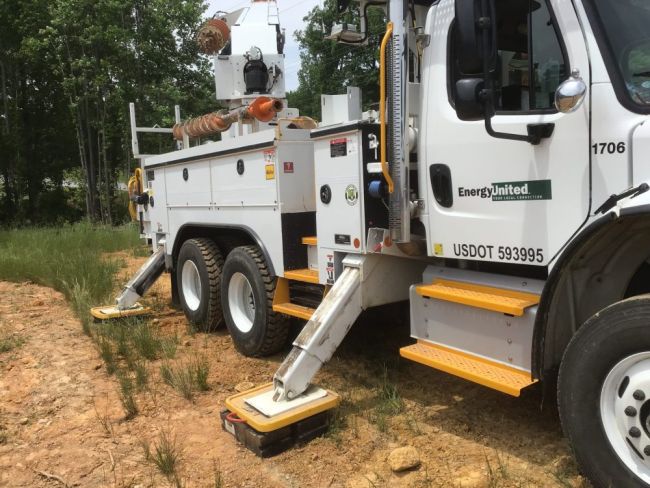
Equipment Stabilization Considerations for Utility Operations
Proper equipment setup is critical to both worker safety and productivity.
Utility workers face numerous challenges in their quest to build, maintain and improve infrastructure. One significant yet sometimes overlooked challenge is the risk associated with equipment instability. Crucial aspects of equipment setup include stabilization of the machine and selection of appropriate supporting materials – such as outrigger pads and cribbing blocks – to enhance work-site safety.
Case Study: EnergyUnited
From busy roadsides to uneven terrain and unstable surfaces, utility workers are no strangers to operating in precarious environments. These conditions can increase the risk of equipment tip-overs, which remain one of the most common – and preventable – job-site accidents. The consequences of such accidents range from equipment damage and project delays to worker injuries and fatalities.
To mitigate the risk of tip-overs, employers should consider a three-pronged approach to proper equipment setup that includes comprehensive employee training, proper work planning and effective use of supporting materials.
To illustrate the importance of work planning, let’s examine an approach taken by EnergyUnited, a North Carolina-based electric cooperative. Under the leadership of Jimmy Brown, director of fleet services, the cooperative established a formal policy for the use of outrigger pads and cribbing.
EnergyUnited collaborated with industry experts to assess their organization’s outrigger requirements, examining factors including truck weight, boom length, lift capacity and typical site conditions. As a result of this study, the cooperative implemented three key policies:
- Mandatory use of outrigger pads for all bucket trucks, digger derricks and small crane trucks.
- Use of cribbing blocks when operating on uneven terrain.
- Implementation of a fleet specification policy intended to ensure all company trucks are equipped with storage bins to carry the necessary stabilization tools.
This approach demonstrates how organizations can systematically address safety concerns related to equipment stability.
Stabilizers and Outriggers
Utility crews employ a wide range of equipment (e.g., aerial devices, digger derricks, boom trucks, compact crawler lifts). These machines typically come equipped with either stabilizers or outriggers.
Stabilizers keep a truck from tipping over or shifting while the bucket or digger is in use, providing lateral support during equipment operations. Equipment with stabilizers is operated “on rubber” – that is, its wheels or tracks stay on the ground – with the equipment’s suspension acting as the primary support. Loads and pressure transferred to the ground through stabilizers are usually lighter than with an outrigger-equipped machine. However, supporting materials are essential as sudden shifts in the boom can create dynamic loading that results in much heavier loads and pressure. Typically, a relatively small effective bearing area or area of supporting materials is required.
In contrast to stabilizers, out-and-down outriggers provide full equipment support. Equipment with these outriggers is operated “off rubber” (i.e., wheels or tracks are raised above ground level). Out-and-down outriggers significantly increase the base of the equipment, allowing for a wider range of motion or heavier lifting capacity. Because the total weight of the equipment, rigging and load is transferred directly through the outriggers, a larger area of supporting materials – properly spec’d to provide the appropriate strength and stiffness properties – is required to support these loads and pressures and to reduce them to levels the ground can withstand.
Materials Selection and Equipment Setup
When utility equipment is involved, two key elements should be incorporated into work planning:
- Guidelines for the selection and use of appropriate supporting materials.
- Procedures for equipment setup, which serve as a roadmap for safe operation.
Supporting materials such as outrigger pads should be selected by engineers and lift planners who are trained and competent to do so, including choosing the appropriate size of the materials. During the selection process, it’s important to evaluate:
- Loads and pressures that will be generated by the equipment.
- Allowable ground-bearing pressures and site-specific ground conditions.
- Whether supporting materials create a sufficient area to reduce ground-bearing pressures to levels the ground can withstand.
Supporting materials must also be inspected before each use to ensure they are not damaged, rotted, bent, delaminated or rusted in any way that could impact safety or stability.
Equipment setup procedures should provide step-by-step instructions for deploying stabilizers or outriggers. They should also include a pre-operation checklist to help ensure all safety measures are in place before work begins. Remember to work within the equipment manufacturer’s guidelines for levelness. Here are some other pointers to keep in mind:
- Always follow the equipment manufacturer’s setup requirements.
- Ensure the ground is firm, drained and level.
- Inspect for visual signs of excavations, standing water or poor soil.
- Ensure your setup plan is communicated to your team and that they fully understand it.
- Assess the work area for potential overhead and underground hazards.
- Properly deploy stabilizers or outriggers.
- Verify equipment stability before operation.
Cribbing Considerations
Cribbing plays a vital role in leveling equipment when the ground is uneven or sloped. Many different materials are used to “crib up,” and most can be stacked or interlocked to provide additional height and stability. However, to ensure a stable setup, it’s essential to use the correct cribbing based on the equipment’s weight and the severity of the slope. And because stacking increases risk, it is often best to use products manufactured for this specific purpose. Cribbing blocks with an interlocking surface or mechanism are an excellent option because they help prevent lateral sliding.
Key considerations when choosing cribbing materials include:
- Strength, stiffness and overall capacity of the materials.
- Safe stacking height.
- The interface between the cribbing and the outrigger pad.
- Overall stability of the cribbed structure.
Note that training on proper cribbing use must be provided to workers; improper use can create additional hazards.
The Science of Supporting Materials
The primary purpose of supporting materials like outrigger pads is to provide a flat, level surface that spreads a piece of equipment’s forces over a large area.
When assessing and selecting materials for outrigger pads, it’s important to understand the properties that contribute to their strength and stiffness. Strength refers to a material’s ability to resist breaking under load. A strong material can withstand great amounts of force without fracturing or failing catastrophically. Stiffness refers to a material’s resistance to bending under load. A stiff material maintains its shape and distributes loads more effectively over its entire surface.
The ideal supporting material should be a balance of both these properties. A pad that’s strong but lacks stiffness may bend excessively, leading to a functional failure even if it doesn’t break. Conversely, a stiff pad with less overall strength might break under extreme loads.
Several materials are commonly used for outrigger pads, each with its own set of characteristics. The best choice of material will depend on specific applications, expected loads, ground conditions and environmental factors. In some cases, a combination of materials may offer the optimal solution.
Factors such as moisture, temperature extremes and chemical exposure can significantly affect a material’s performance and longevity. Wood, an organic material, is particularly susceptible to environmental degradation. Exposure to moisture can rot and weaken the wood, while repeated stress from loading can also cause problems over time. In contrast, engineered materials like high-density polyethylene and fiber-reinforced polymers offer more consistent performance across a range of environmental conditions.
For operations in areas with extreme temperatures, it’s important to select materials that maintain their properties in both hot and freezing conditions. Keep in mind that some plastics may become brittle in extreme cold, while others may soften excessively in high heat.
Commit to a Culture of Safety
Ensuring safety and equipment stability in utility operations requires dedication at all levels of an organization. Without training on their proper use, even the best equipment and supporting materials can’t keep workers safe. A comprehensive employee training program should be equipment-specific and address the correct use of outrigger pads, cribbing and other supporting materials. By teaching equipment stabilization principles through training, selecting appropriate supporting materials and continuously working to sustain a culture of safety, utility companies can reduce their risk of job-site accidents.
About the Author: Kris Koberg is the president and CEO of DICA (https://dicausa.com), a family-owned manufacturer and distributor of supporting materials, ground protection, site access mats and associated products. He is a contributing member of the ASME P30 committee, a member of the North American Matting Association’s technical committee, and recent chair of the Specialized Carriers & Rigging Association’s task force to create “A Guide to Outrigger Pad Materials, Selection and Usage.”
- Are Your Employees 1910.269(a)(2) Qualified?
- Don’t Do This: Lessons Learned in the Field
- December 2024-January 2025 Q&A
- Win and Win Again: The Blueprint for Repeating Safety Successes
- Introducing the USMWF: A Powerful Ally for the Utility Industry
- An Inextricable Link: The Safety Benefits of Holistic Wellness in the Workplace
- Equipment Stabilization Considerations for Utility Operations
- A Three-Tiered Approach to Securing Buy-In for Safety Initiatives