resources must be available to guard a hazard, such as warning signs or barriers that effectively direct people safely around the hazard. Consider visually impaired employees who may not be able to see protective devices and available lighting in the area. Also consider distracted walkers who may be focused on their mobile devices rather than their environment.
Compromised Hazard Controls
Routinely inspect for hazard controls that have become less effective over time. Traction tape can wear through, stair tread covers can become loose, brightly colored warning paint can fade, and warning signs can be damaged or disappear. Hazard controls show that the organization was aware of the hazard, and failure to maintain warnings will not be well-received by OSHA or a jury.
Summary
A strong investigation identifies hazards and system weaknesses so that the employer can improve controls and reduce risk. Getting to the root cause or causes helps to prevent similar incidents from occurring. For a safer tomorrow, strengthen your investigation of slips, trips and falls today.
About the Author: Chip Darius, CUSP, OHST, CET, CSHO, is founder and president of Safety Priority Consultants LLC (www.safetypriority.com). He has provided safety consulting and training services to construction, utility and general industry clients since 1991. Darius serves on the AGC of America Health & Safety Committee and is frequently called upon as an expert witness in safety-related legal matters.