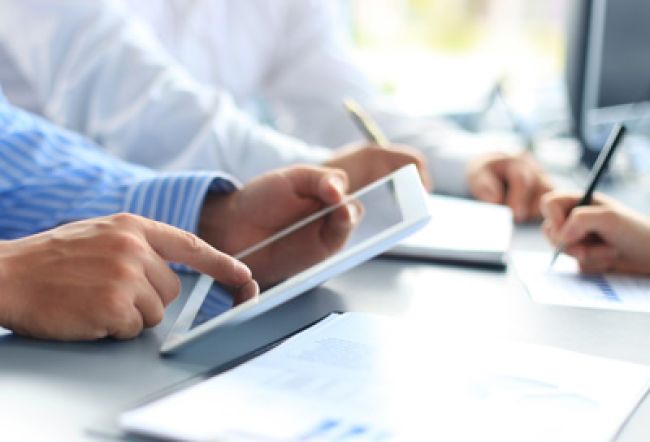
Collaborating for Safety
One of the most vital responsibilities a utility fleet has to its customers – which typically include operators, field management and corporate management – is to provide vehicles and equipment that meet operational and corporate objectives. Those objectives also must be met without compromising the safety of the operators, other workers or the general public.
So, how does fleet uphold safety as a core value while managing all of the other objectives that the department and its customers have – particularly when those other objectives appear to, at times, directly conflict with the safety objective?
The fact is that if only fleet itself attempts that task, it will not only be daunting but nearly impossible to execute. However, success in the area of fleet safety is not only possible but attainable when fleet works with its customers and business partners to understand their needs and challenges. So, let’s review three areas – communication, data analytics and customer buy-in – in which fleet and other work groups can collaborate to help assure safety on the job.
Communication
Communication is a critical part of the foundation of any successful partnership. In today’s world of smartphones and email, there are more avenues than ever for fleet to communicate with the organization’s safety and field teams. But is there still room for improvement? Most fleets do a good job of getting information out to the field. Typical examples include recall notices and technical bulletins, and email certainly provides a quick way to communicate to our teams a great deal of data in a short amount of time. But does each recipient of the data actually get the message?
In order to make certain that the right message is going to the right group, the fleet department, the safety department and the affected field organization should collaborate prior to sending out the message. This is a key step to ensuring the information going to the field is accurate and doesn’t fall flat. Without this pre-check, a few counterproductive things could happen. First, inaccurate or obsolete data could be sent out, potentially hindering safety efforts and killing your credibility. Collaboration between fleet, safety and field management can eliminate any errors in the message. Second, if the subject of the message is a change to a regulation or safety practice, blindsiding field workers – and their supervisors – with the change can cause emotional reactions. These reactions typically will be unproductive and can dilute the content of the message. When fleet works with the safety and field groups before the message is disseminated, all three groups have the opportunity to provide feedback on how to craft the message. This will have the additional benefit of creating awareness among management of any potential emotional reactions that may occur after the message is communicated. Most importantly, not consulting with your partners prior to sending the message could break down trust between the groups. When fleet includes its safety and field partners while assembling the message, it helps to build the trust needed to assure all safety communications are understood by those who receive them.
Data Analytics
Fleet, safety and field management have a great deal of data available to them today that was not available in the past – think telematics and GPS. Many organizations that have embraced telematics have done so with specific singular goals: to reduce fuel spending, use predictive maintenance tools, utilize fault codes to predict component failures, and monitor the productivity and efficiency of field crews. In addition, many safety departments possess a good deal of data on reportable safety incidents, vehicle accidents and the financial impacts of those events. So, how do the fleet and safety groups within an organization collectively utilize their data resources to positively impact the field and their safety performance?
The first step in utilizing all of the data points from multiple work groups is to confirm the quality of the data. As noted in the “Communication” section above, using inaccurate or bad data in any analysis will always yield inaccurate or bad results. That could lead to an erroneous determination of a root cause for a given issue and, ultimately, spending time, talent and treasure to fix the wrong problem.
Once the data quality is verified, the analysis can begin. It will be most effective if all three groups – fleet, safety and field management – are engaged and working toward a common goal of determining what the data is saying. Each of the three groups is needed since the data will tell each group a specific story and could be slanted to favor one group at the expense of another. Having all three groups involved in the analysis helps to assure this potential area of bias is minimized.
When the analysis has been completed, the results must be presented in a way that gives the audience a clear vision of what the issue is and what the path forward should be to address what the data is saying. This is where many organizations simply present data in a format that does not translate well to the audience. Ideally, the data should be presented in such a way that the person looking at it can determine what is being presented after a quick glance. Any analysis of data also should be accompanied by simple, actionable recommendations as to how to correct the issue in question.
Customer Buy-In
A good communication plan and a strong data analytics strategy aren’t worth a whole lot if all the groups involved – fleet, safety and the field – don’t buy into them. So, how can fleet achieve buy-in from the other two groups?
The first place to start is at the top because that’s where the safety culture – as well as the culture of the entire organization – begins. Providing a united front among the three working groups to senior leadership helps to obtain senior-level engagement and shows field workers that everyone is on the same page from a safety perspective.
Once senior-level buy-in has been obtained, field buy-in is the next item to seek out. This can be done with fleet and safety personnel going out to the field to deliver the safety message directly to crews.
Summary
Effective collaboration between fleet, safety and the field is an achievable goal. Developing a robust communication plan, using analytics and gaining customer buy-in are the keys to success in this area.
About the Author: John Adkisson is the corporate head of fleet services for Asplundh Tree Experts LLC. He is responsible for managing a diverse fleet of over 45,000 assets, including on-road vehicles and power-operated and trailed equipment.
- Are You Taxing the Variables?
- Collaborating for Safety
- Arc Flash Considerations for Utility and Construction Activities: Part II
- Aerial Equipment Innovations Aim to Protect Your Workers
- Train the Trainer 101: FMCSR Awareness
- Voice of Experience: Human Performance Failures
- February-March 2020 Q&A
- Learning Styles: Implications for a Trainer