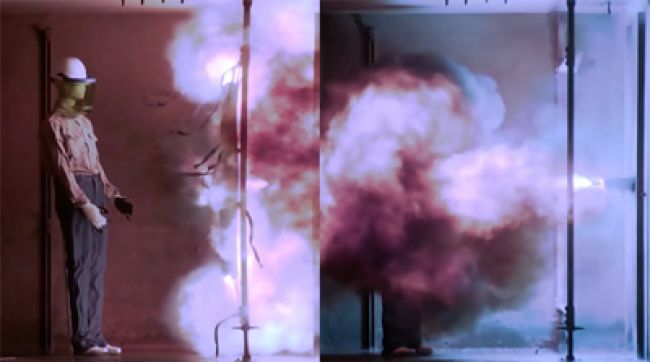
Best Practices for Arc-Rated Clothing Programs
Many things have changed since 1994, when the first hint of arc-rated (AR) materials hit the utilities. Back then, the best practice was to wear cotton jeans, heavy cotton shirts and heavy cotton-shell winter wear. Other personal protective equipment (PPE) like rainwear illustrated an industry problem: There were not many good flame-resistant (FR) clothing options available. At the time, the only markets for FR garments were military, aviation and refineries. Non-melting rainwear was not really on the market since most “FR” rainwear at that time was made of nylon or polyester, which means it melted and thus didn’t meet OSHA requirements.
In the years immediately following the promulgation of the 1994 version of OSHA’s 29 CFR 1910.269 standard, a few utilities began using AR shirts. However, in a 2001 IBEW survey, only 68 percent of utilities reported using AR shirts and rainwear. There was a false belief that cotton was somehow FR, but this was a misinterpretation of ASTM data provided to OSHA about heavy, 11-oz/yd² cotton. Any utility that had done calculations using ARCPRO – software that computes the thermal parameters of electrical arcs – knew it was basically impossible to justify not moving to AR garments given the available data. In the same IBEW survey, 70 percent of respondents reported using FR clothing – which was commonly used interchangeably with “AR clothing” at the time of the survey – as part of a uniform required by the company for which they worked. The tides were turning even then toward company-provided AR garments for line technicians.
In 1994, there were just a few FR fabrics on the market. There were no sanded jeans, no plaid FR shirts and no camo AR shirts. There were no arc ratings, nor any AR denim. Today the largest denim manufacturers in the U.S. offer many styles of AR and flash fire-rated denim. Things have changed for the better in terms of worker safety and clothing comfort, style and cost. While many people consider AR garments expensive, the reality is that most cost the same now as they did in 1994. And when inflation is factored in, they are actually less costly for today’s consumers than they were 10 years ago.
Working alongside our partner, Kinectrics, my colleagues and I perform most of the world’s arc testing. Textile testing for arc flash and flash fire takes place in our ISO 17025-accredited labs. We also sit on the ASTM, NFPA, IEEE and IEC committees related to arc flash and flash fire. We do not sell AR shirts, pants, coveralls or flash suits, but we do have opinions about best practices based on our involvement in more than 150 accident investigations and extensive experience in arc testing. AR garment fabrics, styling, fit, comfort, durability and protection have improved considerably as the market has grown. Even with all this change, however, there continues to be resistance to providing AR clothing as well as some resistance to wearing it. OSHA’s 2014 update to the 1910.269 standard makes it completely indefensible for employers to fail to provide and require employees to wear AR garments, but some best practices for AR worker protection are still not clear in the standard.
From PPE to Daily Wear
It is critical that we begin to consider PPE as daily wear within the utility industry. Many people continue to believe they can get by without wearing AR garments as daily wear. Yes, purchasing AR garments can be costly, but doing so will save lives and increase productivity. A single trip to retrieve a flash suit will cost more than a pair of AR jeans when you consider travel time and the lost productivity of a line technician. And, according to a 1995 PECO study, the cost of one accident will pay for AR clothing for up to 3,000 workers for five years. It makes sense, so just do it. Implement a PPE daily wear program to eliminate or reduce the number of trips for flash suits, and instead use AR layers for protection. This could save thousands of dollars in flash suits. AR rainwear, winter wear and many layered systems can provide more than 40-cal/cm² protection with two to three layers. Merely carrying AR rainwear tested with your garment materials on a truck could eliminate the need for a worker to have a flash suit or travel to retrieve one. Typically, winter wear will also serve as a protective flash suit. Carrying a suit on board for higher-level exposures could make sense. Get the data for the tested system from your garment supplier or an online source – www.arcwear.com/resources/arc-flash-testing-data.php is a free resource – or perform the test yourself and you have protection without buying extra clothing. Only an arc flash hood would need to be added to the normal PPE every line technician needs. One company estimated they could protect every worker using a daily wear program and save 15 percent over buying 1,000 flash suits, excluding travel time. Remember that most lives are saved in high- and low-voltage situations when the clothing simply doesn’t ignite. Additionally, having the exact PPE isn’t what it takes to save a life, but it does speed up healing times, shorten hospital stays and increase quality of life. Wearing the right items makes the most difference.
High-Visibility Garments
A common best practice is using an AR, high-visibility vest instead of a melting vest. Melting “FR” vests do not meet the OSHA 1910.269 standard and definitely do not meet the ANSI 107 high-visibility standard. The U.S.-based International Safety Equipment Association (ISEA), along with ANSI, developed the ANSI/ISEA 107 high-visibility standard with expert knowledge of arc flash, flash fire, and firefighter needs and input. This standard does not allow a garment to be marked as FR unless it meets a specific FR standard; for arcs this would be ASTM F1506 or ASTM F1891. Some less scrupulous manufacturers bypass this requirement by placing an incorrect standard for “flame resistance” on separate labels. Be sure the correct standard is specified and used in your AR purchasing requirements and AR bid specifications for garments. Both safety and purchasing personnel should be involved in writing bid specifications.
Many companies are moving beyond AR vests to AR high-visibility shirts and T-shirts. Some have even begun to use high-visibility pants with high-visibility shirts. This makes high-visibility properties part of the uniform, and it also helps to assure worker compliance with both the AR and high-visibility requirements of all of a utility’s work zones. AR high-visibility garments are not widely available for flash fire protection due to some small-scale NFPA 2112 requirements that do not consider common high-visibility garments. Both the NFPA 2112 and ASTM F1506 standards were developed at the same time with different purposes, and many companies are working to resolve this in the NFPA 2112 standard to allow modacrylic-rich materials – the best non-melting fibers to dye with high-visibility dyes. One high-visibility fabric has met both NFPA 2112 and ASTM F1506 standards but in a heavier weight than what is commonly used in AR high-visibility vests. In Europe, most worker wear is high-visibility. Some companies even have specialty trousers that consist of a high-visibility upper part and a lower part colored navy blue for soil release. Many new ways of thinking can make garments more protective while maintaining their practicality.
Using a high-visibility T-shirt in summer adds a layer of protection beneath the common work shirt, and workers can wear comfortable T-shirt materials while they set up the safe roadside work zone. They can then don the long-sleeve AR shirt only for energized work. Wearing a high-visibility T-shirt eliminates the risk of ignition and melting next to the skin and provides additional protection as a layer in any arc event.
Arc Blast Blankets and Shields
Arc blast blankets typically have been specialty items used in limited applications. Until recently, one blanket cost several thousand dollars and was made of expensive materials unlikely to dip in price. But in late 2014, that all changed. Soon, arc blast blankets could almost be as cost-effective to install as welding blankets. One of the largest welding blanket companies in the world has modified their silicone-coated fiberglass blankets to take 40 kA for more than 10 cycles. These blankets do not absorb water and are basically dielectric. They are priced at a few hundred dollars per blanket. At that improved price point, arc blast blankets could be installed in every manhole and left so that optical-fiber and phone crews can work around cable splices with no liability for the utility. Additional work on installation procedures and methods will need to be completed, but this promising new technology might have just made a leap over older, existing technologies in both price and usability.
Hi Temp, located in Edmonton, Alberta, Canada, has been performing testing to see if PPE levels can be lowered while using the new blankets. Building on research conducted by Hydro-Quebec, Con Edison, ComEd, DTE Energy, Oncor and many others, these new blankets might be used for more applications than first imagined to prevent workers from being exposed to arc flash or to lower the energies to which they are exposed. Kevlar-type arc blast blankets still have many opportunities in the market, and Therm-Equip, Salisbury and Oberon have blankets designed for many applications. Evaluate the types of materials available, their ease of use and their cost for your work conditions because things have changed substantially and economically in the past year with the introduction of new materials.
Arc shields like the GaryGuard and meter shields for pulling meters can help separate workers from hazards and reduce exposure by as much as 50 percent from common arcs and even more from ejected arc exposures. Evaluate these types of materials as engineering methods to reduce arc exposure for your workers in testing and meter pulling.
System Calculations
While the OSHA 1910.269 standard does not require labeling of hazards in utilities, most companies are choosing to do so for power plants and some are using labels in substations. Hazard labels with PPE information make it easier for company and contract workers to select PPE. Since transmission and distribution systems are somewhat fluid with changes in load, feeding directions and connection points, most parts of a utility can’t be labeled like a normal manufacturing plant, nor does the standard require that. But system calculations can allow companies to assess their build standards to assure they build their substations and feeder specifications in ways that make workers safer from an arc flash perspective. Calculations can make a huge difference in arc flash energy potential, especially on the secondary side and in power plants.
Putting all these principles in place offers more work flexibility, greater protection and less variance from best practices by making compliance routine.
About the Author: Hugh Hoagland is senior partner at e-Hazard, a top arc flash and electrical safety training company. He is also president of ArcWear, which performs most of the world’s arc flash testing at Kinectrics in Toronto. Hoagland can be reached at hugh@arcwear.com.