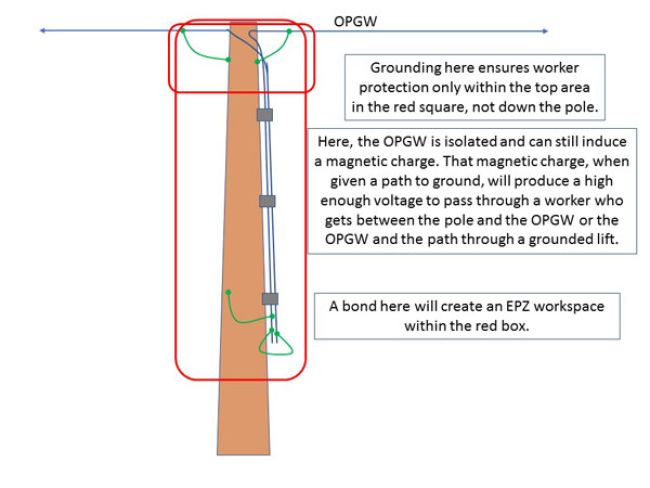
April-May 2021 Q&A
Q: I read the article “A Practical Review of the ANSI A92.2 Standard” in the October-November 2020 issue of Incident Prevention magazine (see https://incident-prevention.com/blog/a-practical-review-of-the-ansi-a92-2-standard/), and I’d like to know, is there a standard for the construction of electrically insulating bucket liners? We have problems with the geometry of a bucket. Because the walls of the bucket and the bucket liner are separated, I need to know the tolerance or maximum distance between the walls of those elements. Can you help?
A: We don’t know of a standard for liners other than the paragraph for buckets with liners in the A92.2 standard. That rule covers the requirements that the liner be rated and capable of passing the appropriate test. The liner also must be supported by the bottom of the bucket, leaving fit in the bucket up to the manufacturer and the buyer of the liner.
Liners are not required if workers are comfortable with that. Many workers have been brought through the industry with liners and believe they are mandatory and safer than buckets without liners. Again, however, liners are an option, and many utilities and contractors use them as a secondary level of protection. If you are gloving from a Category B bucket, the bucket itself is not required to have any primary insulating value because your primary means of protection are gloves, sleeves and cover-up. The bucket and boom are secondary barriers for the protection of the worker. As to the liner, the rule only requires that it be supported by the bottom of the bucket; therefore, it must be tall enough that it is not supported by the lip of the bucket. In the same way, the sides must be narrow enough that they do not support the liner on the sidewalls.
Many manufacturers of insulating devices have a third party fabricate their buckets. Some of those bucket manufacturers also fabricate liners for the buckets they build for other companies. Most of the people we talk to get recommendations from the bucket manufacturer regarding which liner will fit best. There are occasions when a bucket design or dimension may change; the manufacturer can usually find the serial number for your bucket and get you the right liner.
Q: I’ll soon be attending a meeting between our training department and a crane training company in town. The training company has told us that the OSHA rules changed in 2019, so we are required to get crane certifications for our linemen who use digger derricks or, at a minimum, provide them with awareness training. Is this accurate?
A: The only way that could be true is if a state plan has additional requirements for certifying digger derrick operators, which is the case in states including California and Washington. I noticed that you wrote us from New Mexico, so to be certain, I checked New Mexico’s state plan and found this statement: “NM OSHA has adopted all OSHA standards, incorporated by reference, that relate to state and local government and private sector employer operations. Therefore, the state and federal standards are identical.”
There is nothing in the exception to OSHA’s Cranes and Derricks in Construction standard (29 CFR 1926 Subpart CC) that has changed. Digger derrick operators setting poles, hanging equipment on poles, and setting pads and transformers on pads are exempt from the Subpart CC certification requirements as clearly defined in rule 1926.1400(c)(4). The exception is if your lineworkers are using digger derricks to set rebar cages and structural steel or regulators and breakers in a substation. OSHA says such work is normally performed using cranes, so they have limited the digger derrick exclusion to the job that digger derricks are designed for: digging a pole hole and setting a pole in it.
It has always been the case that any operator must be qualified, and per the 2014 revisions, they must demonstrate their qualification as an operator in compliance with the requirements of paragraph 1910.269(a)(2)(viii), which states, “The employer shall ensure that each employee has demonstrated proficiency in the work practices involved before that employee is considered as having completed the training required by paragraph (a)(2) of this section.”
This rule requiring demonstrated proficiency is met at the discretion of the employer and does not require the services of a third party. Typically, an employer’s program includes credentials such as references, job applications showing qualifications, on-the-job training, apprenticeship records, and observation by a person designated by the employer to observe and certify the operator as competent. The certification does not require any written materials, but a written notation describing the day and time a supervisor observed the operator is considered a best practice. As the employer, you only have to be able to defend your policy for ensuring competency of an operator to OSHA, should they ask in the course of an investigation or inspection.
If you wish, you can certainly use the services of a third party to meet these employer obligations, but third-party certification or awareness training is not required by any standard. By the way, the same holds true for riggers and signal persons. They are only required to be qualified, and that also can be done by the employer, just like the digger derrick qualification.
Q: The current practice at our utility is to use an extended tongue trailer or a caisson in certain situations. We’re looking at reconfiguring our trucks to allow the option of carrying poles, but can you tell me if other companies are presently doing this and what the pros and cons are? Also, if there are any policies or procedures that you’re able to share, please let me know.
A: Carrying poles on digger derricks is not uncommon and is done safely across the industry. There are critics, however, and they have a point. Recent fatalities have occurred due to carrying poles this way. One fatality was the result of trying to carry too many poles, which fell from the truck when the binders were removed. Another similar incident we are familiar with occurred while trying to remove one pole from a two-pole load. When the employee unrigged the first pole, the second pole fell on them. In yet another case, a fatality resulted from an operator knocking a pole onto an employee who was setting cones around the digger derrick.
Most experts and operating guidelines allow for carrying one pole on a truck. Others limit carrying poles on the truck from the trailer to the setting location when space does not permit trailering all the way into the setting location.
The process is legal within certain requirements and specifications, and it is successfully employed by many utilities and contractors across the U.S. and Canada. By OSHA’s expectation, the facilities for stowing the pole should be designed for the purpose. By design, the top end cannot exceed load-height limits without an oversize permit. The rear overhang must be flagged in accordance with Federal Motor Carrier Safety Regulations (FMCSR) and cannot exceed limits without an oversize permit. The weight of the pole must not cause the vehicle to exceed gross vehicle weight rating limits, and tie-downs must meet FMCSR requirements – one for every 10 feet of pole length. Yes, people have hit overhanging poles on trucks just as they do on trailers. The problem is that when the pole on the truck is hit, it can become detached, or the cradle can detach and fall onto a nearby car or person. When modifying your digger derrick platforms for pole transport, we suggest that you first consult the manufacturer for their recommendations or use a qualified structural engineer to design the cradle and attachments.
The issues for the working crew are loading and unloading. Picking up a load from a rest at an angle can be tricky, so a procedure should be developed and tested, and then training should be provided to the workforce. These are safety issues covered by 1910.269(a)(2)(viii) that require demonstrated proficiency of workers using this pole-loading technique.
Q: I learned from our engineering department that an optical ground wire (OPGW) is bonded to the pole. Does that protect workers training the OPGW into clamps down the pole for splicing? What do you recommend for protecting the worker?
A: Testing will tell you for sure how great the hazard is for the worker in the exposure you describe. Most OPGW clamps on poles are bushed with a rubber insert that isolates the OPGW from the pole. If there is an induction source, that OPGW will be a current-carrying conductor. A worker who gets between the OPGW and clamp while clipping in the OPGW will be subject to high voltage and current from the OPGW. For that reason, the worker on the pole or in a basket working on the OPGW must be bonded in to prevent becoming a ground path between the OPGW and the pole.
Grounding at the dead-ends at the top of the pole does not necessarily assure any safe values at the far end of the cable near the ground. We are familiar with two recent fatal instances on OPGWs halfway down the pole, and they were both bonded at the pole top. Bonding collapses voltage, but current remains and will create a voltage in the air gap between the OPGW and the grounded pole. If the high-resistance worker gets in that gap, and the voltage across the worker is high enough to penetrate the resistance of the worker’s body, current will flow. These differentials remain away from that pole top all the way to workers on the ground. Bonding at the lower end of the OPGW equalizes the potential differences between the OPGW and the pole, eliminating that voltage across the worker. See the graphic below that demonstrates the safe work zone for the worker who is effectively bonded in. What the graphic does not show is the work platform. If the work platform is a grounded basket, it must be bonded to the OPGW to prevent the worker from becoming a path to ground between the OPGW and the grounded basket.
In the graphic above, you can see that the bonding of the OPGW at the top of the pole only equalizes potentials in that local area. The rest of the OPGW hanging down the pole creates a risk to the worker if the two leads are not bonded together and bonded to the pole.
Q: I watched a webinar in which someone stated there have been changes in the 2018 version of ANSI A92, including new information on rescue devices. With our streetlight guys working alone, our company has provided the strap that attaches to the safety harness, which the worker can step onto to relieve blood flow restriction to the legs. But now, from what we have heard, it appears that a full rescue device to lower the employee is required. Have you heard anything about this? We were also told there is a requirement for arc-proof body harnesses for energized work.
A: As of today, there are no OSHA particulars requiring self-rescue from an aerial device. There also is no requirement for rescue from a bucket, although it is assumed since the risk is associated with two or more crew members. Single-man buckets in compliance with the two-man rule are not used in hazardous environments over 600 volts. The need for rescue is very unlikely.
There is nothing wrong with providing arc-proof or arc-resistant body harnesses and lanyards, and there are testing requirements manufacturers must meet to advertise their products as arc-proof or arc-resistant. However, as to the OSHA standard, there is not a requirement for arc-proof body harnesses. The only heat-proof standard is that they be able to pass the drop test, as noted in 1910.269(g)(2)(ii), which states: “Personal fall arrest equipment used by employees who are exposed to hazards from flames or electric arcs, as determined by the employer under paragraph (l)(8)(i) of this section, shall be capable of passing a drop test equivalent to that required by paragraph (g)(2)(iii)(L) of this section after exposure to an electric arc with a heat energy of 40±5 cal/cm2.” This is not a new rule and has been a requirement for harnesses in the ANSI standard for harnesses since 1994.
Additionally, there is no rule about insulating D-rings or attachments. They are designated in 1910.269(g)(2) as being constructed of steel or aluminum with no requirements for insulation or differentiation as to placement on the harness as insulating or conductive. Just being made of conductive material doesn’t mean it is a hazard. That D-ring would have to be grounded to arc, and that is an unlikely scenario. A worker who makes phase-to-ground contact across a D-ring has more problems to worry about than an arcing D-ring. We do assume that the person who wrote the standard for electrical resistance requirements for lanyards also wrote the requirements for D-rings (and he did), so we also assume he would know they were being used in energized environments. For practical consideration, minimum approach distance and cover requirements should prevent any hazards associated with contact.
There is nothing wrong with an employer training and/or providing equipment for self-rescue. We have consultants associated with Incident Prevention who provide rescue training for employers that is not required by OSHA. We also are aware of more than a dozen bucket incidents as recently as last year, and OSHA never cited the employers for lack of self-rescue training even under the General Duty Clause.
Do you have a question regarding best practices, work procedures or other utility safety-related topics? If so, please send your inquiries directly to kwade@utilitybusinessmedia.com. Questions submitted are reviewed and answered by the iP editorial advisory board and other subject matter experts.