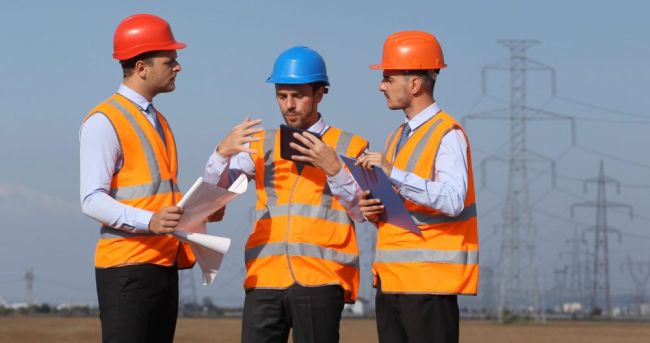
An Experiment in Crew Member Engagement
The new initiative being rolled out by one utility contractor aims to improve safety by increasing engagement among crew members.
I don’t talk about myself a lot – I listen. I developed this skill after taking on a leadership position with a utility contractor in an industry I knew nothing about.
My work history prior to this role included management in pretty much every industry except utilities. In each of my previous jobs, I strived to learn and advance from an entry-level position. In this new position, I no longer had the advantage of knowing how the company ran from the ground up; I had to trust and depend on others to help me. It did not take me long to realize that safety is the most important priority in this industry. Lack of attention to the detail of safety can kill a lineworker and damage a company beyond repair. So, while you could say our company’s journey to interactive safety began four years ago – when I accepted this new role – I would have to say that the real work is just starting.
The First Incident
In the early days of my employment, I was completely focused on understanding the operations of our business. We were growing rapidly at that point, and it was all I could do to keep up with new customers, additional work, and the increase in staff and equipment that come with exponential growth. I admit I had little time for safety, and my only attempts were to put out a weekly bulletin that was pulled from the internet and addressed subjects such as ticks and layered clothing. I was just checking boxes, trying to get things done.
I can remember our first incident during my tenure. It was an overnight fire in eastern New York on a pole that had been improperly grounded. The foreman in the field called me the next morning and suggested that we have an immediate stand-down. I did not know what a stand-down was, so of course I pretended that I did, and I agreed. We stopped work, the field leaders prepared a statement about what had happened and the lessons learned, we covered it at the show-up the next day, and everyone went back to work. The utility had ordered a one-day stand-down and we had complied. We checked that box, too.
Over the next few years, the company had a few more incidents. What I remember most about those times is that there seemed to be a cycle that went like this:
- An incident occurs.
- We examine the job briefing.
- We come up with lessons learned.
- We add some checkboxes to the job briefing.
- Someone is fired.
- We cross our fingers and wait for the next incident.
Essentially, everything was reactive in an industry that can kill in a millisecond.
Somewhere around that time, I noticed a disconnect. We were working with intelligent men and women who had passed classroom testing and field practicums to become lineworkers. They understood science and were proud of their careers. Yet we were responding to incidents by putting them through retraining or firing them, and most decisions regarding field policy were created behind a desk. I wondered, how did we get to the point where the people doing the work did not have input, and why were we creating a workforce that accepted that we did not value them enough to ask their opinions?
In previous jobs, I put a premium on communication and showed the people I worked with my appreciation for the value they brought to the company. This was done through respectful treatment that included requesting and acting on their ideas to improve all aspects of the business. They felt that they mattered and could make a difference. Now I was in an industry that was dictated from the top, and I was uncomfortable with that dynamic.
What could we do? Well, I kept checking boxes. We expanded our safety program by adding safety officers in the field, introducing a weekly safety call, tweaking our job briefing and bringing in safety leadership speakers. I truly care about every single person I work with and was doing everything I had seen done to “improve safety.” Intuitively, however, I knew it was not enough, and my knowledge of the typical lineworker skill set and attitude made me think that crew relationships were often at odds, which I suspected affected safety.
Then I listened to a podcast about crew relationships, engagement and the so-called “illusion of safety” created by checking boxes and autopiloting job briefings. That’s when everything fell into place for me.
A New Partnership
Enter our current safety consultant. He is not just any consultant. His ideas combine lineworker and safety experience, medical knowledge, backcountry rescue practices and a deep knowledge of the human brain. Just as important, he has partnered with our safety officer in the field, and their brains vibrate on the same frequency.
I believe that changing our company mentality is the secret to expanding our safety program and keeping people alive. The industry has improved every PPE item and added documentation ad nauseam to help our workers. I believe we have reached a wall with the physical aspect of safety and now need to work on relationships and experiential knowledge so that our workers can connect with each other and prevent incidents before they happen. Reacting once an incident has already occurred has not lowered the fatality statistics in this industry. That is a fact.
Since working with our current safety consultant, we have instituted two small changes in our field practices.
Change 1
Following the dictation of the job briefing, the crew now gets into a circle. Each participant states their role for the day’s work and points out any concerns they have. This practice activates communication and connection with others in a big way. Many aspects of the crew are affected; I will mention just a few.
First, by looking each other in the eye, workers’ brains are synchronized. Once synchronization occurs, crew members will naturally behave more as a team.
Second, lineworkers are competitive. If one states a concern, others will want to keep up, and information will cascade. This happened recently when a safety officer in the circle pointed out a rotten pole top. His observation queued up another team member, who noticed that a guy wire would create an obstacle in transferring a primary.
Third, by speaking up at the beginning of the day during the job briefing, apprentices are more likely to speak up later in the day as well. This is called the “activation phenomenon,” and I have noticed this in my private life. I am shy by nature, and if I am in a group of people and do not contribute early to the conversation, I sometimes shut down and feel nervous about speaking at all.
Change 2
We now conduct mental rehearsals of injuries and other medical emergencies so that our team can improve the chances of their brothers’ and sisters’ survival and create better health outcomes. These rehearsals are discussions as to what should happen first, second and so on if a co-worker is hurt.
We were recently in a meeting in which a working foreman stated that he was unsure of the order of actions to take if his co-worker collapsed. However, he also believed he would know what to do to help if something happened. This is a commonly held belief and the furthest thing from the truth. Without planning and practicing, your brain is flooded with emotion when a real incident occurs; you may become a deer in the headlights, so to speak. An injured person deserves your full attention and knowledge to help them. Imagine the guilt a crew member would carry if their co-worker died or had another serious outcome because they could not remember how to perform first aid or missed the symptoms of heatstroke.
Is It Working?
As a company leader, I realize the difficulties with this new initiative. How do we prove it is working? As our safety consultant is fond of saying, “There are no parades for things that do not happen.” If you walk into a bank, notice that the doormat is rumpled and straighten it, how can you prove that the elderly woman who entered five minutes later did not trip and break her hip because of your action? The simple answer is that there is no proof. Our new initiative derives from a much higher place, and I believe it is my place to grow this program.
At this point, our company has met with each of our employees for an introductory three-hour meeting followed by field visits to put the crew synchronization practice into place. We hope to encourage the “role and concern” job briefing practice for the next 30 to 60 days and see where it takes us. I am also suggesting that crews personalize the discussion after the job briefing; they can call it anything they want and conduct it in whatever manner is comfortable for them.
We want to accomplish a mission that improves crew relationships. We want to help crew members sync. If this plan does not work, I am committed to exploring other options that focus on psychological safety and the role the human brain plays in creating a safe dynamic.
Conclusion
I am excited to begin this journey that will have no end and whose success will be difficult to prove or quantify. Our safety team has instilled a new sense of confidence in the company by asking our team members for their opinions and helping them to realize that they are our safety. We must rely on the experience and ideas of those who perform the work. They are a valuable part of this endeavor, and their support to help us adjust and make this a practice will ultimately determine whether it succeeds or fails. It is groundbreaking. I believe that the small changes will cascade into other changes in both work life and personal life for many of us.
My lack of knowledge of this business and working in a male-dominated industry were initially of great concern to me. How could I possibly lead when I did not fit the stereotype of what is expected from a leader in this business? What path would I follow? I had such intense internal worries about these challenges in the beginning.
Through the support of the people with whom I work – and I mean from those working in every area of the company – I have grown to believe that the things that I initially considered deficiencies are the reasons we are where we are today. My lack of knowledge has created a situation wherein I do not do things “the way we have always done them.” I ask questions, and I ask for the input of many people. I live by the adage that we must be as safe as or safer than every other contractor, but we do not have to operate like every other contractor. The fact that I am female has brought a different level of caring to this company. While I hope that valuing everyone for what they bring to the table is noticed, the reality is that the culture will benefit from that dynamic.
In closing, I believe engagement will produce men and women who possess a new level of intelligence to model safety that can change outcomes. In turn, that may mean fewer funerals and fewer injuries – and that is our mission.
About the Author: Cheryl Richardson is the president of New York-based H. Richardson & Sons (http://hrsutilities.com).
- Solar Backfeed Safety on Distribution and Secondary Circuits
- An Experiment in Crew Member Engagement
- Skid-Steer Loaders: Hazard Awareness and Recommended Safety Practices
- Five Core Capacities for Sustainable Safety Excellence
- Switching and Tagging
- Ruling Spans and Proper Conductor Sag
- April – May 2024 Q&A
- Receiving Feedback