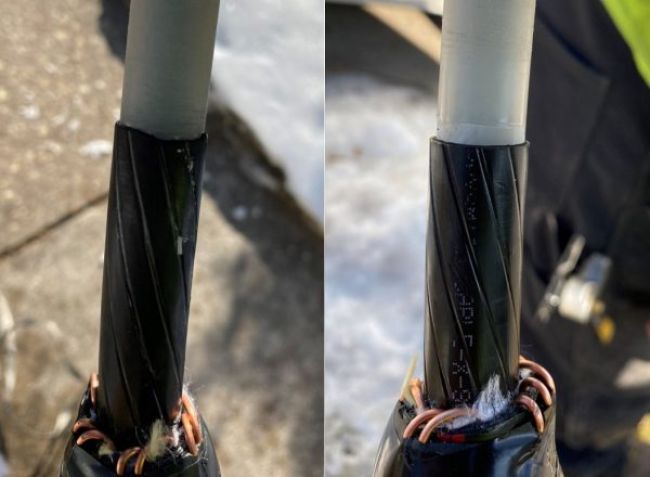
Increasing Safety Through Underground Integrity Management
Lower SIF rates and fewer unexpected outages are among the outcomes possible with a strong underground integrity management program.
The utility sector is at a higher risk of serious injuries and fatalities (SIFs) when compared to construction, manufacturing and mining, according to a 2018 study by DEKRA Organizational Safety & Reliability (see www.dekra.us/en/higher-serious-injuries-and-fatalities-sif-exposure-rate-in-utilities-sector-than-other-industries/). The study found that 30% of the SIFs in the utility industry are the result of motor vehicle incidents and another 28% are attributed to line-of-fire or struck-by incidents. Those are sobering statistics, but they help frame what’s possible in the realm of prevention if we can eliminate the need for many of our unplanned site visits. The encouraging observation is that about 42% (i.e., less than half) of SIFs are related to work on utility equipment. This article focuses on ways to reduce incidents related to underground cable systems, whether they occur due to electrical or non-electrical issues, since identifying and mitigating hazards before work begins should be a main goal of a company’s safety program.
But how do we get there? How can we make our cable systems more reliable so that we improve the safety of our co-workers through reductions in site visits and by conducting less unplanned or reactive work on underground cable systems, all while continuing to provide the type of uninterrupted service that customers expect? The simple answer is to remove the hazard of unplanned site visits altogether, but the path to eliminating that hazard begins with a look at the reliability of our cable systems.
Underground integrity management is a major factor in achieving a higher level of safety through creating a more reliable cable system. It reduces unplanned outages and produces a safer environment for both employees and the public. Let’s now look at four important components of underground integrity management: commissioning, company safety culture, preventive care and maintenance, and proper training.
Underground Cable System Commissioning
Early manufacturing and testing standards were inadequate to detect subtle and even gross defects in cable systems until the 1960s. However, since then, cable and accessory manufacturers have relied on offline 50/60-Hz partial discharge testing as the primary method for quality control of components before they leave the factory.
Using the same method as a final quality control measure in the field helps to ensure that cable system components have been safely transported to the site, and that proper workmanship has occurred during installation. Knowledge regarding cable system failure and its causes is critical to understanding how to resolve issues with your cable system before it is even utilized for the first time. Cable systems are designed to withstand a significant amount of electrical stress, but anything that causes a localized increase in that stress can result in partial discharge, which has the potential to lead to cable system failure.
Factors that contribute to partial discharge include voids in the insulation; damage to the cable from backfill; protrusions such as nails, tacks or other objects; an insufficient application of grease during accessory installation; and/or using improper cutback techniques during accessory installation. Accurately identifying and resolving issues with a cable system before it is put into service can increase the long-term health of that cable system, thereby reducing public and worker exposure to risks associated with unplanned cable system maintenance.
Data compiled from decades of field diagnostic tests by IMCORP, the underground reliability firm I work for, shows that even before energization of a new cable system, approximately 16% of cable components do not meet manufacturers’ standards.
Safety Culture
DEKRA’s 2018 study, referenced earlier, found that organizations with higher scores in management credibility, perceived organizational support, organizational value for safety, procedural justice and leader-member exchange have lower SIF rates. This suggests a direct correlation between safety being part of a company’s culture and improved safety performance.
During unexpected outages, frontline workers may be exposed to hazards that are atypical of their normal work conditions, often resulting in a higher-risk environment. These hazards can include motor vehicle incidents and accidents; working in limited visibility, such as in the dark or during a storm; working without proper equipment or other resources; fatigue; potential lack of a site-specific health and safety plan; and inclement weather. While this is not an exhaustive list, each of these hazards includes their own subset of hazards that will compound the risk of injury to our colleagues as well as the public. NIOSH’s hierarchy of controls shows that the elimination of hazards is the most effective form of hazard control we have. If we can reduce the number of unplanned system outages that we experience, we can increase the safety of our colleagues and the public.
Preventive Care and Maintenance
All of us, at some point or another, have said, “Hindsight is 20/20.” We say this when we know something now that we didn’t know when we made a previous decision. This is where system integrity management, or preventive care, comes into the picture to minimize unplanned work and decrease the number of site mobilizations. Having a method in place to design, install, inspect and maintain our systems to prevent cable system failures is proven to reduce the number of unplanned outages that can create hazardous scenarios. Most of us have a rolodex full of preventive care options, but we don’t always take advantage of them. The unfortunate reality is that the less effective your equipment is, the higher your injury rate is likely to climb.
Training
Underground integrity management also includes ensuring that our frontline workers receive correct, complete and ongoing training. As noted above, some issues with cables and accessories can be corrected on-site by fixing workmanship-related items, such as improper dimensions, non-radial cutbacks or simple contamination. These field issues typically result from a lack of appropriate or updated training for installers.
At IMCORP, our training departments strive for strategic alignment with business goals. Allowing these departments to provide training on new cable accessories or to outsource accessory consultations provides our frontline workers with the current knowledge and resources they need to be successful in the field, which helps to reduce the occurrence of unplanned outages and safety incidents. In-depth, hands-on and train-the-trainer styles of training offer proven results. Traditional training, which consists primarily of lectures and reading materials, results in a lower retention rate, while hands-on training results in a significantly higher retention rate, as does giving workers the opportunity to train others about what they’ve learned.
To ensure that our workers have the resources for success, we must strive to continually provide training opportunities that will enable them to put what they are learning into practice, plus allow them to train others to reinforce what they have learned.
Field Studies
Even with the best training, field studies show that effective partial discharge commissioning tests provide immediate feedback that can be used to improve reliability. A real-world case study of a large-scale aged asset system, consisting of more than 24,000 cable systems, resulted in a greater-than-98% reduction in failure rates (see https://imcorp.com/major-southeastern-utility). During this study, it was determined that 94% of the original cable could be left in service. With the ability to leave most of the cable in the ground, the rehabilitation program cost was reduced by more than 76% compared to a previous replacement program. While safety metrics were not measured during this study, the reduction in cable replacements and cable failures would likely reduce safety hazards and incidents associated with outages and repairs. This is an extreme example of what underground integrity management can provide, but achieving even a fraction of these results would be considered a success.
Conclusion
By developing and implementing an underground integrity management plan containing operational and design improvements, and by developing and implementing a conditional assessment and rehabilitation plan plus an appropriately designed training program, organizations will be better able to:
- Reduce extreme operational conditions.
- Pinpoint and repair existing defects that occur during installation or in the factory, as well as direct future proactive work.
- Reduce injuries.
- Lower costs.
- Ensure employees are equipped with the tools, knowledge and resources for success and efficiency.
As utility professionals, we have the responsibility to provide the safest possible workplace for our employees as well as the obligation to ensure our equipment and practices do not pose safety risks to the public. Underground integrity management is a helpful tool to do just that.
About the Author: Daniel Patseavouras, CPTM, is the EHS, quality and training lead at IMCORP (https://imcorp.com). His professional experience includes more than 18 years in the automotive, electric vehicle and utility sectors.
- From My Bookshelf to Yours: ‘Who Moved My Cheese?’
- 6-Step Method for Safety Harness Inspections
- A Targeted Approach to Safety Gap Analysis
- Crash Analysis: A Personal Story
- Electrical Protective Equipment and Live-Line Tools
- Ground Gradient Step Potential and PPE
- Increasing Safety Through Underground Integrity Management
- Influencing Crew Safety