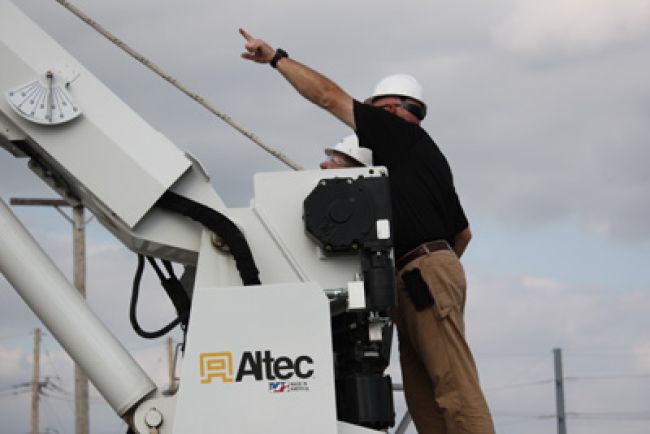
Aerial Equipment Innovations Aim to Protect Your Workers
Aerial devices have improved exponentially over the last 20 years. Many purchasers and users of the devices, however, are not fully aware of the options now available to them. Technology and innovation – driven by ANSI standards and user collaboration with manufacturers – have resulted in aerial equipment that provides greater functionality and improved safety mechanisms for utilities and operators.
In the U.S. and Canadian utility industries, aerial equipment must meet the requirements found in ANSI/SAIA A92.2, “American National Standard for Vehicle-Mounted Elevating and Rotating Aerial Devices.” The most recent version of the standard was published in 2015. For their part, manufacturers work hard to design and produce aerial equipment that meets utilities’ needs and adheres to or exceeds the A92.2 requirements.
In this article, we will review some of the aerial equipment technology and innovations now available in the market. We’ll also discuss pertinent ANSI safety standards for aerial equipment used in the utility industry.
Unlocking/Enabling Devices
Operators want to use equipment that is not subject to unexpected movement caused by accidental contact with controls. New to the ANSI 92.2-2015 standard, an unlocking/enabling device must be engaged before an operator can move a piece of aerial equipment. Previously, for safety purposes, most manufacturers employed triggers or finger pulls on levers to allow operators to mechanically unlatch them. Now, the standard requires all controls to meet the enabling safety latch requirement. Without a properly operating unlocking/enabling device, the aerial work platform can move unexpectedly, rendering it a potential hazard. To ensure the device and other safety mechanisms are functioning as expected, always perform a pre-operational check prior to use of the equipment.
Hydraulic Isolation Devices
There’s a potentially hazardous scenario that some in the industry have seen occur with the use of aerial equipment. A boom is aloft. The operator moves a control, but the boom movement is delayed and surges because someone on the ground is operating a hydraulic tool, robbing the aerial device of constant pressure. Workers aloft and on the ground can be endangered by erratic boom movement. In addition to grounding and bonding of the work area, aerial equipment that includes a hydraulic isolation/selector device can minimize the risk. The isolation device prevents the simultaneous movement of the aerial device and below-rotation functions, such as those related to outriggers, tools and other hydraulic work. The device can be bypassed with a selector but automatically resets when the system is restarted.
Gloving and Equipment Categories
Rubber gloves are barriers that prevent shock. When used as PPE, they are a secondary level of protection. If you are working from an insulating aerial device, they are your primary means of protection from electrical shock. With the exception of bare-hand booms, aerial insulating booms are not considered or designed as a primary means of protection. Category C aerial devices are designed as a secondary level of insulation for use below 46 kV. They can be used for gloving if equipped with boom-tip isolation that covers all metal, hoses and other non-insulating components that are at risk of current flow. Every aerial device manufacturer installs a nameplate on the aerial device that lists the device’s category. The A92.2 standard has criteria for the design and modification of each category and its use in the field.
For the general knowledge of readers, Category A platforms are those designed for bare-hand use at any voltage; they are properly equipped with gradient controls and shielding. Category A can be configured for gloving use. It is the only class where the boom is considered a primary means of isolation for the worker.
Category B booms are a secondary level of protection and designed to be used with hot sticks as primary protection. Category B, configured with the proper equipment, can be used for gloving.
Category C typically are gloving aerial devices.
Category D platforms are not designed for gloving work methods.
Category E platforms are not designed for gloving. They are limited to electrical exposures of 1 kV, 5 kV and 20 kV and typically used in the lights and signage industry.
Highly Resistive Controls
Even with the proper PPE in use during aerial work, accidents can still happen. For example, if the boom tip contacts a power line, the entire boom tip – including the controls – should be considered energized. Contact with another conductor or grounded object has the potential for current flow and an arc flash. If that occurs, PPE is the operator’s primary protection. However, a high electrical resistance control found on today’s aerial equipment provides another layer of safety by offering limited secondary dielectric protection. These insulating controls must be periodically tested and appropriately maintained to verify their dielectric properties. A proper test should occur at 40 kV AC for three minutes with a maximum allowable current of 400 mA.
Insulating Devices and Electrical Hazards
New requirements have been added to ANSI A92.2 for safe operating while handling energized phases. These rules comply with OSHA standards for hot sticks. OSHA has always prohibited use of a bucket to lift a phase, in a roundabout way. First, if the insulating boom is secondary protection, it cannot be used to protect an employee nor can a phase be laid on the lip of the bucket. If rubber goods are not to be used in compression, a live line cannot be sleeved in a line hose and laid on the bucket lip. A material-handling jib can be used if it complies with the hot-stick rules in OSHA 29 CFR 1910.269(j). The jib would have to be rated, tested and maintained for the appropriate voltage.
The A92.2 standard now has written requirements for using jibs to handle live lines. Winch ropes are not insulating, so live lines must be insulated from the rope. Jibs with wire holding tips must be rated and tested for live-line use. If more than one phase is to be handled, the work must be done with a properly equipped jib and insulating arm rated for the phase-to-phase exposure.
Fall Protection and Restraint
Fall protection systems are critical to aerial equipment safety and must be used in all situations to prevent injury from falls. An aerial lift must have fall protection anchor points to operate a fall restraint or fall arrest system. In the past, fall restraint options were extremely limited for insulating liners. However, there are now specially designed liners available that have a fall restraint anchor point inside the platform, giving workers a choice between using a fall restraint or a fall arrest system. For maximum protection, these fall restraint liners should include secondary connections to the boom tip and liner retention devices.
Load Monitoring
Aerial device operators must never exceed the platform and material-handling capacities of their equipment as overloading could cause damage to the aerial device. Active load-monitoring systems help operators stay within capacity limits by providing accurate load information. These systems can even notify the operator before an overload occurs. This helps prevent injury, unit instability and structural damage. Analyzing load-monitoring system data also can help identify undesirable trends and work practices.
An effective load-monitoring system should be easy for an operator to use and accurately warn the operator before platform or material-handling load capacities are exceeded. Visual and audible warnings should be clearly noticeable by the operator on the platform.
Summary
Developing appropriate work practices, following state and federal requirements, and adhering to manufacturer guidelines help to establish an environment for safe aerial equipment operation, which ultimately helps to reduce risk and prevent bodily injury and equipment damage. Staying informed and updated about the latest OSHA requirements, ANSI standards and new aerial device safety features also can help to reduce aerial-related accidents.
About the Author: Eric Lumberg is a manager of prevention and product safety for Altec (www.altec.com). He has worked for the company for over 15 years and has been a member of the ANSI A92.2 subcommittee for more than 10 years.
- Are You Taxing the Variables?
- Collaborating for Safety
- Arc Flash Considerations for Utility and Construction Activities: Part II
- Aerial Equipment Innovations Aim to Protect Your Workers
- Train the Trainer 101: FMCSR Awareness
- Voice of Experience: Human Performance Failures
- February-March 2020 Q&A
- Learning Styles: Implications for a Trainer