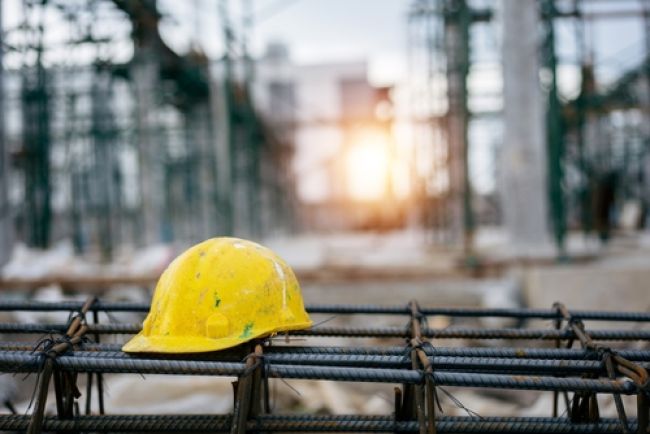
Safety By Design: A System Approach to Organizational Safety Initiatives
Employers can more effectively protect employees by using a planned process to develop their safety initiatives.
Let’s kick off this new series by considering a simple question: Why do we need safety?
Here’s my answer: Safety is a must because hazards and threats exist in our work environments that could cause harm to both our employees and our organizations.
Any initiative designed to protect workers from danger falls under the umbrella of safety. If we were to use minimum approach distances as an analogy, safety is the air gap that insulates an organization. When severe injuries and fatalities occur in our industry, weak safety initiatives – that is, initiatives that do not provide the insulating value needed to appropriately address an organization’s hazards and threats – are often the culprit.
Too many organizations invest their resources in “busy” initiatives that end up adding little value to their safety culture rather than taking a planned approach to determine and implement those activities that will insulate and protect them and their employees. It’s important for leaders to understand that simply increasing an organization’s number of safety initiatives doesn’t necessarily correlate to greater hazard protection for workers. Those safety initiatives must align with the organization’s needs based on the known hazards and threats faced by its employees.
The Approach
Safety is a critical component of all aspects of work in the electric utility industry. As such, it’s imperative to view it – and to work to develop and implement it – as a purposely designed system that aligns with organizational goals and can be integrated into the organization’s operating procedures.
That’s why I developed this series of six articles: to provide electric utility industry professionals with focused discussions about the various facets of using a system approach to determine an organization’s safety initiatives.
The reality is that protection from job-site hazards can be consistently achieved only through a purposely designed approach that allows for continuous improvement. To use a power-line analogy, think of the system approach as a loop feed. Loop feeds are adaptable; one can easily be isolated and fixed so power can continue to flow. Meanwhile, a radial feed loses all connectivity. A well-planned system approach – often referred to as a safety management system, or SMS – will be flexible, allow for improvement and enable continuous employee engagement. A safety program with no plan in place, however, offers no real direction, must often be redesigned and typically has lower levels of employee engagement.
The Plan
An organization that operates without a well-developed safety plan is much like a line crew that shows up to a job site with no staking sheet, materials, equipment or time to complete the job – and then their supervisor asks why the job isn’t getting done. Some companies believe that providing training, complying with regulatory standards and engaging in the latest safety fads will keep their employees safe. But the value of an organization’s safety initiatives is directly connected to their plan for success. A plan must outline these initiatives, including how they will be created, managed, monitored, coordinated, executed, assessed and consistently improved. Furthermore, all employees must be involved in the plan to help ensure they stay engaged with it.
Standards Can Help
Industry organizations use national and global standards to aid them in successfully building power systems. Standards can also be used to help build safety systems. You can refer to these two standards to assist your organization in building a comprehensive SMS plan:
- ANSI/ASSP Z10-2019, “Occupational Health and Safety Management Systems.”
- ASSP GM-Z10.100 provides requirement-by-requirement suggestions to implement and maintain an occupational health and safety management system.
- ASSP GM-Z10.101 is a Z10 quick-start guide for small- to medium-sized organizations. It is offered as a free download.
- ISO 45001, “Occupational Health and Safety Management Systems.”
OSHA also offers excellent recommendations for implementing safety and health programs. These resources are available at www.osha.gov/safety-management.
Future Articles
The remaining articles in this series will describe how to successfully connect and align SMS components and initiatives throughout an organization. In particular, the following topics will be addressed:
- Leadership and employee involvement.
- SMS planning.
- Human performance.
- Implementation and operation.
- Evaluation and effective action.
Summary
To effectively protect workers, utility organizations must develop safety initiatives using a planned process that is based on their assessed hazards and threats. Industry standards can assist in creating and implementing a plan that provides ample opportunity for employee engagement, opening the door for greater organizational safety success.
About the Author: Pam Tompkins, CUSP, CSP, is president and CEO of SET Solutions LLC. She is a 40-year veteran of the electric utility industry, a founding member of the Utility Safety & Ops Leadership Network and past chair of the USOLN executive board. Tompkins worked in the utility industry for over 20 years and has provided electric power safety consulting for the last 20-plus years. An OSHA-authorized instructor, she has supported utilities, contractors and other organizations operating electric power systems in designing and maintaining safety improvement methods and strategies for organizational excellence.
- Bad Attitudes and How to Handle Them
- To Improve On-the-Job Safety, Consistency and Continuing Education are Key
- Rubber Gloves and Chronic Injuries: Are Your Workers at Risk?
- ‘The Worst Day of My Life’
- The Roadmap to Gaining Senior Leader Buy-In for Safety Initiatives
- Safety By Design: A System Approach to Organizational Safety Initiatives
- Optimizing Arc Flash Protection: The Crucial Role of Layered Clothing